Introduction
In the world of manufacturing, efficiency and precision are key factors for success. One remarkable machine that aids in achieving these goals is the corrugated roll forming machine. This article will explore the functionalities, benefits, applications, factors to consider when choosing, maintenance, and top manufacturers of corrugated roll forming machines.
What is a Corrugated Roll Forming Machine?
A corrugated roll forming machine is a specialized piece of equipment used in the manufacturing industry to shape metal sheets or strips into corrugated profiles. These machines utilize a series of rolls and forming stations to gradually bend and shape the metal, resulting in the desired corrugated pattern. The process is continuous and automated, ensuring high productivity and consistency.

How Does a Corrugated Roll Forming Machine Work?
The operation of a corrugated roll forming machine involves several steps. First, the metal sheet or strip is fed into the machine’s entry section. The material passes through a series of rolls that gradually shape it into the desired corrugated profile. Each roll applies a specific bending force, gradually forming the metal into the desired shape.
The machine’s computerized controls allow for precise adjustments of the roll gaps, ensuring accurate corrugation. Additional forming stations may be included in the machine to perform secondary operations, such as punching holes or cutting the corrugated sheet to the desired length.
Advantages of Using a Corrugated Roll Forming Machine
Cost Efficiency
Corrugated roll forming machines offer significant cost savings in comparison to traditional manufacturing methods. The automated process reduces labor costs, and the ability to continuously produce corrugated profiles in large volumes enhances overall efficiency. Additionally, the reduced material waste minimizes expenses associated with material loss.
Versatility
One of the notable advantages of corrugated roll forming machines is their versatility. These machines can shape a wide range of materials, including steel, aluminum, and even composite materials. By adjusting the roll gaps and forming stations, different corrugation patterns and profiles can be achieved, making them suitable for various industries and applications.
High Production Speed
Corrugated roll forming machines are capable of high-speed production, making them ideal for large-scale manufacturing operations. With automated feeding and continuous operation, these machines can produce a high volume of corrugated profiles in a short period, improving overall productivity and meeting demanding production deadlines.
Precision and Consistency
The automated nature of corrugated roll forming machines ensures precise and consistent results. The computerized controls allow for accurate adjustments of the roll gaps, ensuring the desired corrugation dimensions are achieved. This precision is vital for industries that require strict adherence to specifications, such as the automotive and construction sectors.
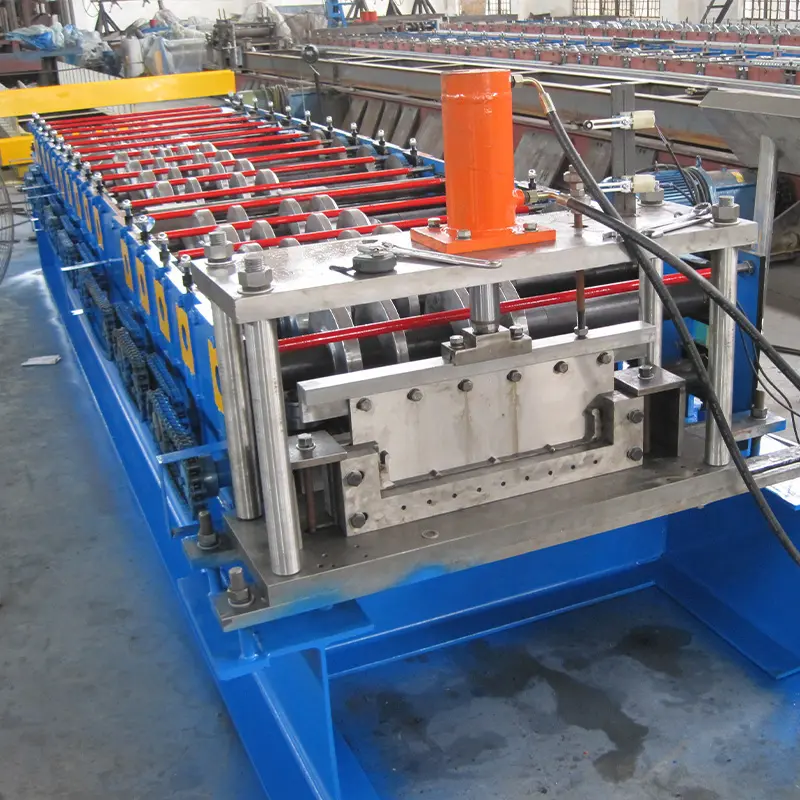
Applications of Corrugated Roll Forming Machines
Corrugated roll forming machines find applications in various industries due to their versatility and efficiency in producing corrugated profiles. Some common applications include:
Roofing and Cladding
Corrugated metal sheets produced by roll forming machines are commonly used for roofing and cladding purposes. The profiles provide excellent structural integrity, weather resistance, and aesthetic appeal. The versatility of the machines allows for customization in terms of sheet thickness, profile shape, and surface finish, catering to different architectural styles and requirements.
Automotive Industry
In the automotive industry, corrugated roll forming machines play a crucial role in manufacturing components such as chassis reinforcements, structural beams, and body panels. The ability to produce precise and consistent profiles ensures the components meet stringent quality standards while offering weight reduction and improved durability.
Packaging Industry
Corrugated packaging materials, such as boxes and containers, are commonly produced using roll forming machines. The corrugated profiles provide excellent strength-to-weight ratios and cushioning properties, ensuring the protection of goods during transportation. The machines allow for customization in terms of size, shape, and flute type, catering to various packaging needs.
Construction Industry
The construction industry benefits from the use of corrugated roll forming machines in manufacturing roofing panels, wall cladding, and structural components. The machines’ ability to produce long, continuous profiles in high volumes makes them highly suitable for large-scale construction projects. The versatility in material selection and profile customization ensures compatibility with different building designs and requirements.
Factors to Consider when Choosing a Corrugated Roll Forming Machine
When selecting a corrugated roll forming machine, several factors should be taken into consideration:
Material Thickness and Width
Different machines have varying capabilities regarding the thickness and width of the material they can handle. It is essential to choose a machine that accommodates the specific material requirements of your intended applications.
Machine Speed and Capacity
Consider the desired production speed and the machine’s capacity in terms of the number of corrugated profiles it can produce per minute. Assess whether the machine’s capabilities align with your production requirements.
Customization Options
Depending on your industry and applications, customization options such as adjustable roll gaps and additional forming stations may be necessary. Ensure the machine offers the flexibility needed to achieve the desired corrugation patterns and profiles.
Durability and Reliability
Investing in a high-quality, durable corrugated roll forming machine is essential for long-term productivity and cost efficiency. Consider the machine’s construction, materials used, and the reputation of the manufacturer to ensure reliability and longevity.
Maintenance and Care for Corrugated Roll Forming Machines
To ensure the optimal performance and longevity of a corrugated roll forming machine, proper maintenance and care are essential. Here are some key maintenance practices:
Regular Cleaning and Lubrication
Regularly clean the machine to remove any debris or buildup that may affect its operation. Lubricate the moving parts to reduce friction and prevent premature wear and tear.
Inspection and Repair
Periodically inspect the machine for any signs of damage or wear. Address any issues promptly to avoid production interruptions and costly repairs. Replace worn-out parts as needed to maintain the machine’s performance and accuracy.
Proper Handling and Storage
Follow proper handling procedures when operating the machine to prevent unnecessary stress or damage. Store the machine in a clean and dry environment when not in use to protect it from dust, moisture, and other potential hazards.
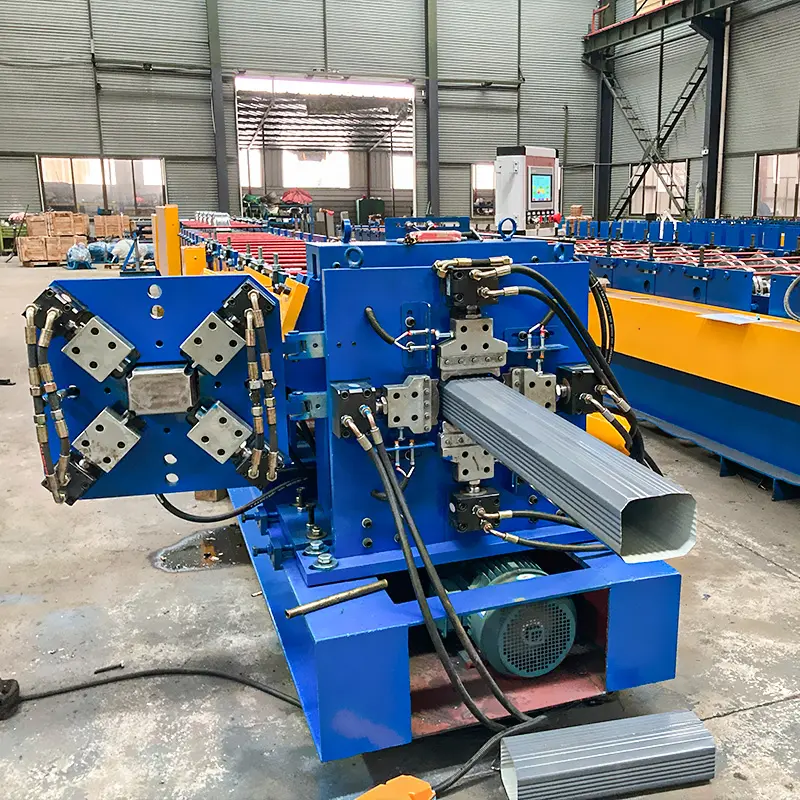
Conclusion
Corrugated roll forming machines are invaluable assets in the manufacturing industry, offering efficiency, precision, and versatility in producing corrugated profiles. They find applications in various industries such as roofing, automotive, packaging, and construction. When choosing a machine, consider factors like material requirements, customization options, and durability. Proper maintenance and care are crucial for maximizing the machine’s lifespan and performance. Reputable manufacturers provide a range of reliable and innovative corrugated roll forming machines to meet diverse industry needs.
FAQs
1. Are corrugated roll forming machines suitable for producing customized profiles?
Yes, corrugated roll forming machines can be customized to produce a wide range of profiles to meet specific industry requirements. By adjusting roll gaps and utilizing additional forming stations, different corrugation patterns and profiles can be achieved.
2. Can corrugated roll forming machines handle different materials besides metal?
Yes, corrugated roll forming machines can process various materials, including steel, aluminum, and composite materials. The machine’s versatility allows for flexibility in material selection based on the specific application.
3. How important is regular maintenance for a corrugated roll forming machine?
Regular maintenance is crucial for ensuring optimal performance and longevity of a corrugated roll forming machine. It helps prevent breakdowns, ensures accuracy, and minimizes downtime. Regular cleaning, lubrication, inspection, and timely repairs are essential maintenance practices.
4. Can corrugated roll forming machines be used for small-scale manufacturing?
Yes, corrugated roll forming machines can be used for small-scale manufacturing, depending on the machine’s speed and capacity. Some manufacturers offer models suited for lower volume production, making them suitable for small-scale operations.
5. What should I consider when choosing a manufacturer for a corrugated roll forming machine?
When selecting a manufacturer, consider factors such as reputation, experience, quality of machines, after-sales support, and customization options. Look for manufacturers with a track record of delivering reliable machines and providing excellent customer service.