Renkli çelik yağmur borusu rulo şekillendirme makineleri çeşitli renklerde önceden boyanmış metal bobinlerden yağmur suyu iniş boruları ve olukları üretmek için kullanılır. Bu yağmur taşıyıcı bileşenler, binalar için çatı drenaj sistemlerinin temel parçalarıdır.
Bu kılavuzda yağmur borusu özellikleri, rulo şekillendirme makinesi türleri, bileşenleri, çalışma prensipleri, üretim hattı tasarım faktörleri, uygulamalar, avantajlar, sınırlamalar ve daha fazlası hakkında ayrıntılı bilgi verilmektedir.
Genel Bakış Renkli çelik yağmur borusu rulo şekillendirme makinesi
Renkli çelik yağmur borusu rulo şekillendirmenin temel adımları şunlardır:
- Boyalı metal bobinlerin bir dizi silindir kalıba beslenmesi
- Şeridin boru ve oluk profillerine kademeli olarak soğuk bükülmesi
- Yuvarlak, dikdörtgen veya yarım yuvarlak kesitlerin oluşturulması
- Boruların ve olukların belirtilen uzunluklarda sıralı olarak kesilmesi
- Bitmiş bileşenlerin otomatik istiflenmesi
- Senkronize üretim için PLC tabanlı kontroller
Önceden boyanmış galvanizli çelik, alüminyum ve alaşımlı kaplamalı çelik bobinler genellikle yağmur taşıyıcı bileşenlere rulo şeklinde şekillendirilir.
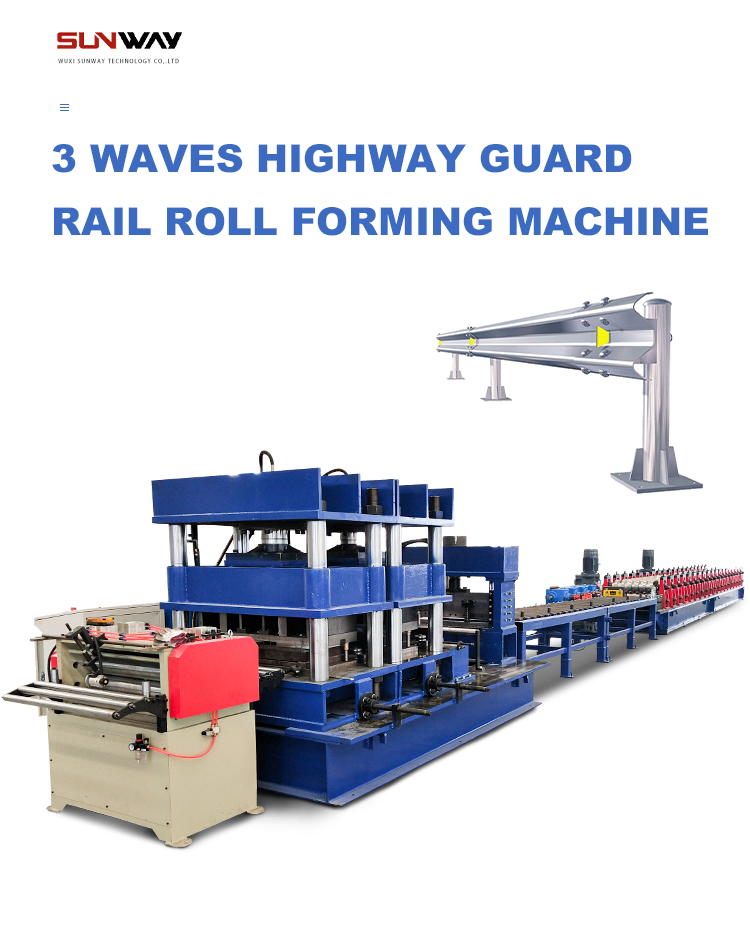
Yağmur Borusu Rulo Şekillendirme Makineleri Çeşitleri
İki ana tip boru rulo şekillendirici vardır:
1. Yuvarlak Boru Rulo Şekillendirme Makineleri
- Yuvarlak yağmur borusu bölümleri oluşturun
- Spiral şekillendirme yöntemi kullanın
- Boru çapı tipik olarak 80-150 mm
- Daha basit, düşük maliyetli tasarım
- Yaklaşık 10-15 m/dak hızlar
2. Yarım Yuvarlak Oluk Rulo Şekillendirme Makineleri
- Yarım yuvarlak ve dikdörtgen oluklar üretin
- Aşamalı rulo şekillendirme yöntemi
- Daha büyük profiller için daha geniş şekillendirme parçaları
- 25-40 m/dak hızlarda çalışın
Yağmur Borusu Rulo Şekillendirici Tiplerinin Karşılaştırılması
Parametre | Yuvarlak Boru | Yarım Yuvarlak Oluk |
---|---|---|
Şekillendirme yöntemi | Spiral | Sıralı |
Profil şekli | Yuvarlak | Yarım yuvarlak, dikdörtgen |
Boyut aralığı | 80-150 mm çap. | 100-300 mm genişlik |
Üretim hızı | 10-15 m/dak | 25-40 m/dak |
Kalıp maliyeti | Daha düşük | Daha yüksek |
Yağmur Borusu Haddeleme Hatlarının Bileşenleri
Renkli çelik yağmur borusu haddeleme hatları çeşitli ekipman modüllerinden oluşur:
Decoiler
- Renkli bobinleri prosese besler
- Gerginlik kontrolü ile donatılmıştır
Sac Besleme
- Bobin şeritlerini yönlendirir ve düzeltir
- Kalınlık izleme sensörleri
Rulo Şekillendirme İstasyonları
- Kademeli olarak profil oluşturmak için silindir kalıplar
- Destek silindirleri, kılavuzlar, presler
Boru Kesme
- Dönen kesiciler boruları boyuna keser
- Servo kontrol kesimi senkronize eder
Oluk Kesimi
- Kesme bıçakları olukları boyuna keser
- Uzunluk ölçüm enkoderleri
İstifleyici
- Yığınlar bitmiş borular ve oluklar
- Demetleme kayışları
Kontrol Sistemi
- HMI ile PLC kontrol paneli
- Sensörler, servo motorlar, güvenlik kilitleri
Konveyörler
- İş parçalarını istasyonlar arasında aktarır
- Motorlu makaralı konveyörler
Yağmur Borusu Haddeleme Hatlarının Çalışma Prensibi
Çalışma prensibi şunları içerir:
- Önceden boyanmış çelik bobinlerin besleme bölümüne açılması
- Şeridin progresif silindir kalıplardan geçirilmesi
- Şeridin boru veya oluk profiline kademeli olarak bükülmesi
- Şekillendirilmiş bileşenlerin döner makaslarla uzunlamasına kesilmesi
- Bitmiş boruların ve olukların otomatik istiflenmesi
- PLC kontrol sistemi otomatik üretim için hattı koordine eder
Modüler tasarım, profilleri değiştirmek için merdane setlerinin değiştirilmesine olanak tanır. Metal kalınlığı, profil boyutları ve hat hızı gibi parametreler takım boyutlarını belirler.
Yağmur Borusu Haddeleme Hatları için Tasarım Hususları
Yağmur borusu rulo şekillendirme hatları için temel tasarım faktörleri:
- Ürün boyutları - Boru çapları ve et kalınlıkları
- Metal şerit parametreleri - Bobin genişliği, ölçüsü, mukavemeti
- Üretim hızı - Dakikada üretilen fit veya metre boru
- Performans gereksinimleri - hassasiyet, değişim süresi
- Otomasyon seviyesi - operatör arayüzü, güvenlik
- Rulo takımları - tasarım, hızlı değişim yeteneği, sağlamlık
- Malzeme taşıma - Bobin kapasitesi, konveyörler, istifleyiciler
- Genişletilebilirlik - Gelecekteki kapasiteyi artırma yeteneği
- Genel ayak izi - Mevcut alan içinde yerleşim
Üretim hedefleri ile rainware boyutlarının eşleştirilmesi, optimum bileşen boyutlandırmasını ve yerleşimini belirler.
Renkli Çelik Yağmur Borusu Haddeleme Makineleri Uygulamaları
Haddelenmiş metal yağmur boruları ve olukların temel uygulamaları:
- Çatı drenaj sistemleri
- Yağmur suyu hasadı için iniş boruları
- Açık alanlar için drenaj boruları
- Özel araçlar için oluklar
- Konut dışı büyük çatı drenajı
- Mimari estetiğe uygun renk
- Korozyon direnci gerektiren kıyı/deniz uygulamaları
Boyalı yağmurluk bileşenleri, bina dış cephelerine uygun renk seçenekleriyle korozyona karşı koruma sağlar.
Renkli Çelik Yağmur Borusu Haddeleme İşleminin Faydaları
Metal yağmur borusu rulo şekillendirme işleminin avantajları:
- Yüksek üretim hızları ve hacimleri
- Bobinlerden sürekli proses
- Tutarlı boyutsal doğruluk
- Geleneksel üretime kıyasla daha düşük maliyetler
- Geniş renk yelpazesi seçenekleri
- Otomatik üretim kaliteyi artırır
- Minimum hurda oluşumu
- Tam zamanında tedarik, teslim sürelerini iyileştirir
- Boyutları değiştirme esnekliği
- Saha inşaat yöntemlerinden daha güvenli
Otomatik rulo şekillendirme, yağmur eşyası bileşenlerinin verimli ve uygun maliyetli üretimini sağlar.
Renkli Çelik Yağmur Borusu Haddeleme Sınırlamaları
Renkli çelik yağmur borusu rulo şekillendirme işleminin bazı sınırlamaları:
- Ekipman için yüksek ilk yatırım
- Profil başına özel ekipman hatları
- Karmaşık takım tasarımı ve işleme
- Operasyon için kalifiye teknisyenler gerektirir
- Düzgün kontrol edilmezse bobin sıkışması riski
- Sadece düz kesitlerle sınırlıdır
- Boyut değişiklikleri için hat değiştirme duruş süresi
- Önemli alan gereksinimi
- Hafifletme gerektiren gürültülü olabilir
Süreç, düşük hacimli veya seri üretim için uygun olmayabilir.
Yağmur Borusu Haddeleme Ekipmanının Anahtar Üreticileri
Renkli çelik yağmur borusu rulo şekillendirme ekipmanlarının önde gelen küresel tedarikçilerinden bazıları şunlardır:
Başlıca Yağmur Borusu Rulo Şekillendirici Üreticileri
Şirket | Konum |
---|---|
Gasparini | İtalya |
Metform | ABD |
Şangay Metal Şirketi | Çin |
Voestalpine Rulo Şekillendirme | Avusturya |
Jouanel | Fransa |
ABC Rollforming | Kanada |
Samco Makine | Hindistan |
Bu şirketler standart ve özelleştirilmiş rainware rulo şekillendirme ekipmanları sunmaktadır. Komple üretim hatları, açıcılar, şekillendirme standları, kesme, istifleme ve paketlenmiş paketleme modüllerini içerir.
Tipik Ekipman Maliyet Aralıkları
Üretim Hızı | Gösterge Niteliğinde Fiyatlandırma |
---|---|
10 m/dak | $100,000 – $250,000 |
25 m/dak | $250,000 – $500,000 |
40 m/dak | $500,000 - $1 milyon |
60 m/dak+ | $1 milyondan fazla |
Fiyatlandırma üretim hızına, otomasyon özelliklerine ve hat aksesuarlarına göre değişir.
Kurulum ve Çalıştırma Yönergeleri
Renkli çelik yağmur borusu rulo şekillendirme hatlarının kurulumu ve işletimi için temel önlemler:
- Güvenli malzeme taşıma için zemin alanı tahsisi
- Ekipmanın uygun şekilde sabitlenmesi ve tesviye edilmesi
- Elektrik, pnömatik ve hidrolik bağlantılar
- Ürün kalitesini doğrulamak için deneme çalışmaları
- Şekillendirme parametrelerinin ve ayarlarının belgelenmesi
- Prosedürler hakkında operatör eğitimi
- Kilitler, E-durdurmalar gibi güvenlik protokolleri
- Rutin bakım programları
- üreticinin tavsiyelerine uyarak
Üretkenliği ve güvenliği optimize etmek için doğru kurulum, çalıştırma eğitimi ve bakım şarttır.
Bakım Uygulamaları
Renkli çelik yağmur borusu rulo şekillendirme hatları için ana bakım faaliyetleri:
- Mekanik tahriklerin periyodik muayenesi
- Motorların, yatakların, dişlilerin yağlanması
- Sensörlerin temizlenmesi ve izlenmesi
- Merdane takımlarının durumunun kontrol edilmesi
- Makas bıçaklarının bilenmesi/değiştirilmesi
- Hidroliklerin ve boruların incelenmesi
- Sensörlerin doğrulanması ve kalibrasyonu
- Güvenlik kilitlerinin ve durdurucuların test edilmesi
- Havalandırma, sıcaklık ve gürültü izleme
- Planlanmamış arıza sürelerini önlemek için zamanında onarımlar
Düzenli önleyici bakım, ekipman ömrünü, üretim çalışma süresini ve güvenliği artırır.
Yağmur Borusu Rulo Şekillendirme Ekipmanı Seçiminde Dikkat Edilecek Hususlar
Yağmur borusu rulo şekillendirme ekipmanı seçimi için temel faktörler:
- Üretim kapasitesi - nominal hızlar gereksinimlerle eşleşir
- Profil boyutları - İhtiyaç duyulan ebatlarda üretim kabiliyeti
- Rulo takım esnekliği - hızlı değiştirme, kolay kullanım
- Hammadde parametreleri - belirtilen bobin kalınlığı için uygun
- Hat otomasyonu - kullanım ve kontrol kolaylığı
- Güvenlik özellikleri - acil durdurmalar, erişim kısıtlamaları
- Performans özellikleri - hız, hassasiyet, esneklik
- Kalite standartları - boyutsal tutarlılık
- Servis desteği - kurulum, eği̇ti̇m, bakim
- Tedarikçi itibarı - kanıtlanmış deneyim, güvenilirlik
- Maliyetler - performans düzeyi için rekabetçi fiyatlandırma
İhtiyaç duyulan profilleri bütçe ve teslim süresi kısıtlamaları dahilinde teslim edebilecek yerleşik bir üreticinin seçilmesi tavsiye edilir.
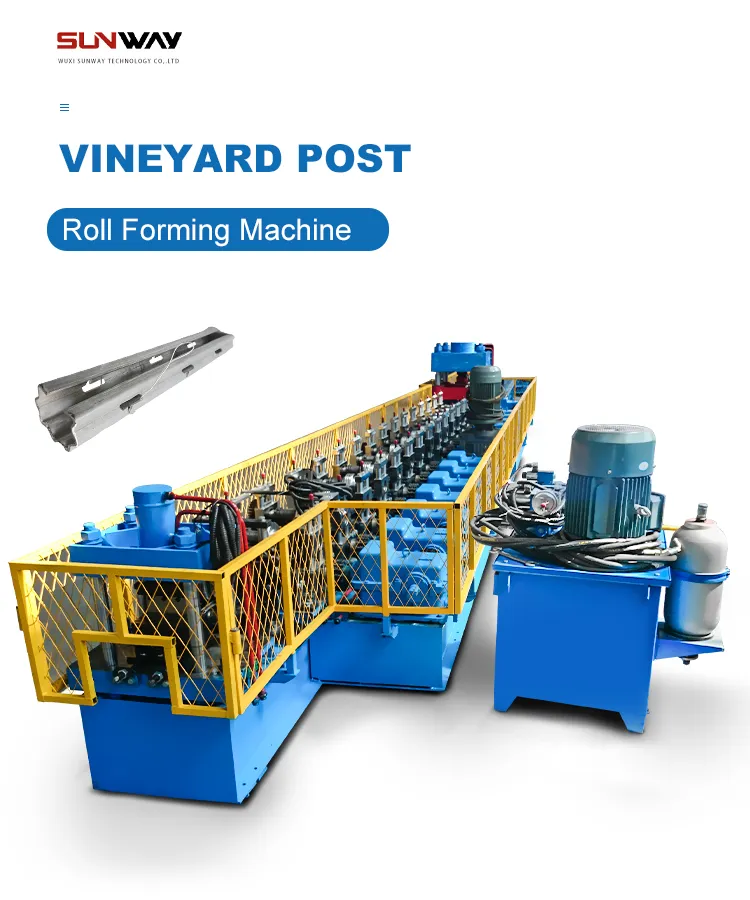
Artıları ve Eksileri Renkli çelik yağmur borusu rulo şekillendirme makinesi
Avantajlar:
- Yüksek üretim oranları ve hacimleri
- Tutarlı ve doğru boyutlar
- Düşük operasyonel maliyetler
- Minimum hurda oluşumu
- Daha iyi kalite kontrolü için otomatikleştirilmiş
- Saha imalatına göre daha güvenli çalışma
- Boyut değiştirme esnekliği
- Geniş renk seçeneği
Dezavantajlar:
- Yüksek başlangıç sermaye harcaması
- Profil başına özel hatlar
- Nitelikli insan gücü gerekli
- Bobin sıkışması riski
- Düz kesitlerle sınırlı
- Önemli alan gereksinimleri
- Boyut değişiklikleri için değişim duruş süresi
- Hafifletme gerektiren gürültülü olabilir
SSS
Yağmur boruları için hangi malzemeler kullanılır?
Yaygın malzemeler arasında önceden boyanmış galvanizli çelik, alüminyum ve alaşımlı kaplamalı çelik bulunur. Bunlar korozyon direnci ve renk kaplama seçenekleri sağlar.
Rainware üretimi için hangi süreçler kullanılıyor?
Yağmur boruları ve oluklar genellikle metal bobinlerin otomatik rulo şekillendirilmesiyle üretilir. Bu, sürekli yüksek hacimli üretime olanak sağlar.
Metal ve plastik yağmurlukların faydaları nelerdir?
Metal, plastiğe kıyasla daha yüksek mukavemet, darbe direnci, daha uzun hizmet ömrü ve daha iyi estetik sağlar. Boyalı metaller renk seçenekleri sunar.
Yağmur borusu rulo şekillendiricileri için hangi bakım gereklidir?
Düzenli bakım, mekanik bileşenlerin, rulo aletlerinin, hidroliklerin, sensörlerin ve güvenlik özelliklerinin incelenmesini içerir. Zamanında yapılan bakım, planlanmamış duruş sürelerini en aza indirir.
Boru rulo şekillendirme için hangi güvenlik önlemleri önemlidir?
Kritik güvenlik önlemleri arasında acil durdurmalar, erişim kısıtlamaları, kilitler, korumalar, işçi eğitimi ve gerekirse gürültünün azaltılması yer alır.
Yağmur borusu rulo şekillendirme ekipmanı tedarikçisi nasıl seçilir?
Üretim kapasitesini, hat otomasyonunu, rulo esnekliğini, servis desteğini ve maliyetleri göz önünde bulundurun. Üretim hacimlerinize ve boru boyutlarınıza uygun güvenilir bir üretici seçin.
Boru haddehaneleri hangi üretim hızlarına ulaşabilir?
Tipik hızlar makine boyutuna bağlı olarak dakikada 10 ila 60 metre arasında değişir. Açıcılara ve otomatik istifleyicilere sahip daha büyük rulo şekillendiriciler daha yüksek üretim hızlarına ulaşabilir.
Yağmur borusu haddeleme ekipmanının maliyetini hangi faktörler belirler?
Temel faktörler üretim hızı, otomasyon seviyesi, takım tasarımı, genel hat aksesuarları ve özelleştirme ihtiyaçlarıdır. Maliyetler bölgesel faktörlere de bağlıdır.