Vue d'ensemble de l'OF Profileuse pour profilés de plafond
Les profileuses pour profilés de plafond sont utilisées pour produire les profilés en C utilisés pour les plafonds suspendus. Ces profilés légers s'emboîtent sur les profilés en T de l'ossature du plafond pour soutenir les panneaux de plafond.
Ce guide fournit une vue d'ensemble des principes de fonctionnement des dérouleurs de plafond, des composants, des spécifications, des dimensions, des configurations, des accessoires, des applications, des avantages, des fabricants, des coûts, des considérations relatives à l'achat, de l'entretien et des conseils de dépannage.
Comment fonctionne le profilage des rails de plafond
La séquence de fonctionnement d'une profileuse à canal de plafond est la suivante :
- Bobine de tôle chargée dans le dérouleur
- La feuille entre dans la planeuse pour un premier redressement
- Tôle nivelée introduite dans les guides d'entrée de la section de formage
- La feuille passe par des cages de formage consécutives
- Les rouleaux plient progressivement la feuille pour lui donner la forme d'un canal en C
- Les sections de canal formées sortent sur la table de coupe
- La lame de scie coupe les profilés à la longueur souhaitée
- Le convoyeur empile les pièces coupées pour les mettre en paquets
- Le groupe hydraulique alimente les stations de roulage
- La commande PLC coordonne la séquence de production
Les rouleaux sont usinés avec précision pour plier les bobines de métal en profilés de plafond.
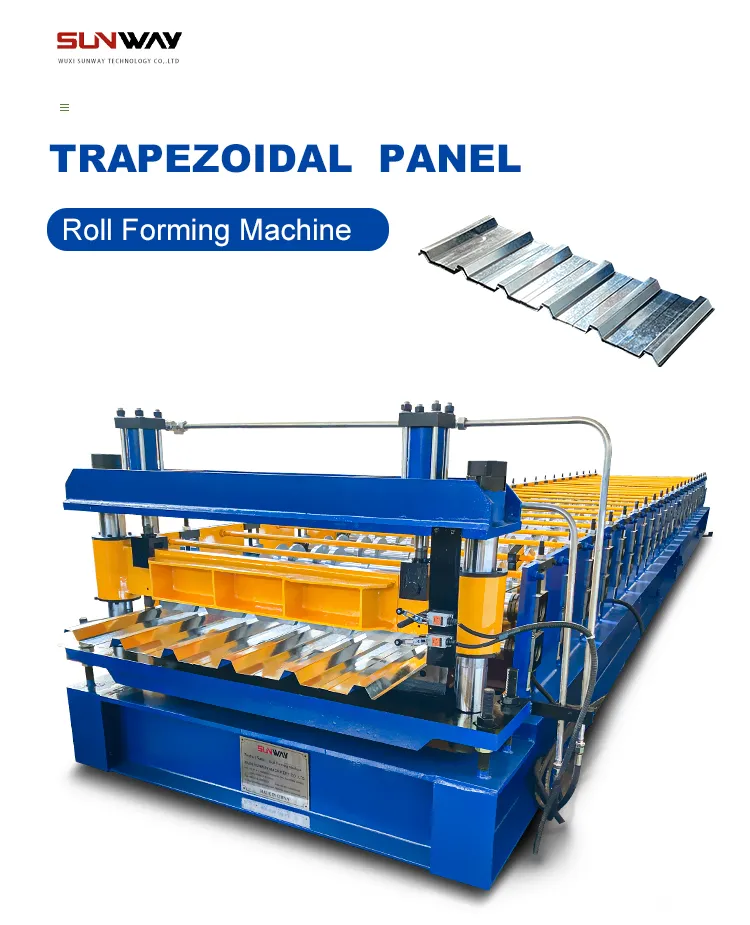
Principaux composants des profileuses pour profilés de plafond
Composants clés de la Machines de formage de profilés de plafond:
- Dérouleur - Maintient la bobine de tôle
- Table d'alimentation - Introduit la tôle dans la machine
- Stations de formage de rouleaux - Former progressivement la forme du canal
- Rouleaux de formage - Acier à outils trempé, usiné au profil
- Unité de coupe - Scie circulaire ou cisaille
- Table empilable - Attrape les pièces coupées et les empile
- Unité de regroupement - Strappe les pièces en paquets
- Système hydraulique - Fournit de l'énergie aux stations
- Armoire électrique - Automates programmables, variateurs, commandes de moteur
- Gardiennage - Pour la sécurité de l'opérateur pendant la production
L'intégration correcte de ces composants permet de produire des canalisations de plafond de qualité.
Spécifications des profilés de plafond
Spécifications typiques :
Paramètres | Spécifications |
---|---|
Diamètre du rouleau | 100-150 mm |
Nombre de stations | 8-16 |
Vitesse maximale de la ligne | 15 m/min |
Épaisseur minimale de la tôle | 0,4 mm |
Épaisseur maximale de la tôle | 0,8 mm |
Largeur de la feuille | 50-200 mm |
Hauteur du canal | 13-50 mm |
Longueurs de coupe | 1-6 mètres |
Puissance du moteur principal | 3-5,5 kW |
Le nombre de stations et la puissance du moteur déterminent le taux de production. Un plus grand nombre de stations permet d'augmenter la taille des canaux.
Types de profilés de rail de plafond produits
Profilés de plafond courants produits :
- Canal standard de 13/16" - pour les plafonds résidentiels
- Canal étroit de 9/16" - pour les espaces plus restreints
- Caniveaux profonds - jusqu'à 2" pour les travaux lourds
- Caniveaux à double jambe - clips sur les deux côtés
- Canaux d'ombres - éclairage encastré
- Canaux perforés - pour l'absorption du son
- Canaux décoratifs - pointillés, gaufrés, etc.
Des jeux de rouleaux interchangeables permettent de réaliser différents profils.
Configurations des profilés de plafond
Les configurations typiques des machines sont les suivantes :
- Compact - Guides d'entrée à scier dans un cadre
- Modulaire - Sections assemblées par boulonnage pour la portabilité
- En ligne - Directement du dérouleur à la sortie
- En forme de L - Gain d'espace au sol
- Boucle fermée - Enrouleur côté sortie
- Sur mesure - Flexibilité de l'agencement de l'atelier
- Semi-auto - Chargement manuel des bobines
- Entièrement automatique - Dérouleur motorisé, empileur, etc.
Les aménagements sont conçus en fonction de l'espace de production et des besoins d'automatisation.
Accessoires pour les profilés de plafond
Les accessoires les plus courants sont les suivants
- Unité de poinçonnage - Pour les trous, les fentes, les motifs
- Cylindres de gaufrage - Textures de surface décoratives
- Cintrage CNC - Imprime des courbes lorsque c'est nécessaire
- Entaille - Perforer des encoches le long du bord
- Avance servo du rouleau - Pour la rapidité et la précision
- Kits de changement rapide - Pour des changements de profil rapides
- Garde-corps de sécurité - Clôture périmétrique complète
- Mandrin de dérouleur - Nécessaire pour le maintien de la bobine
- Protection de l'outillage - Couvertures pour porte-rouleaux
- Conduit sur mesure - Pour l'alimentation de bobines façonnées
Les accessoires améliorent la flexibilité, la productivité et la sécurité.
Applications des panneaux de plafond
Les profilés de caniveau de plafond produits sur ces profileuses à rouleaux sont utilisés dans.. :
- Plafonds résidentiels - Maisons, appartements
- Bâtiments commerciaux - Bureaux, espaces commerciaux
- Espaces institutionnels - Écoles, hôpitaux
- Secteur de l'hôtellerie et de la restauration - Hôtels, gymnases
- Chambres propres - Pharma, médical, agroalimentaire
- Bâtiments modulaires - Structures préfabriquées
- Accessoires en magasin - Stands d'exposition, signalisation
- Stands d'exposition - Stands temporaires, auvents
Les rails de plafond constituent un moyen économique et facile de créer des plafonds suspendus dans tous les secteurs.
Avantages du profilage des rails de plafond
Principaux avantages du profilage des profilés de plafond :
- Une production plus rapide que le pliage manuel
- Coût moins élevé que les canaux extrudés
- Grande précision dimensionnelle de l'outillage de précision pour les rouleaux
- Zéro rebut par rapport à d'autres méthodes
- Qualité constante sur toute la longueur
- Flexible pour différents profils et tailles
- Empreinte compacte adapté à la production locale
- Un fonctionnement plus sûr que les presses plieuses ou l'encochage
- Production évolutive des petits aux grands volumes
Les canaux formés par laminage sont plus performants que les autres méthodes de fabrication en termes de qualité, de coût et de livraison.
Principaux fabricants de machines à canaux pour plafonds
Les principaux fabricants de profileuses pour canaux de plafond sont les suivants
- Eurobend - Lignes à grande vitesse d'ingénierie européenne
- Metform - Solutions de profilage personnalisées
- Jupiter Rollforming - Des machines robustes fabriquées en Inde
- RollMax - Des machines abordables de grande qualité
- Zhongfu - Large gamme de modèles de profileuses
- Samco - Lignes de production intégrées avec gaufrage et poinçonnage
Considérations sur les coûts
Facteurs typiques influant sur les coûts des laminoirs à profilés de plafond :
- Vitesse de production - Influence directe sur la fixation des prix
- Niveau d'automatisation - Dérouleur manuel ou motorisé, convoyeurs, etc.
- Gamme de tailles de canaux - Les dimensions plus larges nécessitent des rouleaux de plus grand diamètre
- Outillage supplémentaire - Pour le poinçonnage, l'encochage et le gaufrage
- Installation et formation - Souvent inclus dans le prix de la machine
- Frais d'expédition - Variable en fonction de la localisation
Fourchette de prix totale - $15,000 à $65,000 en fonction des facteurs susmentionnés
Des besoins de production plus importants justifient l'investissement dans des équipements automatisés plus avancés.
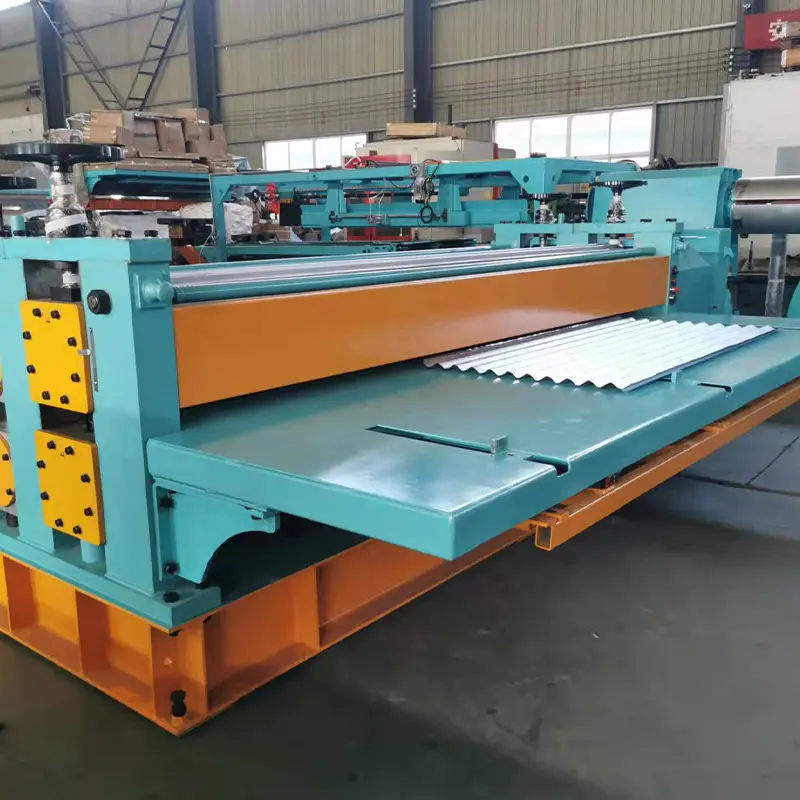
Considérations relatives à l'achat
Principaux éléments à prendre en compte lors de l'achat d'un équipement de profilage de profilés de plafond :
- Type et taille des profilés de plafond requis
- Estimation des volumes de production et de la production annuelle
- Profil unique ou changements rapides pour plusieurs profils
- Nombre de variations nécessaires - trous, découpes, courbes, etc.
- Espace d'installation disponible et disposition
- Niveau de compétence de l'opérateur et besoins de formation
- Protection de la sécurité et réduction du bruit
- Possibilités d'améliorations et d'extensions futures
- Assistance aux distributeurs locaux et capacités de maintenance
L'analyse des besoins de production actuels et futurs permet de sélectionner la profileuse adéquate.
Conseils d'entretien
Activités de maintenance recommandées :
- Nettoyage quotidien des débris métalliques à l'aide d'un aspirateur
- Lubrification des roulements, des boîtes de vitesses et des convoyeurs selon le calendrier prévu
- Inspection de l'usure des rouleaux et remplacement des éléments endommagés ou usés
- Vérification du niveau de l'huile hydraulique et contrôle des fuites
- Confirmation que le câblage électrique est intact et qu'il n'y a pas de connexions desserrées
- Test des boutons d'arrêt d'urgence et vérification des protections
- Contrôle de la tension des courroies et des chaînes pour l'étirement
- Documenter les détails des travaux de maintenance
- Stockage de pièces détachées comme les roulements, les lames, les courroies
La maintenance proactive améliore le temps de fonctionnement et l'homogénéité de la production.
Conseils de dépannage
Résolution des problèmes courants liés à l'enroulement des profilés de plafond :
Distorsion du profil
- Vérifier l'alignement et l'espacement des rouleaux
- Remplacer les rouleaux endommagés ou usés
- Ajuster la pression du rouleau si nécessaire
Longueur de coupe inégale
- Réaligner la lame de coupe
- Vérifier le positionnement du capteur
Incohérence de la vitesse de la ligne
- Tester les servomoteurs et les variateurs de vitesse
- Vérifier que les courroies de transmission ne patinent pas
Blocage de la machine
- Augmenter la lubrification
- Débarrasser les stations de tout débris
- Veiller à ce qu'aucune pièce de la machine ne soit desserrée
Perte de puissance hydraulique
- Contrôler les joints des cylindres, les valves, les pompes
- Inspecter le niveau de liquide et le filtre
- Resserrer les raccords qui fuient
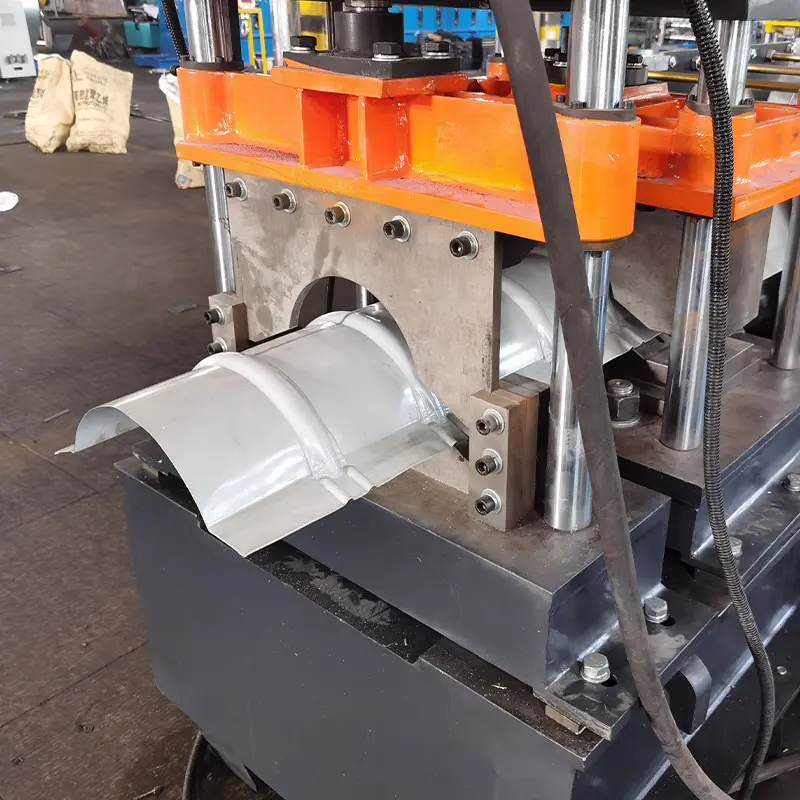
FAQ
Quels sont les matériaux qui peuvent être transformés en profilés de plafond ?
Les matériaux courants sont l'acier galvanisé, l'acier inoxydable, l'aluminium et l'acier plastifié. L'acier galvanisé offre le meilleur rapport qualité-prix pour la plupart des applications.
Quelle est la gamme d'épaisseurs qui peut être typiquement traitée ?
Les profileuses standard peuvent traiter des tôles d'une épaisseur de 0,4 mm à 0,8 mm. Des modèles spéciaux sont disponibles pour des tôles plus épaisses si nécessaire.
Quel est le taux de production habituel ?
10-15 mètres par minute. La vitesse maximale varie en fonction de la taille de la pièce, de ses caractéristiques et de l'épaisseur du matériau.
Quelle est la longueur des canaux qui peuvent être produits ?
Les longueurs de 1 à 6 mètres sont typiques. Des longueurs plus importantes peuvent être obtenues en ajoutant des stations de laminage supplémentaires ou en utilisant une encocheuse au lieu d'une scie.
Quels sont les facteurs qui influencent le prix de la machine ?
Les principaux facteurs sont la vitesse de production, la gamme de tailles, le niveau d'automatisation en termes de dérouleurs motorisés, de convoyeurs, de changements rapides, etc. et d'accessoires supplémentaires.
Conclusion
Machines à former les profilés de plafond offrent une précision et une régularité inégalées par les autres méthodes de fabrication. En choisissant avec soin l'équipement approprié aux besoins de production, les fabricants peuvent obtenir un retour sur investissement rapide grâce aux économies de matériaux et d'énergie, à la réduction de la main-d'œuvre et à l'amélioration de la qualité des produits. Lorsqu'elles sont équipées de changements rapides et d'accessoires, les profileuses pour profilés de plafond constituent une solution polyvalente.