Introduction of portable metal roll forming machine
Portable metal roll forming machines have revolutionized the metal fabrication industry in recent years. Also known as mobile roll formers or portable roll forming machines, they offer metal fabricators efficient and cost-effective solutions for producing premium quality metal parts.
Unlike stationary roll forming systems that require expensive foundations and extensive setup, portable roll forming machines are lightweight and flexible. They can be easily moved from one location to another and quickly set up for metal forming operations. With rapid deployability and exceptional versatility, portable roll formers enable metal fabricators to fulfill a wide range of customer orders without restrictions of space or production capacity.
This articles explores the key benefits of portable metal roll forming equipment that make it an indispensable asset for modern metal fabricators.
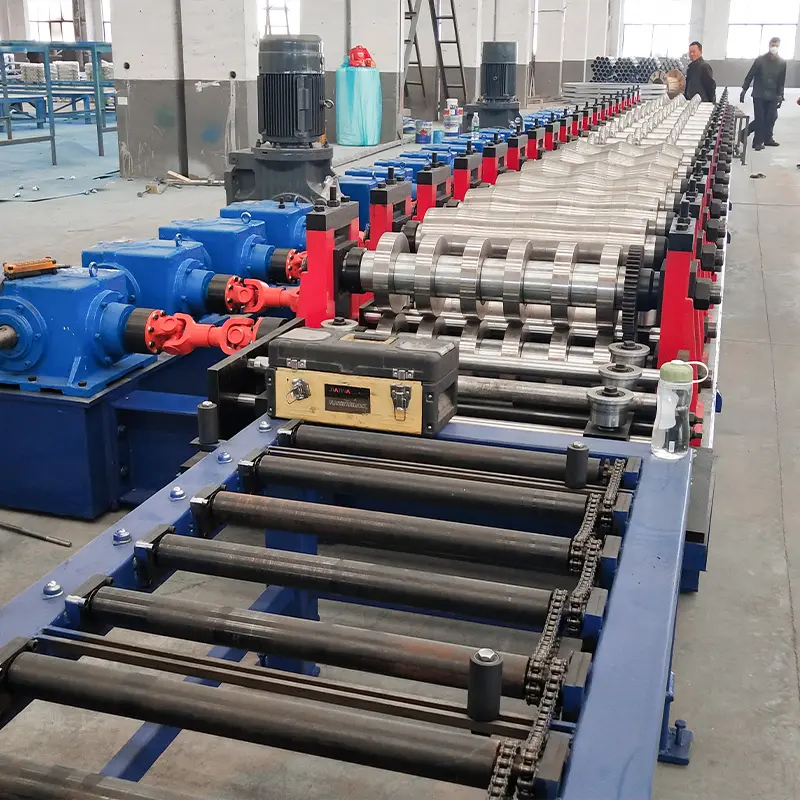
Flexibility in Production and Operation
One of the biggest advantages of portable roll formers is the exceptional flexibility they provide in production and operation. Here are some of the key ways portable roll forming systems enable flexible metal fabrication:
Easy Relocation and Quick Setups
Portable roll forming machines are designed to be quickly dismantled, relocated and set up with minimal effort. The average setup time for a portable roll former is 1-2 hours only. This enables metal fabricators to respond faster to changing production needs and easily move the equipment where needed. If a large order comes in, portable roll formers can be deployed to ramp up production capacity. They can be set up right next to the production floor, warehouse or even at the client’s site if required.
Suitability for Low to Mid Volume Production
Portable roll forming machines are ideal for producing low to medium production volumes efficiently. Their production output usually ranges from 1000 to 5000 feet per hour. This makes portable rolling equipment perfect for handling small to mid-size production runs. Metal fabricators can use them to profitably fulfill orders of 100 to 5,000 end-products.
Ability to Handle Varying Material Thicknesses
Portable roll formers can process sheet metal and coils ranging from 26 gauges to 1 inch thickness. This exceptional flexibility in material thickness enables metal fabricators to produce components of varying sizes and complexities without needing to invest in additional equipment. A single portable machine can handle production orders for thin gauge sheets as well as thick metal structures.
Formability for Diverse Metals and Alloys
Portable rolling mills can form different metals and alloys like galvanized steel, stainless steel, aluminum and copper. Metal fabricators can use the same machine to fulfill orders for diverse metal components without being limited by material type. Quick changeover and minimum setup time enables easy transition between different metals.
Compact Size Occupies Minimal Space
Portable roll forming equipment have a compact footprint ranging from 8 feet to 40 feet in length. They can be easily accommodated in limited spaces and moved through standard doors. This enables deployment directly on the production floor or near workstations. No dedicated foundations or space is required to install portable rolling mills.
Quick Changeover Between Profiles
Portable roll formers utilize quick-change forming heads that can be switched out rapidly to change profiles. Average changeover time is 15-30 minutes. This enables fabricators to switch between different custom profiles in a single production shift. Short changeovers allow accommodating urgent orders for new custom profiles even with small production runs.
Integration of Secondary Operations
Portable roll forming machines can be equipped with punches, cutoffs, embossing and other secondary processing capabilities. This enables completing multiple fabrication processes in a single portable setup. Secondary operations can be added modularly on the same machine as per application requirements.
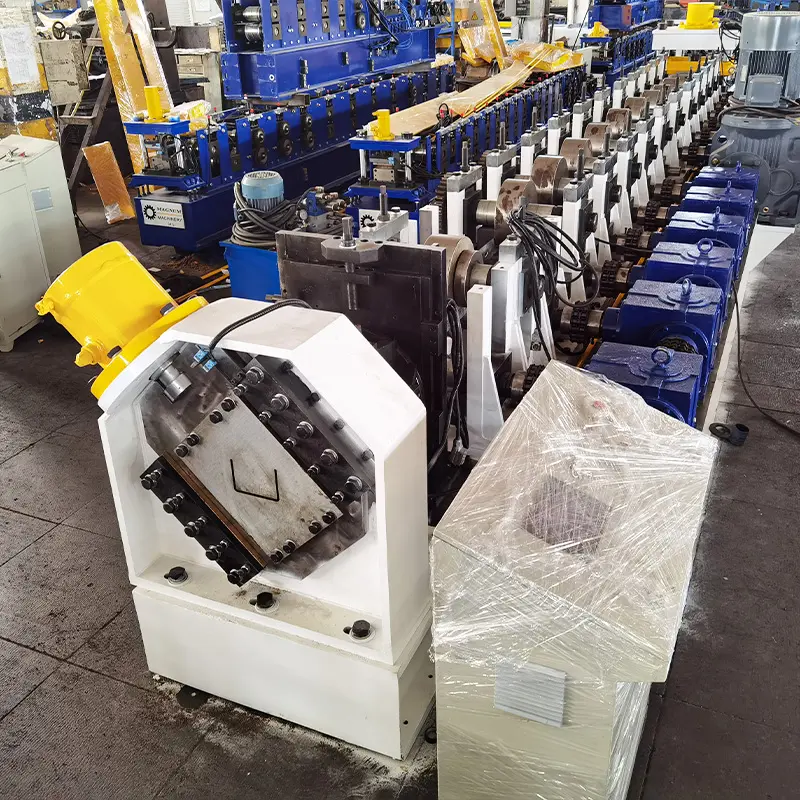
Cost Efficiency
Portable roll forming equipment provides exceptional cost efficiency that enables fabricators to maximize profits on every production order. Some of the ways portable rolling mills enhance cost-effectiveness are:
Low Equipment Investment
Portable roll formers require significantly lower upfront investment compared to stationary rolling equipment. A portable roll former costs just 20-30% of an equivalent stationary machine. The low equipment cost makes these machines accessible even for small or mid-size metal fabrication businesses with limited capital expenditure budgets.
Minimal Foundations Needed
Stationary roll forming lines require substantial foundations for installation which incur huge costs. Portable roll formers do not need special foundations since they are designed to be fully self-supporting. This drastically reduces set up costs.
Lower Energy Consumption
Portable rolling mills utilize advanced designs that minimize friction and energy losses. smart power transmission and drivetrain systems further optimize energy efficiency. The portable machines have 50-70% lower energy consumption compared to stationary roll formers.
Reduced Labor Costs
The automated operation, quick set up and integration capabilities of portable rolling equipment minimize the labor needed. Just 1-2 operators can set-up and run the portable roll former. Automated size changing and integration of secondary processes reduces the forming labor significantly.
Lower Maintenance Costs
Portable roll formers are designed for rugged use with minimal maintenance needs. Easy access to all the components also simplifies routine maintenance. The maintenance costs are reduced by 40-60% compared to stationary rolling mills.
Scalable Production Capacity
Portable rolling equipment provides scalable production capacity at lower costs. Metal fabricators can start with a single portable machine and add more modules as demand grows. This incremental expansion costs significantly lower than upsizing stationary equipment. Temporary portable roll formers can also be brought in on rent to meet seasonal or temporary spikes in production.
Reduced Material Handling
Quick set up and relocation capabilities of portable rolling mills eliminate the need for extensive material handling systems. No dedicated conveyors or cranes are required as the equipment can be placed near the raw material and finished products location. This provides major cost savings.
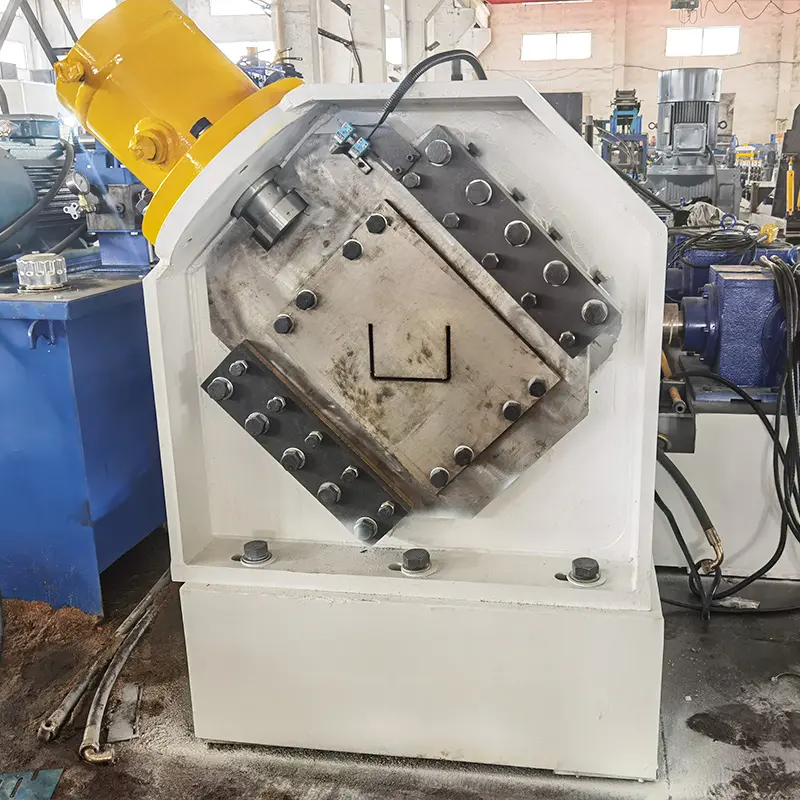
Superior Quality and Consistency
While providing flexibility and cost efficiency, portable roll forming machines also ensure the forming quality matches or exceeds that of stationary rolling mills. The latest portable roll formers utilize advanced features that enhance formed part quality and consistency.
Precise Forming With Automated Size Control
Portable rolling mills use high precision forming rolls made from milled H13 tool steel that provides excellent surface finish. Automated gauging systems continuously monitor and adjust size to maintain extremely tight tolerances of +/- 0.005 inches throughout the production run.
Consistent Feeding and Alignment
Heavy duty rollers, automated feed systems and precision formed guides maintain consistent feeding and alignment of the strip. This prevents edge waviness and distortion. Integrated guiding systems also enable forming narrow width coils without misalignment.
Real-Time Monitoring and Control
Smart sensor systems monitor key parameters like temperature and speed in real-time. The data is analyzed by the machine controller to make instant adjustments that maintain uniform quality. If any process deviations occur, the forming operation is immediately stopped to prevent defective output.
Synchronized High Speed Production
All the milling, feeding, forming, punching and cutting operations are synchronized to enable high speed production while maintaining part quality. The entire process is optimized to maximize throughput without quality loss.
Advanced 3D Forming Capabilities
With advanced controls and precision components like box guides, some portable roll formers can handle complex 3D profiles that undergo sequential bending and twisting. The machines can form spiral ducts, complex panels, spheres and cones while still being portable.
Secondary Process Integration
Any secondary processes like punching, piercing, slotting, dimples etc. are integrated inline within the portable rolling mills. This avoids rough handling of partly formed strips and ensures pristine quality of the final formed components.
Superior Finish and Tolerances
The combination of precision rolling heads, tempered steel rolls, inline gauging and real-time monitoring ensures exemplary finish with tolerances up to +/- 0.005 inches. This capability matches and even exceeds stationary rolling mills.
Safety
While providing unmatched efficiency, portable roll forming machines also incorporate advanced safety features that enable reliable and incident-free operation.
Complete Enclosure With Interlocks
The entire forming area is fully enclosed with interlocked access doors that immediately disengage power whenever opened. All moving components are completely isolated from operators.
Emergeny Stops
Easily accessible emergency stop buttons are provided at multiple locations around the equipment. The machine can be completely shut down immediately in case of any unexpected situation.
Integrated Safety PLC
A dedicated safety PLC provides an additional layer of monitoring and control for promptly responding to any anomalies. Safety sensors shut down the system instantly if any parameter exceeds allowable limits.
Roll Speed Monitoring
Speed of each set of forming rolls is continuously monitored. If any abnormal acceleration or deceleration occurs, the machine is shut down to avoid mishaps.
Current and Load Monitoring
Load on the motors and drives is monitored in real-time. Automatic shutdown occurs if overload conditions are detected to prevent equipment damage.
Foolproof Material Feed
Precision alignment and positive gripping rollers ensure consistent material feed without misalignment that can cause jams. Optical sensors detect any feed issues and stop operation.
Conclusion
Portable metal roll forming technology has completely transformed the economics and capabilities of metal fabricators today. Portable roll forming machines enable cost-effective solutions for rapid deployment, scalability, quick changeovers, small production runs, and integration of secondary processes – while still ensuring superior part quality and consistent high productivity.
With unmatched versatility, cost efficiency and quality capabilities packed in a rapidly deployable compact footprint, portable roll formers are an essential equipment investment for metal fabrication businesses of the future.
FAQ
What types of profiles can portable roll formers produce?
Portable rolling mills can produce almost all types of common structural, architectural, solar and component profiles including roofing panels, wall panels, trim, studs, track, channels, angles, tubes etc. Advanced portable roll formers can also produce complex 3D shapes.
What metal thickness can portable roll former process?
Most portable rolling mills have a thickness capacity range of 26 gauge to 1 inch. Larger portable roll formers are also available that can process metal coils up to 1.5 inch thickness.
How long does it take to set up a portable roll former?
Average setup time for a portable roll forming machine is just 1-2 hours. The quick set up enables relocation and production startup within a single shift.
What is the typical production speed of portable rolling mills?
Production speed offered by most portable roll forming equipment ranges from 1000 to 5000 linear feet per hour. Higher production speeds are also achievable with some advanced portable roll former models.
What is the average payback period for investing in a portable roll former?
For most metal fabricators, the cost savings and extra business enabled by portable roll formers results in a payback period of less than 12 months.
What size of facility is needed to operate a portable roll former?
Portable rolling mills do not need any special facility or foundation. They are fully self-supporting and can be deployed in any standard workshop or fabrication floor of sufficient length.
Can secondary processes like punching be integrated on portable roll formers?
Yes, most portable roll forming machine manufacturers offer options for integrating punching, shearing and other secondary processing within the portable rolling mill.
How many operators does a portable roll former require?
Most portable rolling mills are designed for operation by 1-2 persons. Automated size change, material handling and secondary processes minimize labor requirements.
What is the maintenance requirement for portable roll forming equipment?
Portable roll formers are designed for quick, tool-less component access to minimize maintenance. Just basic preventive maintenance like lubrication and inspection is required at regular intervals.