Introduction
In the ever-evolving world of metal fabrication, innovative machines play a crucial role in shaping various products used in diverse industries. One such revolutionary equipment is the Box Beam Roll Forming Machine. This remarkable device enables manufacturers to produce complex and customized box beam profiles with unmatched precision and efficiency. In this article, we will explore the ins and outs of this machine, its working principle, applications, benefits, safety considerations, maintenance tips, and more.
Understanding Box Beam Roll Forming Machine
Before delving into the technical aspects, let’s grasp the fundamentals of the box beam roll forming machine. This equipment is specifically designed for roll forming box beam profiles, which find extensive usage in construction, automotive, and storage system manufacturing.
Components of a Box Beam Roll Forming Machine
A box beam roll forming machine comprises several essential components working in harmony to produce impeccable box beam profiles. Understanding these components is vital to comprehend the machine’s overall functionality.
Base
The base serves as the robust foundation of the machine, providing stability and support during the roll forming process.
Rollers
The heart of the machine lies in its rollers, responsible for shaping the raw material into the desired box beam profile.
Gearing System
The gearing system facilitates the synchronized movement of rollers, ensuring precise and consistent roll forming.
Hydraulic System
The hydraulic system provides the necessary force and pressure required for the roll forming process.
Electrical Control System
The electrical control system governs the machine’s operation, allowing for easy adjustments and control over various parameters.
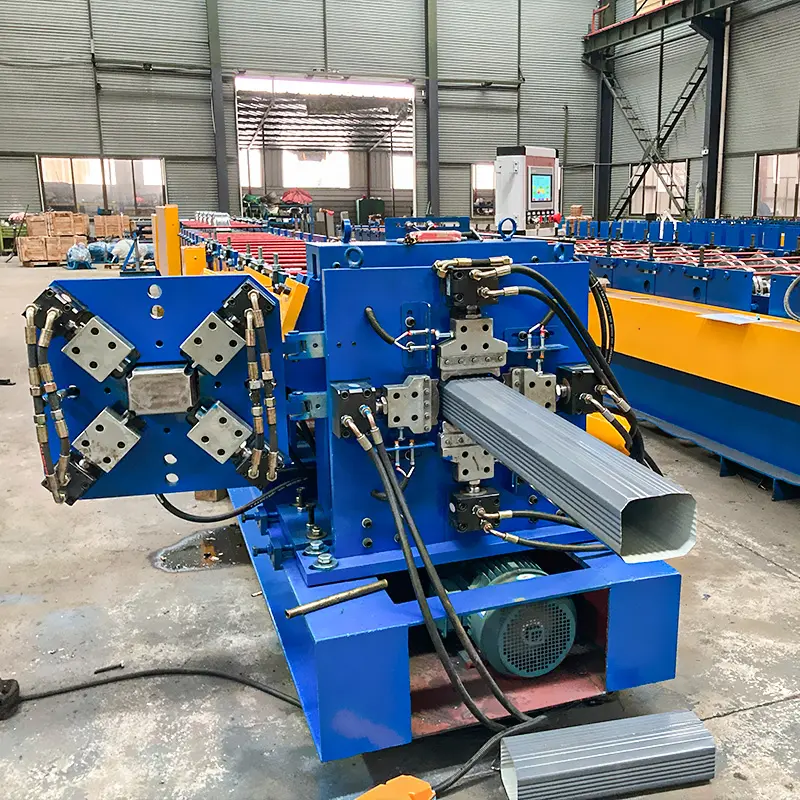
How Does a Box Beam Roll Forming Machine Work?
Understanding the step-by-step process of box beam roll forming sheds light on the ingenuity of this machine.
Step 1: Material Loading
The process begins with loading the raw material, usually in the form of coiled metal sheets, onto the machine.
Step 2: Guiding and Feeding
The material undergoes guiding and feeding through the machine, ensuring it enters the roll forming section accurately.
Step 3: Roll Forming Process
The rollers shape the material as it passes through the roll forming stations, creating the desired box beam profile.
Step 4: Cutting
After roll forming, the formed box beams are cut to the desired lengths, ready for further processing.
Step 5: Stacking or Packaging
The final step involves stacking or packaging the finished box beams, preparing them for shipment or use.
Advantages of Using a Box Beam Roll Forming Machine
The widespread adoption of box beam roll forming machines can be attributed to several key advantages they offer over traditional metal fabrication methods.
High Efficiency and Productivity
Box beam roll forming machines can operate at high speeds, significantly increasing production efficiency and output. The continuous roll forming process ensures a steady flow of finished box beams.
Precision and Consistency
The use of precision rollers and advanced control systems ensures consistent and accurate shaping of box beam profiles, reducing material wastage and minimizing variations in finished products.
Versatility in Profile Shapes
These machines can create a wide range of box beam profiles with varying dimensions and features, catering to diverse industry requirements.
Cost-effectiveness
The combination of high productivity and reduced material wastage contributes to cost-effectiveness, making box beam roll forming a financially viable solution for manufacturers.
Applications of Box Beam Roll Forming Machine
The versatility of box beam roll forming machines extends their application across multiple industries.
Construction Industry
Box beams find extensive usage in the construction of bridges, buildings, and infrastructure due to their high load-bearing capacity and structural integrity.
Automotive Industry
Automotive manufacturers employ box beams in vehicle chassis and body frames to enhance structural strength and crash resistance.
Manufacturing of Storage Systems
The storage and racking industry relies on box beams to construct robust and space-efficient storage solutions for warehouses and distribution centers.
Other Industries
The applications of box beam roll forming machines expand into industries such as aerospace, shipbuilding, and renewable energy, where strong and customized profiles are essential.

Factors to Consider When Choosing a Box Beam Roll Forming Machine
Selecting the right box beam roll forming machine is crucial for ensuring smooth operations and optimal results.
Material Compatibility
Consider the type and thickness of materials the machine can handle to ensure it meets your specific production requirements.
Production Speed and Capacity
Evaluate the machine’s production speed and capacity to align with your production targets and demands.
Customization Options
Look for machines that offer customization options, allowing you to create a wide variety of box beam profiles.
Ease of Maintenance and Service Support
A machine with accessible parts and good service support simplifies maintenance and minimizes downtime.
Budget and Cost Analysis
Factor in the initial cost of the machine, ongoing maintenance expenses, and potential returns on investment to make an informed decision.
Safety Precautions While Operating a Box Beam Roll Forming Machine
Safety should always be a top priority when operating any industrial equipment, including box beam roll forming machines.
Employee Training and Awareness
Properly train operators and personnel on the safe operation and handling of the machine to prevent accidents and injuries.
Machine Guarding
Install safety guards and barriers to protect workers from moving parts and potential hazards.
Regular Maintenance and Inspection
Routine maintenance and inspection help identify and rectify potential safety issues before they escalate.
Handling and Storage of Raw Materials
Adhere to safety guidelines for the proper handling, storage, and transportation of raw materials to prevent accidents and material damage.
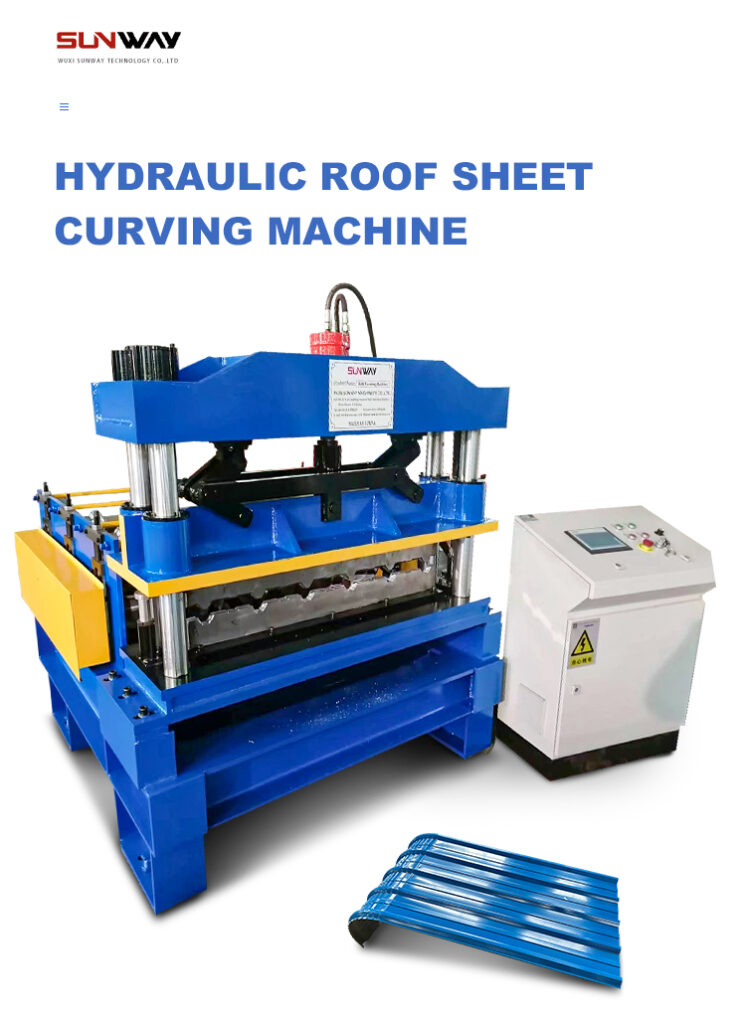
Common Maintenance and Troubleshooting Tips
Maintaining a box beam roll forming machine is essential for its longevity and optimal performance.
Regular Lubrication
Ensure all moving parts are well-lubricated to reduce friction and prevent premature wear.
Checking for Wear and Tear
Regularly inspect rollers, cutting blades, and other components for signs of wear and replace them as needed.
Cleaning and Rust Prevention
Keep the machine clean and apply rust prevention measures to protect it from corrosion.
Dealing with Jammed Materials
Train operators on how to handle material jams safely and efficiently to avoid damage to the machine and injuries.
Choosing the Right Manufacturer for a Box Beam Roll Forming Machine
Selecting a reliable and reputable manufacturer is vital for acquiring a high-quality box beam roll forming machine.
Research and Reviews
Conduct thorough research and read reviews to assess the manufacturer’s reputation and customer satisfaction.
Manufacturing Experience and Expertise
Opt for manufacturers with extensive experience and expertise in designing and producing roll forming machines.
Customization and Support Services
Choose a manufacturer that offers customization options and provides excellent after-sales support.
Warranty and After-Sales Support
Ensure the manufacturer provides a comprehensive warranty and readily available after-sales support for any technical issues.
Future Trends in Box Beam Roll Forming Technology
As technology continues to advance, the box beam roll forming industry is poised to witness exciting developments.
Automation and Industry 4.0 Integration
Automation and integration with Industry 4.0 technologies will enhance productivity and efficiency in roll forming processes.
Advanced Material Handling and Forming Techniques
Innovative material handling and forming techniques will allow the production of complex box beam profiles with improved precision.
Eco-Friendly Roll Forming Solutions
The industry is likely to see the adoption of more eco-friendly practices, such as using sustainable materials and optimizing energy consumption.
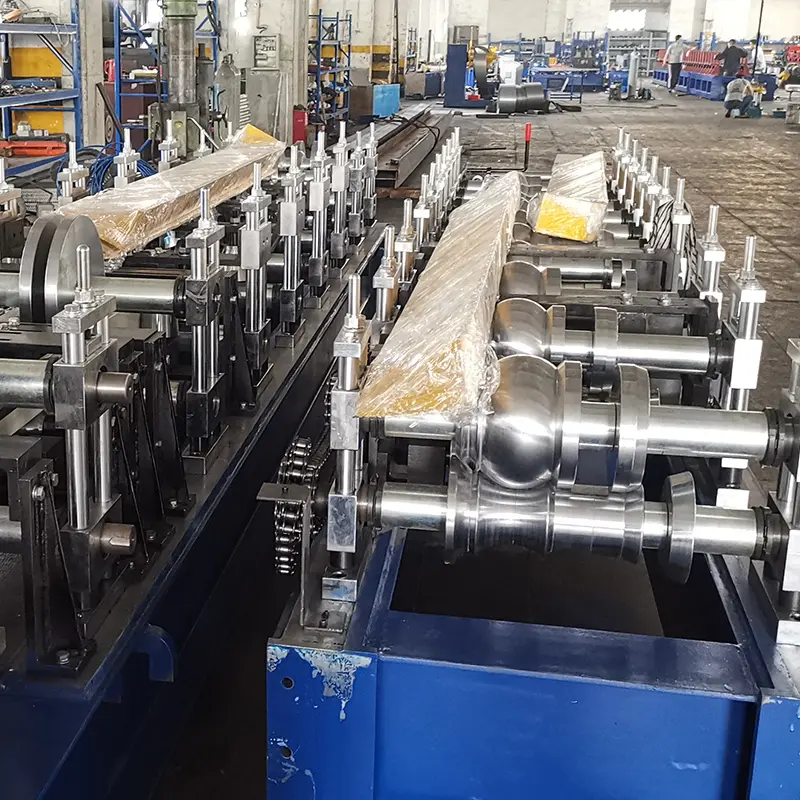
Conclusion
The box beam roll forming machine has revolutionized metal fabrication, enabling manufacturers to produce custom box beam profiles with unmatched efficiency and precision. Its applications across various industries and potential future advancements make it an invaluable asset in the realm of modern manufacturing.
FAQs
1. What is a box beam roll forming machine?
A box beam roll forming machine is a specialized equipment used to shape metal sheets into customized box beam profiles for various industrial applications.
2. How does a box beam roll forming machine work?
The machine uses precision rollers to shape raw material as it passes through the roll forming stations, creating the desired box beam profile.
3. What are the advantages of using a box beam roll forming machine?
The advantages include high efficiency, precision, versatility, and cost-effectiveness in producing box beam profiles.
4. What industries use box beam roll forming machines?
Box beam roll forming machines are commonly used in the construction, automotive, and storage system manufacturing industries, among others.
5. How do I choose the right box beam roll forming machine for my business?
Consider factors such as material compatibility, production speed, customization options, maintenance, and budget to make an informed decision.