t grid making roll forming machine are used to produce T grid structures from coil strips of metal. They form the raw material into the distinctive T shape through a series of progressive rolling bending and forming stations. T grid structures have applications as support frames in construction, shelves, mezzanines, platforms, walkways and more.
t grid making roll forming machine allow efficient, automated and continuous production of T grid components in long lengths as per requirement. They offer advantages over traditional fabrication in terms of speed, consistency and cost savings. This article provides a comprehensive guide to t grid making roll formers covering types, specifications, suppliers, applications, operation, advantages and more.
Types of T Grid Roll Forming Machines
There are two main types of t grid making roll forming machine:
Standard Fixed T Grid Roll Forming Machines
- Produce standard fixed sizes of T grid in pre-set dimensions.
- Come with forming stations arranged in-line as per the profile.
- Allow limited flexibility in grid dimensions.
- Well-suited for mass production of fixed T grid sizes.
- Offer lower cost compared to customizable machines.
Customizable T Grid Roll Forming Machines
- Allow programming and adjustments to produce different T grid sizes.
- Come with quick change forming stations and tooling.
- Enable fast set up changeover to new profiles.
- Ideal for producing T grids in multiple sizes and dimensions.
- Offer more flexibility but higher cost.
T Grid Machine Specifications
t grid making roll forming machine are available with different specifications and capabilities to suit needs:
Specification | বিস্তারিত |
---|---|
Production Speed | 10-25 m/min based on thickness. Faster speeds possible with high frequency motors. |
Metal Thickness | 0.5 – 1.5 mm. Varies based on machine capacity. |
Grid Width | 100 – 300 mm standard. Wider possible with customized setup. |
Grid Height | 25 – 150 mm range. Depends on stations and tooling. |
Length Capability | Up to 25m. Restricted only by space for coils and formed grid. |
Forming Stations | 10 -16 stations. More allow more processing and steps. |
Power Consumption | 5-10 kW connected load depending on number of motors. |
Voltage | 380V or 415V AC three phase industrial power supply. |
ফ্রেম | Heavy duty welded steel frame for rigidity. Stress relieved. |
PLC Control | For precision monitoring and control of motors during production. |
HMI | For inputting machine settings and monitoring operation parameters. |
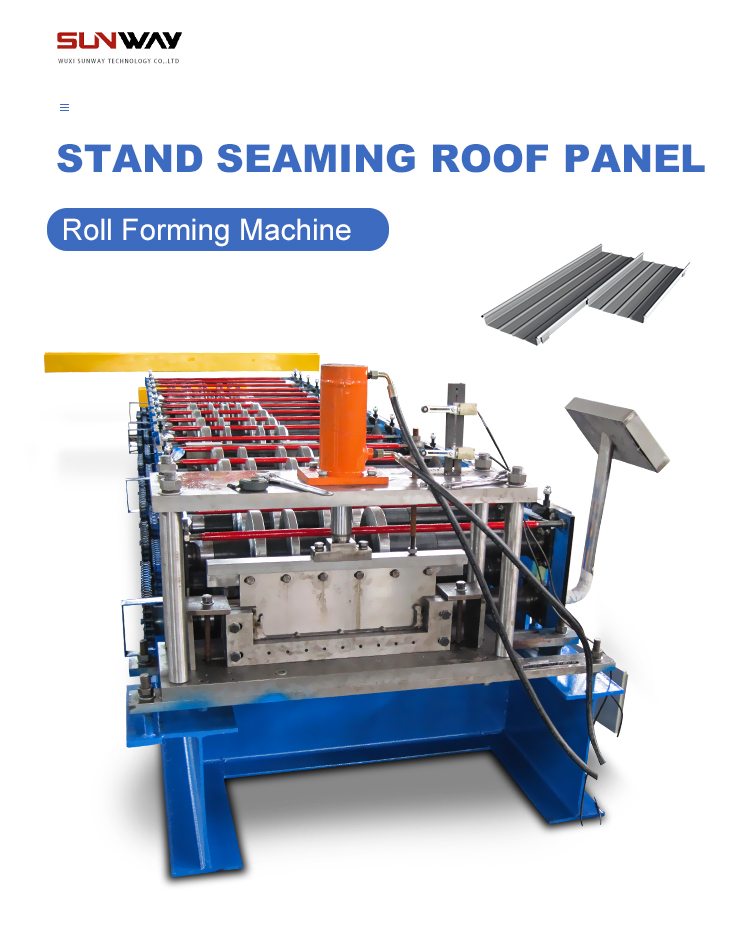
T Grid Roll Former Applications
T grid profiles produced by these machines find uses in:
- Mezzanine and platform flooring
- Material storage racks
- Shelving structures
- Walkways, catwalks
- Building frames
- Wall supports
- Scaffolding
- Safety barriers
- Canopies
- Fencing
- Window security grilles
- Agricultural livestock pens
- Machinery safety guards
- Heavy duty pallet racking
- Industrial flooring
Choosing t grid making roll forming machine Suppliers
When selecting a t grid roll forming machine, here are key considerations for choosing reliable suppliers:
- Technology – Supplier should use high precision forming technology for dimensional accuracy.
- Build Quality – Machine frame and stations should be rugged for smooth performance.
- Tooling – Availability of standard and custom tooling for different profiles.
- Automation – PLC based automation for precise monitoring and control.
- Reliability – Proven machine designs that ensure low maintenance and trouble-free operation.
- অভিজ্ঞতা – Number of years supplying such roll forming equipment.
- কাস্টমাইজেশন – Capability to produce customized grid sizes apart from standard sizes.
- Service – Responsiveness to queries, ordering, installation and after-sales support.
- Certifications – Quality certifications like ISO 9001 to ensure standardized processes.
- Cost – Competitive pricing combined with quality equipment and features.
Supplier Comparison Table | Supplier 1 | Supplier 2 | Supplier 3 |
---|---|---|---|
Technology | AAA | AAA | AA |
Build Quality | AAA | AA | AAA |
Tooling Range | AA | AAA | AA |
Automation | AAA | AA | AAA |
Reliability | AA | AAA | AA |
অভিজ্ঞতা | 10 Years | 15 Years | 5 Years |
কাস্টমাইজেশন | Yes | On Request | No |
Service | AAA | AA | AAA |
Certifications | ISO 9001 | ISO 9001 | None |
Cost | $$$ | $$ | $ |
T Grid Roll Former Pricing
t grid making roll forming machine are priced based on:
- Type – Customizable machines cost 20-30% more than fixed size machines.
- Speed – Faster output increases price.
- Capacity – Higher metal thickness capacity increases price.
- Automation – More motors and automation increases price.
- Brand – Premium brands command higher prices.
- Origin – Imported machines are more expensive than domestic.
Machine Type | Speed | Metal Thickness | Price Range |
---|---|---|---|
Fixed | 10 m/min | Up to 1 mm | $8,000 – $12,000 |
Fixed | 15 m/min | Up to 1.2 mm | $15,000 – $20,000 |
Customizable | 15 m/min | Up to 1.5 mm | $22,000 – $30,000 |
Customizable | 20 m/min | Up to 1.5 mm | $32,000 – $40,000 |
Installing and Operating t grid making roll forming machine
Proper installation and operation ensures optimal performance of t grid roll formers:
- Install on flat leveled surface and anchor bolts.
- Provide adequate space around for coil loading and grid offloading.
- Connect electrical supply and pneumatic lines.
- Load tooling and adjust stations as per profile.
- Feed coil strip into machine and align with rollers.
- Set speed, thickness, protective device limits on HMI panel.
- Start motors and test run machine without coil.
- Monitor forming process and inspect initial grids for defects.
- Make adjustments to stations if required to achieve correct profile.
- Operate continuously to produce grids of desired length.
- Apply corrosion resistant coating if required.
- Ensure safety by fencing off around machine during production.
Maintenance of t grid making roll forming machine
Regular maintenance activities:
- Clean stations, tooling and clear metal debris.
- Lubricate bearings, gears and moving parts.
- Check alignment and settings of forming rollers.
- Inspect electrical wiring and connections.
- Check hydraulic systems and pneumatic supply pressure.
- Verify PLC system signals and responses.
- Replace worn out or defective components like bearings, rollers etc.
- Touch up paint on machine frame to prevent corrosion.
Advantages of t grid making roll forming machine
Key benefits of using t grid roll formers:
- High production speed and output compared to manual methods.
- Consistent and uniform profile dimensions.
- Cost savings from raw material savings and labor reduction.
- Flexibility to change sizes with adjustable tooling.
- Automated continuous production improves efficiency.
- Allows long length grids to be formed on demand.
- Safe enclosed forming process minimizes accidents.
- Low maintenance required compared to other metal working machines.
- Ideal for producers supplying large volumes of T grid.
- Enables manufacturers to meet changing market demand faster.
Limitations of T Grid Roll Forming Machines
Some drawbacks to consider:
- High initial capital investment required.
- Customized machines with quick changeover cost more.
- Trained personnel needed to operate and maintain.
- Regular tooling changes can reduce productivity.
- Limitations on thickness and widths that can be formed.
- Not economical for small volume or prototype production.
- Occupies significant floor space.
- After-sales service support varies among suppliers.
- Fixed machines cannot meet new profile requirements.
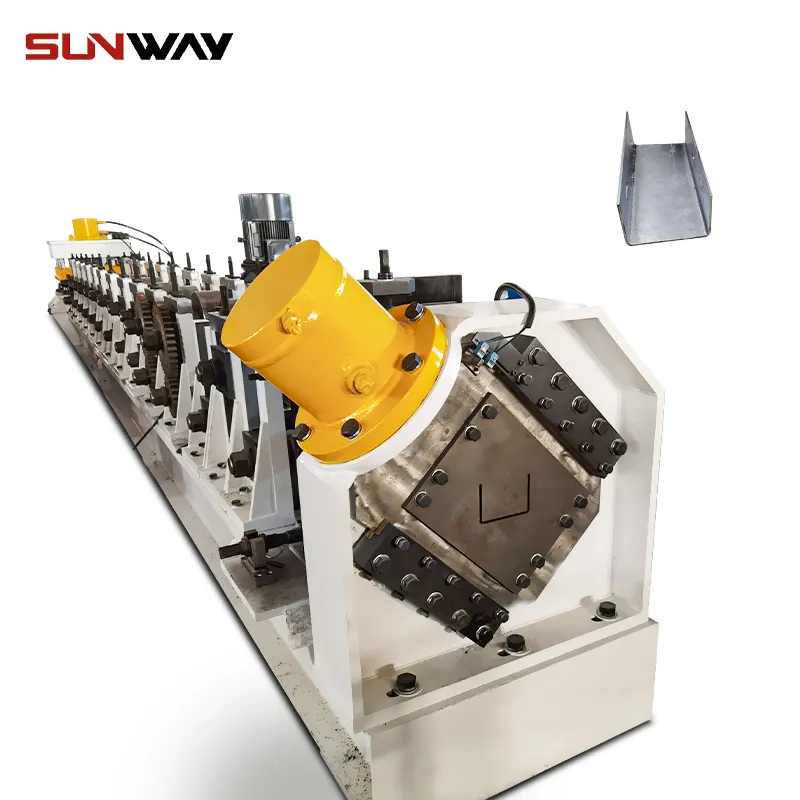
FAQ
Q: What metals can be used to produce T grid profiles on these machines?
A: Mild steel and galvanized steel coils are commonly used. Aluminum coils can also be formed with appropriate tooling.
Q: What thickness of coils can be processed?
A: Standard machines can process 0.5 mm to 1.5 mm thickness. Upper limit can be increased on customized machines.
Q: How long sections of T grid can be produced continuously?
A: Typical length is 15-25 meter sections. Unlimited lengths possible if space allows coils and formed grid to exit.
Q: How many operators are required to run a T grid roll former?
A: Normally 1-2 operators needed for loading coils, monitoring operation and offloading formed grids.
Q: What safety aspects should be considered when using these machines?
A: Enclosing the machine, protective fencing, safety limit switches, and PPE for operators are essential safety requirements.
Q: What type of foundations are needed to install T grid roll formers?
A: Flat leveled concrete or masonry floor. Anchor bolts to secure machine. No special foundation required.
Q: What is the estimated lifetime of a T grid roll forming machine?
A: Approximately 15-20 years lifespan can be expected if routine maintenance is carried out.
Q: Are spare parts for T grid machines readily available?
A: Most suppliers can provide common spare parts for motors, bearings, cutting tools. Unique components may have longer lead times.
Q: What factors determine the production speed of a T grid roll former?
A: Metal thickness, number of passes, machine power, and tooling type. Typical speed range is 10-25 m/min.