Introduction
In the construction and manufacturing industries, the demand for efficient and cost-effective steel structures is ever-increasing. Purlins, which are horizontal support members used in roof and wall framing, play a crucial role in providing structural stability. To meet the growing demand and streamline the production process, the C shape purlin roll forming machine has emerged as a game-changer.
What is a C Shape Purlin Roll Forming Machine?
A C shape purlin roll forming machine is an advanced piece of equipment designed to fabricate C-shaped steel purlins through a continuous roll forming process. It takes raw materials, usually steel coils, and transforms them into accurately shaped C purlins with consistent dimensions and high precision.
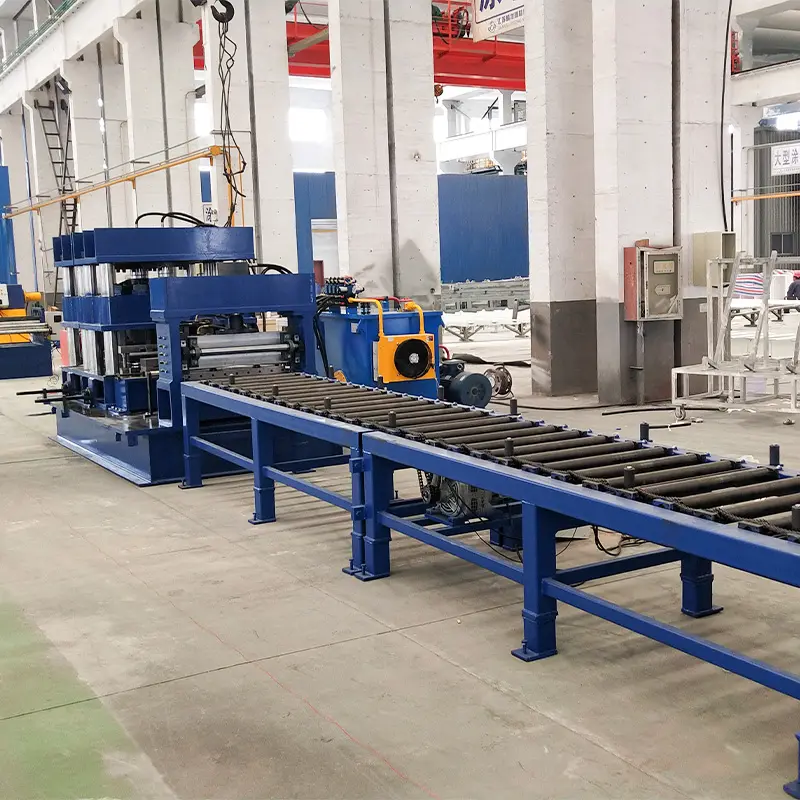
How does a C Shape Purlin Roll Forming Machine work?
The operation of a C shape purlin roll forming machine involves several distinct steps, each contributing to the smooth production of high-quality purlins.
Step 1: Material Loading
The process begins with loading the raw material, typically steel coils, onto the machine. The material is placed on the uncoiler, ready for further processing.
Step 2: Uncoiling
The uncoiler unwinds the steel coil, and the material feeds into the roll forming system.
Step 3: Feeding and Leveling
The material goes through a feeding system that ensures precise alignment and leveling of the steel coil, reducing the risk of defects during the roll forming process.
Step 4: Roll Forming
In this stage, the C shape purlin roll forming machine shapes the steel strip into the desired C-shaped profile. The material passes through a series of carefully contoured rollers that gradually bend it into the required shape.
Step 5: Cutting
Once the desired length of the C purlin is achieved, the machine automatically cuts it to the specified dimensions using a flying saw or a hydraulic cutting system.
Step 6: Stacking
The finished C-shaped purlins are then stacked and prepared for further transportation and use.
Advantages of Using a C Shape Purlin Roll Forming Machine
The utilization of a C shape purlin roll forming machine offers numerous benefits to manufacturers and construction companies alike.
Cost-Effective Production
The roll forming process is highly efficient and minimizes material waste, leading to cost savings in the long run.
Customization Options
C shape purlin roll forming machines can produce a wide range of purlin sizes and profiles, allowing for customization based on specific project requirements.
High Efficiency and Productivity
The continuous roll forming process ensures rapid production rates and high productivity, making it ideal for large-scale projects.
Consistent and Precise Results
The automated nature of the machine ensures consistent product dimensions and precise shaping, eliminating variations and defects.
Reduced Material Waste
Unlike traditional cutting methods, roll forming generates minimal waste, optimizing material usage and reducing overall costs.
Easy Maintenance
C shape purlin roll forming machines are designed for ease of maintenance, minimizing downtime and ensuring continuous operation.
Applications of C Shape Purlin Roll Forming Machines
The versatility of C shape purlins makes them indispensable in various industries and applications.
Construction Industry
C purlins are extensively used in constructing buildings, warehouses, and industrial structures due to their strength and load-bearing capabilities.
Infrastructure Projects
C shape purlins find application in infrastructure projects like bridges and roadways, providing essential support to various structural elements.
Manufacturing Sector
The manufacturing industry employs C purlins in the production of machinery, equipment, and storage systems, enhancing structural stability.
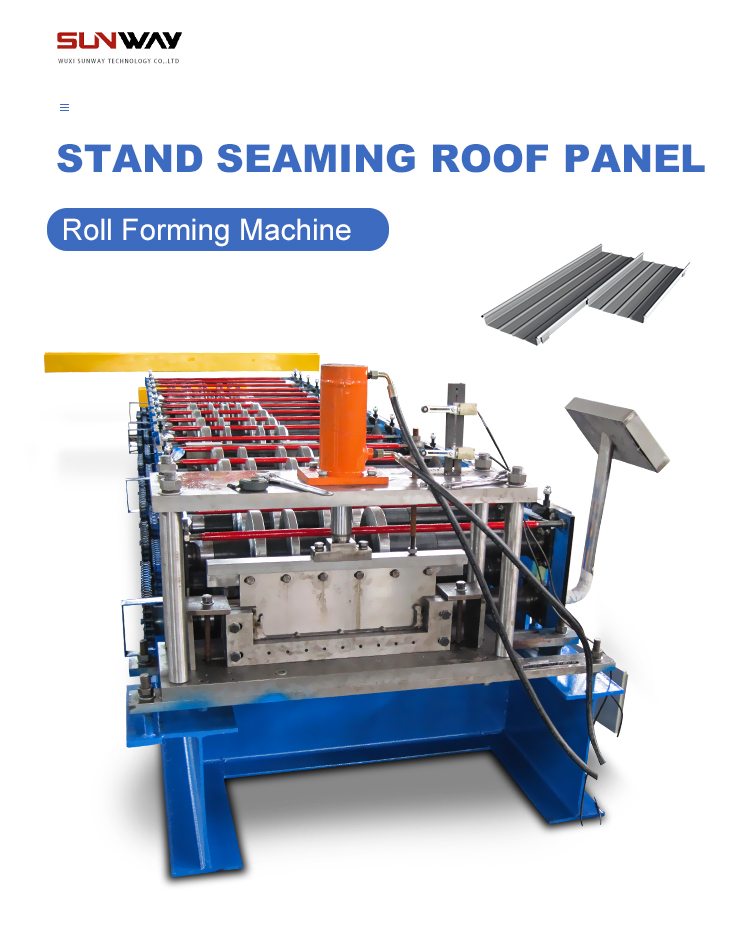
Choosing the Right C Shape Purlin Roll Forming Machine
Selecting the appropriate C shape purlin roll forming machine is crucial for achieving optimal results in the production process.
Consideration of Material Types
Different roll forming machines are designed to work with specific materials, so it’s essential to choose one that suits the intended application.
Machine Specifications
Evaluate the machine’s technical specifications, including roll forming speed, production capacity, and power requirements, to ensure it meets production needs.
Customization Capabilities
Look for machines that offer customization options to cater to unique project requirements and design preferences.
Automation and Control Systems
Advanced automation and control systems enhance operational efficiency and reduce the chances of errors during production.
After-Sales Support and Warranty
Ensure the manufacturer provides reliable after-sales support and a warranty to address any technical issues that may arise.
Maintenance and Care for C Shape Purlin Roll Forming Machines
Regular maintenance is vital for maximizing the lifespan and performance of a C shape purlin roll forming machine.
Regular Cleaning and Lubrication
Keep the machine clean and well-lubricated to prevent the buildup of debris and ensure smooth operation.
Inspection of Components
Regularly inspect critical components for wear and tear, addressing any issues promptly to avoid costly breakdowns.
Repairs and Replacements
In case of any mechanical or electrical problems, it’s essential to have a qualified technician conduct repairs promptly. Timely replacements of worn-out components are also crucial to prevent further damage.
Safety Precautions While Operating C Shape Purlin Roll Forming Machines
Safety should be a top priority when operating a C shape purlin roll forming machine to protect both operators and the equipment itself.
Proper Training of Operators
Ensure that all operators receive comprehensive training on the machine’s operation, safety procedures, and emergency protocols.
Use of Personal Protective Equipment (PPE)
Operators must wear appropriate PPE, such as safety helmets, gloves, and safety goggles, to minimize the risk of accidents.
Safety Features of the Machine
Verify that the roll forming machine is equipped with safety features, such as emergency stop buttons and safety guards.
Emergency Protocols
Establish clear emergency procedures and ensure that all operators are familiar with them to handle unexpected situations efficiently.
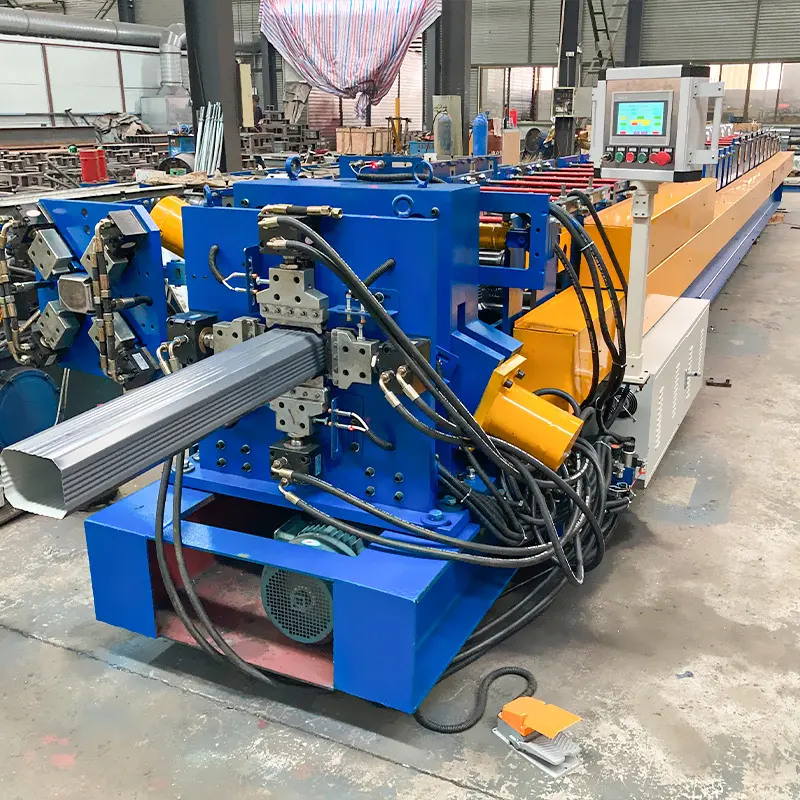
Common Issues and Troubleshooting
Despite its reliability, a C shape purlin roll forming machine may encounter certain issues during operation.
Material Jamming
Address material jamming promptly to avoid disruptions in the production process. Regular maintenance can help prevent this issue.
Uneven Roll Forming
If the machine produces purlins with inconsistent dimensions, check the rollers and alignment systems for any misalignments.
Cutting Errors
Inaccurate cutting can lead to defective purlins. Ensure the cutting mechanism is properly calibrated and functioning correctly.
Electrical and Mechanical Problems
For any electrical or mechanical issues, seek assistance from qualified technicians to prevent further complications.
Tips for Maximizing Efficiency and Performance
Implementing certain strategies can help optimize the performance of a C shape purlin roll forming machine.
Optimal Production Speed
Adjust the machine’s production speed according to the material and project requirements to achieve the desired output.
Proper Material Handling
Ensure proper material handling to prevent damage and ensure smooth processing throughout the roll forming stages.
Regular Machine Upkeep
Follow a scheduled maintenance routine to keep the machine in optimal condition and extend its lifespan.
Future Trends in C Shape Purlin Roll Forming Technology
The future of C shape purlin roll forming machines holds exciting developments to further enhance efficiency and sustainability.
Enhanced Automation
Advancements in automation will lead to even more streamlined production processes and reduced human intervention.
Integration with Industry 4.0
Integration with Industry 4.0 technologies will enable real-time data monitoring, predictive maintenance, and enhanced quality control.
Sustainable Manufacturing Practices
Manufacturers will focus on eco-friendly practices to reduce the environmental impact of production processes.
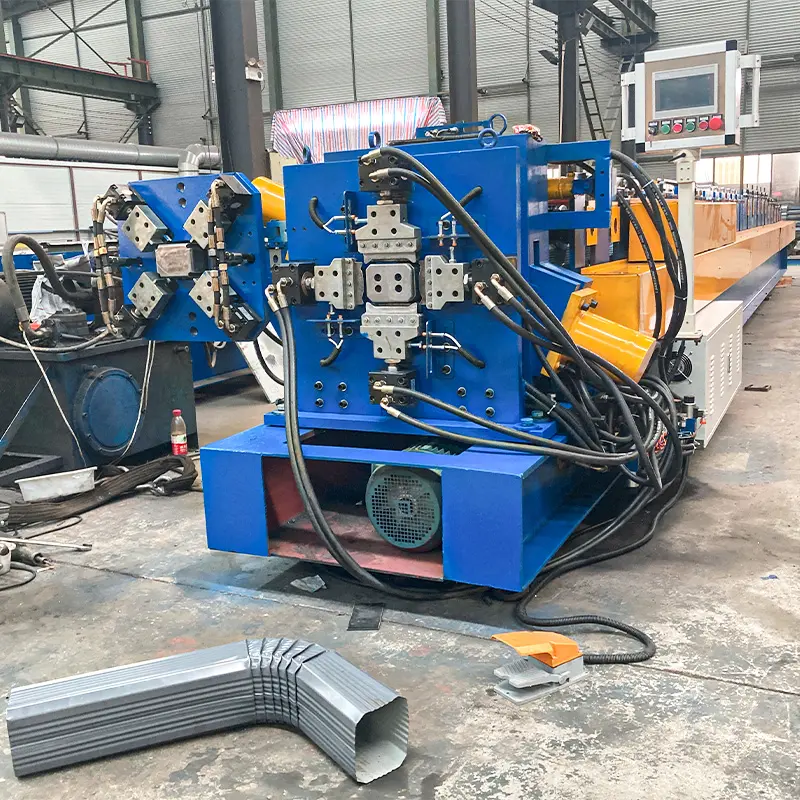
Conclusion
The C shape purlin roll forming machine is a crucial tool for the construction and manufacturing industries, enabling efficient and cost-effective production of C-shaped steel purlins. By understanding its working principles, advantages, and maintenance requirements, businesses can leverage this technology to achieve greater productivity and high-quality results.
FAQs
Q: What is the typical lifespan of a C Shape Purlin Roll Forming Machine?
A: With proper maintenance and care, a well-maintained C shape purlin roll forming machine can last for several years, often exceeding a decade.
Q: Can a C Shape Purlin Roll Forming Machine handle different material thicknesses?
A: Yes, most modern C shape purlin roll forming machines are designed to handle various material thicknesses, offering flexibility in production.
Q: Can I create custom profiles with a C Shape Purlin Roll Forming Machine?
A: Absolutely! C shape purlin roll forming machines can be customized to produce a wide range of profiles to meet specific project needs.
Q: Are C shape purlins suitable for both residential and commercial constructions?
A: Yes, C shape purlins are widely used in both residential and commercial constructions due to their structural strength and versatility.
Q: How can I ensure the safety of operators while using the machine?
A: To ensure operator safety, provide comprehensive training, enforce the use of personal protective equipment, and regularly inspect and maintain the machine’s safety features.