Introduction
In the realm of metal profile manufacturing, efficiency, precision, and cost-effectiveness are paramount. To meet these demands, the C channel roll forming machine has emerged as an invaluable tool. This article delves into the world of C channel roll forming machines, exploring their functionality, applications, advantages, and considerations when choosing one.
What is a C Channel Roll Forming Machine?
A C channel roll forming machine is a specialized equipment used for shaping metal coils into C-shaped profiles with consistent dimensions. This machine utilizes a continuous bending process that gradually forms the metal sheet into the desired profile. The resulting C channel profiles find applications in various industries, including construction, automotive, and electrical sectors.
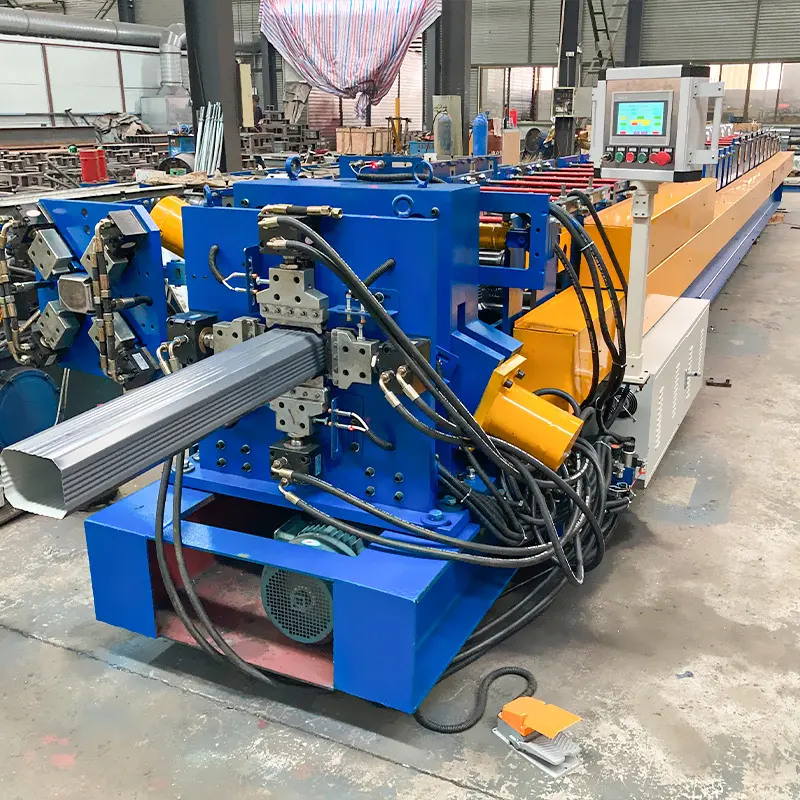
Applications of C Channel Roll Forming Machines
Construction Industry
In the construction industry, C channel profiles play a vital role in structural applications. These profiles are widely used for framing buildings, supporting roof panels, manufacturing window frames, and creating durable and reliable structures. The versatility of C channel profiles makes them a popular choice in construction projects of all scales.
Automotive Industry
The automotive industry benefits greatly from C channel roll forming machines. These machines can produce C channel profiles used in manufacturing car frames, chassis, door frames, and other structural components. The precise dimensions and consistent quality achieved by roll forming machines make them ideal for automotive applications where safety and reliability are paramount.
Electrical Industry
The electrical industry relies on C channel profiles for cable management and support systems. These profiles are utilized in the construction of cable trays, ladder racks, and other electrical infrastructure. C channel roll forming machines enable the production of profiles with precise dimensions, ensuring compatibility with electrical components and ease of installation.
Advantages of Using C Channel Roll Forming Machines
Cost Efficiency
One of the significant advantages of utilizing a C channel roll forming machine is its cost efficiency. By utilizing continuous bending and forming processes, these machines minimize material waste. The ability to produce consistent profiles in high volumes also leads to cost savings, reducing the need for manual labor and additional machining processes.
Precision and Consistency
C channel roll forming machines excel in delivering precise and consistent profiles. The automated process ensures that each profile adheres to the required dimensions and specifications. This high level of precision is critical for industries such as construction and automotive, where compatibility and structural integrity are vital.
Versatility
C channel roll forming machines offer versatility in profile design and material compatibility. With adjustable tooling and customization options, these machines can produce a wide range of C channel profiles to meet specific project requirements. Additionally, they can handle various materials, including steel, aluminum, and other alloys, further expanding their application potential.
Time-saving
Efficiency and speed are key advantages of C channel roll forming machines. These machines can produce profiles at a rapid pace, allowing for increased productivity and shorter lead times. The automated process reduces the need for manual intervention, streamlining production and minimizing downtime.
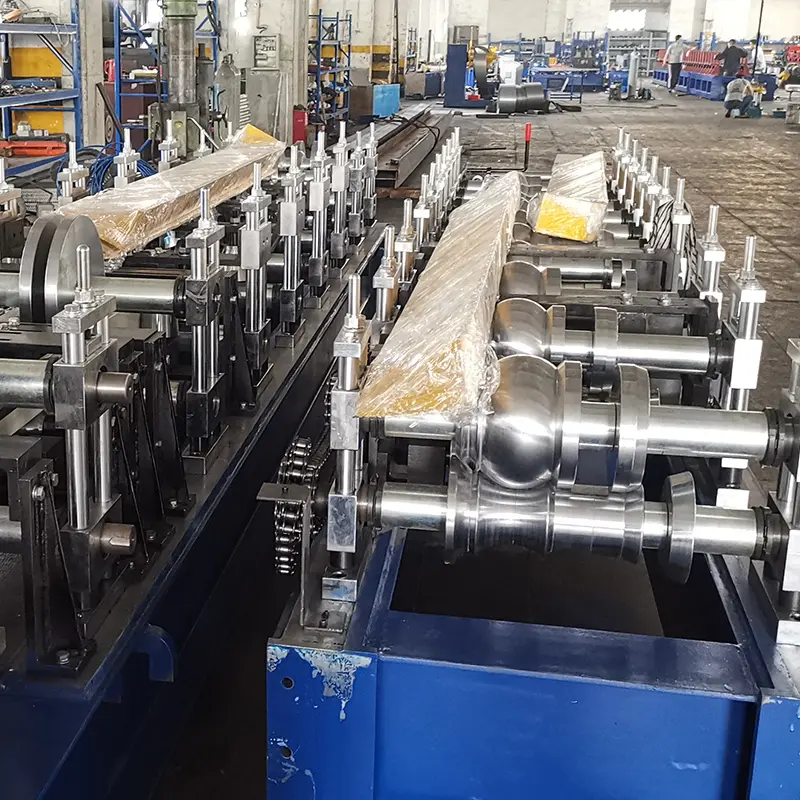
Factors to Consider When Choosing a C Channel Roll Forming Machine
Machine Size and Capacity
When selecting a C channel roll forming machine, it is essential to consider its size and capacity. The machine should be able to accommodate the required width and thickness of the metal coil. Additionally, it is crucial to ensure that the machine can handle the desired production volume without compromising quality.
Material Compatibility
Different projects may require the use of various materials, such as steel or aluminum. It is important to choose a roll forming machine that can handle the specific material required for the application. The machine should have the necessary tooling and adjustments to work with the desired material effectively.
Customization Options
Flexibility in profile design is often crucial for meeting specific project requirements. A C channel roll forming machine with customization options allows for the production of unique profiles with varying dimensions and features. Look for machines that offer adjustable tooling and easy reconfiguration for efficient customization.
Production Speed
The production speed of a roll forming machine is a vital consideration, particularly for high-volume projects. The machine should be capable of meeting the required production output without compromising quality. It is essential to assess the speed capabilities of different machines and select one that aligns with the project’s timeline.
Durability and Maintenance
Investing in a durable and reliable C channel roll forming machine is crucial for long-term productivity. Consider the machine’s build quality, materials used, and reputation of the manufacturer. Additionally, it is essential to understand the maintenance requirements of the machine and ensure that proper support and spare parts availability are provided.
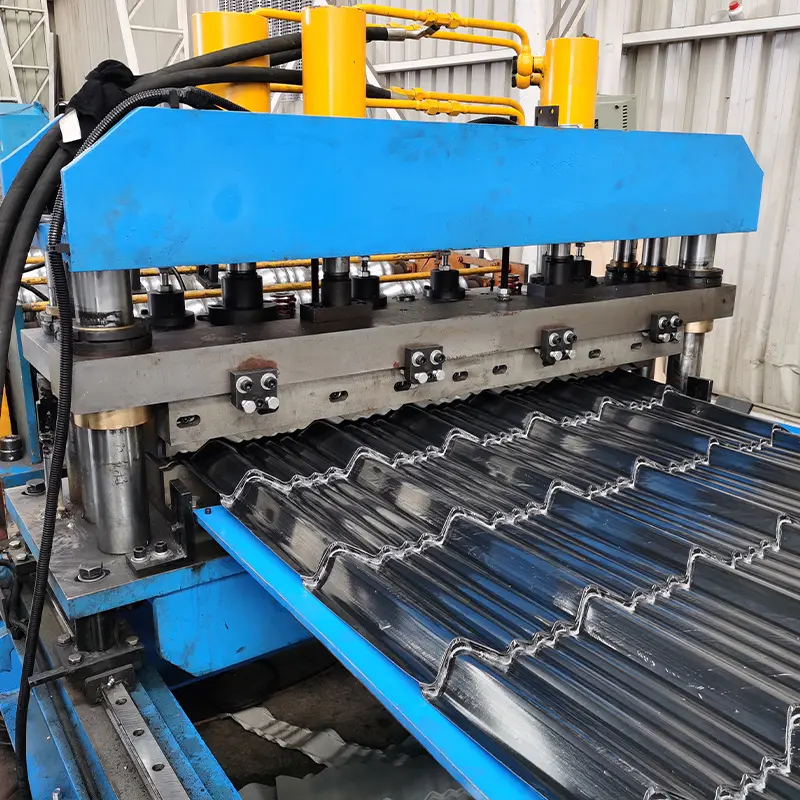
How Does a C Channel Roll Forming Machine Work?
C channel roll forming machines operate through a continuous process that transforms metal coils into C-shaped profiles. The process starts with an uncoiler that feeds the metal coil into the machine. The metal strip then passes through a series of rollers and forming stations, each performing a specific bending or shaping operation. Gradually, the metal strip takes the shape of a C channel profile. Finally, a cutting mechanism trims the profile to the desired length, and the finished profile is collected.
Maintenance and Troubleshooting Tips for C Channel Roll Forming Machines
To ensure optimal performance and longevity of a C channel roll forming machine, regular maintenance is essential. Some maintenance tips include:
- Regular lubrication of moving parts to prevent friction and wear.
- Routine inspection and adjustment of the machine’s alignment.
- Cleaning the machine regularly to remove debris and prevent build-up.
- Periodic inspection and replacement of worn-out tooling and components.
- Training operators on proper machine operation and safety protocols.
In the event of any issues or malfunctions, it is advisable to consult the manufacturer’s manual or seek professional assistance for troubleshooting and repairs.
Common Questions about C Channel Roll Forming Machines
What is the typical price range for a C channel roll forming machine?
The price of a C channel roll forming machine can vary depending on factors such as size, capacity, customization options, and the manufacturer. Generally, the price range for a standard C channel roll forming machine starts from a few thousand dollars and can go up to several hundred thousand dollars for larger, more advanced models. It is recommended to obtain quotes from multiple suppliers and consider the specific requirements of your project before making a purchasing decision.
Can a C channel roll forming machine be used for other profiles?
While C channel roll forming machines are primarily designed for producing C-shaped profiles, many models offer flexibility to produce other profiles as well. By adjusting the tooling and settings, these machines can be utilized to manufacture U channels, hat channels, Z channels, and various other profiles. It is essential to check the capabilities and customization options of the specific machine to determine its suitability for producing other profiles.
How long does it take to set up and start using a C channel roll forming machine?
The setup time for a C channel roll forming machine can vary depending on the complexity of the machine, operator expertise, and familiarity with the specific model. Generally, it involves adjusting the tooling, configuring the machine for the desired profile dimensions, and ensuring proper material feed and alignment. The setup process can take a few hours to a full day, depending on the complexity. Once set up, the machine is ready for production, and the time it takes to start using the machine depends on the operator’s proficiency and the specific project requirements.
Are C channel roll forming machines easy to operate?
C channel roll forming machines are designed with user-friendly interfaces and automation features to simplify operation. While there may be a learning curve initially, operators can quickly grasp the machine’s operation with proper training and practice. The ease of operation also depends on the machine’s complexity and the operator’s familiarity with roll forming technology. Manufacturers often provide training and support to ensure operators have the necessary knowledge to operate the machine effectively and safely.
What safety precautions should be taken when using a C channel roll forming machine?
Safety is of utmost importance when operating any machinery, including C channel roll forming machines. Some key safety precautions to consider include:
- Ensuring operators receive comprehensive training on machine operation and safety protocols.
- Providing appropriate personal protective equipment (PPE) such as safety glasses, gloves, and ear protection.
- Regularly inspecting the machine for any signs of wear or damage and addressing any issues promptly.
- Adhering to proper lockout/tagout procedures when performing maintenance or adjustments on the machine.
- Implementing safety guards and emergency stop buttons to prevent accidents and quickly halt machine operation if needed.
- Maintaining a clean and organized workspace to minimize potential hazards.
By following these safety precautions and promoting a safety-conscious culture, operators can minimize risks and ensure a safe working environment.
Conclusion
C channel roll forming machines have revolutionized the metal profile manufacturing industry, providing efficiency, precision, and cost-effectiveness. These machines offer numerous advantages, including cost savings, consistency, versatility, and time efficiency. When selecting a C channel roll forming machine, factors such as size, material compatibility, customization options, production speed, durability, and maintenance requirements should be considered. Understanding the working principle and maintenance tips ensures optimal performance and longevity. By harnessing the capabilities of C channel roll forming machines, industries can meet their metal profile manufacturing needs with confidence.
FAQs
Q1: What is the typical price range for a C channel roll forming machine?
The price range for a C channel roll forming machine can vary from a few thousand dollars to several hundred thousand dollars, depending on factors like size, capacity, and customization options.
Q2: Can a C channel roll forming machine be used for other profiles?
Yes, many C channel roll forming machines offer flexibility to produce various profiles by adjusting the tooling and settings.
Q3: How long does it take to set up and start using a C channel roll forming machine?
The setup time can range from a few hours to a full day, depending on the complexity of the machine and operator expertise.
Q4: Are C channel roll forming machines easy to operate?
C channel roll forming machines are designed with user-friendly interfaces and automation features, making them relatively easy to operate with proper training and practice.
Q5: What safety precautions should be taken when using a C channel roll forming machine?
Operators should receive comprehensive training, use appropriate PPE, perform regular machine inspections, and adhere to safety protocols to ensure a safe working environment.