Introduction
In recent years, China has emerged as a leading player in the manufacturing industry, offering a wide range of machinery and equipment. One such machine that has gained popularity is the cold roll forming machine. In this article, we will explore the world of china cold roll forming machine, their working principles, advantages, applications, top manufacturers in China, cost considerations, maintenance tips, and emerging trends in the industry.
What is a Cold Roll Forming Machine?
A cold roll forming machine is a specialized equipment used in the metalworking industry to shape metal sheets into various profiles, such as channels, angles, tubes, and panels. It operates by gradually bending and forming a continuous strip of metal, usually in coil form, using a series of rolls and dies. The process is called “cold” roll forming because it is performed at room temperature, unlike hot roll forming which involves heating the metal.
How Does a Cold Roll Forming Machine Work?
The working principle of china cold roll forming machine involves several sequential steps. First, the coil of metal is fed into the machine and passed through a set of rollers. These rollers gradually shape the metal according to the desired profile. Each set of rollers is designed to perform a specific bending or forming operation.
As the metal moves through the machine, it undergoes a series of incremental transformations until it reaches the final shape. Various cutting, punching, and notching operations can be incorporated into the machine to create customized profiles. The entire process is automated and controlled by computer programs, ensuring precise and consistent results.

Advantages of Cold Roll Forming Machines
China cold roll forming machines offer numerous advantages over traditional metalworking methods. Some of the key benefits include:
- Versatility: China Cold Roll Forming Machines can produce a wide range of complex profiles, allowing for customization and flexibility in design.
- Cost-efficiency: The continuous production process of cold roll forming minimizes material waste and reduces labor costs. It also eliminates the need for secondary operations, such as welding or riveting.
- High precision: China cold roll forming machines provide excellent dimensional accuracy and repeatability, resulting in consistent and high-quality products.
- Time-saving: The automated nature of China Cold Roll Forming Machines ensures faster production rates and shorter lead times compared to manual methods.
- Material compatibility: Cold roll forming can be performed on various metals, including steel, aluminum, copper, and stainless steel, making it suitable for a wide range of applications.
Applications of Cold Roll Forming Machines
China cold roll forming machines find extensive use in several industries due to their versatility. Some common applications include:
- Construction: Cold roll formed profiles are widely used in the construction industry for applications such as roofing, cladding, framing, and partitioning systems.
- Automotive: The automotive sector utilizes cold roll forming machines to produce components like chassis parts, door frames, and structural reinforcements.
- Furniture: Cold roll formed metal profiles are employed in the manufacturing of furniture, such as shelves, drawers, and storage systems.
- Electrical and Electronics: China cold roll forming machines help create intricate profiles used in electrical cabinets, cable trays, and switchboards.
- Solar Energy: China Cold Roll Forming Machines play a crucial role in the production of solar panel frames and mounting systems.
- Agriculture: The agricultural sector utilizes cold roll formed profiles for applications like greenhouse structures, irrigation systems, and livestock housing.
- Transportation: China cold roll forming machines are involved in the manufacturing of transportation components like railings, handrails, and trailer frames.
- Appliances: The appliance industry utilizes cold roll formed profiles for the production of components like refrigerator shelves, oven racks, and ventilation systems.
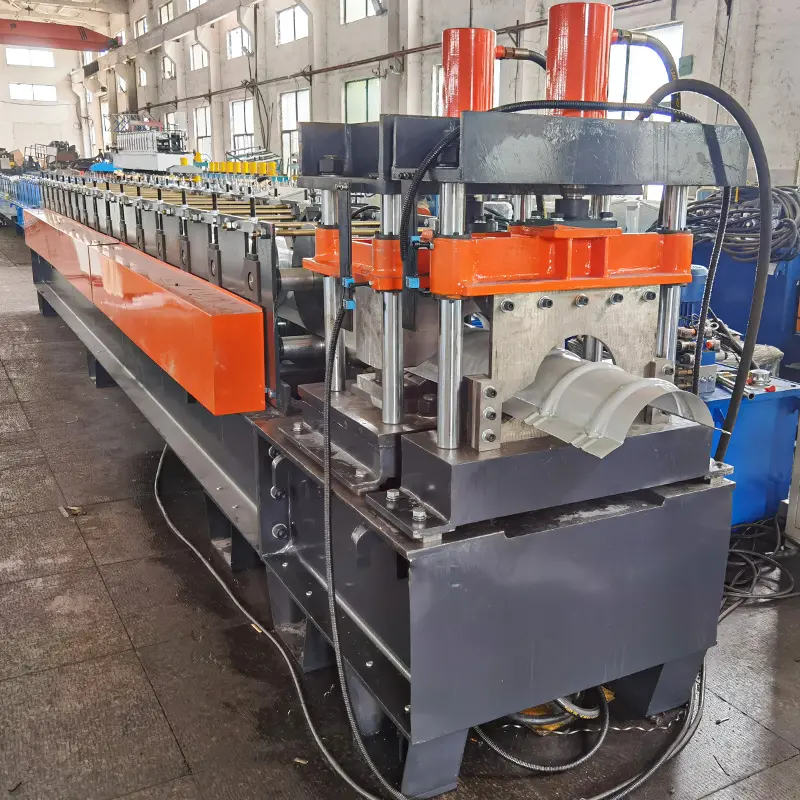
Factors to Consider When Choosing a Cold Roll Forming Machine
When selecting China Cold Roll Forming Machines, several factors need to be taken into account. These include:
- Profile Complexity: Determine the complexity of the profiles you intend to produce and ensure that the machine can handle the required customization and forming operations.
- Material Compatibility: Consider the types of materials you will be working with and ensure that the machine is compatible with those materials, whether it is steel, aluminum, or other metals.
- Production Speed: Assess the desired production speed and output requirements to ensure that the machine can meet your production demands.
- Machine Size and Space: Consider the available space in your facility and choose a machine that fits within the allocated area while allowing for smooth operation and maintenance.
- Quality and Precision: Evaluate the machine’s track record in delivering high-quality, precise profiles consistently.
- Maintenance and Support: Consider the availability of spare parts, maintenance requirements, and the reputation of the manufacturer in providing timely support and service.
Top Manufacturers of Cold Roll Forming Machines in China
China is known for its robust manufacturing industry, and several top manufacturers specialize in China Cold Roll Forming Machines. Some prominent companies in China that produce high-quality cold roll forming machines include:
- Company A: Known for its advanced technology and expertise in producing a wide range of China Cold Roll Forming Machines for various industries.
- Company B: Specializes in customized cold roll forming machines and provides comprehensive solutions tailored to specific customer requirements.
- Company C: Offers a diverse portfolio of China Cold Roll Forming Machines, known for their durability, precision, and efficiency.
- Company D: Known for its innovative approach and continuous research and development in the field of cold roll forming technology.
It is advisable to research and evaluate the capabilities, reputation, and customer reviews of these manufacturers to select the most suitable supplier for your specific needs.
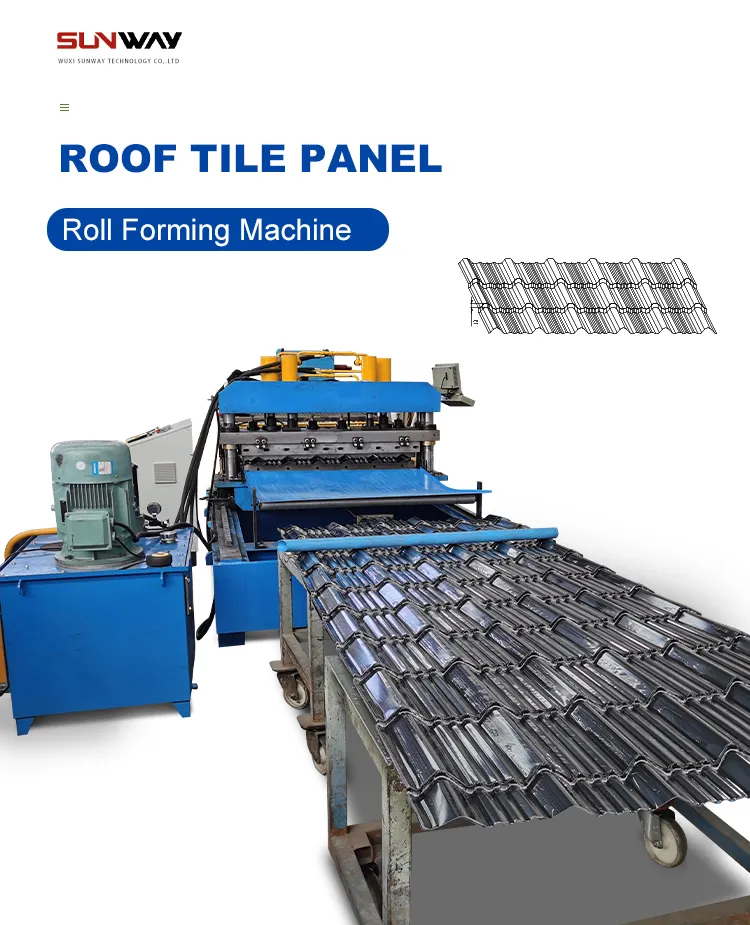
Cost of Cold Roll Forming Machines in China
The cost of China Cold Roll Forming Machines in China can vary depending on several factors, including the complexity of the machine, the desired features and customization, the brand reputation, and the level of automation. Generally, the price range for cold roll forming machines in China starts from a few thousand dollars and can go up to several hundred thousand dollars for high-end, fully automated systems.
It is essential to consider the long-term return on investment when assessing the cost of a cold roll forming machine. Factors such as productivity gains, reduced labor costs, material savings, and product quality should be taken into account to determine the overall value of the machine.
Maintenance and Troubleshooting of Cold Roll Forming Machines
To ensure optimal performance and longevity of China Cold Roll Forming Machines, proper maintenance is crucial. Here are some maintenance tips and troubleshooting guidelines:
- Regular Cleaning: Keep the machine clean from dust, debris, and metal shavings to prevent any interference with the operation.
- Lubrication: Follow the manufacturer’s guidelines for lubricating the machine’s moving parts to minimize friction and ensure smooth operation.
- Inspection and Adjustment: Periodically inspect the rolls, guides, and cutting mechanisms for any signs of wear or misalignment. Make necessary adjustments or replacements as needed.
- Operator Training: Provide adequate training to machine operators to ensure they understand the correct operation procedures, safety protocols, and troubleshooting techniques.
- Electrical and Mechanical Checks: Regularly inspect the electrical connections, sensors, and motors to identify any potential issues. Also, check belts, gears, and bearings for wear and tear.
- Calibration and Alignment: Periodically calibrate the machine to maintain accuracy and precision. Ensure that the rolls and dies are properly aligned to avoid any inconsistencies in profile formation.
- Preventive Maintenance Schedule: Establish a preventive maintenance schedule to conduct routine inspections, cleanings, and lubrications. This helps identify and address minor issues before they escalate into major problems.
- Troubleshooting: Familiarize yourself with common issues that may arise during machine operation, such as material jams, misfeeds, or irregular profile formations. Develop troubleshooting protocols and train operators to handle these situations effectively.
In case of complex issues or major breakdowns, it is recommended to seek assistance from qualified technicians or contact the manufacturer’s support team for expert guidance.
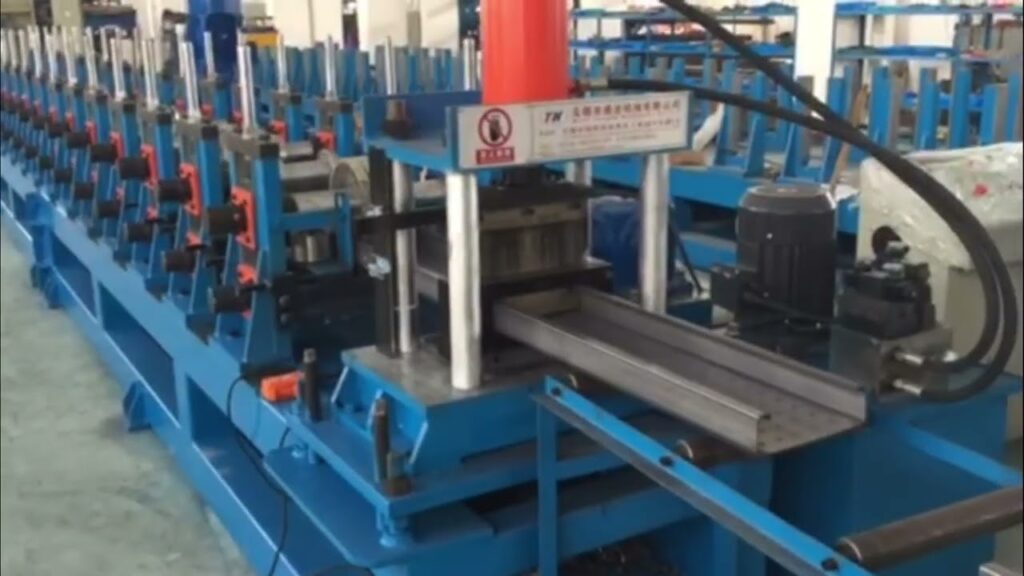
Emerging Trends in the Cold Roll Forming Machine Industry
The China Cold Roll Forming Machines industry continues to evolve with advancements in technology and market demands. Here are some emerging trends shaping the industry:
- Automation and Industry 4.0: China Cold Roll Forming Machines are becoming increasingly automated, integrating advanced robotics, artificial intelligence, and data analytics. This enables higher productivity, faster changeovers, and real-time monitoring for improved efficiency.
- Lightweight and Sustainable Solutions: With a growing focus on environmental sustainability, the industry is witnessing a shift towards lightweight materials and energy-efficient processes. China Cold Roll Forming Machines are adapting to accommodate these materials and support eco-friendly manufacturing practices.
- Customization and Flexibility: Customers are seeking highly customized profiles to meet their specific requirements. China Cold Roll Forming Machines are incorporating advanced software and tooling technologies to offer greater flexibility and faster changeovers, allowing for efficient production of diverse profiles.
- Integration with CAD/CAM Software: China Cold Roll Forming Machines are integrating with computer-aided design (CAD) and computer-aided manufacturing (CAM) software. This integration streamlines the design-to-production process, enhances accuracy, and reduces lead times.
- Remote Monitoring and Predictive Maintenance: Manufacturers are leveraging IoT (Internet of Things) capabilities to enable remote monitoring of machine performance and predictive maintenance. Real-time data analysis and condition monitoring help optimize machine uptime and prevent unplanned downtime.
- Energy Efficiency: China Cold Roll Forming Machines are incorporating energy-saving features, such as intelligent power management systems, regenerative braking, and optimized motor controls. These innovations contribute to reduced energy consumption and operational costs.
As the industry continues to evolve, staying abreast of these trends and embracing technological advancements will be crucial for manufacturers and businesses involved in cold roll forming.
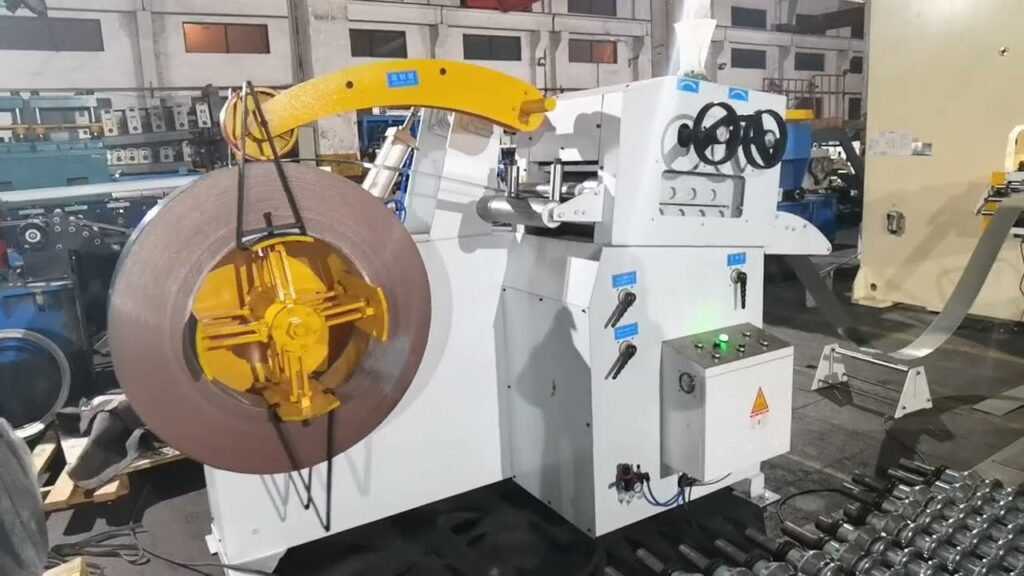
Conclusion
China has established itself as a significant player in the production of China Cold Roll Forming Machines. These machines offer numerous advantages, including versatility, cost-efficiency, high precision, and wide-ranging applications. When choosing a cold roll forming machine, factors like profile complexity, material compatibility, production speed, and maintenance support should be considered.
Top manufacturers in China specialize in producing high-quality China Cold Roll Forming Machines, catering to various industries. The cost of these machines varies depending on features, customization, and automation levels. Proper maintenance, regular inspections, and operator training are essential for optimal machine performance and longevity.
The cold roll forming machine industry is experiencing emerging trends such as automation, customization, lightweight solutions, and integration with advanced software. Embracing these trends will contribute to enhanced productivity, sustainability, and competitiveness in the market.
In summary, China’s cold roll forming machines offer tremendous potential for businesses seeking efficient and reliable solutions for metal profile manufacturing.
FAQs (Frequently Asked Questions)
- What is the difference between cold roll forming and hot roll forming? Cold roll forming is performed at room temperature, while hot roll forming involves heating the metal before shaping it. Cold roll forming offers advantages such as better dimensional accuracy, lower material waste, and the ability to work with a wider range of materials.
- Can cold roll forming machines produce complex profiles? Yes, cold roll forming machines are capable of producing complex profiles with high precision. They can be customized to create various shapes, angles, and sizes according to specific design requirements.
- What are the main industries that utilize cold roll forming machines? Cold roll forming machines find applications in industries such as construction, automotive, furniture, electrical and electronics, solar energy, agriculture, transportation, and appliances. They are used to manufacture components, structures, and systems specific to each industry.
- Are cold roll forming machines cost-effective? Yes, cold roll forming machines are considered cost-effective in the long run. They minimize material waste, reduce labor costs, and eliminate the need for additional processes like welding or riveting. The continuous production process and high precision of cold roll forming machines contribute to improved efficiency and overall cost savings.
- What maintenance is required for cold roll forming machines? Regular cleaning, lubrication, inspection of parts, operator training, and adherence to preventive maintenance schedules are essential for the proper functioning and longevity of cold roll forming machines. It is also important to address any troubleshooting issues promptly and seek professional assistance when needed.
- What are the emerging trends in the cold roll forming machine industry? Emerging trends in the industry include automation and Industry 4.0 integration, lightweight and sustainable solutions, customization and flexibility, integration with CAD/CAM software, remote monitoring and predictive maintenance, and energy efficiency measures. These trends aim to enhance productivity, reduce environmental impact, and improve overall machine performance.