Introduction
Are you in the metal fabrication industry and looking for an efficient and cost-effective way to produce square pipes? Look no further than a square pipe roll forming machine. This advanced piece of equipment allows you to automate the process of creating square pipes with precision and consistency. In this article, we will explore the various aspects of square pipe roll forming machines, including their benefits, working principles, key components, maintenance requirements, and more. So let’s dive in!
What is a Square Pipe Roll Forming Machine?
A square pipe roll forming machine is a specialized piece of equipment used in the metalworking industry to manufacture square pipes from flat sheet metal. It employs a continuous bending process where a strip of metal is passed through a series of rolls that gradually shape it into a square pipe profile. The machine uses a combination of rollers, guides, and cutting tools to ensure precise dimensions and a high-quality finish.
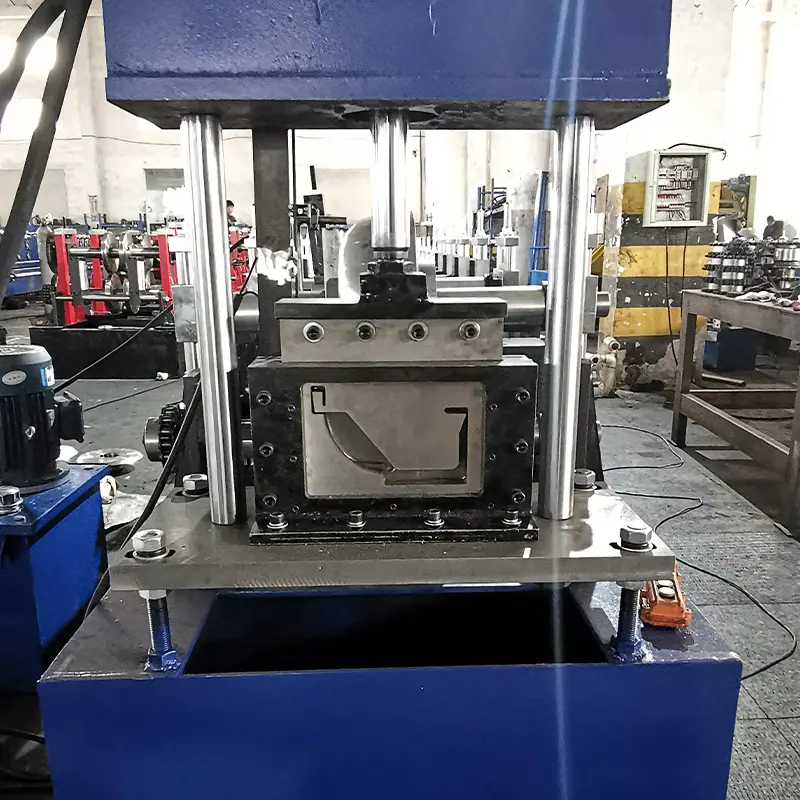
Benefits of Using a Square Pipe Roll Forming Machine
Using a square pipe roll forming machine offers several advantages over traditional manufacturing methods. Here are some key benefits:
- Cost Efficiency: Square pipe roll forming machines can produce square pipes at a faster rate and with less material waste compared to other fabrication methods. This leads to significant cost savings in terms of both material and labor.
- High Precision: Roll forming machines provide excellent dimensional accuracy, ensuring consistent square pipe profiles throughout the production process. This precision is essential for applications that require tight tolerances.
- Versatility: Square pipe roll forming machines can accommodate a wide range of material thicknesses and sizes. By adjusting the machine settings, you can produce square pipes of different dimensions to suit various applications.
- Time Efficiency: With automated feeding and cutting mechanisms, square pipe roll forming machines can produce square pipes in a continuous and efficient manner. This saves time and increases overall productivity.
Applications of Square Pipe Roll Forming Machines
Square pipes manufactured using roll forming machines find applications in various industries. Some common applications include:
- Construction and architecture: Square pipes are used in building structures, support columns, handrails, and fences.
- Automotive industry: Square pipes find use in vehicle frames, chassis components, and exhaust systems.
- Furniture manufacturing: Square pipes are utilized in the production of furniture frames, such as tables, chairs, and shelves.
- Electrical enclosures: Square pipes serve as the framework for electrical panels and cabinets.
- Greenhouse construction: Square pipes are employed in the construction of greenhouse frames and support structures.
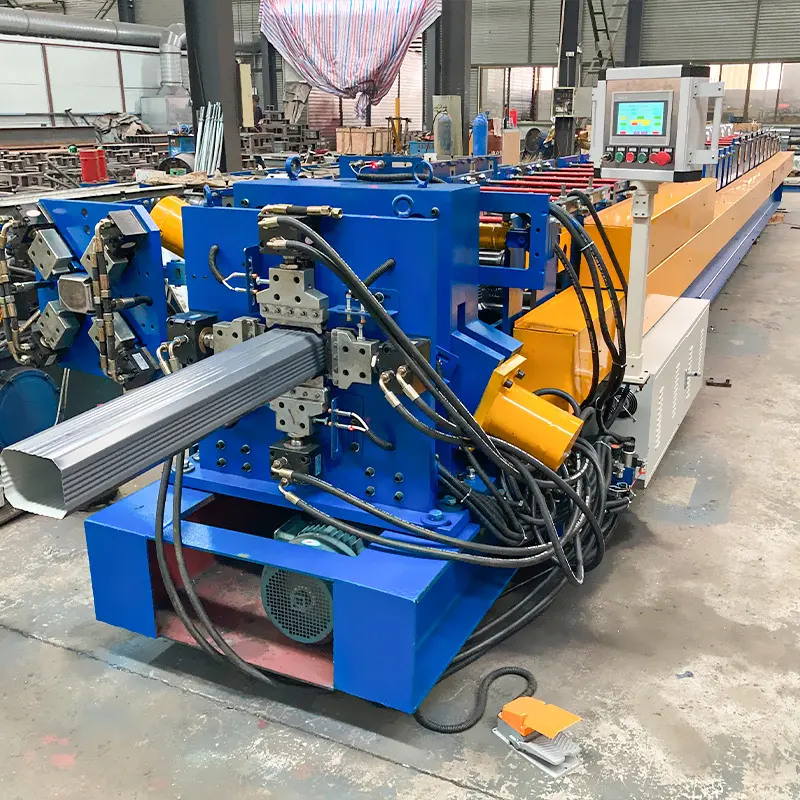
How Does a Square Pipe Roll Forming Machine Work?
A square pipe roll forming machine operates on the principle of continuous bending. Here is a step-by-step overview of the working process:
- Material Feeding: A flat strip of metal, usually steel or aluminum, is fed into the roll forming machine. The strip passes through a series of rollers that gradually shape it into a square pipe profile.
- Roll Forming: As the strip moves through the rollers, it undergoes a series of bending and forming operations. Each set of rollers gradually bends the metal strip closer to the desired square shape.
- Cutting and Length Measurement: Once the desired length of the square pipe is achieved, the roll forming machine automatically cuts the pipe to the required size. Simultaneously, a length measurement system ensures accurate cutting.
- Ejection and Stacking: After cutting, the square pipes are ejected from the machine and collected in a stacking area for further processing or packaging.
Key Components of a Square Pipe Roll Forming Machine
A square pipe roll forming machine consists of several essential components that work together to produce high-quality square pipes. Here are the key components:
- Decoiler: This component holds and feeds the flat strip of metal into the machine. It ensures a continuous supply of material during the roll forming process.
- Roller Stations: The roller stations consist of multiple sets of rollers that progressively bend and shape the metal strip. Each roller set performs a specific forming operation.
- Cutting Mechanism: The cutting mechanism is responsible for accurately cutting the square pipe to the desired length. It can utilize various cutting methods, such as shearing or sawing.
- Control System: The control system comprises electrical and electronic components that regulate and monitor the machine’s operations. It allows for precise control of speed, length measurement, and other parameters.
- Stacking System: The stacking system collects the finished square pipes and arranges them in an organized manner for easy handling and further processing.
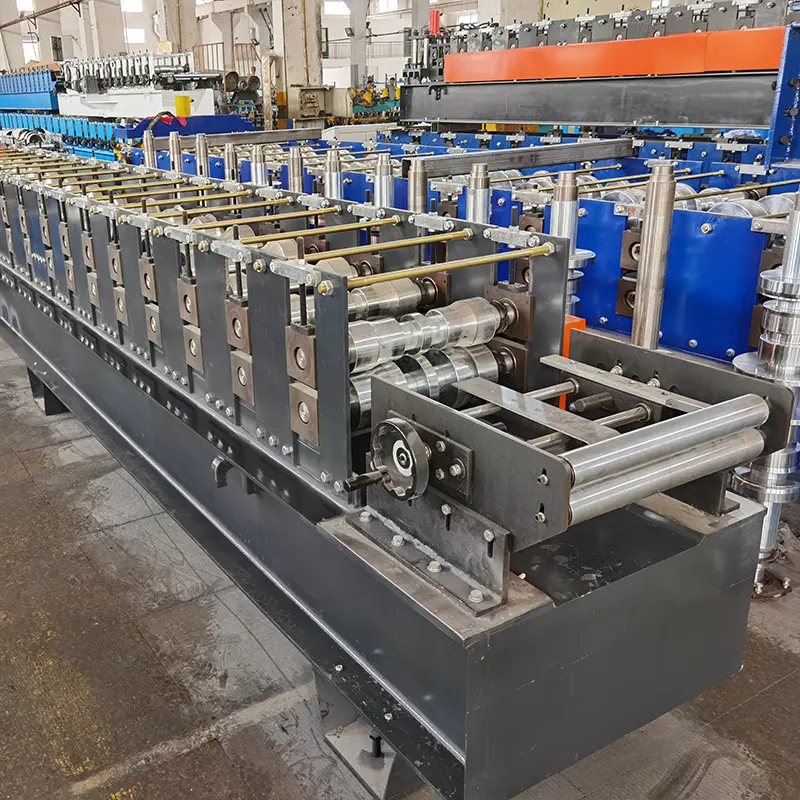
Factors to Consider When Choosing a Square Pipe Roll Forming Machine
When selecting a square pipe roll forming machine for your business, it’s essential to consider several factors to ensure you make the right choice. Here are some key considerations:
- Material Compatibility: Determine the type and thickness of the metal you plan to use for square pipe production. Ensure that the machine you choose can handle the specified material.
- Production Volume: Assess your production requirements in terms of the number of square pipes you need to produce per unit of time. Choose a machine that can meet your desired production volume.
- Customization Options: If you require the flexibility to produce square pipes of different dimensions, look for a machine that offers adjustable settings and tooling options.
- Machine Size and Space Requirements: Consider the available space in your facility and choose a machine size that fits within your production area without causing any constraints.
- Maintenance and Support: Inquire about the maintenance requirements of the machine and the availability of technical support from the manufacturer. Choose a reliable supplier with a good track record.
Maintenance and Care for Square Pipe Roll Forming Machines
Proper maintenance and care are crucial to ensure the longevity and optimal performance of your square pipe roll forming machine. Here are some maintenance practices to follow:
- Regular Cleaning: Keep the machine clean by removing dust, debris, and metal shavings. This prevents them from interfering with the machine’s moving parts and affecting its performance.
- Lubrication: Apply lubricating oil or grease to the machine’s bearings, gears, and other moving components as recommended by the manufacturer. This reduces friction and prevents premature wear.
- Routine Inspections: Regularly inspect the machine for any signs of wear, loose fasteners, or damaged parts. Replace or repair any faulty components to maintain the machine’s reliability and safety.
- Training and Operator Awareness: Ensure that the machine operators are properly trained on the operation and maintenance procedures. Promote awareness of safety protocols and best practices.
Troubleshooting Common Issues with Square Pipe Roll Forming Machines
While square pipe roll forming machines are designed for reliability, occasional issues may arise. Here are some common issues you may encounter with square pipe roll forming machines and possible troubleshooting steps:
- Uneven Bending: If the square pipes produced have inconsistent bending or irregular profiles, it may indicate a misalignment issue with the rollers. Check the alignment of the roller stations and adjust them if necessary.
- Material Jamming: If the metal strip gets stuck or jams during the roll forming process, it can disrupt production. Inspect the material feeding system for any obstructions or misfeeds. Clear any jams and ensure smooth material flow.
- Cutting Defects: Poor-quality cuts or inaccurate length measurements can result in defective square pipes. Check the cutting mechanism for any dull blades or misalignment. Sharpen or replace the blades if needed and recalibrate the length measurement system.
- Machine Vibrations: Excessive vibrations during operation can affect the quality of the square pipes. Inspect the machine’s foundation and support structure for stability. Tighten loose bolts and ensure proper leveling of the machine.
- Electrical Issues: If the machine experiences electrical problems, such as power fluctuations or control panel malfunctions, check the electrical connections and circuitry. Ensure all wiring is secure and consult a qualified electrician if needed.
- Excessive Noise: Unusual or excessive noise during operation may indicate worn-out bearings, gears, or other moving parts. Inspect the machine for signs of wear and replace any damaged components. Lubricate the moving parts as recommended.
If you encounter persistent issues that cannot be resolved through troubleshooting, it is advisable to contact the manufacturer or a qualified technician for assistance. Regular maintenance, timely repairs, and proper operator training can minimize the occurrence of problems and ensure smooth operation of your square pipe roll forming machine.
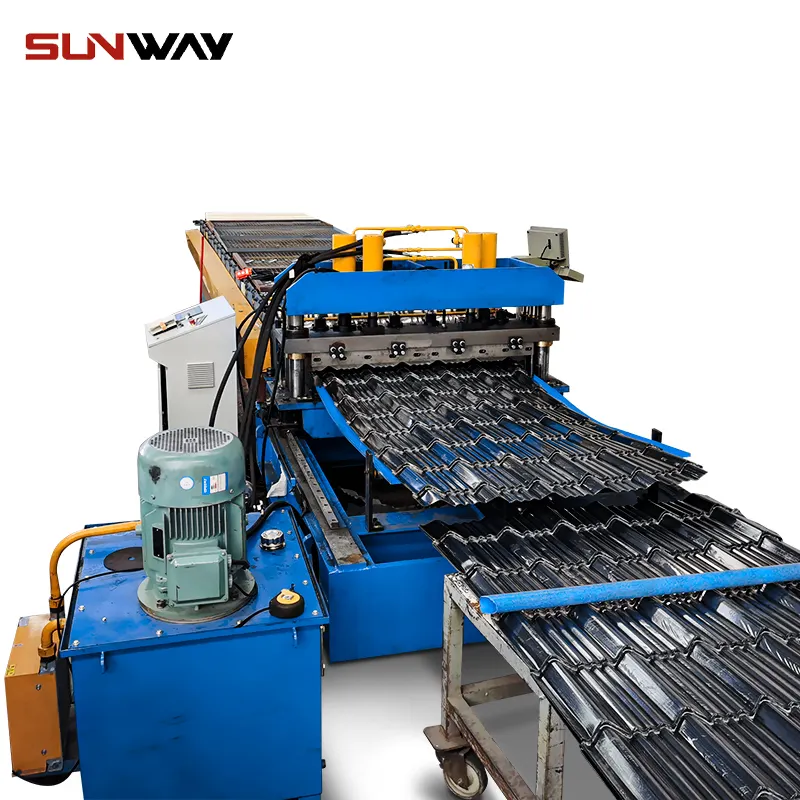
Tips for Optimal Performance of Square Pipe Roll Forming Machines
To maximize the performance and efficiency of your square pipe roll forming machine, consider the following tips:
- Regular Calibration: Periodically calibrate the machine to ensure accurate dimensions and precise bending. Verify the settings and make adjustments as needed to maintain consistent square pipe profiles.
- Quality Control: Implement a thorough quality control process to inspect the square pipes produced by the machine. Check for dimensional accuracy, surface finish, and any defects. This ensures that only high-quality products are delivered to your customers.
- Operator Training: Provide comprehensive training to the machine operators to familiarize them with the operation, maintenance, and safety procedures. Well-trained operators can identify and address issues promptly, reducing downtime and improving productivity.
- Optimize Material Usage: Optimize the material usage by minimizing waste and optimizing nesting patterns. Proper planning and programming can help maximize the number of square pipes produced from a given sheet of metal, reducing material costs.
- Continuous Monitoring: Regularly monitor the machine’s performance, including speed, tension, and alignment. Use sensors and monitoring systems to detect any deviations or abnormalities. Promptly address any issues to prevent further damage or production delays.
By implementing these tips, you can enhance the overall performance, reliability, and longevity of your square pipe roll forming machine, leading to increased productivity and customer satisfaction.
Safety Precautions for Operating a Square Pipe Roll Forming Machine
Operating a square pipe roll forming machine requires strict adherence to safety guidelines to protect the operators and maintain a safe working environment. Here are some essential safety precautions:
- Operator Protection: Ensure that the machine operators wear appropriate personal protective equipment (PPE) such as safety glasses, gloves, and hearing protection. Encourage the use of safety shoes and clothing to minimize the risk of injuries.
- Machine Guarding: Install safety guards and barriers around the moving parts, rollers, and cutting mechanisms of the machine. This prevents operators from accidental contact with hazardous areas during operation.
- Lockout/Tagout Procedures: Implement proper lockout/tagout procedures to isolate and de-energize the machine during maintenance or repair activities. Provide training on these procedures to all personnel involved.
- Emergency Stop Devices: Equip the machine with easily accessible emergency stop buttons or switches. Train operators on their location and proper usage to quickly stop the machine in case of an emergency.
- Risk Assessment: Conduct a thorough risk assessment of the machine and its operating environment. Identify potential hazards and implement appropriate control measures to mitigate the risks.
- Regular Maintenance: Keep the machine well-maintained and ensure that all safety features, such as interlocks and safety sensors, are functioning properly. Perform routine inspections and address any safety concerns promptly.
Remember, safety should always be a top priority when operating a square pipe roll forming machine. By following these precautions, you can create a safe and secure working environment for your operators and minimize the risk of accidents or injuries.
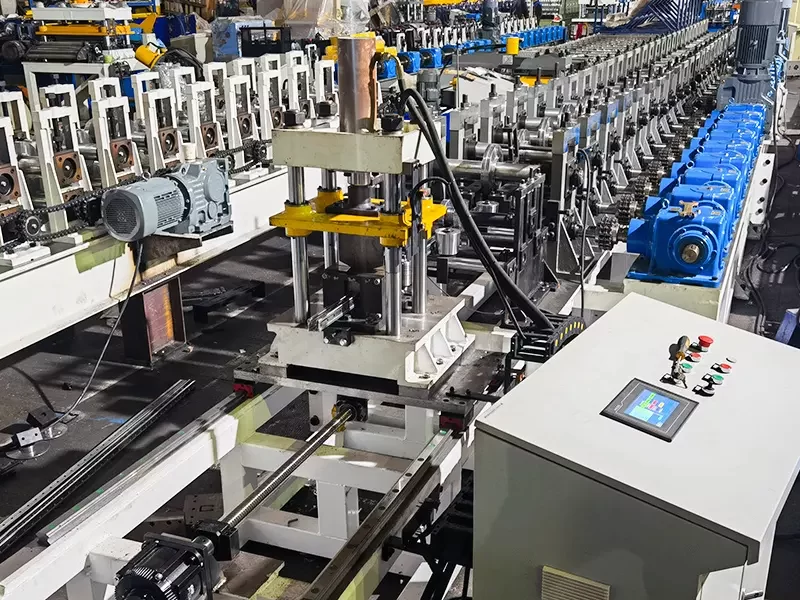
Future Trends in Square Pipe Roll Forming Technology
The field of square pipe roll forming continues to evolve, driven by technological advancements and industry demands. Here are some future trends to watch for:
- Automation and Integration: The integration of robotics and automation technologies will further enhance the efficiency and productivity of square pipe roll forming machines. Automated material handling, tool changing, and quality inspection systems will streamline the production process.
- Advanced Control Systems: Improved control systems with intuitive user interfaces and real-time monitoring capabilities will provide operators with enhanced control and visibility over the roll forming process. This will enable faster setup, easier troubleshooting, and improved production control.
- Advanced Material Handling: Innovations in material handling systems will enable seamless integration between different stages of the production line. This will minimize manual intervention, reduce material waste, and optimize overall production efficiency.
- Smart Manufacturing and Data Analytics: The implementation of smart manufacturing concepts, such as the Industrial Internet of Things (IIoT) and data analytics, will enable real-time monitoring, predictive maintenance, and data-driven decision-making. This will result in improved machine performance, reduced downtime, and better overall production optimization.
- Energy Efficiency: As sustainability becomes a crucial aspect of manufacturing, future square pipe roll forming machines will focus on energy-efficient operations. Integration of energy-saving technologies, such as regenerative braking and optimized motor controls, will reduce energy consumption and environmental impact.
These future trends indicate a promising future for square pipe roll forming technology, offering increased efficiency, productivity, and sustainability for the metal fabrication industry.
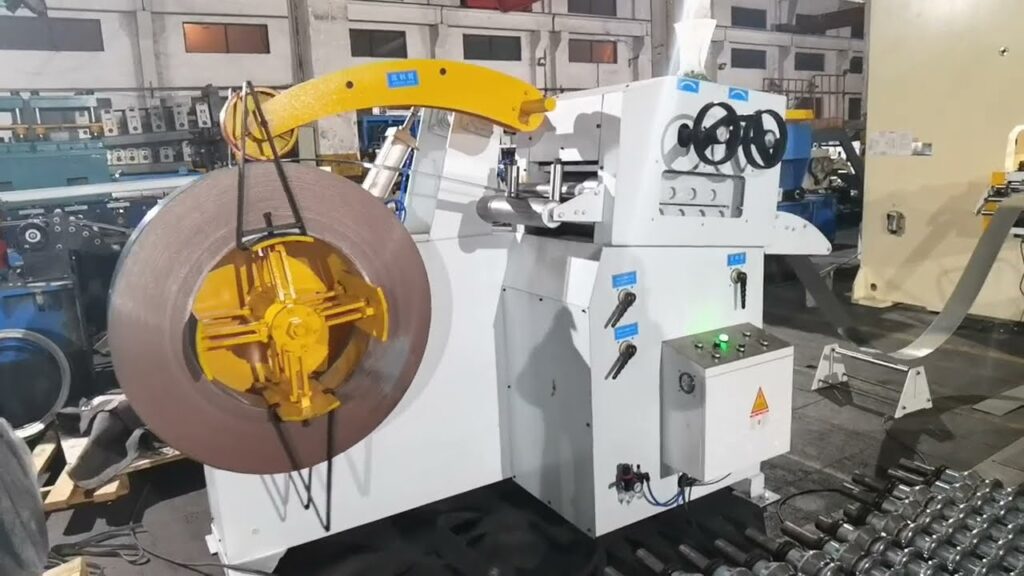
Conclusion
Square pipe roll forming machines have revolutionized the manufacturing process of square pipes, providing cost-effective, precise, and efficient production solutions. By understanding the benefits, working principles, key components, and maintenance requirements of these machines, you can make informed decisions and optimize their performance.
Remember to consider factors such as material compatibility, production volume, customization options, and maintenance requirements when choosing a square pipe roll forming machine. Regular maintenance, troubleshooting common issues, and implementing safety precautions are vital for safe and reliable operation.
As the industry continues to evolve, embracing future trends like automation, advanced control systems, and smart manufacturing will further enhance the capabilities and efficiency of square pipe roll forming machines.
By harnessing the power of square pipe roll forming technology, you can meet the growing demand for square pipes and gain a competitive edge in the metal fabrication industry.
FAQs
1. Is a square pipe roll forming machine suitable for producing other shapes besides square pipes?
While square pipe roll forming machines are primarily designed for square pipe production, they can often be customized or equipped with different tooling to produce other shapes, such as rectangular pipes or profiles.
2. What types of materials can be used with a square pipe roll forming machine?
A square pipe roll forming machine can work with various types of metals, including:
- Steel: Both mild steel and high-strength steel can be processed with a square pipe roll forming machine. Different grades and thicknesses of steel can be accommodated, allowing for versatility in manufacturing.
- Aluminum: Square pipes made from aluminum are lightweight, corrosion-resistant, and often used in applications where weight reduction is a priority, such as the aerospace industry.
- Stainless Steel: Stainless steel square pipes offer excellent corrosion resistance and durability, making them suitable for applications where hygiene, aesthetics, and strength are crucial, such as architectural and food processing industries.
- Copper: Copper square pipes find use in electrical and plumbing systems due to their excellent conductivity and resistance to corrosion.
It’s important to ensure that the square pipe roll forming machine you choose is compatible with the specific type and thickness of material you intend to use. This will help ensure optimal performance and product quality.
3. Can square pipe roll forming machines produce pipes of different sizes?
Yes, square pipe roll forming machines can be adjusted to produce square pipes of various sizes. The machine settings, including the position of the rollers, can be modified to achieve the desired dimensions. This flexibility allows for the production of square pipes with different side lengths and wall thicknesses to meet specific application requirements.
4. Are square pipe roll forming machines suitable for high-volume production?
Yes, square pipe roll forming machines are well-suited for high-volume production. Once properly set up and calibrated, these machines can operate continuously, producing square pipes at a rapid rate. Their automated feeding, forming, and cutting processes contribute to increased productivity and efficiency, making them ideal for meeting high-demand production needs.
5. Can square pipe roll forming machines be integrated into existing production lines?
Yes, square pipe roll forming machines can be integrated into existing production lines. They can be incorporated into a fully automated production system or used as a standalone machine depending on the specific requirements of the production process. Integration with material handling systems, quality control mechanisms, and downstream processing equipment can optimize the overall production flow and increase efficiency.