Introduction
The construction industry is constantly evolving, seeking innovative solutions to enhance efficiency and productivity. Among the many advancements, the purlin roll forming machine stands out as a valuable tool for manufacturing high-quality purlins. This article explores the features, benefits, working principles, applications, and maintenance of purlin roll forming machines.
What is a Purlin Roll Forming Machine?
A purlin roll forming machines is a specialized piece of equipment designed to produce purlins with consistent shape, size, and quality. Purlins are structural components used in roof and wall systems to provide support and stability. These machines automate the process of roll forming, which involves feeding metal coils into the machine, passing them through a series of rolls, and shaping them into the desired profile.
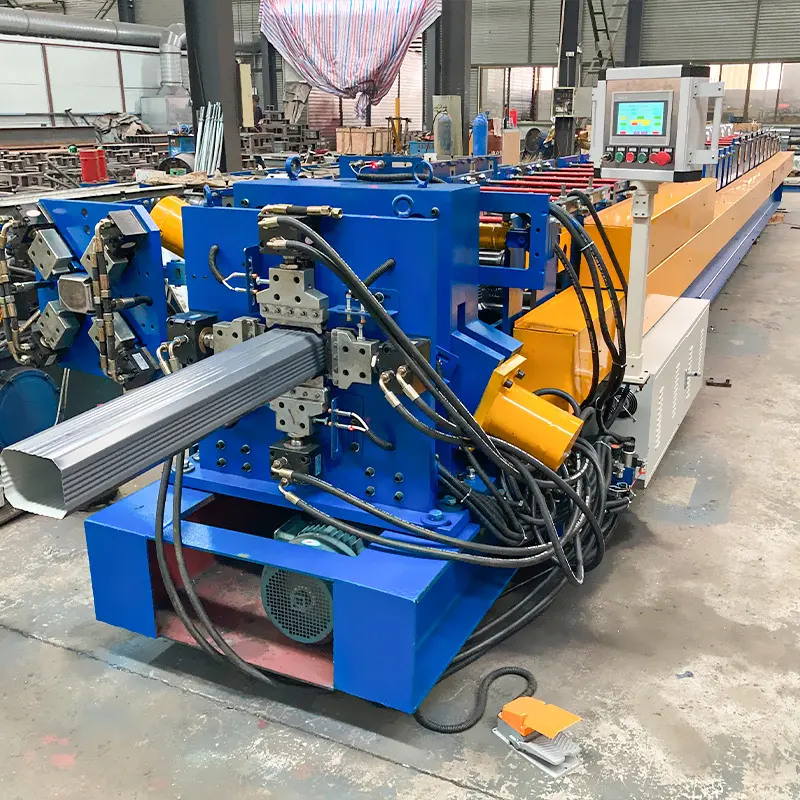
Benefits of Using a Purlin Roll Forming Machine
Utilizing a purlin roll forming machines offers several advantages for construction and manufacturing purposes. Firstly, it significantly improves efficiency by automating the production process, reducing manual labor, and increasing output. The machine’s high-speed operation allows for quick production cycles and faster project completion.
Secondly, purlin roll forming machines ensure consistent quality. The precision and accuracy of the machine’s rollers guarantee that each purlin produced adheres to the required specifications. This eliminates variations in size, shape, and strength, ensuring reliable and predictable results.
Another benefit is the flexibility and customization options provided by purlin roll forming machines. They can accommodate various material thicknesses and widths, allowing for the production of different purlin sizes and profiles. Additionally, manufacturers can incorporate specific design features to meet their customers’ unique requirements.
Types of Purlin Roll Forming Machines
Purlin roll forming machines come in different types to cater to specific purlin profiles. Some common variations include:
Single C Purlin Roll Forming Machine
The single C purlin roll forming machine is designed to produce C-shaped purlins, which have a single curve resembling the letter “C.” These purlins are commonly used in roof and wall systems for lightweight construction projects.
Double C Purlin Roll Forming Machine
The double C purlin roll forming machine is similar to the single C purlin machine but produces double C-shaped purlins. Double C purlins offer increased load-bearing capacity and are often used in larger-scale industrial and commercial buildings.
Z Purlin Roll Forming Machine
Z purlin roll forming machines are used to manufacture Z-shaped purlins. Z purlins have a unique shape with two flanges connected by a web in the middle. They are widely used in roofing systems due to their strength and stability.
Sigma Purlin Roll Forming Machine
The sigma purlin roll forming machine is designed specifically for producing sigma-shaped purlins. Sigma purlins are characterized by a “Σ” shape and are commonly used in structural applications where higher load-bearing capacity is required.
Other Variations
Apart from the aforementioned types, there are other variations of purlin roll forming machines available in the market, each catering to specific profile requirements. These variations include custom purlin roll forming machines that can produce unique shapes and sizes according to the customer’s needs.
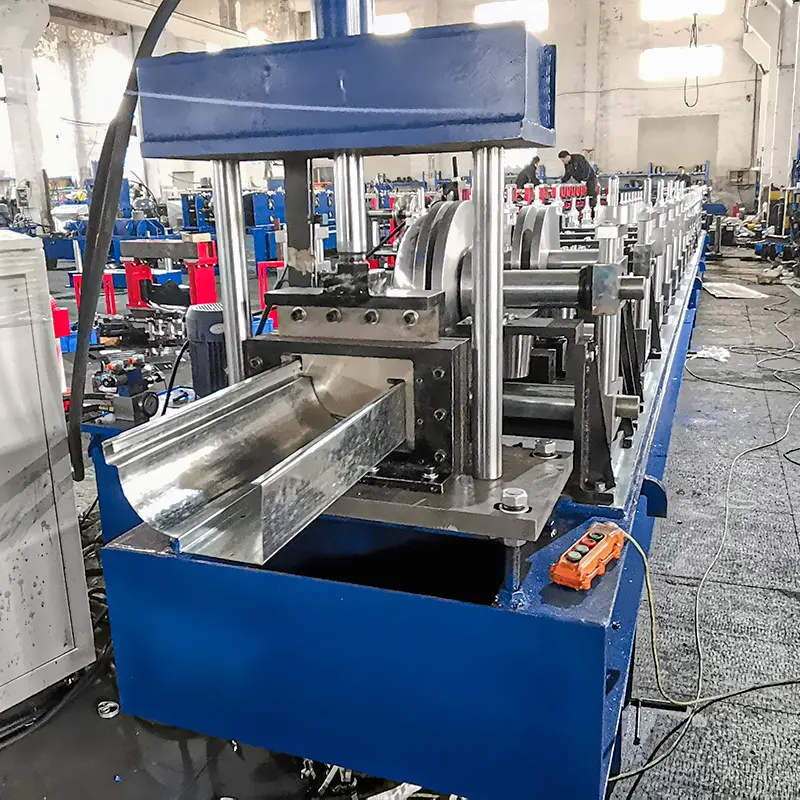
How Does a Purlin Roll Forming Machine Work?
Purlin roll forming machines operate on a continuous process. The machine starts by uncoiling the metal coil, which is then fed into the machine’s entry section. The metal strip passes through a series of rolls, each designed to gradually shape it into the desired purlin profile.
The rolls exert precise pressure and bending force on the metal strip, gradually forming it into the required shape. The machine’s cutting system then trims the purlin to the desired length. Finally, the finished purlins are stacked or conveyed for further processing or packaging.
Features to Consider When Choosing a Purlin Roll Forming Machine
When selecting a purlin roll forming machine, it is essential to consider various features to ensure it meets your specific requirements. Here are some key factors to evaluate:
Material Thickness and Width
The machine should be capable of handling the desired material thickness and width. Different projects may require different material specifications, so it is crucial to choose a machine that can accommodate those variations.
Speed and Production Capacity
The machine’s speed and production capacity determine the output it can deliver. Consider the required production volume and choose a machine that can meet or exceed those expectations.
Flexibility and Customization
Flexibility is important when dealing with diverse project requirements. Look for a machine that allows easy adjustment and customization to produce different purlin profiles and sizes.
Control System and Automation
A modern purlin roll forming machine should have an advanced control system for seamless operation. Automation features, such as computerized controls and programmable settings, enhance productivity and reduce manual errors.
Quality and Durability
Investing in a reliable and durable machine is essential for long-term success. Consider the build quality, materials used, and reputation of the manufacturer to ensure the machine will withstand the demands of your operations.

Applications of Purlin Roll Forming Machines
Purlin roll forming machines find extensive use in various industries and applications. Some notable applications include:
Construction Industry
Purlin roll forming machines are widely used in the construction industry to manufacture purlins for residential, commercial, and industrial buildings. These machines contribute to efficient and cost-effective construction processes.
Roofing and Cladding Systems
Purlins play a crucial role in roofing and cladding systems, providing structural support and stability. Purlin roll forming machines enable the production of purlins that meet specific design requirements for different types of roofs and cladding.
Warehouse and Industrial Buildings
Warehouse and industrial buildings often require large quantities of purlins to support their structures. Purlins produced by purlin roll forming machines are ideal for these applications due to their high strength and load-bearing capacity.
Infrastructure Projects
Infrastructure projects such as bridges, flyovers, and railway stations require sturdy and reliable structural components. Purlin roll forming machines can produce purlins that meet the stringent quality standards and specifications needed for such projects.
Greenhouse Construction
Greenhouses require specialized purlins to support the structure and hold the greenhouse coverings in place. Purlin roll forming machines can manufacture purlins with the necessary profiles and dimensions for greenhouse construction, ensuring optimal performance and durability.
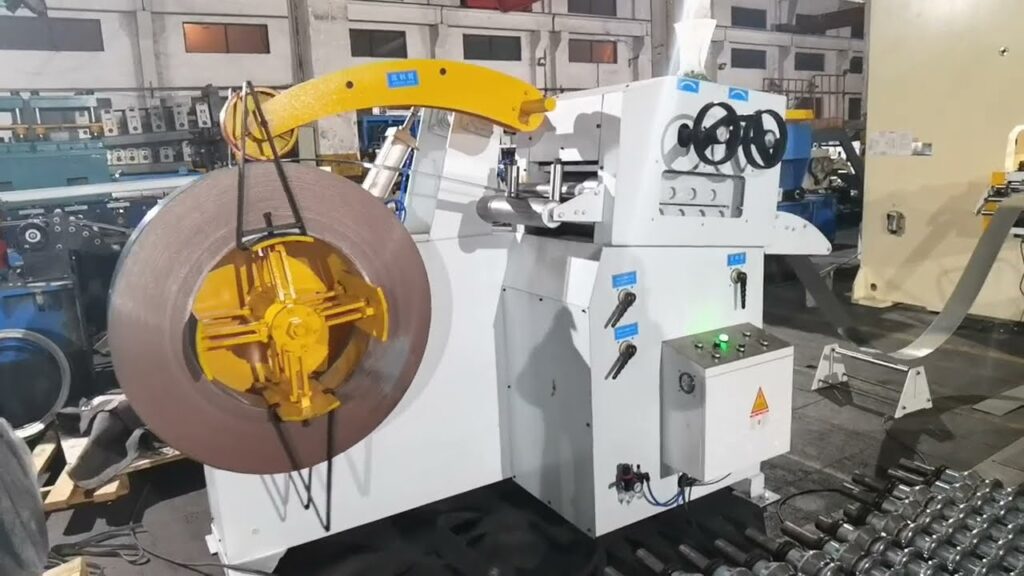
Maintenance and Care for Purlin Roll Forming Machines
To maintain the longevity and performance of a purlin roll forming machine, regular maintenance is essential. Here are some maintenance tips to consider:
- Lubrication: Regularly lubricate the machine’s moving parts to reduce friction and prevent wear. Follow the manufacturer’s guidelines for lubricant type and frequency of application.
- Cleaning: Keep the machine clean from dust, debris, and metal shavings. Regularly remove any accumulation of material to prevent damage to the machine and maintain optimal performance.
- Inspection: Conduct routine inspections to identify any signs of wear, damage, or misalignment. Promptly address any issues to prevent further damage and ensure the machine operates smoothly.
- Calibration: Periodically check and calibrate the machine to maintain accuracy in producing purlins. Verify the machine’s settings and measurements to ensure it is within the desired tolerances.
- Training and Operator Skills: Provide proper training to machine operators to ensure they understand the machine’s operation, maintenance requirements, and safety protocols. Skilled operators can contribute to efficient and safe machine performance.
Tips for Maximizing Efficiency and Productivity
To maximize efficiency and productivity when using a purlin roll forming machine, consider the following tips:
- Optimize Material Usage: Plan the production process to minimize material waste. Optimize the cutting and shaping patterns to maximize the utilization of the metal coils.
- Batch Production: Whenever possible, batch similar purlin profiles together to minimize setup time and increase productivity. Grouping similar production runs reduces downtime and improves overall efficiency.
- Regular Inspections: Conduct routine inspections of the purlins produced by the machine. Check for any quality issues or defects and take corrective actions promptly to maintain high-quality output.
- Operator Training: Invest in comprehensive training for machine operators to enhance their skills and knowledge. Well-trained operators can troubleshoot minor issues, improve machine setup time, and minimize errors.
- Continuous Improvement: Regularly evaluate the machine’s performance and production processes. Identify areas for improvement, implement changes, and adopt best practices to continuously enhance efficiency and productivity.
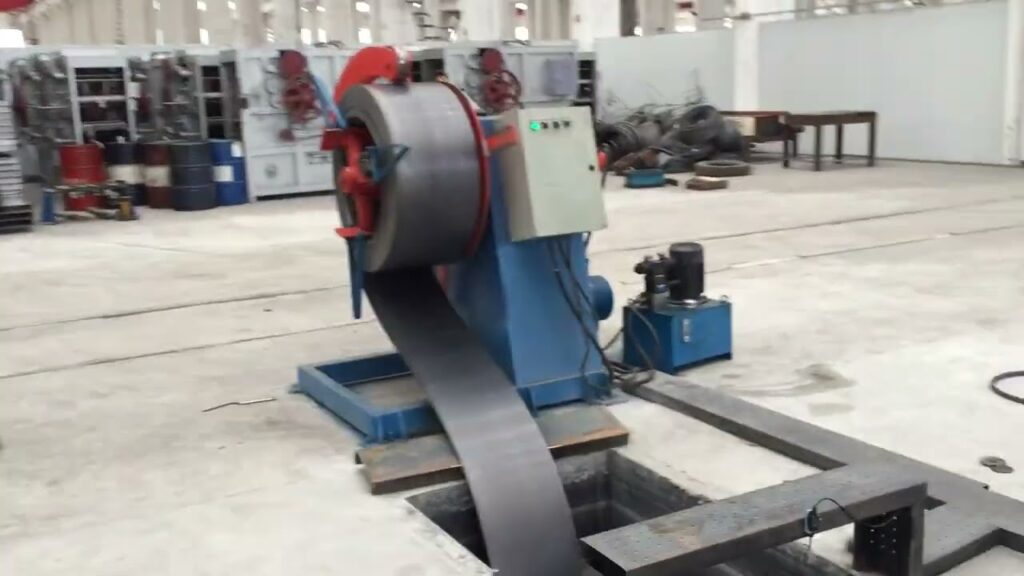
Choosing the Right Manufacturer
Selecting the right manufacturer is crucial when investing in a purlin roll forming machine. Consider the following factors:
- Experience and Reputation: Choose a manufacturer with a proven track record and extensive experience in producing roll forming machines. Look for customer reviews and testimonials to gauge their reputation.
- Customization Options: Ensure the manufacturer offers customization options to tailor the machine to your specific requirements. This includes the ability to produce different purlin profiles and sizes.
- Support and Service: Evaluate the manufacturer’s after-sales service and support. Check if they provide technical assistance, spare parts availability, and maintenance support to ensure smooth operation and minimize downtime.
- Technology and Innovation: Look for manufacturers who invest in research and development to stay up-to-date with the latest technological advancements. Innovative features can improve efficiency, accuracy, and overall performance.
- Pricing and ROI: Consider the machine’s price in relation to its features, quality, and long-term return on investment. Choose a machine that offers a balance between affordability and value.
Conclusion
Purlin roll forming machines have revolutionized the construction and manufacturing industries by streamlining the production of high-quality purlins. Their automated operation, consistent output, and customization options make them indispensable tools for efficient and cost-effective construction projects. By understanding the different types, working principles, applications, and maintenance requirements of purlin roll forming machines, businesses can make informed decisions to enhance their productivity and competitiveness.
FAQs
Q1: What materials can be used with a purlin roll forming machine?
A purlin roll forming machine can handle a variety of materials, including steel, aluminum, and galvanized steel. The choice of material depends on the specific project requirements and desired properties of the purlins.
Q2: Can a purlin roll forming machine produce different purlin sizes?
Yes, purlin roll forming machines can be adjusted to produce purlins of various sizes. They offer flexibility in terms of width, thickness, and shape customization to meet different construction needs.
Q3: Is it necessary to lubricate a purlin roll forming machine?
Yes, regular lubrication is crucial to maintain the smooth operation of a purlin roll forming machine. Lubricating the moving parts reduces friction, prevents wear, and prolongs the machine’s lifespan.
Q4: How long does it take to set up a purlin roll forming machine for a new production run?
The setup time for a purlin roll forming machine depends on various factors, including the complexity of the purlin profile, operator skills, and the machine’s automation features. With proper training and efficient processes, setup times can be minimized.
Q5: Can a purlin roll forming machine be integrated into an existing production line?
Yes, purlin roll forming machines can be integrated into existing production lines. They can be customized and configured to seamlessly fit into specific manufacturing processes, enhancing overall production efficiency.