Roll forming is a metal forming process used to transform flat sheet metal or coils into customized profiles with complex cross-sections. রোল গঠন মেশিন are essential equipment for manufacturing precision metal parts with repetitive profiles efficiently and economically. This guide provides a comprehensive overview of the key factors to consider when selecting the optimal roll former for your production needs.
Overview of Roll Forming Machines
Roll forming machines use a series of consecutive pairs of contoured rolls to gradually shape metal sheet or strip into the desired cross-sectional profile. Each roll forming pass incrementally forms the material closer to the target shape.
The main components of a basic roll former include:
- Uncoiler or decoiler to feed raw coil or sheet metal into the machine
- Feed table with pinch rolls to guide sheet through machine
- Forming stations with top and bottom rolls to progressively shape the profile
- Cutoff knife to cut finished parts to length
- Controls and sensors to set and monitor process parameters
Table 1: Types of Roll Forming Machines
Type | Description |
---|---|
Coil-to-coil | Continuous process, outputs formed coil |
Cut-to-length | Cuts formed profile to length after rolling |
End formers | Form ends of profile with special rolls |
Portable | Compact units for on-site or short-run production |
Specialty | Custom machines for unique profiles |
Roll formers are available in different configurations and levels of automation. Key characteristics that vary by machine include:
- Number of roller stations – more stations allow more complex profiles.
- Roller size – determines maximum sheet width.
- Roller materials – steel, rubber, urethane coated etc.
- Inline processes – punching, welding, hardware insertion.
- Speed and precision – depends on mechanical design.
- Controls – basic vs. digital controls and monitoring.
- Automation features – coil handling, part cutoff and stacking.
Table 2: Roll Former Size Specifications
Parameter | Typical Range |
---|---|
Number of stands | 10 – 26 |
Maximum sheet width | 18 – 80 inches |
Minimum sheet thickness | 0.5 – 2 mm |
Maximum sheet thickness | 3 – 8 mm |
Roll diameters | 4 – 8 inches |
The choice of machine depends on the profile shape, dimensions, materials, and production volume requirements. Work with roll former manufacturers to select the optimal configuration for your specific application.
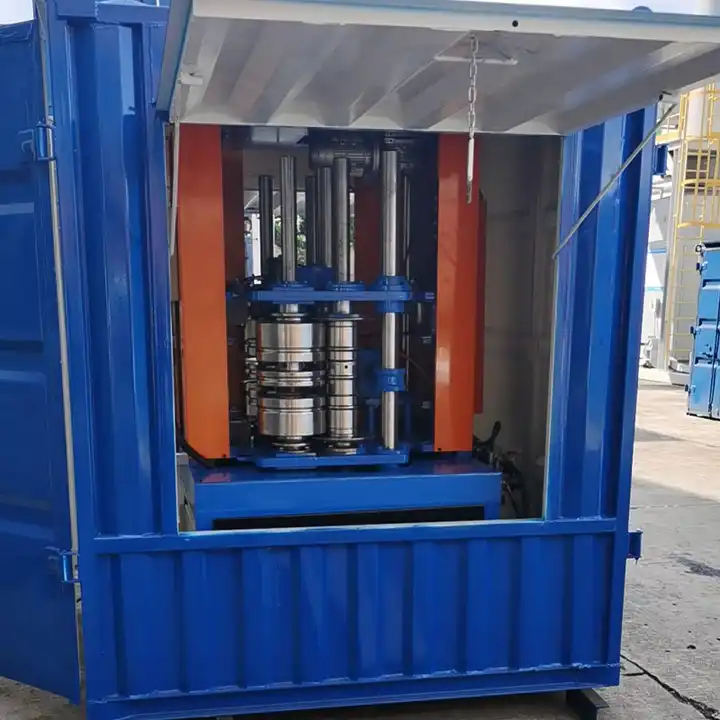
Applications of Roll Forming Machines
Roll forming is suited for high productivity and efficient continuous production of metal parts with cross-sections that would be difficult to form with other processes.
Table 3: Roll Forming Applications
Industry | Common Profiles Produced |
---|---|
Construction | Studs, tracks, panels, decking, roofing, siding, drainage |
Automotive | Door pillars, roof rails, windshield trim |
Appliances | Frames, housings, shelves, panels |
Furniture | Legs, frames, shelving, handles |
Lighting | Poles, frames |
Transportation | Rail car and truck frames, interiors |
Almost any open thin-walled shape can be roll formed as long as it can be decomposed into a series of simple cross-sectional stages. Hollow and enclosed tube profiles require specialized roll forming techniques.
Common materials roll formed include:
- Low carbon steel
- High strength steel
- Stainless steel
- Aluminum
- Brass
- Copper
Benefits of Roll Forming
Table 4: Advantages of Roll Forming
Benefit | Description |
---|---|
High productivity | Continuous process with fast cycle times |
Material savings | Efficient use of raw material with little waste |
Labor efficiency | Automated process requires minimal operators |
Flexibility | Quick changeover between profiles |
Strength | Cold forming work hardens and strengthens metal |
Quality | Consistent and repeatable to tight tolerances |
Cost effective | Low tooling costs compared to other processes |
Design freedom | Complex shapes can be produced |
Key strengths of roll forming include high throughput, material utilization, and geometric flexibility for mass production of parts with sectional profiles.
Roll Forming Machine Operations
Proper setup and operation of roll formers is key to achieving quality outcomes. The main process steps include:
- Loading coils or de-stacking sheet onto the infeed table
- Threading the strip through the roller stations
- Setting the requred rotation speeds and pass schedules
- Monitoring forming process and inspecting output
- Cutting parts to specified lengths or coiling finished product
- Safety procedures for safe operator work environment
Table 5: Roll Former Operation Guidelines
Parameter | Recommendations |
---|---|
Material feed | Use proper decoiler tension; clean stock; lubricate as needed |
Roller adjustment | Set roll gaps progressively per procedure |
Roll setup | Check parallelism and proper rotation direction |
Speeds | Start slow and incrementally increase; avoid slippage |
Scrap | Allow multiple parts as scrap until process stabilizes |
Lubrication | Apply correct lubricant to reduce friction; avoid over oiling |
Maintenance | Follow schedule for roll and bearing inspection and lubrication |
Tooling wear | Monitor roll condition and replace timely |
Safety | Use proper guarding; ear and eye protection |
Taking time to properly set up and trial the roll former will ensure optimal performance and output quality.
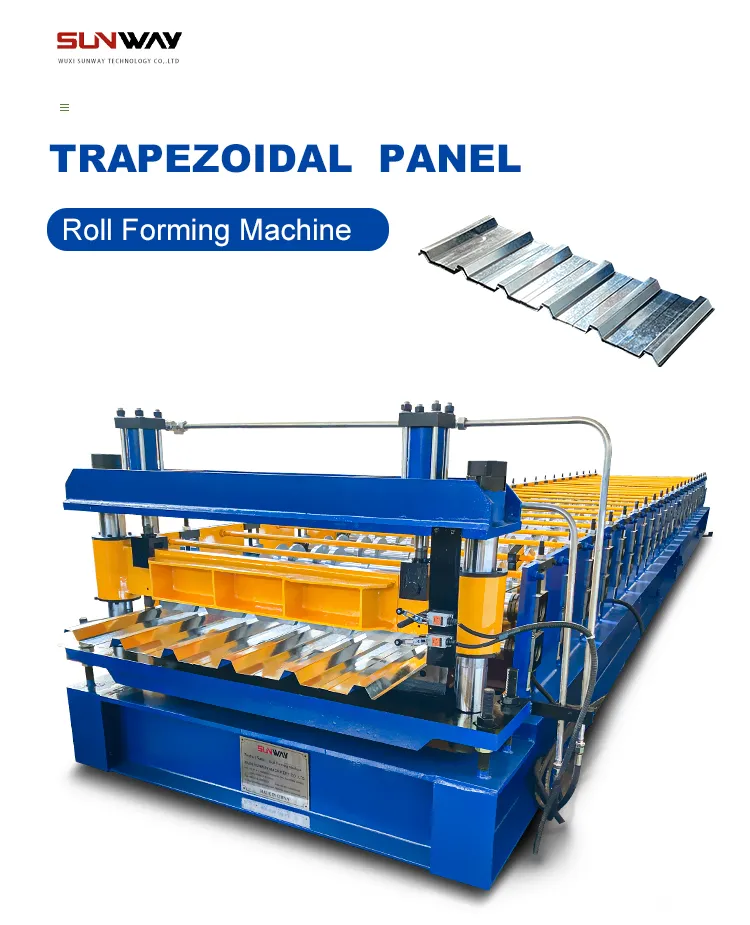
Roll Forming Machine Maintenance
A sound maintenance program is essential for trouble-free operation and maximum longevity of roll forming equipment.
Table 6: Roll Former Maintenance Schedule
Maintenance Task | Frequency |
---|---|
Inspect roll condition | Daily |
Check alignments | Monthly |
Lubricate bearings | Per OEM schedule |
Lubricate guides | Weekly |
Inspect chains and sprockets | Monthly |
Verify hydraulic pressure | Monthly |
Inspect sensors and controls | Annually |
Roll refinishing or replacement | As needed |
Common problems caused by poor maintenance include profile distortion, excessive noise, roll marking, and increased scrap rates. Proactive maintenance prevents unplanned downtime and quality issues.
Choosing a Roll Forming Machine Manufacturer
Selecting the right roll former supplier is key to getting a machine that matches your needs. Below are important factors to consider:
Table 7: Roll Former Supplier Evaluation Criteria
Consideration | Assessment Guidelines |
---|---|
Reputation | Years in business; customer reviews |
কাস্টমাইজেশন | Ability to engineer for custom profiles |
Quality | Process control and tolerances; certifications |
Design expertise | Experience with similar applications |
Cost | Pricing for features; total cost of ownership |
Lead time | Standard and expedited schedule options |
সমর্থন | Installation assistance; training; manuals |
Maintenance | Ease of service; spare parts availability |
Upgradeability | Ability to add functionality later |
Work closely with shortlisted suppliers to review designs and capabilities. Get references to contact their existing customers. Select the roll former company that best fits your business.
Roll Former Pricing
The total cost of a roll forming system includes the base machine cost plus additional accessories and tooling.
Table 8: Roll Forming Equipment Pricing
Component | Price Range |
---|---|
Basic machine | $50,000 – $500,000 |
Inline punches | $10,000 – $100,000 |
Secondary processes | $25,000 – $250,000 |
Automation | $25,000 – $250,000 |
Tooling – rolls per station | $1,000 – $5,000 |
Design and engineering | $5,000 – $50,000 |
Installation and training | $10,000 – $100,000 |
Pricing varies significantly based on the machine size, features, precision, and production volumes. Get quotes from several suppliers to compare options. Consider total cost against productivity benefits.
Roll Forming vs Other Metal Forming Processes
Table 9: Comparison of Metal Forming Processes
রোল গঠন | Press Brake Bending | Stamping | Extrusion | |
---|---|---|---|---|
Setup time | Low | High | Very high | Medium |
Tooling cost | Low | Medium | Very high | High |
Geometric flexibility | High | Medium | Low | Medium |
Part length | Continuous | Batch | Batch | Continuous |
Strength | High | Medium | High | Medium |
Tolerances | +/- 0.5mm | +/- 1mm | +/- 0.5mm | +/- 1mm |
Productivity | Very high | Medium | High | High |
Cost effectiveness | High – medium volumes | Low volumes | High volumes | High volumes |
Roll forming is advantageous for medium to high production volumes of parts with length or complex shapes, compared to other processes like stamping that have higher setup costs.
Roll Forming Machine Limitations
Despite the benefits, roll forming does have some inherent limitations to consider:
- Not efficient for low volume production.
- Limited to simple cross-sections.
- Size limited by roller dimensions.
- Sequential nature makes some shapes challenging.
- Secondary operations often required.
- Significant tooling investment for design changes.
Complexity of the profile and total length of the machine are key factors impacting cost.
উপসংহার
Specifying the optimal roll forming machine is essential to achieve maximum productivity, efficiency, and quality for producing metal parts with sectional profiles. This guide covers the key factors such as machine capabilities, features, operations, maintenance, suppliers, costs, and tradeoffs to help select the best roll former for your manufacturing needs. Leveraging the flexibility of the roll forming process can provide significant benefits over alternate metal forming approaches for producing repetitive sectional parts to meet your product requirements.
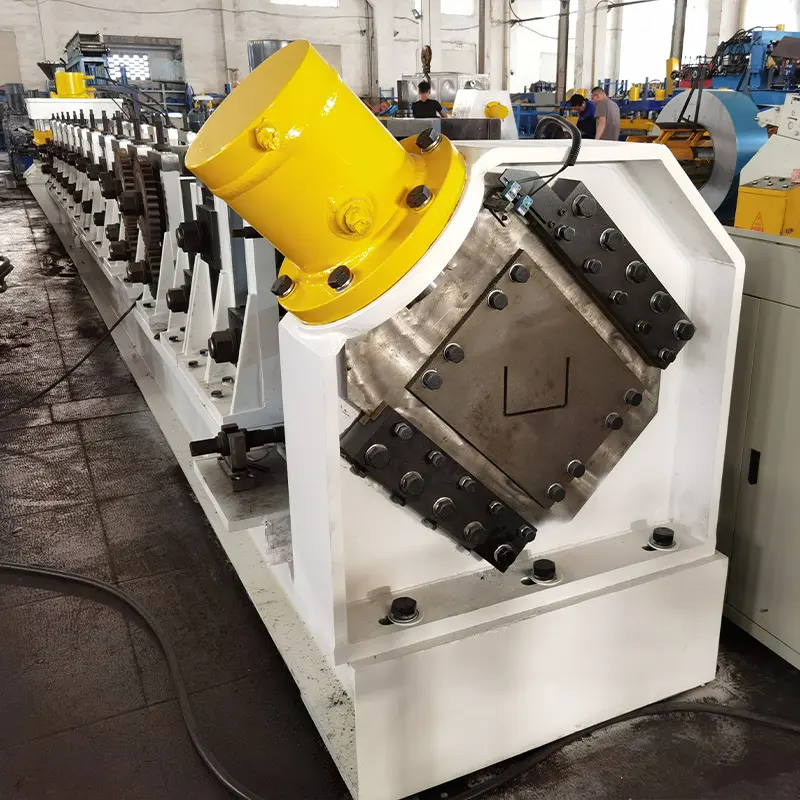
FAQ
Q: What thickness of metal sheet can be roll formed?
A: Standard roll formers can typically process metal sheets between 0.5mm to 8mm thickness. The maximum thickness depends on the roller size and power. Thinner gauges down to 0.3mm can be formed with proper machine adjustments.
Q: What shapes can be roll formed?
A: Any open cross-sectional shape is possible, such as C, U, Z, tubular, and hat channel profiles. Closed tube shapes require special roll forming methods. The more complex the profile, the more roller stations are required.
Q: How long can a part be roll formed?
A: There is no theoretical limit to the length as it is a continuous process. Practical lengths range from a few inches to hundreds of feet depending on the machine and application. Extended runout tables allow supporting longer parts.
Q: How accurate is roll forming?
A: Dimensional tolerances within +/- 0.5mm are standard based on machine precision and process controls. Tolerances down to +/- 0.25mm are possible but require tight monitoring and calibration.
Q: How does roll forming affect material properties?
A: The cold working strengthens the metal by work hardening. Yield and ultimate tensile strength increase. Elongation percentages decrease. Annealing can recover ductility.
Q: What defects can occur in roll forming?
A: Common defects are twist, bow, curl, wrinkles, and marking. These are prevented with proper design, machining, roll setup, and operation. Edge waviness can result from excessive roll pressures.
Q: How long do roll forming machines last?
A: With proper use and preventative maintenance, service lifetimes of over 20 years are common. Roll replacement and upgrades to controls or automation can extend useful production life further.
Q: What safety measures are required?
A: Roll formers contain many pinch points. Machine guarding, interlocked barriers, E-stops, and lockouts are essential. Workers also need PPE such as close-fitting clothing, ear protection, safety glasses, and gloves.
Q: How much does roll forming cost?
A: Total cost depends on size and features. Small manual machines may cost ~$75,000. Large fully automated high-speed production lines can cost over $500,000. Get quotes based on your part design and volumes.