The ag classic rib roof roll forming machine is an essential equipment for manufacturing ribbed metal roofing panels and decking sheets efficiently. This guide provides a comprehensive overview of ag classic rib roof roll forming machines, their working, types, applications, specifications, suppliers, installation, operation, maintenance, and selection criteria.
Overview of Ag Classic Rib Roof Roll Forming Machine
The ag classic rib roof roll forming machine is used to form metal coil into roofing panels and sheets with ribbed or corrugated profiles. These machines utilize a series of roller dies to bend and shape the sheet metal into the desired rib shapes as it passes through the different forming stations.
Some key features of ag classic rib roof roll formers:
- High production efficiency and speeds up to 25 m/min
- Capability to produce different rib profiles and heights
- Quick roll change design allows fast profile changes
- Robust all-steel welded construction for durability
- Advanced PLC control system for precision and automation
- Safety features like sheet guiding equipment and protections
Main Components
The major components of an ag classic rib roof forming machine include:
Component | Description |
---|---|
Uncoiler | Holds metal coil and feeds into the roll former |
Feeder | Feeds metal sheet into forming stations at set speed |
Forming stations | Each station progressively forms the rib shape |
Punching unit | Punches holes if required |
Hydraulic system | Provides power for forming operations |
Control system | PLC and HMI for controlling and monitoring machine |
Roll-changing system | Allows quick roll die change for profile change |
Working Principle
The working principle involves:
- Sheet metal coil loaded onto the powered unwinding reel
- Sheet gets fed into the feeder at a constant speed
- Forming rollers bend the sheet progressively into the ribbed shape
- Punching unit punches holes if needed for fastening
- Formed corrugated sheet gets collected continuously at the exit
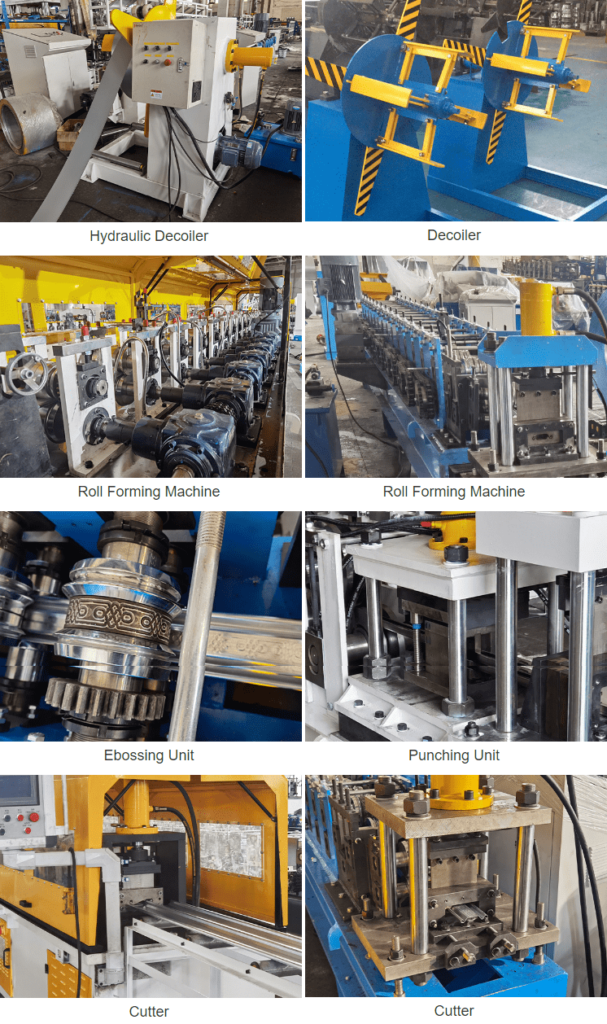
Types of Ag Classic Rib Roof Forming Machines
Ag classic rib roof formers are available in different types based on:
1. Number of corrugations:
- Single rib machine
- Double rib machine
- Multi-rib machine
2. Roofing sheet width capacity:
- Narrow width up to 800mm
- Standard width up to 1250mm
- Wide width up to 2100mm
3. Rib sheet metal thickness:
- Light gauge 0.35 – 0.8mm
- Regular gauge 0.8 – 2.0mm
- Heavy gauge above 2.0mm
4. Level of automation:
- Manual rattling and roll change
- Semi-automatic with powered features
- Fully automatic PLC-controlled
Applications of Rib Roof Forming Machines
Ag classic rib roof forming machines are used to manufacture:
- Trapezoidal roofing sheets
- Corrugated roofing sheets
- Decking and structural sheets
- Cladding sheets
- Wall panel profiles
- Roof drainage sheets
- Architectural and decorative sheets
These ribbed metal roofing products are used widely in:
- Industrial and commercial buildings
- Warehouses and factories
- Residential roofing
- Steel structure buildings
- Pre-engineered buildings
- Agricultural sheds and outhouses
- Roof drainage and rainwater collection
Technical Specifications
The main technical specifications of ag classic rib roof formers include:
पैरामीटर | Specifications |
---|---|
Coil Width Capacity | 800mm to 2100mm |
Sheet Thickness | 0.35mm to 3mm |
Rib Height Range | 15mm to 150mm |
बनाने की गति | 8 – 25 m/min |
Number of Stands | 16 – 24 stands |
बिजली की आपूर्ति | 380V or 415V AC, 3 Phase |
Motor Power | 5.5kW to 11kW |
Machine Dimensions | 8000mm x 1200mm x 2200mm |
Machine Weight | 8000kg to 12000kg |
Design and Construction
The ag classic rib roof forming machine has an all-steel fabricated construction and is designed for heavy-duty performance:
- चौखटा – Made from welded steel plates and beams providing rigidity
- Roll housings – Fabricated from thick steel plates for stability under loads
- Rolls – Hardened steel with ground and polished forming surfaces
- Bearings – Heavy-duty roller bearings in cast iron housings
- Transmission – Hardened and ground gears and sprockets with chains
- ** Guards** – Steel sheet metal guards for safety protections
- PLC Control – Controls all electric motors, sensors, operations and HMIs
The structural design ensures minimal vibrations, precision forming and long service life.
Roll Tooling Design Standards
The roll dies and tooling for the ag classic rib roof former are designed as per international standards:
- Rib profile shape as per AISI, AS/NZS standards
- Roll materials follow DIN EN10263 steel grades
- Hardness levels between 50-60 HRC
- Surface roughness of Ra 0.4μm to 0.8μm
- Roll concentricity within 0.005mm
- ISO 2768 tolerance grades for rib dimensions
- RoHS compliance for eco-friendliness
Precision roll tooling is essential for producing high-quality ribbed roofing sheets efficiently.
Manufacturing Capabilities
The ag classic rib roof forming machine can manufacture roofing sheets and panels to meet industry requirements:
Sheet Width
- Narrow width up to 800mm
- Standard width up to 1250mm
- Wide width up to 2100mm
Sheet Thickness
- Light gauge 0.35mm to 0.8mm
- Regular gauge 0.8mm to 2.0mm
- Heavy gauge over 2.0mm
Rib Dimensions
- Height from 15mm to 150mm
- Pitch/spacing from 180mm to 350mm
Hole Punching
- Holes diameter up to 20mm
- Hole spacing/pitch up to 300mm
- Round, slotted, elongated holes
Advanced Features
- Quick roll changing
- Edge curling device
- Automatic stacker
- Profile counting
- Entry tables and exit conveyors
Suppliers and Pricing
Some leading manufacturers and suppliers of ag classic rib roof forming machines include:
Supplier | Location | Price Range |
---|---|---|
Ag Machinery | China | $10000 – $50000 |
RoofRoll Tech | भारत | $15000 – $80000 |
Railelectric Corp | Europe | $18000 – $100000 |
Jindezhen Machinery | China | $12000 – $60000 |
Hansoo Engineering | South Korea | $20000 – $90000 |
- Entry-level – $15000 to $30000
- Mid-range – $40000 to $60000
- Heavy-duty – $80000 to $150000
Pricing varies based on speed, width, automation levels, and optional accessories.
Installation and Commissioning
Installing an ag classic rib roof forming machine involves:
- Positioning on a flat leveled floor
- Leaving minimum 1000mm space around for access
- Leveling within 0.5mm tolerance using shims
- Securing foundation bolts to the floor
- Aligning machine sections and drives
- Checking power supply connections
- Filling lubricants in gears and bearings
- Testing running empty and with sheets
- Setting machine parameters and limits
- Testing safety functions
- Debugging and optimizing operations
Vendors provide installation guidance documentation and certified technicians to support the roll forming machine installation.
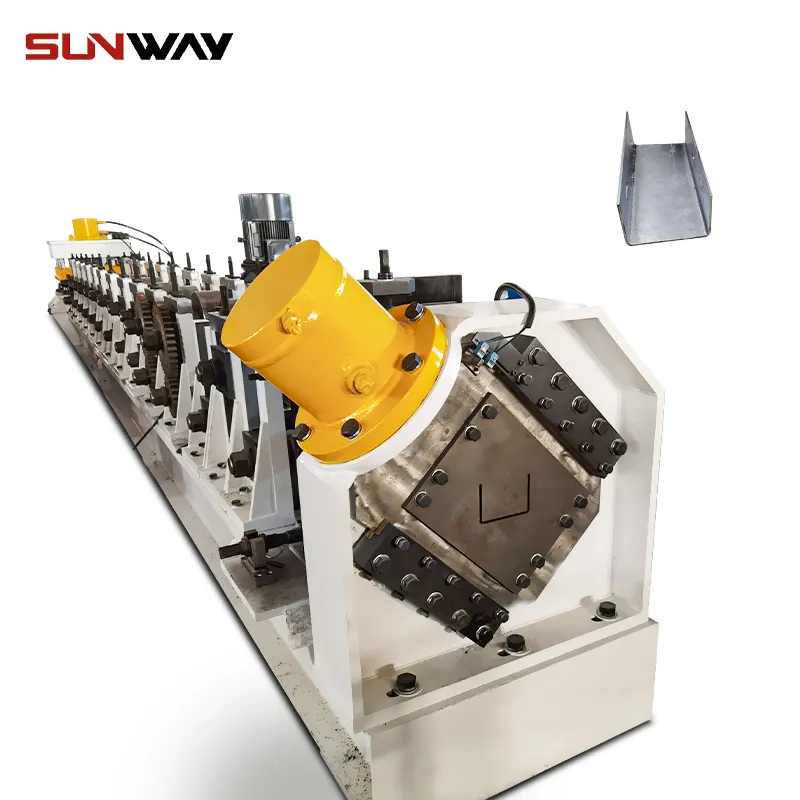
Operation and Working
Operating the ag classic rib roof forming machine involves:
Pre-checks
- Power supply availability
- Lubrication levels
- Hydraulic oil level
- Emergency stop check
- Rolls condition and clearance
- Feeder ready
Starting
- Switch ON control power
- Start hydraulic pumps
- Jog feeder and rolls slowly to check
- Set speed and parameters
- Thread the sheet through the rolls
- Activate edge guidance system
- Increase speed progressively to production
Running
- Monitor roll current and hydraulics pressure
- Check formed sheets quality continuously
- Watch for any abnormal noise or vibration
- Ensure steady sheet flow without jamming
- Regulate parameters to control profile dimensions
- Count produced sheets
- Stack sheets properly at exit conveyor
Stopping
- Reduce speed gradually to zero
- Retract feeder to last formed sheet position
- Switch off hydraulic pumps
- Switch off control power
- Properly collect and stack remaining sheets
Maintenance and Inspection
To sustain performance, the ag classic rib roof forming machine needs regular maintenance:
Daily
- Clean machine surfaces and remove sheet debris
- Check hydraulics, lubricants, oil levels
- Check for abnormal temperature or noise
- Check all fasteners and bolts are tight
- Check roll edge clearances
Monthly
- Clean and inspect all bearings and gears
- Grease bearings and lubricate drives
- Verify alignments, backlash, tolerances
- Check wear on guiders and roll surfaces
Quarterly
- Test emergency stop and safety functions
- Check electrical connections and panel
- Verify hydraulic hoses and cylinders
- Change hydraulic oil and filter
Yearly
- Complete inspection of components
- Flush coolant and lubrication systems
- Replace worn parts like belts, chains
- Coat machine surfaces for corrosion protection
Keeping logbooks and maintenance schedules is beneficial for proper upkeep.
How to Select the Rib Roof Forming Machine
Selection of the ideal ag classic rib roof forming machine depends on:
1. Production Requirements
- Roofing sheet dimensions
- Rib profile and height
- Metal thickness and grade
- Output speed and volume
2. Machine Specifications
- Sheet width capacity
- Thickness range
- Number of corrugation stations
- Speed and power
3. Automation Level
- Manual, semi-auto, or fully auto
- Type of control system
- Handling and stacking needs
4. Quality Standards
- Roll tooling design standards
- Precision and repeatability
- Vibration control features
- Sheet guiding method
5. Supplier Credentials
- Experience and past installations
- Local presence for support
- Compliance to safety standards
- Roll tooling design expertise
- Training services offered
Selecting the right ag classic rib roof forming machine model ensures the roofing production requirements are fulfilled reliably and efficiently.
Comparison Between Machine Models
Here is a comparison between two ag classic rib roof forming machine models:
पैरामीटर | Model RRF-16 | Model RRF-20 |
---|---|---|
Sheet Width | 1000mm | 1500mm |
Sheet Thickness | 0.5-1.6mm | 0.4-2.0mm |
Rib Height | 25-120mm | 20-150mm |
Speed | 10m/min | 15m/min |
शक्ति | 7.5kW | 11kW |
Stands | 16 | 20 |
Control | Semi-auto | Fully-auto PLC |
Roll Change | Manual | Powered |
Price | $45000 | $95000 |
The RRF-20 is wider, more automated, faster and can handle heavier sheets compared to RRF-16. But the RRF-16 is adequate for small to medium production needs and is lower cost.
Pros and Cons
Advantages
- High production efficiency and output
- Flexible to produce different rib profiles
- Durable and robust construction
- Advanced safety protections
- Lower operating costs than alternate methods
- Consistent quality and close tolerances
Limitations
- High initial investment cost
- Regular maintenance required
- Roll changing needs downtime
- Limited sheet metal strength and ductility
- Need skilled labor for operation and maintenance
- Fixed setup restricts profile changes
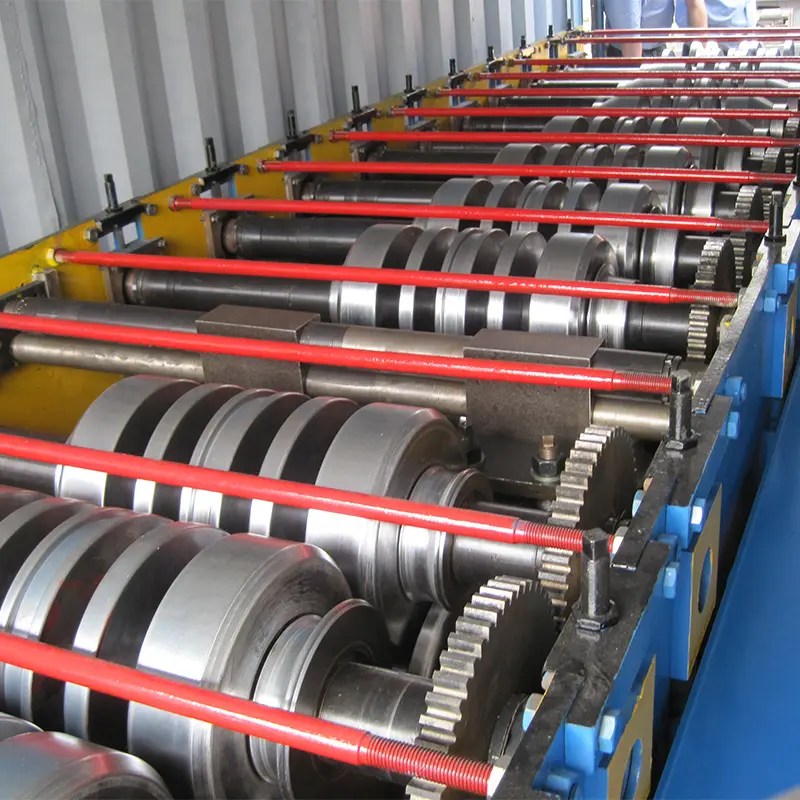
सामान्य प्रश्न
Q: What sheet metal can be formed on these machines?
A: Commonly Mild steel, galvanized steel, aluminum, stainless steel within ductility limits.
Q: What rib profiles can be produced?
A: Trapezoidal, sinusoidal, curved, angular profiles of different heights and spacing.
Q: What are the key maintenance aspects?
A: Lubricating rolls and drives, inspecting tooling wears, checking alignments and clearances, testing safety systems.
Q: What sheet guiding methods are used?
A: Roller side guiders, inner expandable guiders, edge pressing rolls, steering rolls.
Q: What automation levels are available?
A: Manual handling, semi-auto with power features, and fully automated with stacking.
Q: How quick is the roll changing process?
A: 10-20 minutes for manual changing. Less than 5 minutes for automatic powered roll changing.
Q: What secondary operations can be integrated?
A: Cutting, hole punching, notching, length cutoff, edge hemming and molding.
Q: What factors affect the price?
A: Width, speed, automation level, power specs, added accessories like auto stacker.
निष्कर्ष
The ag classic rib roof roll forming machine provides efficient on-site production of quality ribbed roofing sheets. With a range of models, widths, automation levels, speeds, and capabilities – these roll formers meet requirements for small workshops to large industrial roofing manufacturers. By selecting the appropriate machine specifications based on the roofing profiles, metal properties, quality needs and production volumes – manufacturers can benefit from fast setup, lower operation costs, and flexible manufacturing. With regular maintenance and skilled operation, the ag classic rib roof forming machines perform reliably for years of roofing production.