Roll forming is a metal working process in which sheet metal is progressively formed into a desired cross-sectional profile through a series of rolling stands. Filo steel roll forming machines are designed specifically for rolling filo or thread wire profiles from steel strips.
Roll formed filo wire profiles have applications in sectors like construction, infrastructure, automobiles, appliances, and furniture. Filo profiles provide excellent finishing for metal structures, frames, panels etc. This guide provides a detailed overview of filo steel roll forming equipment.
Introduction to Filo Steel Roll Forming
Filo forming machines create threaded wire profiles by passing steel strips through consecutive sets of roller dies. Each die set incrementally forms the strip into the desired filo shape.
Key characteristics of filo steel roll forming:
- Creates filo wire profiles continuously from steel coil feed stock
- Flexible process capable of producing different filo shapes and sizes
- Output ranger from small batches to high volume production
- Lower tooling costs compared to other processes
- High dimensional accuracy and consistency in output
- Capable of handling a range of materials including mild steel, stainless steel, aluminum etc.
Filo profiles have a distinct screw or spiral type external shape. The key parameters that define filo shape are wire diameter, pitch length and hand direction.
Parameter | Description |
---|---|
Wire diameter | The thickness of the circular profile wire |
Pitch length | Distance between adjacent thread peaks |
Hand direction | Right or left hand spiraling of threads |
Common filo profile cross-sections include round, half-round, square and rectangular. Major application fields of filo wire profiles:
Filo Steel Profile Applications
- Fencing, railing and balustrades
- Roofing and cladding
- Window frames and door panels
- Scaffolding, safety barriers
- Furniture and storage systems
- Automobile frames and chassis
- Shelving and partition systems
- Decorative finishes and trims
Filo profiles are often coated for protection against corrosion and weather effects. The forming process can incorporate operations like degreasing, cleaning, phosphating, chromating, galvanizing, powder coating etc.
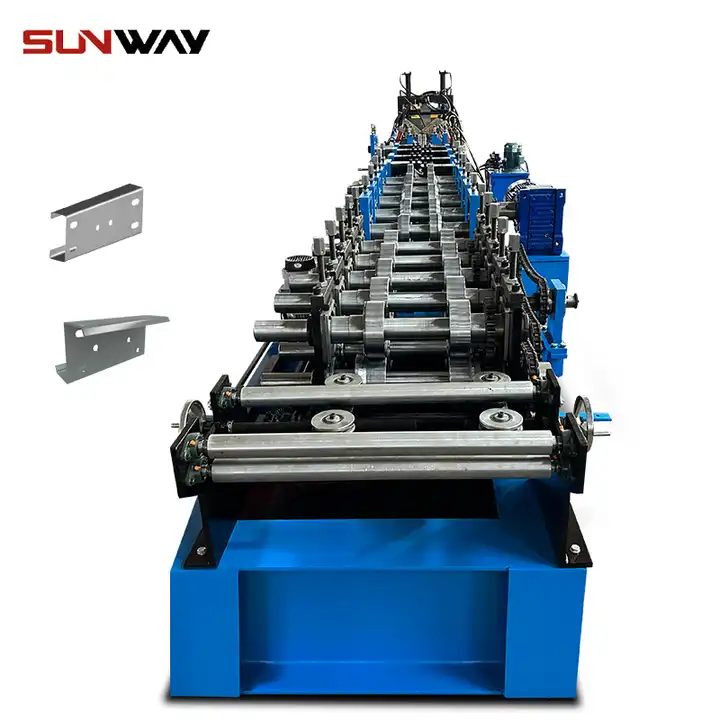
Filo Steel Roll Forming Equipment
The main components of a filo steel roll forming line are:
Key Sections of Filo Roll Forming Machine
- Coil handling system
- Feed table
- Forming stands
- Cutoff device
- আউটপুট টেবিল
- Controls and sensors
Coil Handling System
The coil handling system manages smooth uncoiling and feeding of the strip coil into the roll former. Key elements are:
- Coil loading mandrel or reel
- Coil straightener to correct coil curvature
- Decoiler with pinch rolls for controlled unwinding
- Coil guiding equipment
Feed Table
The feed table provides an extended flat section for adjusting strip positioning before it enters forming. This allows optimizing strip alignment for the first forming rolls.
Forming Stands
The forming section comprises of a series of roll stands each with male and female roller dies. Typical configurations have 10-16 stands placed in a zig-zag layout. The number of stands determines the length of progressive profile bending. More stands allow longer curve development for complex shapes.
On each stand, the rollers incrementally bend and twist the strip into the spiral filo form. Precise roller design and hash mark markings help achieve accurate thread pattern.
Cut Off Device
A rotating shear or cutoff saw cuts the continuously produced filo profile at preset lengths as per application. Cutter position can be adjusted to discard starting coil section containing irregularities.
Output Table
The finished cut filo lengths are collected on the exit table for downstream processing or storage. Various guiding equipment can be used for orderly output.
Controls and Sensors
Automated filo roll forming lines have controls for monitoring and coordinating different machine functions:
- PLC computer controls
- Line speed control
- Roller die adjustment
- Strip feed control
- Cutoff operation control
- Safety interlocks and limit switches
Sensors provide feedback on parameters like strip tension, thickness, position etc. This allows real-time control adjustments by the line computer.
Filo Steel Roll Forming Process
The roll forming process involves these main steps:
Filo Steel Roll Forming Process
- Loading and preparing strip coil
- Feeding strip into machine
- Initial forming through progression of stands
- Final filo profile shape achievement
- Cutting at preset length
- Collecting finished profiles
First, the steel coil is loaded on the rear mandrel and the tail end fed over the equipment. The decoiler regulates strip unwinding into the feed table.
As the strip enters the first forming stand, the roller dies make initial bends and twists. At each subsequent stand, the profile takes shape progressively.
Finally, the fully formed filo shape exits the last stand into the cutoff device for slicing at the required length. The cut pieces slide onto the exit table for further handling.
Effective filo profile rolling requires careful control of parameters like feed speed, strip alignment, inter-stand tension etc. Automated monitoring and adjustments are made by the line PLC system.
Filo Steel Roll Forming Machine Specifications
Main technical specifications of filo roll forming equipment:
Filo Steel Roll Forming Machine Specifications
Specification | Typical Values |
---|---|
Production Speed | 10 – 45 m/min |
Strip Width Range | 50 – 200 mm |
Strip Thickness Range | 0.5 – 2 mm |
Filo Diameter Range | 5 – 25 mm |
Pitch Length Range | 10 – 75 mm |
Length Tolerance | ± 1 mm |
Power Consumption | 10 – 30 kW |
Voltage | 380V or 415V AC 3 Phase |
Machine Weight | 8000 – 15000 kg |
Machine Dimensions | 10m x 3m x 3m (LxBxH) |
Higher end filo forming lines can achieve speeds of up to 80 m/min depending on the product shape and quality. The overall equipment length increases for slower forming of more intricate shapes.
Design and Customization
Filo roll forming machines can be customized to produce profiles as per desired size, pitch, and complexity. Key design factors include:
Filo Roll Forming Machine Design Factors
- Target filo shape and dimensions
- Type of input material – thickness, width, grade etc.
- Required output precision and surface finish
- Production speed and output volume
- Available space for machine installation
- Level of automation needed
The roller die tooling is specially engineered for the target filo profile using CAD software and CNC machining. The number of stands, decoiler capacity, and other parameters are selected accordingly.
Customized machine control programming allows flexibility in output length, speed adjustment, and production monitoring. Additional functionalities like coil joiners, loop control systems, runout tables etc. can be incorporated based on need.
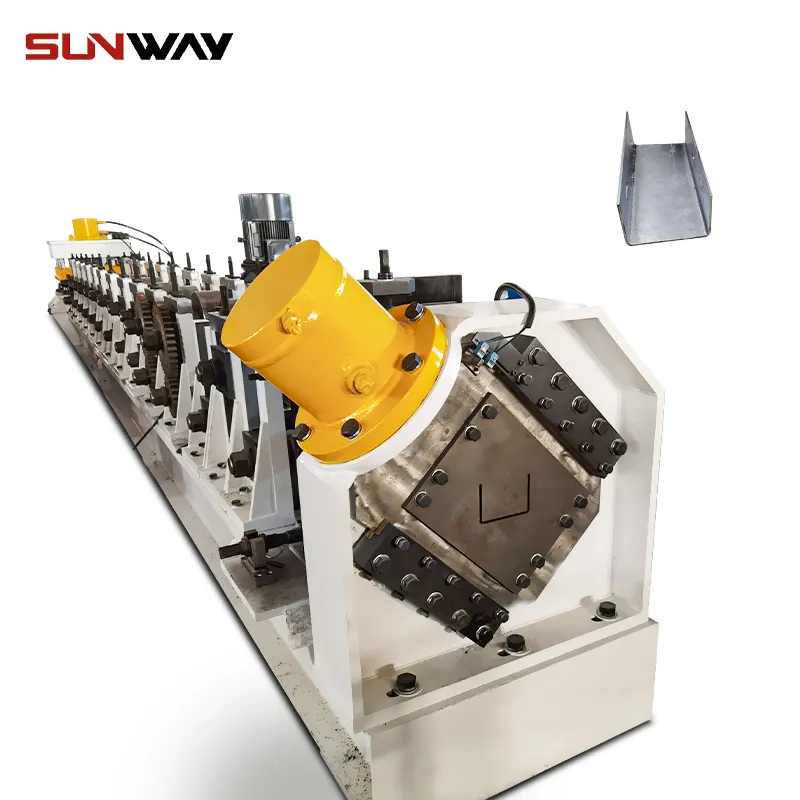
Filo Steel Roll Forming Machine Manufacturers
Some leading global manufacturers of filo steel roll forming equipment are:
Major Filo Roll Forming Machine Manufacturers
প্রতিষ্ঠান | Location |
---|---|
Ukrainian Engineering | Ukraine |
স্যামকো মেশিনারি | China |
Erdman Automation | Canada |
Metform | Turkey |
Gasparini | ইতালি |
TDW United Industries | Taiwan |
Everest Equipment | ভারত |
When selecting a supplier, factors like build quality, cost, production output levels, service support etc. must be evaluated. Getting technical advice from filo profile manufacturing experts is recommended.
Filo Steel Roll Forming Machine Pricing
Filo roll forming line cost depends on:
- Machine size and capacity
- Level of automation and additional features
- Customization needs
- Manufacturer’s brand value
Filo Roll Forming Equipment Price Range
Capacity | Price Range |
---|---|
Small up to 20 m/min | $75,000 to $150,000 |
Medium up to 45 m/min | $150,000 to $350,000 |
Large up to 80 m/min | $350,000 to $750,000 |
Larger machines with higher output, multiple features, and extensive customization can cost over $1 million. Selecting cost-effective equipment that meets current and future business requirements is advised.
Installation, Operation and Maintenance
Filo roll forming machines require these main steps for installation and setup:
- Positioning and leveling on flat foundation
- Anchoring and securing in place
- Connecting power and utilities
- Installation of decoilers andguiding equipment
- Positioning and aligning forming stands
- Setting up control panel
- Loading tooling and dies
- Calibration and trial runs
The supplier will provide complete guidelines for installation and commissioning. Proper machine anchoring, alignment, and calibration is critical for smooth functioning.
Filo Roll Forming Machine Operation
- The line is operated from the control panel
- Operating parameters like speed, cut length etc. are inputted
- Tooling maintenance and adjustments done if needed
- Automatic operation with real-time monitoring
- Output testing and quality checks performed
Periodic maintenance involves oiling, cleaning, visual inspections, and testing roller alignment. Preventive maintenance as per supplier schedule is recommended. Immediate investigation of any abnormal vibrations, noises or loosening is required.
How to Select a Filo Steel Roll Forming Machine Supplier
Follow these tips for choosing a filo roll former supplier:
Selection Criteria for Filo Roll Forming Machine
- Review product brochures and videos to gauge capability
- Assess technical expertise by interacting with their team
- Evaluate build quality of machines at their facility if possible
- Discuss after-sales service and spare parts support
- Compare costing and delivery time estimates
- Check client feedback and visit referrals if possible
- Select a supplier well-versed in your target applications
- Prioritize suppliers providing comprehensive service
Choosing an established manufacturer with proven equipment quality and customer service lowers project risk. Getting guidance from sector experts is advised.
Advantages and Limitations of Filo Steel Roll Forming
Benefits of Filo Steel Roll Forming Process
- High production speeds and volumes
- Flexible in producing different filo profiles
- Consistent and precise output quality
- Lower tooling costs than other methods
- Capable of forming high-strength steels
- Suitable for finishing sheets and panels
- Automated process requiring less labor
Limitations of Filo Steel Roll Forming
- Not economical for very low production quantities
- Size range restrictions based on machine design
- Precise roller design and machining required
- Skill needed for proper machine setup and operation
- Correct coil feed angles crucial for defect-free output
- Roll forming alone may not achieve requisite surface finish
Combining filo profile rolling with operations like cleaning, coating, oven curing etc. can overcome some limitations. Overall, roll forming remains a predominant continuous process for high-quality filo production.
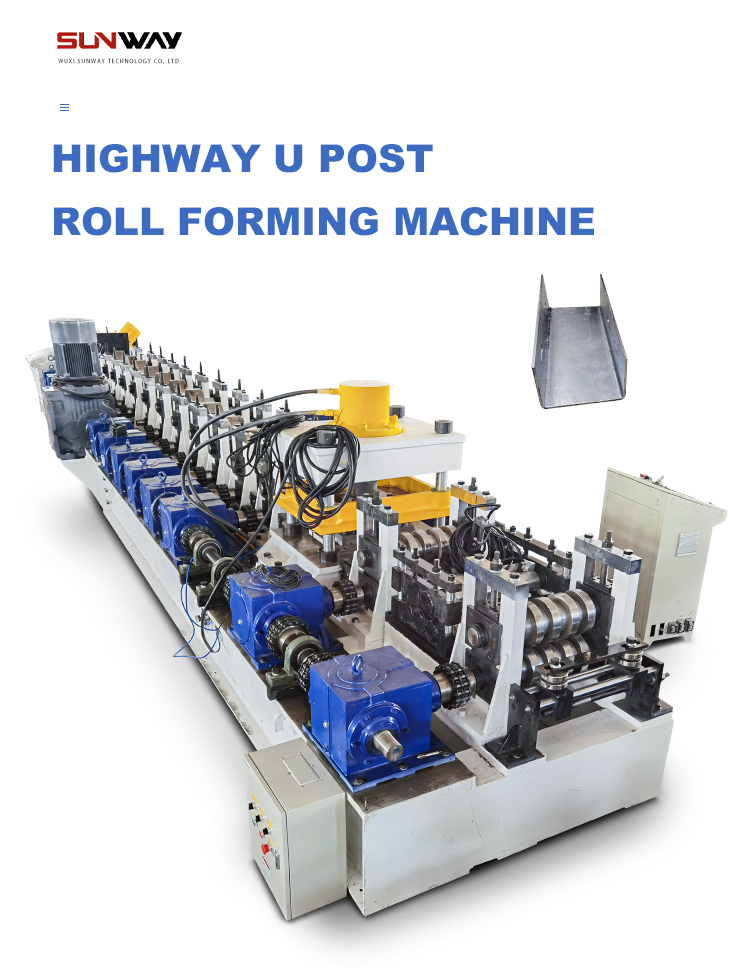
FAQ
Frequently Asked Questions on Filo Steel Roll Forming
Q: What materials can be filo roll formed?
A: Most low carbon steels, HSLA steels, stainless steels can be roll formed into filo profiles. With correct tooling design, even high strength steels, copper, aluminum is possible.
Q: What tolerances are achievable on filo diameter and pitch?
A: Tolerances within ±0.1mm on diameter and ±0.5mm on pitch length are typical for standard roll forming equipment. Higher precision machines can achieve ±0.05mm tolerances.
Q: Does filo profile quality depend on input strip quality?
A: Yes, high-quality defect-free input coil is essential for good filo rolling output. Any coil feed issues cause surface defects on the profiles.
Q: How easy is it to change tooling for different filo shapes?
A: Quick-change style tooling allows profile changes in 1-2 hours. Fixed tooling requires 6-8 hours for changing complete roller sets.
Q: What defects can occur in filo roll forming?
A: Common defects are scratch marks, fluting marks, waviness, twists, flat spots etc. caused by parameters like feed speed, strip alignment, roller gap etc.
Q: What safety is required when operating filo roll forming?
A: Machine safeguarding, emergency stops, lockouts, and PPE like cut-resistant gloves, safety glasses are mandatory when running and maintaining filo rolling mills.
Q: Can filo profiles be painted or coated after forming?
A: Yes, additional coating processes like powder coating, electroplating or painting can be performed on roll formed filo profiles if specified.
Q: Can filo roll forming make variable width profiles?
A: Yes, by oscillating certain roller dies filo profiles with gradually changing width can be produced. Special machine programming is required for this.
Q: Can filo roll forming machines handle stainless steel?
A: Yes, stainless can be filo formed but requires hardened tooling and lubricants to handle the higher strength and abrasiveness. Feed speeds are lower for stainless.