What is an AG Panel Roll Forming Machine?
An AG panel roll forming machine is a specialized piece of equipment used in the manufacturing of agricultural panels. These panels find extensive use in construction, roofing, and other agricultural applications. The machine operates by continuously bending and forming metal coils into the desired shape and profile. The result is a precise and consistent panel with uniform dimensions and high structural integrity.
AG panel roll forming machines consist of multiple rollers, each designed to gradually shape the metal as it passes through the machine. The process involves a series of progressive bending steps, ensuring that the material follows the desired contour accurately. This level of precision makes AG panel roll forming machines an ideal choice for producing panels that require intricate designs or specific measurements.
Key Features of AG Panel Roll Forming Machines
Feature | Description |
---|---|
Roller Configuration | AG panel roll forming machines typically feature a set of rollers that are strategically positioned to gradually shape the metal. |
Automated Operation | These machines are designed for automated operation, reducing the need for constant manual intervention. |
Quick Changeovers | Many AG panel roll forming machines allow for quick and easy changeovers between different panel profiles. |
Material Feeding System | A well-designed material feeding system ensures consistent material flow, contributing to uniform panel quality. |
Cutting Mechanism | Most machines include an integrated cutting mechanism that precisely cuts panels to the desired length. |
AG panel roll forming machines are known for their versatility, allowing manufacturers to produce panels with various profiles, thicknesses, and lengths. Their automated operation minimizes the need for extensive labor, resulting in improved efficiency and reduced production costs. These machines are an essential asset in the modern manufacturing landscape, enabling the creation of high-quality panels used in agricultural and construction projects.
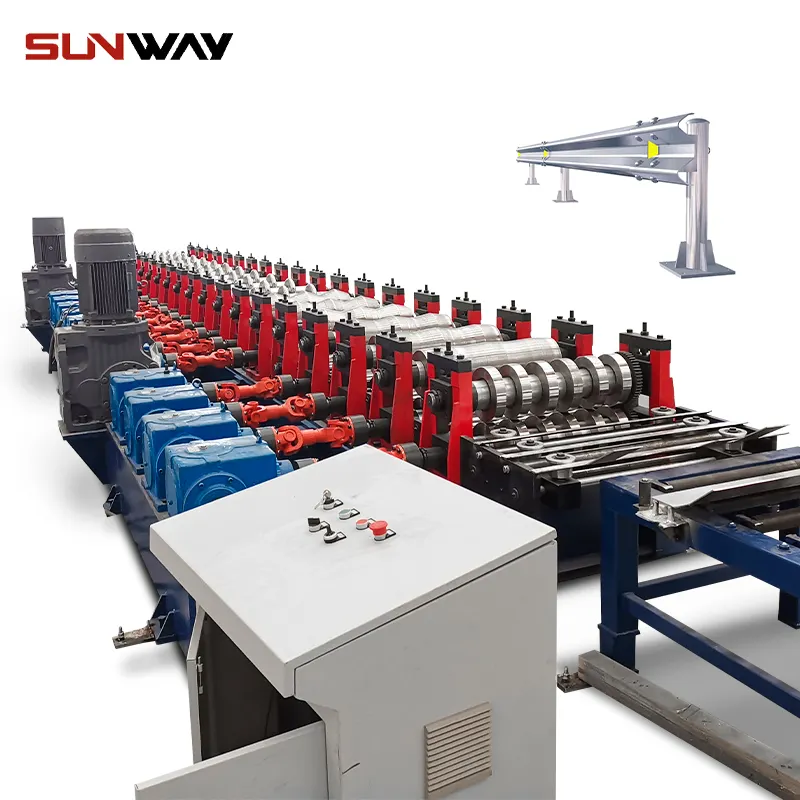
What are the Benefits of Using AG Panel Roll Forming Machines?
The utilization of AG panel roll forming machines offers several significant advantages over traditional manufacturing methods. These benefits contribute to increased efficiency, higher product quality, and enhanced cost-effectiveness in the production of agricultural panels.
- Precision and Consistency: AG panel roll forming machines ensure precise and consistent panel dimensions, reducing the likelihood of defects and material waste. The automated process guarantees that each panel adheres to the desired specifications.
- Efficient Production: The automated nature of AG panel roll forming machines allows for continuous and rapid production. This results in higher output rates compared to manual or semi-automated processes, meeting the demands of large-scale projects.
- Material Savings: Traditional manufacturing methods often lead to excessive material wastage due to imprecise cutting and forming. AG panel roll forming machines minimize material waste by accurately shaping the panels, optimizing material usage.
- Quick Changeovers: Manufacturers can easily switch between different panel profiles on AG panel roll forming machines. This flexibility enables efficient handling of diverse project requirements without lengthy setup times.
- Labor Reduction: Automated operation reduces the need for manual labor, decreasing production costs associated with workforce management. Skilled operators are still essential but in a more supervisory role.
- Enhanced Product Strength: The uniform shaping process of AG panel roll forming machines enhances the structural integrity of panels. This results in panels that are stronger and more durable, suitable for various agricultural and construction applications.
- Reduced Lead Times: The combination of efficient production, minimal material waste, and precise shaping leads to shorter lead times for manufacturing projects. This benefits both manufacturers and clients.
In conclusion, AG panel roll forming machines offer a host of advantages that make them a superior choice for producing agricultural panels. From precision and efficiency to reduced material waste and enhanced product quality, these machines play a pivotal role in modern manufacturing processes.
What Types of Materials Can be Used in AG Panel Roll Forming Machines?
AG panel roll forming machines are versatile tools that can process various types of materials, each with its unique properties and applications. The ability to work with different materials adds to the flexibility and broadens the scope of projects that can be undertaken.
Material | Description | Applications |
---|---|---|
Steel | Steel is a common choice due to its durability and strength. It’s used in roofing, siding, and agricultural structures. | |
Aluminum | Aluminum panels offer lightweight solutions and resistance to corrosion. They find use in portable structures and agricultural buildings. | |
Copper | Copper panels are prized for their aesthetic appeal and weathering characteristics. They’re often used in upscale architectural projects. | |
Galvanized Steel | Galvanized panels are coated with a layer of zinc for increased corrosion resistance. They’re suitable for harsh environments and outdoor applications. | |
Zinc | Zinc panels develop a protective patina over time, making them low-maintenance choices for roofing and cladding in various settings. |
The choice of material depends on factors such as the intended application, environmental conditions, and aesthetic preferences. AG panel roll forming machines can efficiently process these materials, ensuring that the resulting panels meet the required standards and specifications.
What is the Typical Production Speed of AG Panel Roll Forming Machines?
The production speed of AG panel roll forming machines can vary based on factors such as the complexity of the panel profile, the material being used, and the specific machine’s capabilities. However, these machines are designed for efficient and continuous production, making them suitable for high-volume manufacturing.
On average, AG panel roll forming machines can produce panels at speeds ranging from 60 to 150 feet per minute (18 to 45 meters per minute). It’s important to note that this speed is a general range and can differ based on the aforementioned factors.
The ability to achieve consistent high-speed production makes AG panel roll forming machines ideal for meeting the demands of large projects and tight deadlines. Manufacturers can adjust the speed based on their requirements, balancing efficiency with precision to ensure the quality of the panels remains uncompromised.
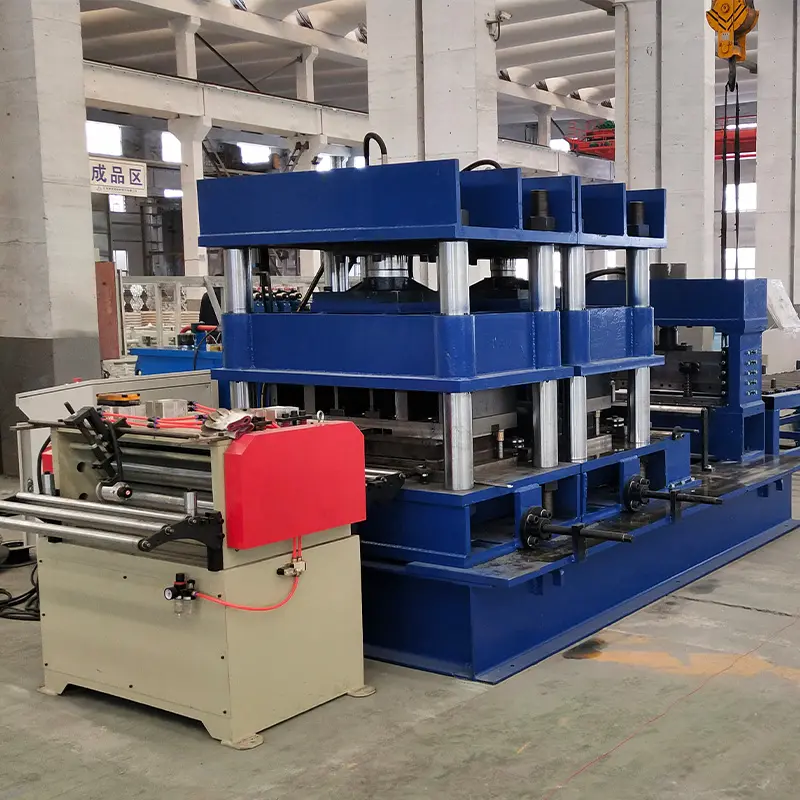
How Does the Maintenance Process Look Like for AG Panel Roll Forming Machines?
Proper maintenance is crucial to ensure the longevity and optimal performance of AG panel roll forming machines. Regular maintenance practices not only extend the machine’s lifespan but also contribute to the consistent quality of the panels produced.
Daily Maintenance:
- Check for any unusual noises or vibrations during operation.
- Inspect rollers and guides for wear or damage, addressing issues promptly.
- Lubricate moving parts as needed to prevent friction-related problems.
- Clean the machine and surrounding area to remove accumulated debris and prevent contamination of the panels.
Weekly Maintenance:
- Examine the electrical components for signs of wear, corrosion, or loose connections.
- Verify the accuracy of measurements and settings to ensure the panels maintain their intended dimensions.
- Inspect the cutting mechanism and replace any worn-out cutting blades.
Monthly Maintenance:
- Conduct a more thorough inspection of the machine’s structural integrity, including the frame and support components.
- Check the hydraulic or pneumatic systems for leaks and proper functioning.
- Review the machine’s software and controls, performing any necessary updates or recalibrations.
Quarterly Maintenance:
- Perform a comprehensive check of safety features, including emergency stops and interlocks.
- Verify the alignment of rollers and guides, making adjustments as needed.
- Inspect the overall cleanliness of the machine’s internal components.
Annual Maintenance:
- Disassemble and clean the rollers, guides, and forming sections thoroughly.
- Replace any components showing significant signs of wear, such as bearings or belts.
- Conduct a professional inspection to identify potential areas of improvement or parts that require replacement.
It’s essential to follow the manufacturer’s guidelines for maintenance and consult the machine’s manual for specific instructions. Regular maintenance not only ensures the machine’s proper functionality but also contributes to the safety of operators and the quality of the panels produced.
What Safety Measures Should be Considered When Operating AG Panel Roll Forming Machines?
Operating AG panel roll forming machines requires strict adherence to safety protocols to prevent accidents and ensure the well-being of operators. Safety measures should be in place throughout the entire production process.
- Training: All operators should receive proper training on the machine’s operation, safety procedures, and emergency protocols.
- Protective Gear: Operators should wear appropriate personal protective equipment (PPE), including gloves, safety glasses, and hearing protection.
- Machine Guards: Ensure that all necessary machine guards are in place before starting the operation. These guards prevent accidental contact with moving parts.
- Emergency Stops: AG panel roll forming machines should be equipped with easily accessible emergency stop buttons. Operators should know the location of these buttons and how to use them.
- Material Handling: Follow safe practices when loading and unloading materials to prevent injuries. Use lifting equipment or assistance when dealing with heavy coils.
- Regular Inspections: Regularly inspect the machine for any signs of wear, damage, or malfunction. Address any issues promptly to prevent safety hazards.
- Maintenance Procedures: Perform maintenance tasks only when the machine is properly locked out and tagged out to prevent accidental start-up.
- Fire Safety: Keep fire extinguishers readily available in case of emergencies. Ensure that the workspace is clear of flammable materials.
- Proper Lighting: Adequate lighting in the working area ensures better visibility, reducing the risk of accidents.
- Safe Work Environment: Maintain a clean and organized work environment to prevent tripping hazards and promote overall safety.
By following these safety measures, operators can minimize risks and create a safer working environment when operating AG panel roll forming machines.
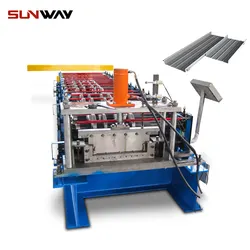
Summarizing the World of AG Panel Roll Forming Machines
AG panel roll forming machines have significantly transformed the manufacturing landscape, providing efficient solutions for producing high-quality agricultural panels. These machines offer precision, consistency, and versatility, making them essential tools for construction, roofing, and various agricultural applications. Their benefits, which include efficiency, material savings, and enhanced product quality, set them apart from traditional manufacturing methods.
AG panel roll forming machines can work with a range of materials, offering flexibility and the ability to cater to different project requirements. Their production speed, maintenance requirements, and safety considerations all contribute to their efficiency and effectiveness in modern manufacturing.
Whether it’s the choice of material, the production process, maintenance, or safety measures, understanding the world of AG panel roll forming machines is crucial for manufacturers and professionals in the construction and agricultural sectors.
FAQ
- Question: What is an AG panel roll forming machine?
Answer: An AG panel roll forming machine is a specialized piece of equipment used in manufacturing agricultural panels. It employs a continuous bending process to shape metal coils into uniform panels, commonly used in construction and roofing. - Question: What are the key features of AG panel roll forming machines?
Answer: AG panel roll forming machines come with several essential features, including a roller configuration for precise shaping, automated operation for efficiency, quick changeover capabilities, a reliable material feeding system, and an integrated cutting mechanism. - Question: How do AG panel roll forming machines compare to traditional methods, and what benefits do they offer?
Answer: AG panel roll forming machines excel in terms of precision, efficiency, and material savings. They produce consistent panel dimensions, offer rapid automated production, reduce material waste, enable quick profile changes, decrease labor requirements, enhance product strength, and shorten lead times. - Question: What types of materials can be effectively processed using AG panel roll forming machines?
Answer: AG panel roll forming machines can proficiently work with materials such as steel, aluminum, copper, galvanized steel, and zinc. The choice of material depends on factors like application, durability, corrosion resistance, and aesthetic preferences. - Question: What is the typical production speed of AG panel roll forming machines?
Answer: The production speed of AG panel roll forming machines varies based on factors like panel complexity and material used. On average, these machines can produce panels at speeds ranging from 60 to 150 feet per minute (18 to 45 meters per minute).