Introduction
In the world of manufacturing and production, efficiency and precision are paramount. Industries such as construction, automotive, and electrical rely heavily on the ability to shape metal sheets into desired profiles quickly and accurately. This is where double layer cold roll forming machines come into play. This article explores the ins and outs of double layer cold roll forming machines, their benefits, working principles, components, applications, factors to consider when choosing one, and the maintenance required to ensure optimal performance.
What is a Double Layer Cold Roll Forming Machine?
A double layer cold roll forming machine is an advanced piece of equipment used in metalworking industries to transform flat metal sheets into desired profiles with a high degree of accuracy and efficiency. It is called a “double layer” machine because it has the capability to form two different profiles simultaneously, effectively doubling the productivity compared to single-layer machines.
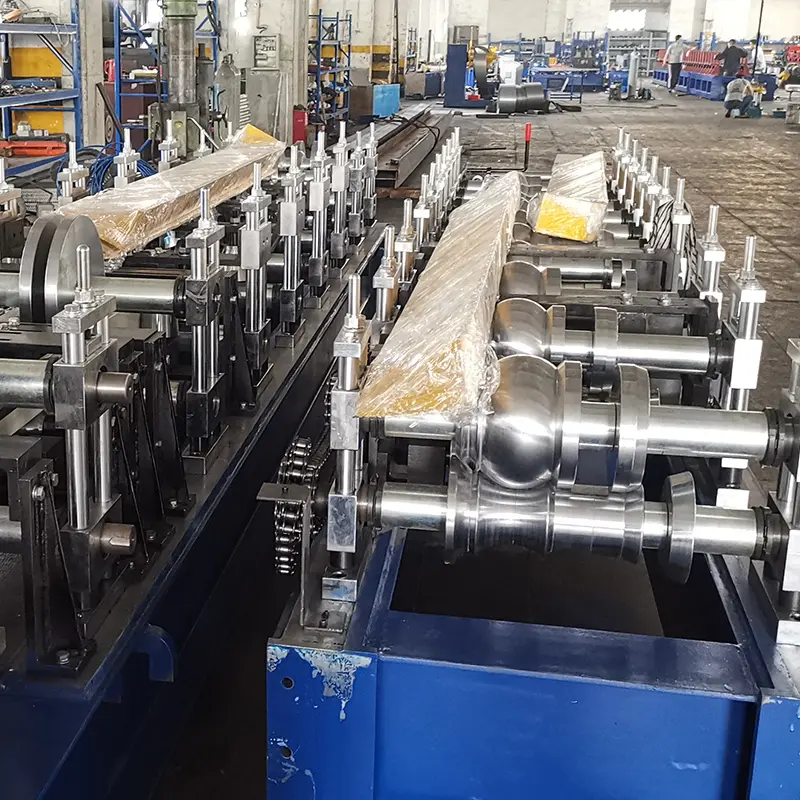
Benefits of Double Layer Cold Roll Forming Machine
Increased Efficiency and Productivity
One of the primary advantages of a double layer cold roll forming machine is its ability to significantly increase efficiency and productivity. By forming two different profiles simultaneously, it eliminates the need for separate machines or additional processes. This reduces production time, labor costs, and the risk of errors, resulting in a streamlined and more efficient manufacturing process.
Versatility in Design and Output
Double layer cold roll forming machines offer exceptional versatility in design and output. They can create a wide range of profiles, including complex and intricate shapes, with precise measurements. This flexibility enables manufacturers to meet various customer demands and adapt to changing market trends effectively.
Cost Savings
The cost savings associated with using a double layer cold roll forming machine are significant. With increased productivity and reduced labor requirements, manufacturers can lower production costs per unit. Furthermore, the precision and accuracy of the machine reduce material waste, minimizing material expenses. These cost-saving benefits ultimately contribute to improved profitability and competitiveness in the industry.
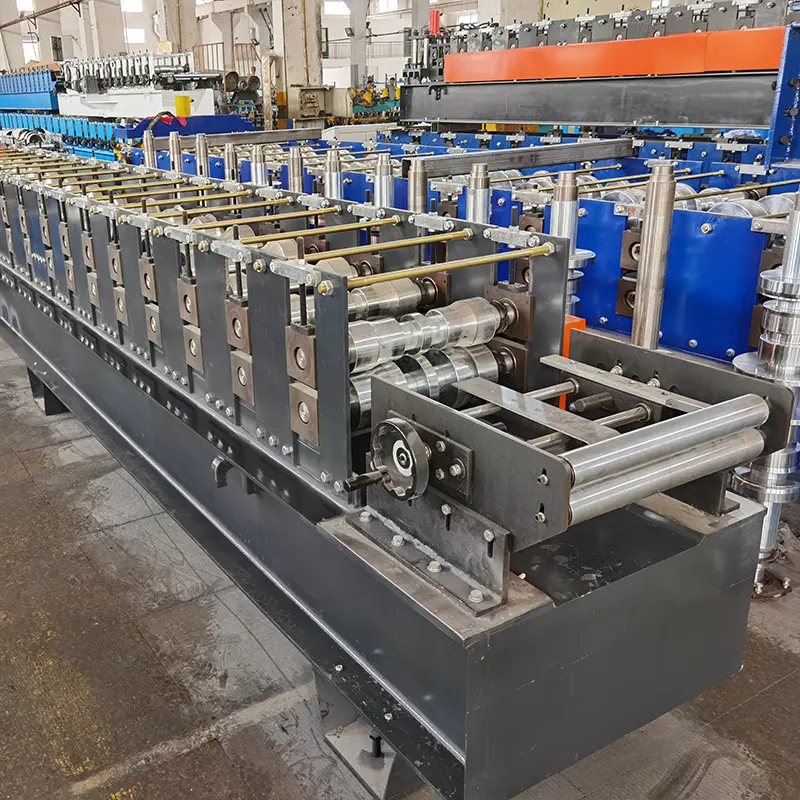
Working Principle of Double Layer Cold Roll Forming Machine
The working principle of a double layer cold roll forming machine involves several sequential processes. Initially, the metal sheets are fed into the machine through a feeding system. The roll forming system then gradually shapes the metal sheets into the desired profiles by passing them through a series of rolls. Finally, the cutting system cuts the formed profiles to the desired lengths, ready for further processing or assembly.
Components of Double Layer Cold Roll Forming Machine
A double layer cold roll forming machine consists of several essential components that work together to ensure smooth and efficient operation. These components include:
Feeding System
The feeding system is responsible for feeding the metal sheets into the machine consistently. It usually includes a decoiler, a leveling device, and a servo feeding system to ensure precise control of the material flow.
Roll Forming System
The roll forming system is the heart of the machine, where the metal sheets undergo shaping. It comprises a series of rolls and tooling sets that gradually bend and form the material into the desired profiles. The roll forming system is highly customizable, allowing manufacturers to create profiles of varying shapes and sizes.
Cutting System
The cutting system is responsible for cutting the formed profiles to the desired lengths. It typically employs a flying cutting technique or a hydraulic cutting system, ensuring accurate and clean cuts.
Control System
The control system acts as the brain of the double layer cold roll forming machine. It integrates various sensors, controllers, and software to monitor and control the machine’s operation. The control system allows operators to adjust parameters, set production parameters, and ensure the machine operates smoothly and safely.
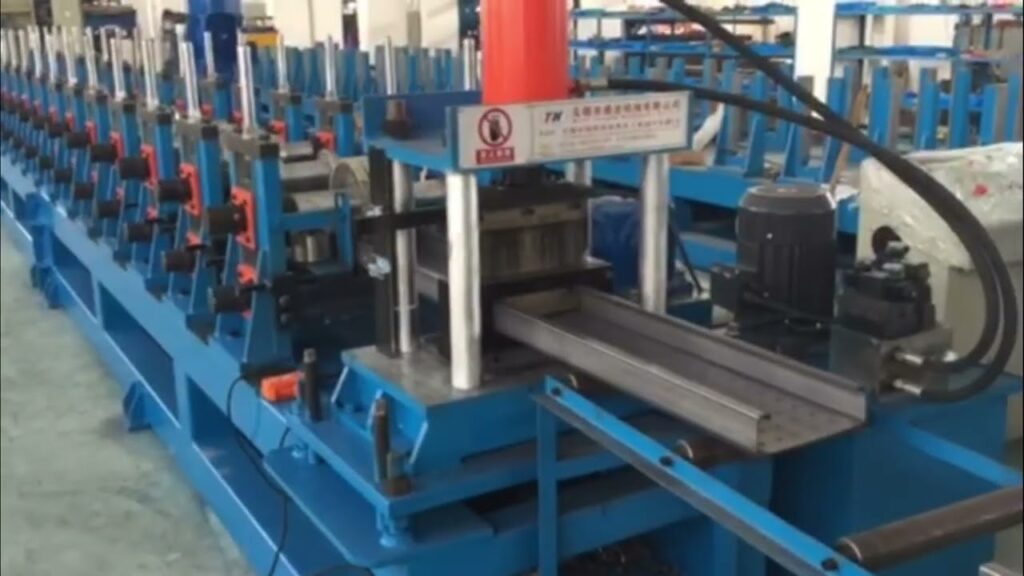
Applications of Double Layer Cold Roll Forming Machine
Double layer cold roll forming machines find applications in various industries due to their versatility and efficiency. Some of the common industries that benefit from this technology include:
Construction Industry
In the construction industry, double layer cold roll forming machines are used to manufacture roofing panels, wall cladding profiles, and structural components such as purlins and studs. These machines enable quick and precise production of metal profiles, contributing to efficient construction processes.
Automotive Industry
In the automotive industry, double layer cold roll forming machines play a crucial role in producing components like automotive body panels, door frames, and chassis members. The ability to create complex profiles with high precision ensures the structural integrity and aesthetic appeal of the vehicles.
Electrical Industry
The electrical industry benefits from double layer cold roll forming machines for manufacturing electrical enclosures, cable trays, and support systems. These machines enable the production of customized profiles that meet specific electrical requirements while maintaining cost-effectiveness.
Factors to Consider When Choosing a Double Layer Cold Roll Forming Machine
When selecting a double layer cold roll forming machine, several factors need to be taken into account to ensure optimal performance and value for money. These factors include:
Material Compatibility
Different machines may have varying material compatibility. It is essential to choose a machine that can handle the specific types and thicknesses of materials required for your production needs.
Machine Specifications
Consider the machine specifications such as roll forming speed, motor power, and dimensions to ensure they align with your production requirements. Assessing the maximum forming width and thickness capacity is crucial for accommodating the desired profiles.
Customization Options
Evaluate the machine’s flexibility in terms of profile design and customization. A good double layer cold roll forming machine should offer options for adjusting roll positions, tooling sets, and forming processes to meet the specific needs of your products.
Supplier Reputation and Support
Choose a reputable supplier with a track record of delivering reliable and high-quality machines. Additionally, ensure they provide excellent after-sales support, including training, maintenance services, and spare parts availability.
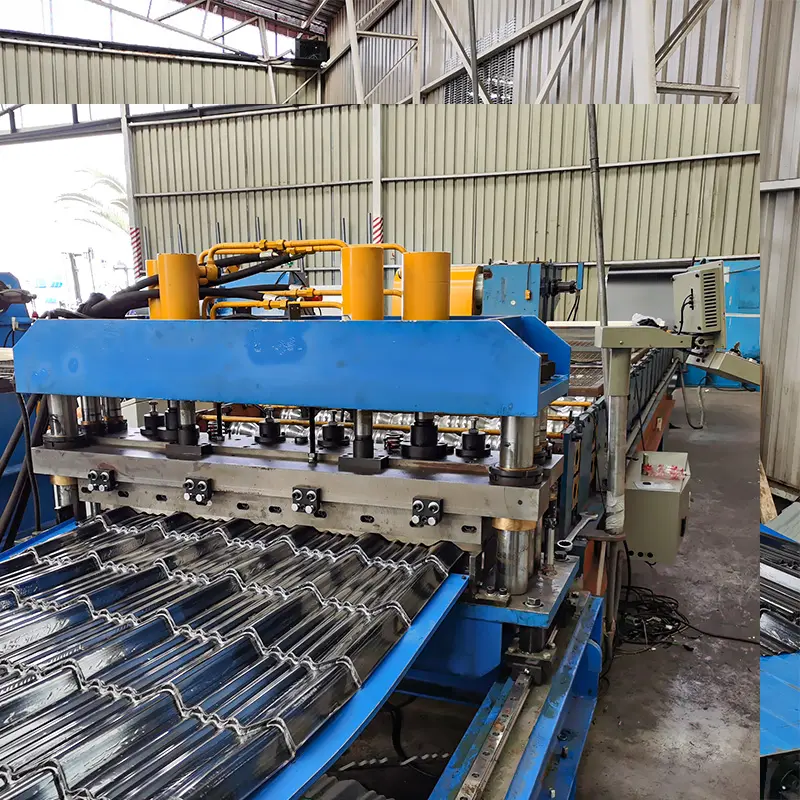
Maintenance and Care for Double Layer Cold Roll Forming Machine
To ensure the longevity and optimal performance of a double layer cold roll forming machine, regular maintenance and care are essential. Here are some key practices to follow:
Regular Cleaning and Lubrication
Regularly clean the machine to remove any debris or buildup that may affect its performance. Lubricate the moving parts and components according to the manufacturer’s recommendations to prevent friction and ensure smooth operation.
Inspection and Repairs
Conduct routine inspections to identify any signs of wear, damage, or misalignment. Promptly address any issues by repairing or replacing faulty components. This includes checking the rolls, cutting blades, drive system, and electrical connections.
Operator Training
Provide proper training to the operators to ensure they understand the machine’s operation and maintenance procedures. Educate them on safety protocols and best practices to prevent accidents and maximize efficiency.
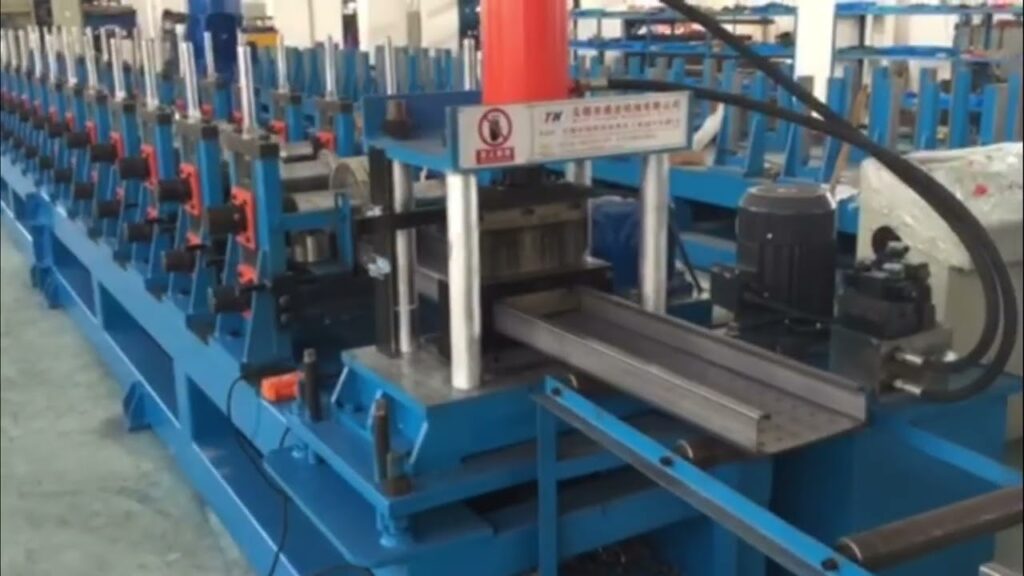
Conclusion
Double layer cold roll forming machines have revolutionized the metalworking industry by increasing efficiency, versatility, and precision. These machines offer numerous benefits, including improved productivity, cost savings, and the ability to create complex profiles. By understanding the working principles, components, applications, and factors to consider when choosing a machine, manufacturers can make informed decisions to optimize their production processes. Proper maintenance and care further contribute to the longevity and reliable performance of these machines, ensuring consistent quality output.
FAQs
Q1: Can a double layer cold roll forming machine produce profiles with different thicknesses?
Yes, double layer cold roll forming machines can handle different thicknesses of metal sheets, allowing for the production of profiles with varying thicknesses.
Q2: Is operator training necessary for using a double layer cold roll forming machine?
Yes, operator training is crucial to ensure safe and efficient operation of the machine. Training helps operators understand the machine’s functionality, maintenance procedures, and safety protocols.
Q3: Can a double layer cold roll forming machine be customized for specific profile designs?
Yes, double layer cold roll forming machines offer customization options to accommodate specific profile designs. These machines can be adjusted for roll positions, tooling sets, and forming processes to meet specific production requirements.
Q4: How often should a double layer cold roll forming machine be inspected for maintenance purposes?
Regular inspections should be conducted to identify any signs of wear, damage, or misalignment. The frequency of inspections may vary depending on the machine’s usage, but it is generally recommended to inspect the machine at least once every few months.
Q5: What are the key benefits of using a double layer cold roll forming machine in the construction industry?
Using a double layer cold roll forming machine in the construction industry offers benefits such as increased efficiency, faster production, precise shaping of roofing panels and wall cladding profiles, and the ability to manufacture structural components like purlins and studs. These machines contribute to streamlining construction processes and ensuring high-quality output.