UN machine à former les rouleaux de rayonnages est un équipement essentiel pour les usines et les entrepôts qui produisent des systèmes de stockage. Ce guide donne un aperçu complet de la technologie du profilage des rayonnages, y compris les principes de fonctionnement, les types de machines, les principaux composants, les processus de production, les domaines d'application, les facteurs de sélection lors du choix d'un fournisseur, les procédures d'installation et d'entretien, les avantages et les limites par rapport à d'autres méthodes, et les questions fréquemment posées.
Introduction au profilage des rayonnages
Le profilage est une opération de pliage en continu au cours de laquelle une feuille ou une bande de métal est progressivement façonnée lors de son passage à travers des cylindres consécutifs jusqu'à l'obtention du profil de section transversale souhaité. Les machines de profilage sont utilisées pour la production efficace et en grande quantité d'éléments de crémaillère avec des tolérances précises et des coûts d'exploitation faibles.
Comparé à d'autres techniques de fabrication telles que la découpe au laser, le poinçonnage, le pressage ou le soudage, le profilage est idéal pour créer de longues poutres, des montants, des entretoises et des connecteurs dans les structures de rayonnage à partir d'acier enroulé. Des profils personnalisés sont également possibles en fonction des exigences de l'application.
Les pièces formées ont une qualité constante et une précision dimensionnelle sur toute la longueur grâce à la coupe automatisée en ligne. Le gaspillage de matériau est minimal grâce au logiciel d'imbrication. Les changements rapides d'outils facilitent la flexibilité des programmes de production. Globalement, le profilage permet aux fabricants de rayonnages de répondre rapidement et économiquement à une demande croissante.
Principe de fonctionnement
Dans un machine à former les rouleaux de rayonnagesSur la ligne de production, la feuille ou la bobine brute passe par une série de cages de laminage consécutives. Chaque cage de laminage donne au matériau la forme souhaitée au fur et à mesure qu'il progresse sur la ligne.
Les cages de laminage se composent d'un ensemble de rouleaux supérieurs et inférieurs conçus spécifiquement pour créer des profils de crémaillère. Les rouleaux exercent une pression pour plier la bande lors de son passage en continu. Des mécanismes d'alimentation automatisés avec des rouleaux pinceurs assurent un guidage précis du matériau dans l'outillage de laminage.
Lorsque le matériau sort de la station de laminage finale, il a atteint la section transversale entièrement formée du composant de la crémaillère, comme une poutre, un poteau, une entretoise, etc. Les pièces formées en continu peuvent ensuite être acheminées vers d'autres machines intégrées pour des étapes de traitement telles que le poinçonnage de trous, le tranchage à la longueur avant l'empilage automatique.
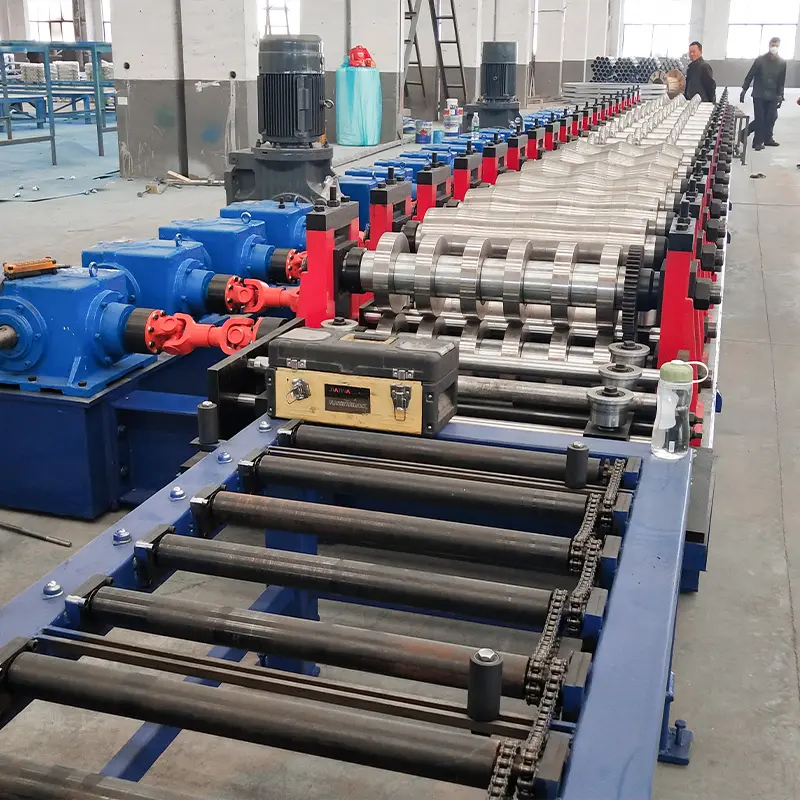
Types de rayonnages formés par laminage
Les rayonnages à tablettes sont des structures fabriquées à partir de profilés d'acier formés à froid qui servent de systèmes de stockage pour supporter des charges matérielles sur des niveaux horizontaux. Ils constituent des plates-formes modulaires réglables pour les usines, les entrepôts, les magasins de détail, etc. Parmi les éléments couramment formés par laminage, on peut citer
Poutrelles à crémaillère - Éléments porteurs horizontaux avec languettes et trous pour les connexions
Montants / Colonnes - Éléments verticaux avec trous pour ajuster la position des poutres
Entretoises et goussets - Renforts diagonaux pour la stabilité et la rigidité de l'articulation
Connecteurs - Rivets spéciaux, boulons pour fixer les éléments aux intersections
Guide de la machine de formage de rayonnages à rouleaux
Cette section explique les principaux aspects à prendre en compte lors de la sélection et de l'utilisation d'une ligne de profilage de rayonnages pour la fabrication de rayonnages en interne ou en collaboration avec des fournisseurs d'équipements de profilage.
1. Alimentation en matériaux
Le matériau d'entrée pour le profilage peut être fourni soit sous forme de feuilles de largeur fixe ou bobines des largeurs plus étroites. Les lignes de bobines sont plus courantes car elles permettent d'éviter les pertes dues au cisaillement des feuilles et de produire des volumes importants grâce au déroulement automatisé.
| Lignes de feuilles | Convient aux volumes de production faibles à moyens où les changements de format sont fréquents. Chargement manuel des feuilles coupées. | | Lignes de bobines | Des taux de production plus élevés sont possibles grâce au déroulement automatique des bobines et à un flux de travail fluide. |
2. Capacité de formation
La gamme de tailles et la vitesse déterminent la capacité globale :
- Épaisseur - Acier laminé à froid de 0,5 mm à 2 mm
- Largeur - Jusqu'à 1200 mm
- Longueur - 1 m à 9 m (ou plus)
- Vitesse - Jusqu'à 30 m/min (variable en fonction de la complexité)
Plus le nombre de têtes de laminage est élevé, plus les sections transversales pouvant être formées sont grandes. Le formage 3D avancé est possible avec jusqu'à 10 étapes de laminage dans une seule machine.
3. Conception du profil
L'outillage de roulage se compose de rouleaux supérieurs et inférieurs usinés pour créer progressivement la forme de la section transversale sur toute la largeur. Les nouveaux profils nécessitent la conception, l'usinage et l'assemblage de jeux de rouleaux personnalisés spécifiques à chaque géométrie.
Des profils standard sont disponibles, mais pour les applications spéciales, des formes uniques peuvent être nécessaires - par exemple des perforations pour réduire le poids et le coût.
4. Coupe automatisée
Lorsque le profilé formé en continu sort de la station finale, des scies commandées par ordinateur découpent la poutre/colonne longitudinale aux longueurs souhaitées pour les rayonnages, les cadres verticaux, etc.
Des unités de coupe supplémentaires permettent de créer des encoches, des trous ou des contours complexes sur la longueur si nécessaire. Les scies électriques servo de précision permettent des pas plus étroits pour les rayonnages de stockage denses.
5. Systèmes de manutention des pièces
Pour les gros volumes, des convoyeurs de sortie avec empileurs automatisés déplacent efficacement les pièces coupées finies pour le traitement antirouille, l'emballage et l'expédition. Les systèmes robotisés de prélèvement et de placement en ligne alimentent directement d'autres machines, telles que les lignes de perçage, si un traitement secondaire est nécessaire.
6. Suivi de la production
Les lignes modernes sont dotées d'une interface homme-machine à écran tactile et de PC industriels permettant de contrôler l'état actuel, d'enregistrer les commandes, de signaler les défauts, d'assurer le suivi de la maintenance et d'analyser les performances passées. Le logiciel SCADA permet d'accéder à distance aux données afin d'optimiser l'efficacité globale de l'équipement.
7. Options de personnalisation
- Marquage du logo par des cylindres de gaufrage
- Enregistrement de l'impression pour les étiquettes sérialisées et les codes à barres
- Perçage de trous pour un ajustement modulaire
- Enveloppe de profilé pour la sécurité et l'esthétique
- Revêtements de surface spéciaux
Haut de page Machine de formage de rouleaux pour rayonnages Fabricants
Compagnie | Localisation | Fourchette de prix typique |
---|---|---|
ECC Co, Ltd | Taïwan | $100k - $250k |
Groupe Formtek | Chine | $50k - $500k |
Groupe DIMECO | Italie | $250k - $750k |
Finn-Power | Finlande | $200k - $800k |
Kingsland | Royaume-Uni | $150k - $800k |
-
Machine à courber les panneaux de toiture à joint debout
-
Machine de formage de rouleaux ondulés de baril
-
Machine de formage de panneaux de toiture par roulage à joint debout
-
Machine de formage de rouleaux de tuyau de descente
-
Rouleau de gouttière formant la machine
-
Profileuse pour panneaux trapézoïdaux
-
Ridge Cap Roll formant la machine
-
Machine de formage de rouleaux de panneaux à double couche
-
Petit pain de panneau de tuile de toit formant la machine
Comment choisir une profileuse pour rayonnages
Le choix de l'équipement de profilage optimal pour la production de racks dépend de facteurs spécifiques à l'entreprise. Cette section aborde les principaux éléments à prendre en compte.
Exigences en matière d'installation
- Surface au sol
- Puissance - jusqu'à 75 kW de charge connectée
- Air comprimé - 10 bar de pression
- Espace de manutention pour bobines, empileur
- Températures ambiantes de fonctionnement
Une mise à la terre, une ventilation et des mécanismes de sécurité appropriés doivent être prévus. La mise en service sur le terrain par un technicien est incluse.
Considérations relatives à la production
- Volume annuel en mètres linéaires
- Temps de cycle pour les profils en fonction de la longueur, de l'épaisseur et de la complexité
- Types de matériaux - acier doux, acier inoxydable, aluminium
- Procédés secondaires nécessaires - perforation, encochage, emballage, etc.
Besoins de flexibilité
- Fréquence des changements de profil
- Gamme de tailles - épaisseur, largeur et longueurs
- Types de sections - poutres, colonnes, contreventements, etc.
Modularité de l'outillage pour s'adapter à une variété de pièces par rapport à des jeux de rouleaux dédiés à des profils de produits de base à haut volume
Facteurs de coût
- Prix de la machine - le modèle de base commence à ~$100k, les lignes fortement personnalisées à ~$500k+.
- Frais de conception des profils - à partir de $5k par profil
- Coût de l'outillage - $20k à $60k pour des jeux d'outils complets
- Fret, taxes, frais d'installation supplémentaires
- Rabais de production accordés par les fournisseurs pour les commandes supérieures à 500 tonnes/an
Capacités logicielles
- Modélisation de formes en 3D
- Simulation virtuelle du processus de laminage
- Flexibilité de l'interface de programmation
- Protocoles de communication avec d'autres équipements
- Modes de diagnostic, enregistrement des données et analyse
Les contrôles avancés et l'interopérabilité réduisent les efforts manuels lors de l'exploitation ou de la maintenance.
Soutien aux services
- Réactivité aux questions techniques
- Visites d'entretien par an par technicien
- Équipe interne contre agents locaux pour les pièces, les réparations
- Formation des opérateurs
- Mises à jour du logiciel pendant toute la durée de vie de l'appareil
Évaluer les coûts de propriété complets sur une durée de vie de 10 à 15 ans, ainsi que les facteurs liés aux relations avec les fournisseurs.
Installation, fonctionnement et entretien d'une profileuse
Une installation correcte, une utilisation quotidienne et une maintenance préventive sont essentielles pour assurer le bon fonctionnement, la sécurité et la longévité des équipements de profilage. Les travailleurs doivent suivre les protocoles indiqués dans les manuels d'utilisation des équipements. Les aspects clés sont mis en évidence :
Exigences en matière d'installation
- Positionnement sur une surface plane et nivelée
- Boulons d'ancrage pour résister aux vibrations
- Connexions électriques au panneau de contrôle
- Raccords pneumatiques, unité de traitement de l'air
- Installation de manutention des bobines, convoyeurs de sortie
- Barrières de sécurité, barrières immatérielles
Méthodes de fonctionnement
- Réglage des paramètres - largeur, épaisseur, avance
- Contrôle de la vitesse et de la température
- Calibrage de l'enregistrement
- Inspection visuelle des sorties
- Contrôles de qualité selon les spécifications
- Empilage automatisé des produits finis
Calendrier d'entretien
- Rouleau de nettoyage outillage hebdomadaire
- Lubrification mensuelle des roulements
- Remplacer les composants usés si nécessaire
- Inspection des chaînes et des courroies tous les 6 mois
- Contrôle du système hydraulique
Avantages et inconvénients des profileuses
Le profilage présente des avantages dans la production de racks, mais aussi des limites en fonction du contexte. La comparaison des avantages et des inconvénients permet une sélection appropriée pour les différents fabricants.
Avantages
Productivité élevée
- Un rendement jusqu'à 10 fois supérieur à celui des autres méthodes
- Possibilité de fonctionnement 24 heures sur 24 et 7 jours sur 7 avec une supervision minimale
- La manipulation automatisée des bobines améliore le rendement
Précision dimensionnelle
- Tolérance de précision sur toute la longueur
- Angles formés avec une cohérence de ± 0,5°.
- Enregistrement adapté aux processus secondaires
Flexibilité
- Plusieurs profils sur la même ligne
- Conception et changement d'outils plus rapides
- Possibilité d'extension modulaire de la capacité
Réduction des coûts d'exploitation
- La préfabrication réduit la main-d'œuvre et les travaux de soudage
- Consommation d'énergie inférieure à celle des presses plieuses
- Un logiciel d'imbrication permet de minimiser les pertes de ferraille
Évolutivité
- Manipuler une large gamme de tailles
- Convient à la production de masse, à faible volume ou à mélange élevé
- Croître en intégrant l'automatisation robotique
Sécurité
- Bruit réduit par rapport aux planchers de fabrication
- Barrières immatérielles de sécurité pour la protection de l'opérateur
- Surveillance en boucle fermée des anomalies
Limites
Capital initial élevé
- Les rouleaux doivent être usinés en fonction de leur profil
- Machines spécialisées à usage unique
- Amortissement sur plusieurs années d'utilisation élevée
Contraintes de forme
- Rayon de courbure limité par passage
- Défi pour les sections étroites et fermées
- Les formes en 3D peuvent nécessiter des machines à plusieurs étages
Matériaux plus épais
- Au-delà de 2 mm, il faut un moteur de grande capacité
- Le maintien des tolérances est plus difficile
Limites de longueur
- Supports nécessaires pour les pièces longues
- Problèmes liés au gauchissement des feuilles plus fines
Transformation secondaire
- Des mesures supplémentaires seront probablement nécessaires
- Nécessite une bonne interface de gestion des pièces
Expertise en matière de processus
- Compétences spécialisées requises
- Modes de défectuosité difficilement détectables
Grande empreinte
- Les structures lourdes occupent beaucoup d'espace
- Des zones de circulation des matériaux sont également nécessaires
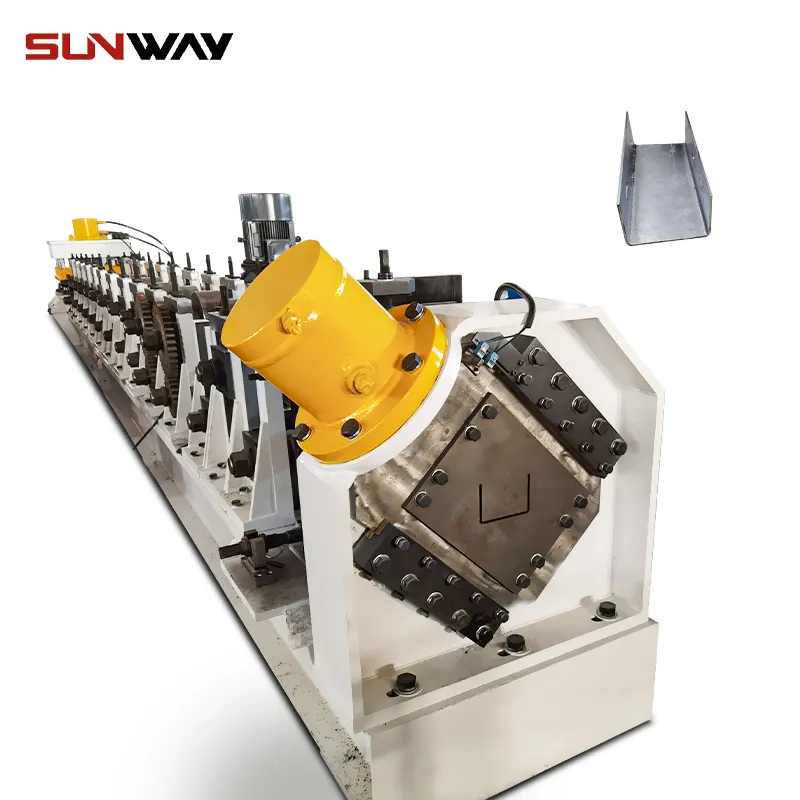
Applications des profilés à crémaillère formés par laminage
Le procédé polyvalent de formage en continu permet de créer des géométries de produits à crémaillère pour des cas d'utilisation très répandus :
Systèmes de rayonnages pour entrepôts
Rayonnages à palettes ajustables, rayonnages mobiles et rayonnages à grande portée pour les centres de distribution et les entrepôts qui ont besoin d'un stockage dense et d'une optimisation de la manutention.
Rayonnages pour magasins de détail
Systèmes de rayonnages pour la vente au détail, présentoirs et caisses personnalisés pour répondre aux besoins de merchandising tout en respectant les codes esthétiques.
Rayonnages de bibliothèque
Rayonnages spécialisés à ossature renforcée pour le stockage de livres et d'archives avec accès mobile sur rails ou bases roulantes.
Postes de travail industriels
Bâtis sur mesure avec tables intégrées, planches à outils, hangars en tant qu'établis modulaires pour les opérations d'assemblage, les contrôles de qualité, etc.
Baies pour centres de données
Baies de serveurs informatiques conçues pour le montage de dispositifs de mise en réseau, de commutateurs et de panneaux pour la gestion des cordons tout en permettant la dissipation de la chaleur.
FAQ
Q : Quelles sont les dimensions des éléments de rack qui peuvent être formés par roulage ?
R : Les capacités courantes sont une épaisseur de 0,5 mm à 2 mm, une largeur allant jusqu'à 1200 mm et des longueurs de 1 à 12 m. Il existe des lignes indépendantes multi-standards de 18 m de long pour des applications spéciales. Des lignes indépendantes multi-stations de 18 m de long existent pour les applications spéciales.
Q : Quelles sont les tolérances possibles dans le processus de profilage ?
R : La tolérance standard est de ± 0,5 mm, mais les machines de précision équipées de guides et de jauges supplémentaires peuvent atteindre une précision de ± 0,2 mm sur toute la longueur.
Q : Quel est le degré d'automatisation possible dans le domaine de la manutention ?
A : Gamme de convoyeurs de sortie simples jusqu'aux robots d'empilage hautement automatisés avec regroupement intégré, palettisation en fonction des volumes et des contraintes d'agencement.
Q : Quelle est la fréquence des changements d'outillage nécessaires pour les nouveaux profils ?
R : Pour les lignes à haut volume dédiées aux profils standard, la durée de vie de la conception est supérieure à 5 ans. Lorsque le mélange change tous les mois, l'outillage modulaire permet des changements plus rapides.
Q : Quels sont les processus secondaires qui peuvent être intégrés au profilage ?
R : Les machines en ligne couramment ajoutées sont : le poinçonnage, l'encochage, le taraudage, le rétreint, le marquage, l'emballage, les systèmes robotisés de prise et de mise en place.
Q : Comment calculer les taux de production de mètres linéaires par jour ?
A : Multiplier la vitesse de la machine (m/min) x 60 min x le temps de fonctionnement (% de 24 heures) x le taux d'efficacité. Exemple - 20 m/min x 60 x 0,9 x 0,8 = 8 640 mètres par jour.
Q : Quels peuvent être les défauts des pièces de rack formées par laminage ?
A : Profils tordus, erreurs dimensionnelles, plis, évasements, courbures et cambrures hors normes, bavures et accumulation de particules étrangères nécessitant une remise en état.
Q : Combien de plis par passe sont courants dans les machines de formage par roulage ?
R : L'outillage de laminage standard crée 1 à 3 courbes incrémentales par paire de stations de laminage. Le formage 3D avancé permet de réaliser jusqu'à 6 courbes en un seul passage, ce qui accélère la production.
Q : Quelle est la durée de vie des profileuses ?
R : Environ 12 à 15 ans en moyenne, avec un entretien programmé approprié, avant que des coûts de remise en état importants ne surviennent lorsque des systèmes obsolètes sont confrontés à des défis.
Q : Quels sont les facteurs qui influencent le choix entre les lignes de bobines et les lignes de feuilles ?
R : Les principaux facteurs à prendre en compte sont le volume, la largeur, le rendement du matériau, les besoins en matière de traitement secondaire et les coûts de manutention associés, spécifiques à l'environnement de production.