Introduction
When it comes to the manufacturing of door panels, efficiency, precision, and customization are key factors. Door panel roll forming machines have revolutionized the production process by offering a highly efficient and automated solution. In this article, we will explore the world of door panel roll forming machines, their benefits, key components, operation, maintenance, and safety considerations.
Understanding Door Panel Roll Forming Machines
Door panel roll forming machines are specialized equipment designed to produce door panels with consistent dimensions and complex shapes. This process involves feeding a continuous strip of metal into the machine, which then passes through a series of rollers and gradually forms the desired shape of the door panel. The machine’s precision and speed ensure a high-quality output with minimal material waste.
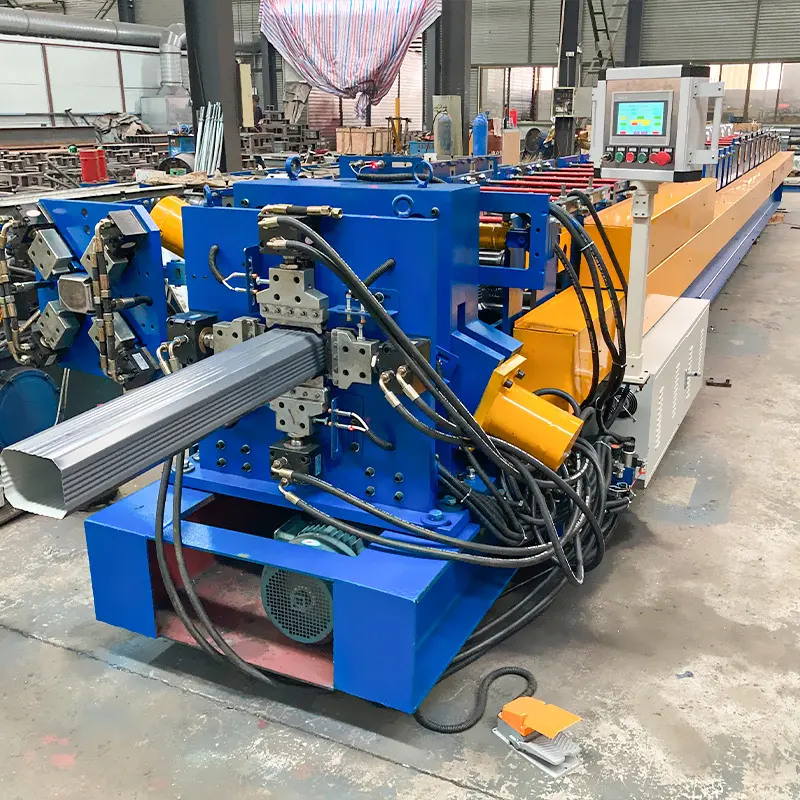
Benefits of Using Door Panel Roll Forming Machines
Using a door panel roll forming machine offers several advantages:
- Efficiency: Roll forming machines automate the production process, allowing for high-speed and continuous manufacturing of door panels. This significantly increases productivity and reduces labor costs.
- Customization: Door panel roll forming machines can be easily adjusted to produce door panels of different sizes, profiles, and designs. This versatility enables manufacturers to meet diverse customer demands.
- Consistency: Roll forming machines provide precise and consistent results, ensuring that every door panel produced meets the required specifications. This consistency enhances product quality and customer satisfaction.
- Material Savings: Roll forming machines optimize material usage, minimizing waste during the manufacturing process. This leads to cost savings and a more sustainable production approach.
- Time Savings: By automating the production process, roll forming machines reduce the time required to manufacture door panels. This enables manufacturers to meet tight deadlines and fulfill orders promptly.
Types of Door Panel Roll Forming Machines
There are two main types of door panel roll forming machines:
Single Station Roll Forming Machines
Single station roll forming machines are suitable for manufacturing door panels with simple shapes and limited design variations. The machine operates in a linear fashion, with each station performing a specific forming operation. While these machines offer lower initial investment costs, they are less flexible compared to continuous roll forming machines.
Continuous Roll Forming Machines
Continuous roll forming machines are designed for producing door panels with complex shapes and intricate designs. These machines have multiple stations, each performing a specific forming operation simultaneously. Continuous roll forming machines provide high production speeds, increased flexibility, and the ability to create door panels with various profiles and features.
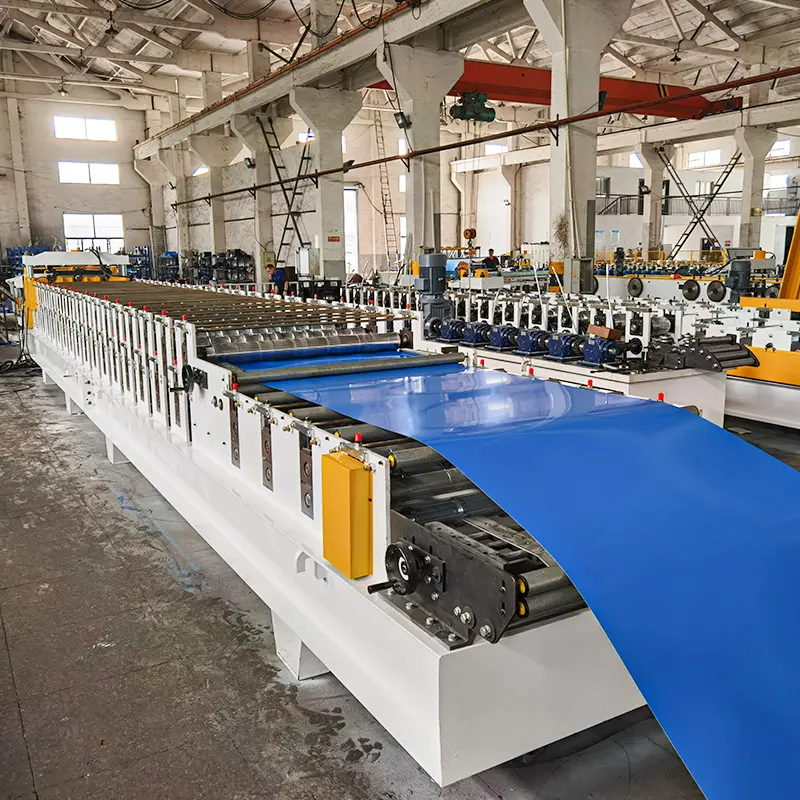
Key Components of a Door Panel Roll Forming Machine
A door panel roll forming machine consists of several key components:
Decoiler
The decoiler is responsible for holding and unwinding the coil of metal strip that will be fed into the machine. It ensures a continuous and smooth supply of material during the production process.
Roll Forming System
The roll forming system is the heart of the machine. It consists of a series of rollers that gradually shape the metal strip into the desired door panel profile. The rollers can be customized to achieve different panel designs.
Cutting System
The cutting system is responsible for accurately cutting the formed door panels to the desired length. It ensures clean and precise cuts, contributing to the overall quality of the finished products.
Control System
The control system of a door panel roll forming machine oversees and regulates the entire production process. It controls the speed, length, and accuracy of the machine’s operations, ensuring consistent and reliable output.
Stacking System
The stacking system collects and organizes the finished door panels, preparing them for further processing or packaging. It enhances efficiency by reducing the need for manual handling.
Factors to Consider When Choosing a Door Panel Roll Forming Machine
When selecting a door panel roll forming machine, consider the following factors:
Production Speed
The production speed of the machine determines how quickly you can manufacture door panels. Consider your production requirements and choose a machine that meets your desired output.
Flexibility
Look for a roll forming machine that offers flexibility in terms of profile and design changes. This allows you to adapt to evolving market demands and cater to various customer preferences.
Material Compatibility
Ensure that the machine can handle the specific type and thickness of metal strip required for your door panel production. Compatibility with different materials expands your range of manufacturing possibilities.
Machine Durability
Invest in a robust and durable roll forming machine that can withstand continuous operation and deliver consistent performance over time. Check the quality of materials used in its construction and inquire about its maintenance requirements.
Cost
Consider your budget and evaluate the long-term return on investment. Balance the machine’s capabilities and features with its cost to make an informed decision.
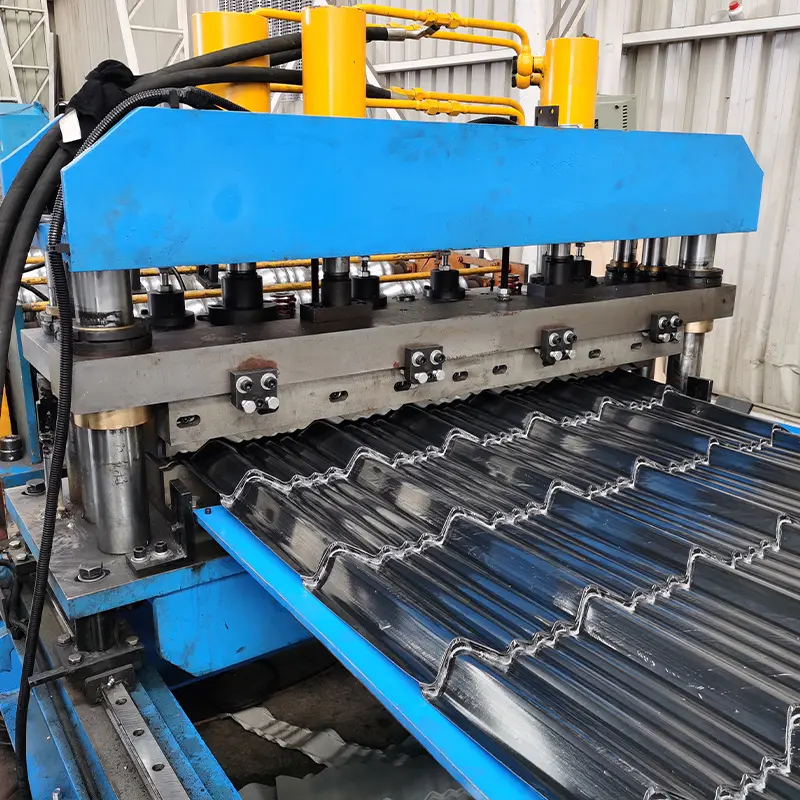
How to Operate a Door Panel Roll Forming Machine
Operating a door panel roll forming machine involves the following steps:
Set Up the Machine
Ensure that the machine is properly installed and securely anchored to the floor. Adjust the rollers and cutting system according to the desired door panel specifications.
Load the Material
Place the coil of metal strip onto the decoiler and thread the strip through the roll forming system. Ensure that the material is correctly aligned and free from any defects or debris.
Start the Machine
Power up the machine and initiate the roll forming process. Monitor the machine’s performance and make necessary adjustments to optimize the production output.
Monitor the Production Process
Regularly inspect the formed door panels as they pass through the roll forming system. Check for any irregularities, such as improper shaping or misalignment, and make adjustments as needed to maintain product quality.
Inspect the Output
Once the door panels are cut to the desired length, carefully examine them for any defects or imperfections. Ensure that the dimensions, shape, and surface finish meet the required specifications. Reject any panels that do not meet the quality standards.

Maintenance and Troubleshooting Tips for Door Panel Roll Forming Machines
To keep your door panel roll forming machine in optimal condition, follow these maintenance and troubleshooting guidelines:
Regular Maintenance
Implement a regular maintenance schedule for your machine. This includes cleaning, lubrication, and inspection of key components. Replace worn-out parts and address any issues promptly to prevent downtime.
Lubrication
Proper lubrication is crucial for smooth operation and prolonging the lifespan of your machine. Apply lubricants to the moving parts as recommended by the manufacturer.
Checking and Adjusting Alignment
Periodically check the alignment of the rollers, cutting system, and other components. Misalignment can result in uneven panel shaping or inaccurate cuts. Adjust and align the parts as necessary.
Common Troubleshooting Issues
Familiarize yourself with common issues that may arise during machine operation, such as material feed problems, roller slippage, or cutting system malfunctions. Troubleshoot these problems systematically and seek professional assistance if needed.
Safety Considerations for Door Panel Roll Forming Machines
Safety should be a top priority when operating a door panel roll forming machine. Consider the following safety measures:
Operator Safety
Provide proper training to machine operators on safe operating procedures, including material handling, machine setup, and emergency protocols. Ensure that operators wear appropriate personal protective equipment (PPE) and follow safety guidelines at all times.
Machine Safety
Install safety guards and devices to protect operators from potential hazards, such as moving parts, pinch points, or flying debris. Regularly inspect these safety features and repair or replace them as needed.
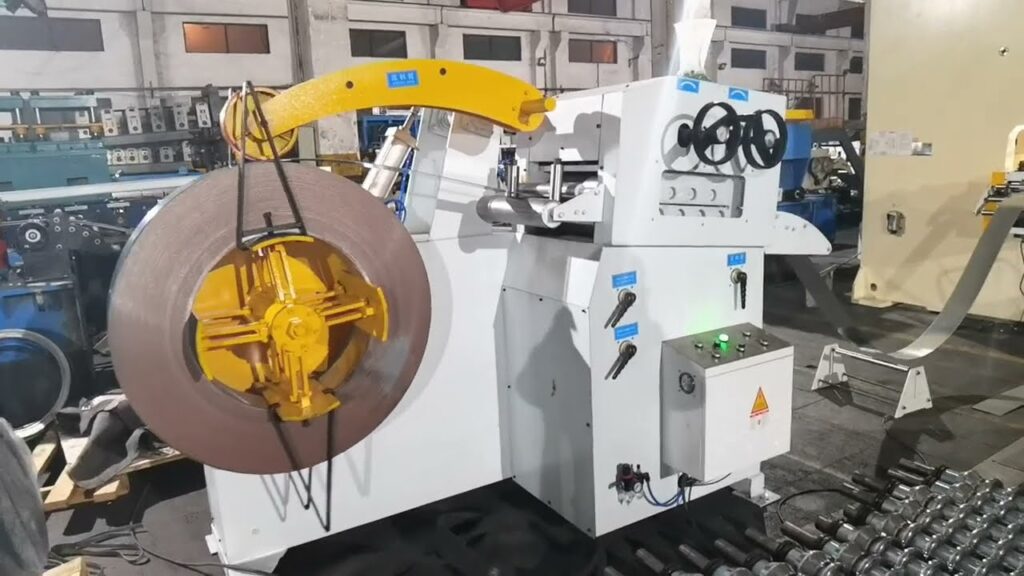
Applications of Door Panel Roll Forming Machines
Door panel roll forming machines find applications in various industries, including:
- Automotive: Manufacturing door panels for cars, trucks, and other vehicles.
- Construction: Producing door panels for residential and commercial buildings.
- Furniture: Creating customized door panels for cabinets, closets, and other furniture pieces.
- Appliances: Manufacturing door panels for refrigerators, ovens, and other household appliances.
The versatility of door panel roll forming machines makes them suitable for a wide range of applications, catering to different industries’ specific needs.
Future Trends and Innovations in Door Panel Roll Forming Machines
The field of roll forming technology is constantly evolving. Some future trends and innovations in door panel roll forming machines include:
- Advanced Control Systems: Integration of smart control systems that allow for real-time monitoring, data analysis, and predictive maintenance.
- Customization Capabilities: Further advancements in roll forming technology to enable more intricate and customized door panel designs.
- Material Innovation: Exploration of new materials and alloys that offer improved strength, durability, and aesthetic properties for door panels.
- Automation and Robotics: Continued integration of automation and robotics to enhance productivity, reduce labor requirements, and improve overall efficiency.
Manufacturers should stay informed about these trends and embrace technological advancements to stay competitive in the market.
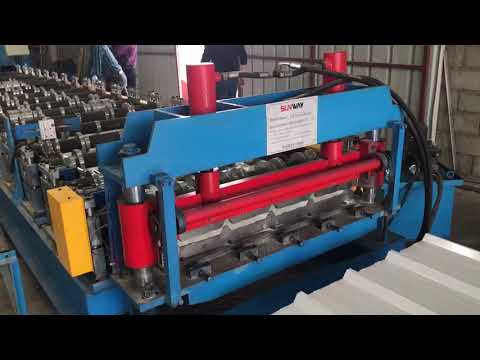
Conclusion
Door panel roll forming machines have revolutionized the production process of door panels, offering efficiency, customization, and consistent quality. By understanding the different types, key components, operation, and maintenance of these machines, manufacturers can optimize their production and meet customer demands effectively. Safety considerations and future trends should also be taken into account to ensure continuous improvement and success in the industry.
FAQs
Q1: Can door panel roll forming machines work with different types of metals? A: Yes, door panel roll forming machines can handle various types of metals, including steel, aluminum, and stainless steel. The machine’s design and specifications should be compatible with the specific material being used.
Q2: Are door panel roll forming machines suitable for small-scale production? A: Yes, door panel roll forming machines can be used for small-scale production. The machine’s flexibility allows for efficient production runs of varying sizes, making it suitable for both large and small manufacturing operations.
Q3: How long does it take to set up a door panel roll forming machine? A: The setup time for a door panel roll forming machine depends on the complexity of the door panel design and the operator’s familiarity with the machine. With proper training and experience, the setup process can be completed within a reasonable timeframe.
Q4: What are the main maintenance requirements for a door panel roll forming machine? A: Regular cleaning, lubrication, and inspection of key components are essential for the maintenance of a door panel roll forming machine. Additionally, addressing any issues or malfunctions promptly and replacing worn-out parts are necessary to keep the machine in optimal condition.
Q5: Can door panel roll forming machines produce door panels of different thicknesses? A: Yes, door panel roll forming machines can be adjusted to accommodate different thicknesses of metal strip. This allows manufacturers to produce door panels with varying strength and structural properties based on their specific requirements.