Standing seam metal roll forming machines are an essential equipment for manufacturers of metal roofing and siding panels. This comprehensive guide provides an overview of standing seam roll formers, their working, types, applications, specifications, suppliers, installation, operation, maintenance, and benefits.
Overview of Standing Seam Metal Roll Forming Machines
Standing seam metal roll forming machines create corrugated or interlocking raised seams on metal panels. The seams enable joining of panels and provide mechanical strength. Roll forming converts flat metal coils into shaped panel profiles by progressively bending the strip through consecutive roller dies.
What is a Standing Seam Metal Roof?
A standing seam metal roof has raised seams where panel edges fold over each other. The vertical seams interlock panels together from eave to ridge. This allows panels to expand and contract freely with temperature changes. Panels are attached to the structure without penetration of the metal surface.
Advantages of Standing Seam Metal Roofs
- Durability – Lasts 50 years or more with minimal maintenance
- Wind and fire resistance – Seams allow flexibility during high winds
- Leak resistance – Water runs off with no penetration points
- Energy efficiency – Reflective surface and thermal break under seams
- Aesthetics – Available in variety of colors with attractive seams
একটি রোল ফর্মিং মেশিন কিভাবে কাজ করে?
Roll forming is a continuous bending process which converts a flat strip of sheet metal into a desired cross-sectional shape by passing it through consecutive roller dies. Each die makes a small incremental bend until the final profile is achieved. Standard components of a roll former include:
- Coil feed unit
- Feed table with pinch rolls
- Roller station unit with roller dies
- Cutoff press
- আউটপুট টেবিল
The sheet is pulled from the coil through the rollers by drive rolls. Roller stations make the longitudinal bends while transverse dies make ribbing or embossing. Cutoff dies shear the panels to required length.
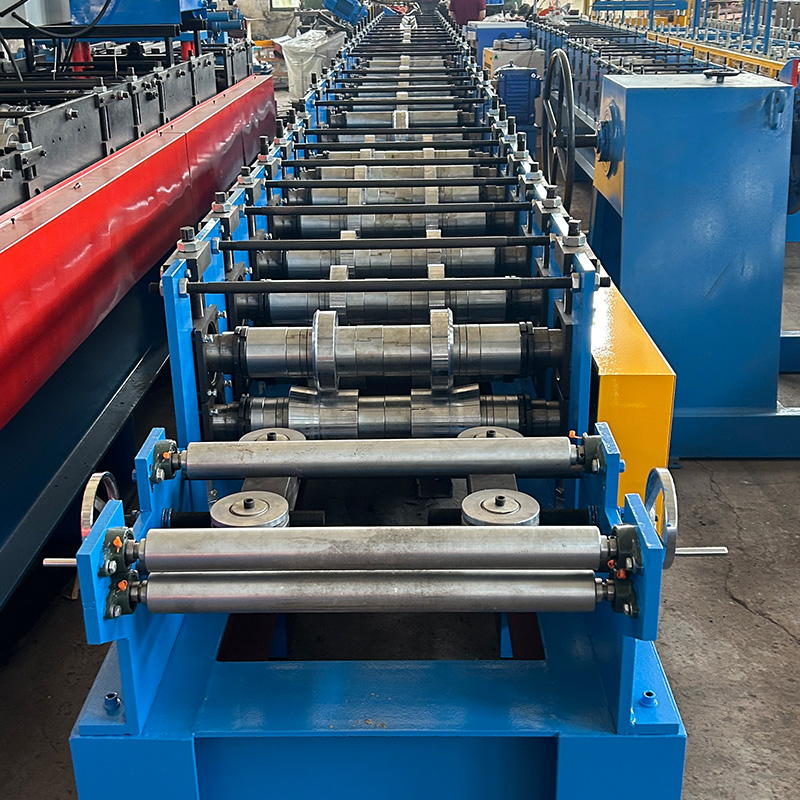
Types of Standing Seam Metal Roll Forming Machines
Portable vs Stationary Roll Formers
Portable Roll Formers | Stationary Roll Formers |
---|---|
Compact and movable | Larger heavy-duty production machines |
Lower output capacity | Higher output capacity |
Used at construction site | Used in manufacturing facilities |
Form limited profiles | Form wide range of profiles |
Manual operation | Automated operation |
Roofing vs Siding and Wall Panel Roll Formers
Roofing Panel Roll Formers | Siding and Wall Panel Roll Formers |
---|
- Designed for roofing profiles like standing seam, batten rolls, and corrugated sheets | Designed for siding, fascia, soffit, interior wall profiles
- Form higher ribs and seams | Form lower profile panels
- Strengthened framework | Lighter frameworks
- Layout allows angled roof panel production | Layout for vertical wall panel production
Custom vs Standard Roll Forming Machines
Custom Roll Formers | Standard Roll Formers |
---|
- Custom built to required profile | Limited profile shapes |
- Flexibility to make special profiles | Fixed standard profiles like standing seam |
- Higher cost | Lower cost |
- Longer lead times | Readily available |
- Dedicated to particular profile | Can make different profiles with quick change tooling |
Main Components of a Standing Seam Roll Former
আনকোয়লার
- Feeds metal coil strip into the roll former
- Expansion mandrel to mount coil
- Powered decoiler with leveler
- Guide rolls feed coil into forming section
Forming Section
- Progressive roller dies make incremental bends
- Configured into different roller stations
- Number of stations determines profile complexity
- Quick change tooling allows profile variations
Shearing Operation
- Cutoff press with plasma torch or shear blade
- Cuts formed panels to specified length
- Conveyor carries cut panels to exit
নিয়ন্ত্রণ ব্যবস্থা
- PLC automates production sequence
- HMI for monitoring and parameter control
- Servo motors synchronize roller stations
Specifications of Standing Seam Roll Formers
Specifications | Typical Values |
---|---|
Production Speed | 16 – 49 feet/min |
Maximum Coil Width | 26 – 80 inches |
Minimum/Maximum Thickness | 24/26 gauge |
Roll Forming Stations | 10 – 20 |
Main Drive Power | 5.5 – 15 kW |
Weight | 6000 – 20000 lbs |
- Speed and thickness capacity determine output rate up to 12,000 lbs/hour
- Number of roller dies influence profile complexity
- Framework size and coil capacity affect maximum sheet width
Applications of Standing Seam Metal Roll Forming
Standing seam roll forming machines are ideal for manufacturing:
- Metal roofing panels
- Wall and facade cladding
- Curved roofing and facades
- Metal decking and flooring
- Roof drainage systems
- Architectural metal panels
- Silo and tank shell panels
- Tunnel liners
- Solar panel racking
How to Choose a Standing Seam Metal Roll Former
Consider the following when selecting a standing seam roll former:
Type of Panels to be Produced
- Roofing, siding or custom architectural profiles
- Geometry and seam height requirements
- Metal thickness range
Production Volume Requirements
- Output rate needed based on order sizes
- Level of automation or manual operation
Available Space in Facility
- Length and width constraints
- Outdoor installation for portable versions
Investment Budget
- Customized versus standard machine
- Level of automation features
Production Efficiency Desired
- Quick changeovers between profiles
- Data monitoring and analysis
- Integration with upstream and downstream equipment
Technical Support
- Installation and operator training
- Maintenance and service capabilities
- Availability of spare parts
Standing Seam Roll Former Suppliers
Supplier | Location | Type |
---|---|---|
Safintra Roofing & Machines | Michigan, USA | Stationary and portable roll formers |
Arrow United Industries | New Jersey, USA | Custom roll forming equipment |
LT Metal Roll Formers | Bangkok, Thailand | Roofing, decking and solar panel roll formers |
Gasparini SpA | ইতালি | CNC roll forming lines for roofing and cladding |
Metal Forming Systems Inc | Wisconsin, USA | Custom and standard roll formers |
- Choose supplier based on machine types, capabilities, and services offered
- Local suppliers beneficial for equipment maintenance and support
- Leading North American and European companies have dealers globally
Supply Price Range:
- Standard portable roll former – $15,000 to $60,000
- Custom stationary roll former – $60,000 to $150,000
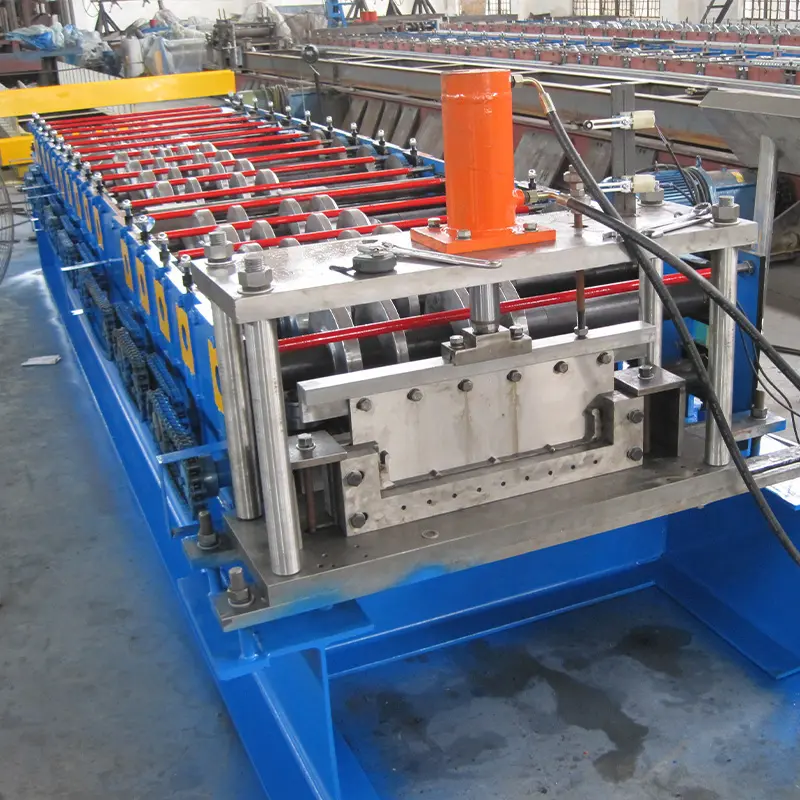
Installation and Setup of Standing Seam Roll Former
Proper installation is key for standing seam roll former performance:
- Mount machine on flat leveled surface
- Bolt sections together and align carefully
- Connect electric power to required voltage and amps
- Install hydraulic unit and piping circuits
- Thread coil strip through feed section
- Install tooling and dies into roller stations
- Adjust rollers, guides, sensors as per profile
- Test run to confirm forms correct seam shape
Operation and Maintenance of Standing Seam Roll Former
- Operators should be properly trained for safety and optimal running
- Monitor line speed, pressures, power consumption during operation
- Schedule periodic maintenance checks according to manual
- Lubricate bearings, gears, seals, rollers as specified
- Inspect rollers, guides, sensors and replace worn parts
- Verify hydraulic fluid level and filtration regularly
- Monitor coil strip feeding and shearing operations
- Create maintenance logbook to record work done
How Standing Seam Roll Forming Works
The roll forming process shapes metal coils into panels with raised seams in a continuous process:
- Coil strip pretreated for corrosion resistance is loaded on the powered de-coiler which feeds the strip through an initial leveling stage.
- The strip enters the forming section and passes through consecutive roller stations. Each set of rollers makes a incremental bend until the complete panel profile is achieved.
- Seam rollers fold over the edges longitudinally to form interlocking standing seams. Transverse dies can make ribs for added rigidity.
- After forming, the cutoff press shears the strip to required panel length based on preset parameters.
- Conveyors transport finished panels to the exit for inspection and downstream processes like coating, accessories or palletizing.
- Roller stations are equipped with quick change tooling to allow fast die changeovers for different seam configurations.
- Automatic controls synchronize the roller stations and cutoff operation for continuous high-speed production.
Pros and Cons of Standing Seam Roll Forming
Advantages | Limitations |
---|---|
Highly efficient continuous process | Initial tooling cost for custom profiles |
Versatile forming of complex shapes | Limited for short production runs |
Consistent quality and tolerances | Heavy equipment requiring rigidity |
Adaptable automation features | Roll changes needed for different metals/gauges |
Low maintenance and operating cost | Setup and changeover time for profiles |
Compact equipment footprint | Trained personnel required for operation |
FAQ
What materials can be roll formed into standing seams?
- Most common are galvanized steel, aluminum, copper. Stainless steel requires high rigidity and horsepower.
What thickness of metal sheet can be roll formed?
- 22 gauge to 14 gauge (0.8mm – 2mm) for most standing seam profiles. Custom machines can do thicker sheets.
How long does a standing seam metal roof last?
- Properly installed standing seam roofs last 40-60 years with minimal maintenance required. The interlocking seams prevent leaks.
What is the cost of standing seam metal roofing?
- Installed costs range from $4.50 – $12 per square feet depending on material, sheet thickness, and accessories.
What are the advantages of standing seam over exposed fastener metal roofs?
- Standings seams provide greater uplift resistance, flexibility, leakproofing, and aesthetics compared to through-fastened panels.
How many square feet can be produced per hour?
- Output rates range from 500 – 2500 square feet per hour depending on the machine, line speed, and panel width.
How much does a standing seam roll forming machine cost?
- Standard portable machines start around $18,000. Heavy-duty stationary machines range from $60,000 to $140,000.
What safety precautions are required for roll former operation?
- Safety guards for pinch points, lockouts, worker training. Proper PPE like close-fitting clothing, gloves, eye protection. Do not exceed rated speeds.
উপসংহার
Standing seam roll formers are the optimal equipment to produce interlocking metal panels for roofs, walls, and architectural façades. Their versatility, efficiency and automation capabilities make roll forming ideal for both small and high volume production. This guide covered various types of standing seam roll formers, their key components, applications, specifications, suppliers, installation, operation, benefits and limitations. Equipped with this overview, manufacturers can make informed decisions for selecting the right standing seam roll forming system for their specific production needs.