Visión general
Perfiladoras de chapa de acero se utilizan para transformar bobinas o chapas de acero en perfiles personalizados de dimensiones precisas y calidad uniforme. Para ello, se hace pasar la chapa por conjuntos consecutivos de rodillos que van dando forma progresivamente al material según las necesidades.
El perfilado es una de las formas más económicas de fabricar piezas metálicas de gran longitud y grandes volúmenes de producción. El proceso es versátil, rápido y eficaz en comparación con otros métodos como la extrusión o el prensado. Permite líneas de producción continuas y automatizadas, lo que se traduce en bajos costes operativos por pieza.
Los componentes laminados tienen amplias aplicaciones en sectores como la automoción, la construcción, la agricultura, el mobiliario, los electrodomésticos y otros. Algunos ejemplos comunes son los paneles para tejados y paredes, las estanterías, los montantes metálicos, los canalones para tejados, los raíles para autopistas, los marcos de puertas y las piezas del chasis de automóviles, entre muchos otros.
Esta guía ofrece una visión completa de los distintos aspectos de las máquinas de perfilado de chapa de acero, desde los principios de funcionamiento, las capacidades, los componentes, los parámetros y las configuraciones hasta las consideraciones de diseño, los costes económicos y la selección de proveedores.
Tipos de perfiladoras de chapa de acero
Las perfiladoras se clasifican en función de la disposición de los rodillos, el número de operaciones, el nivel de automatización, etc. Los principales tipos incluyen:
Perfiladoras en línea
- Conocidas como formadoras de rodillos rectos o continuos
- Las chapas pasan por rodales consecutivos en sentido longitudinal
- Adecuado para piezas largas como paneles, carriles, canales con perfil constante
- Capacidad limitada para variaciones de perfil
Perfiladoras rotativas
- Rodillos dispuestos en forma circular para el conformado rotativo
- La chapa se enrolla alrededor de un mandril central
- Se utiliza para fabricar anillos, cilindros, conos y secciones transversales variadas
- Alto rendimiento y consistencia dimensional
Máquinas combinadas o modulares
- Máquinas híbridas con soportes en línea y giratorios
- Ofrece a la vez flexibilidad de perfil y alta productividad
- Permite conformar formas helicoidales y componentes cónicos
Perfiladoras CNC
- Utillaje de rodillos ajustable mediante controles informatizados
- Cambio rápido entre perfiles
- Supervisión avanzada, precisión y control de procesos
- Ideal para prototipos rápidos y perfiles personalizados
Máquinas accionadas por servomotor
- Los servomotores controlan cada rodillo de forma independiente
- Permite realizar ajustes en tiempo real durante la producción
- Reduce los costes de equipamiento y mantenimiento
- Mejora la precisión y la repetibilidad del conformado
Perfiladoras portátiles
- Unidades compactas y portátiles de rápida instalación
- Se utiliza directamente en las obras
- Limitado a aplicaciones sencillas y de bajo volumen
- Rentable para la producción de piezas individuales largas
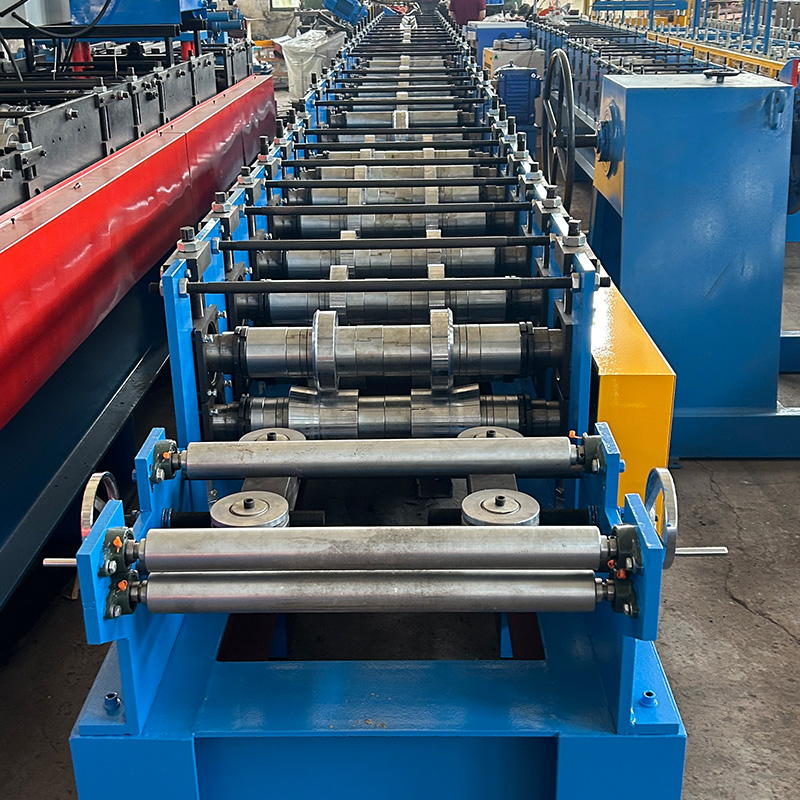
Componentes principales de una perfiladora
Las perfiladoras, ya sean en línea o rotativas, constan de los siguientes componentes fundamentales:
Soportes para rodillos
Estos alojan los rodillos superior e inferior entre los que pasa la hoja. Los soportes se disponen consecutivamente según la secuencia del perfil. Contienen:
- Ejes de rodillos montados sobre rodamientos
- Carcasas para soportar los ejes y permitir el ajuste vertical
- Mecanismos de accionamiento para hacer girar los ejes
Rodillos conformadores
Se encargan de doblar y dar forma a la chapa mediante contornos calibrados. Varios tipos de rodillos:
- Desglose - conformación inicial
- Acabado - perfilado final
- Pareja - rodillo superior e inferior a juego
- Dimensionado: para reducir el grosor
- Rodillo - sin contornos, para apoyo
Guías de entrada
Primer juego de rodillos rectos que guían la hoja hacia la máquina. Minimiza la desalineación.
Rodillos de proceso
Rodillos adicionales para gofrar, perforar, cortar, entallar o taladrar las chapas durante el conformado.
Rodillos de apoyo
Proporcionan soporte y mantienen la alineación de la chapa entre los soportes de conformado. Evitan el pandeo.
Guías de salida
Rodillos rectos finales que estabilizan y guían el perfil acabado fuera de la máquina.
Decoiler o Coche de bobinas
Sujeta la bobina y alimenta la chapa a la máquina mediante un desbobinador motorizado. Tiene control de tensión.
Mesa de alimentación
Soporta chapas entre el desenrollador y las guías de entrada. Puede tener sensores de posición de la chapa.
Accionamientos de conformación
Motores acoplados mediante reductor a un eje de línea que acciona todos los ejes de rodillos mediante cadenas o correas.
Sistema hidráulico
Acciona la apertura vertical de los soportes de rodillos para cambiar rápidamente las herramientas.
Sistema de control
Controles automatizados para velocidades precisas de los rodillos, supervisión del proceso y funciones de seguridad.
Especificaciones clave y factores de diseño
Las máquinas de perfilado se adaptan a las necesidades específicas de producción. La siguiente tabla resume los principales parámetros y factores que se tienen en cuenta durante la selección y el diseño de los equipos:
Especificaciones | Detalles |
---|---|
Velocidad de formación | Velocidad de producción en pies/min o m/min. Las velocidades más altas requieren más potencia. |
Velocidad del eje de línea | Velocidad de rotación del eje de transmisión principal en rpm. Determina la velocidad de los rodillos. |
Estaciones de formación | Número de soportes de rodillos necesarios para una secuencia completa de perfiles. |
Tamaño del rodillo | Diámetro y anchura de la cara. Más grande para chapas de grueso calibre. |
Material del rodillo | Calidades de acero con endurecimiento para mayor solidez, longevidad y resistencia al desgaste. |
Rodamientos de rodillos | Soportan cargas elevadas. Los tipos sellados evitan la pérdida de lubricante. |
Tipo de accionamiento | Servoeléctrico, hidráulico, mecánico, etc. Afecta al control y a la eficiencia energética. |
Sistema de alimentación | Capacidad del desenrollador, diseño de la mesa de alimentación, posicionamiento de la hoja. |
Sistema de herramientas | Cambio fácil y rápido a nuevos perfiles. |
Nivel de automatización | Participación del operador frente a control programable de precisión. |
Manómetros manipulados | Gama de espesores de las chapas a conformar. Necesita un tamaño de rodillo y una potencia adecuados. |
Materiales | Acero, aluminio, otras aleaciones. Se necesitan materiales y resistencias de rodillos adecuados. |
Dimensiones de la pieza | Anchura, longitud, complejidad de la forma del perfil deseado. |
Volumen de producción | Tirada corta frente a gran volumen. Impacto en el nivel de automatización. |
Espacio | Longitud de la máquina. Rotativa más compacta que en línea. |
La selección adecuada de los parámetros anteriores garantiza un perfilado suave y eficaz que maximiza la producción al tiempo que ofrece la calidad y precisión requeridas.
Principio de funcionamiento y flujo del proceso
A continuación se describen los fundamentos del funcionamiento de las perfiladoras:
- Carga de hojas - Bobinas cargadas en el desbobinador motorizado. Las hojas se introducen en las guías de entrada.
- Alimentación - El desenrollador desenrolla la chapa que se arrastra a través de soportes de rodillos consecutivos.
- Conformado progresivo - La lámina pasa por sucesivos rodales, cada uno de los cuales le va dando forma.
- Contorneado con rodillo - Los rodillos superior e inferior tienen perfiles coincidentes para una flexión gradual.
- Precisión dimensional - Separaciones entre rodillos, rotaciones y progresión controladas con precisión.
- Apoyo y estabilización - Los rodillos locos y de apoyo estabilizan la chapa durante el conformado.
- Operaciones adicionales - El estampado, troquelado o corte se realiza entre soportes.
- Finalización del perfil - El soporte final termina la forma del perfil. Las guías de salida estabilizan la chapa.
- Salida de la pieza formada - La longitud continua del perfil terminado sale de la máquina para los procesos posteriores.
El perfilado consiste en alimentar, doblar y calibrar las chapas longitudinalmente de forma continua y sincronizada para conseguir las secciones transversales deseadas. El perfilado incremental permite grandes deformaciones sin sobrecargar el material.
Ventajas del perfilado
El perfilado ofrece varias ventajas que lo hacen ideal para grandes volúmenes de producción:
Procesado de alta velocidad
- Velocidad de conformado posible hasta 100 m/min
- Producción automatizada y continua
- Capaz de satisfacer demandas de gran volumen
Coherencia dimensional
- Proceso programable con control de precisión
- Perfiles repetibles y precisos
- Tolerancias relativamente bajas
Flexibilidad del perfil
- Amplia gama de formas posibles
- Piezas con secciones transversales variadas
- Capacidad para formar geometrías complejas
Ahorro de material
- Sin desperdicio de material de corte
- La transformación ajustada mejora el rendimiento
- Menor índice de desechos
Eficiencia de costes
- Proceso altamente productivo y rápido
- Menor inversión en equipos que las prensas
- Reducción de los costes de explotación
- Bajo coste por pieza producida
Aspecto final
- Acabados suaves y estéticamente agradables
- El conformado consecutivo evita los planos
- Sin necesidad de postprocesado
Estos factores hacen que el perfilado sea adecuado para producir componentes metálicos en grandes volúmenes en muchas industrias.
Aplicaciones y productos típicos
La versatilidad del perfilado le permite producir perfiles diversos, desde los más sencillos a los más complejos. Entre las aplicaciones típicas se incluyen:
Construcción e infraestructuras
- Tejados, revestimientos y paneles murales
- Montantes de acero para entramado
- Canalones y tubos de desagüe metálicos
- Barreras de seguridad
- Barandillas, pasamanos y balaustradas
- Puertas, ventanas y marcos de muros cortina
- Varias secciones estructurales
Automoción y transporte
- Bastidores y travesaños del chasis
- Pilares, raíles, travesaños
- Armazones de asiento
- Ruedas, perfiles de llanta
- Carrocerías de camiones
- Piezas de remolques utilitarios
- Secciones de vagones de ferrocarril
Muebles y electrodomésticos
- Estanterías, racks, armarios
- Cajas, armarios, bastidores
- Paneles, carcasas, cubiertas
- Tubos, asas, brazos de soporte
- Perfiles y embellecedores personalizados
Agricultura y Maquinaria
- Secciones de la pluma, brazos de la cargadora
- Guardias, escudos, plataformas
- Transportadores, tolvas
- Piezas de silo, sinfines
- Bastidores de máquinas, soportes
Espacios comerciales y minoristas
- Cajas
- Expositores, estantes
- Señalización e iluminación
- Revestimientos, tabiques
- Embellecedores decorativos
Los componentes laminados mejoran tanto las propiedades estructurales como la estética de muchos productos.
Capacidades del proceso de perfilado
Las modernas máquinas perfiladoras ofrecen amplias capacidades que aumentan la flexibilidad:
Materiales de alta resistencia
- Capacidad para conformar aceros de alta resistencia de hasta 80 ksi de límite elástico
- Conformado de calidades de acero inoxidable, titanio y aluminio
- Materiales en rollos adaptados al material en hojas
Gama de espesores
- Puede procesar chapas de entre 0,5 mm y 8 mm de grosor
- Anchura de las caras de los rodillos adaptada al grosor
Perfil Características
- Formación de diferentes estilos de cuentas, relieve, nervaduras, etc.
- Perforación y taladrado en línea
- Posibilidad de tratamientos especiales de los bordes, como dobladillos
Gama dimensional
- Posibilidad de anchuras de hasta 2.500 mm y longitudes de más de 15 m
- Máquinas rotativas para anillos de más de 3 m de diámetro
Cambios rápidos
- Sistemas modulares de herramientas para cambios rápidos de perfil
- Sistemas de posicionamiento asistido por ordenador
Fabricación integrada
- Operaciones adicionales como punzonado, corte, soldadura
- Integración con procesos posteriores
Automatización flexible
- Opciones de funcionamiento de manual a totalmente automático
- Fácil integración de la alimentación, el apilamiento y la agrupación
Precisión y control
- Control forzoso para garantizar la calidad
- Servoaccionamientos eléctricos para mayor precisión
- CNC para supervisión y control avanzados
Con unas capacidades tan amplias, el perfilado puede adaptarse para producir una amplia gama de diseños de componentes.
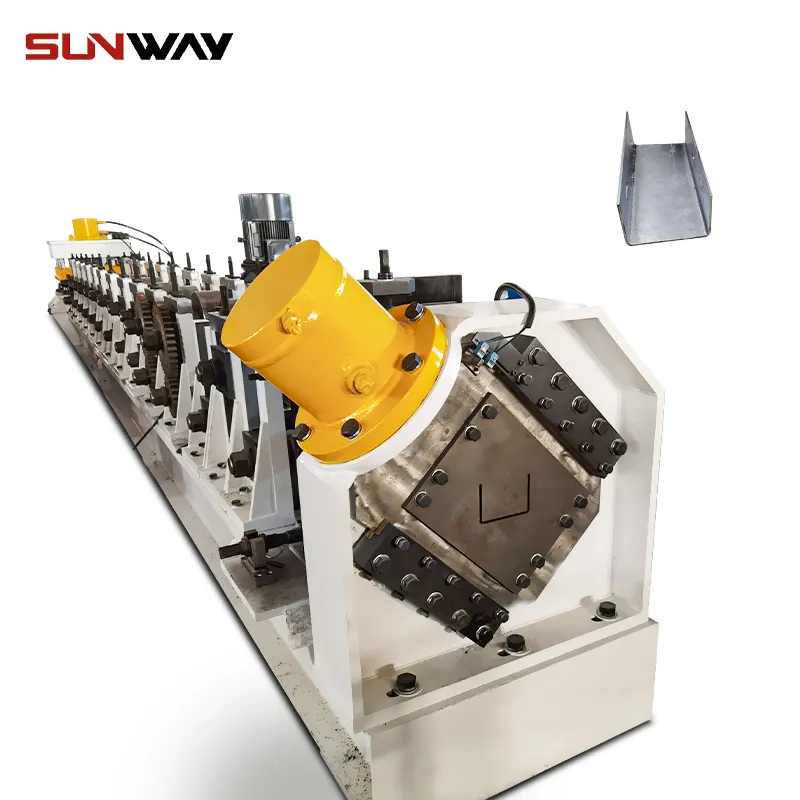
Principios de diseño y optimización de procesos
El perfilado ofrece amplias posibilidades, pero requiere un diseño óptimo para aprovechar plenamente su potencial y evitar al mismo tiempo los defectos. Los principales principios de diseño son:
Perfil Ubicación
Determinar el eje neutro: la secuencia de conformado debe avanzar desde el eje neutro hacia el exterior. Esto minimiza las tensiones.
Secuencia de flexión
Realice primero todos los codos longitudinales de longitud completa. A continuación, las curvas de los bordes o los extremos.
Conformado seccional
Lo mejor es evitar curvas muy diferentes de varios planos en una sola pasada. Hágalo por secciones para mayor estabilidad.
Contornos de balanceo
Debe coincidir con el grosor de la chapa. Una holgura excesiva provoca inestabilidad, mientras que una holgura insuficiente atasca la hoja.
Tamaño del rodillo
El diámetro del cilindro de laminación influye en el agarre. La anchura determina el soporte de la chapa durante el conformado.
Número de pases
Más pasadas permiten curvas más grandes con menos estiramiento. Pero aumenta el número de soportes necesarios.
Requisitos de fuerza
Calcule la fuerza por soporte para determinar las necesidades de potencia de la línea. Una fuerza excesiva daña el utillaje del rodillo.
Orientación del grano
Alinee el grano de la chapa en paralelo a la dirección de avance. De este modo se evitan las grietas durante el plegado.
Soporte de hojas
Utilice rodillos tensores/de apoyo adecuados para evitar el pandeo y mantener la planitud.
La aplicación de principios de diseño de eficacia probada da como resultado un procesamiento fiable y unos resultados de alta calidad de las máquinas de perfilado. Además, el proceso global puede optimizarse mediante:
- Colocación correcta de la bobina y disposición de la línea de desbobinado
- Zonas de entrada y salida generosas para un seguimiento adecuado
- Sistema de alimentación ajustable para diferentes anchos de hoja
- Herramientas modulares de cambio rápido para cambios rápidos
- Control preciso de procesos mediante sensores, servos y automatización
- Control en tiempo real de fuerzas, velocidades y tolerancias
- Mantenimiento adecuado de los rodillos para mantener el rendimiento
- Formación de operarios para un trabajo eficaz y seguro
Un diseño y una disposición de la línea bien pensados, junto con mejoras en el proceso, garantizan un perfilado fluido con la máxima eficacia y calidad.
Economía de costes de los equipos de perfilado
El perfilado puede suponer una inversión inicial considerable, pero ofrece unos costes de producción por pieza muy económicos.
Coste de adquisición de equipos
- Coste de la máquina de $100.000 a más de $1 millón
- La personalización, la automatización y el tamaño aumentan el coste
- Coste por pie ~$800 a $1500 para máquinas medias
Coste de utillaje
- Alrededor de $3000 hacia arriba por estación de conformado
- Deben adquirirse rollos específicos para cada perfil
- Los sistemas de cambio rápido permiten reutilizar las herramientas
Costes de explotación
- Mano de obra, mantenimiento y consumibles
- ~10% de coste anual de equipos
- Inferior a otros procesos como la estampación
Economía del precio por pieza
- Proceso ideal para volúmenes superiores a 100.000 piezas
- El coste por pieza puede ser de $1 a $5
- Ahorro de más de $100 por pieza frente a otros procesos
- También se minimizan los plazos de entrega y los costes logísticos
Con una planificación y un diseño eficaces, las líneas de perfilado ofrecen un excelente rendimiento de la inversión al tiempo que minimizan los costes de producción.
Criterios de evaluación y selección de proveedores
La elección del proveedor adecuado de equipos de perfilado es clave para el éxito de un proyecto. Algunos criterios de selección clave son:
Reputación y experiencia de la empresa
- Años de experiencia en empresas e industria
- Historial probado de instalaciones y asistencia
- Testimonios de clientes y casos prácticos
Calidad y fiabilidad
- Uso de componentes de primera calidad
- Rigurosos procesos de fabricación y ensayo
- Instalaciones que funcionan sin problemas
Experiencia en personalización
- Capacidad para diseñar soluciones personalizadas
- Gama de máquinas y prestaciones ofrecidas
- Familiaridad con diversas aplicaciones
Capacidades técnicas
- Ingeniería y fabricación propias
- Equipos y controles de última tecnología
- Diseños de máquinas de rendimiento probado
Servicios ofrecidos
- Apoyo al diseño y simulación/modelado
- Contratos de formación y mantenimiento de operadores
- Servicios de modernización, adaptación y traslado
Entrega y asistencia
- Plazos de fabricación
- Instalación, puesta en marcha y asistencia
- Servicio postventa y suministro de piezas de repuesto a largo plazo
La evaluación de los proveedores de maquinaria de perfilado en función de los parámetros anteriores minimiza los riesgos de ejecución del proyecto y garantiza un rendimiento optimizado de los equipos.
Ventajas frente a inconvenientes y limitaciones
El perfilado ofrece muchas ventajas, pero también tiene algunas limitaciones inherentes:
Ventajas
- Proceso continuo altamente productivo
- Baja inversión en equipos
- Coste por pieza muy bajo
- Sin desperdicio de material
- Precisión dimensional y repetibilidad
- Amplia gama de tamaños
- Adecuado para materiales de alta resistencia
Desventajas
- Coste inicial de utillaje por perfil
- Limitaciones de tamaño y peso de las piezas
- Plazo de diseño y fabricación de los rodillos
- Capacidad limitada para variaciones transversales
- No es ideal para volúmenes de producción bajos
- Perfiles inversos complejos difíciles
- Riesgo de defectos como torsión o arqueamiento
Estas ventajas hacen que el perfilado sea ideal para grandes volúmenes. Para volúmenes inferiores, otros procesos pueden resultar más adecuados y económicos en función del tamaño y la complejidad de la pieza.
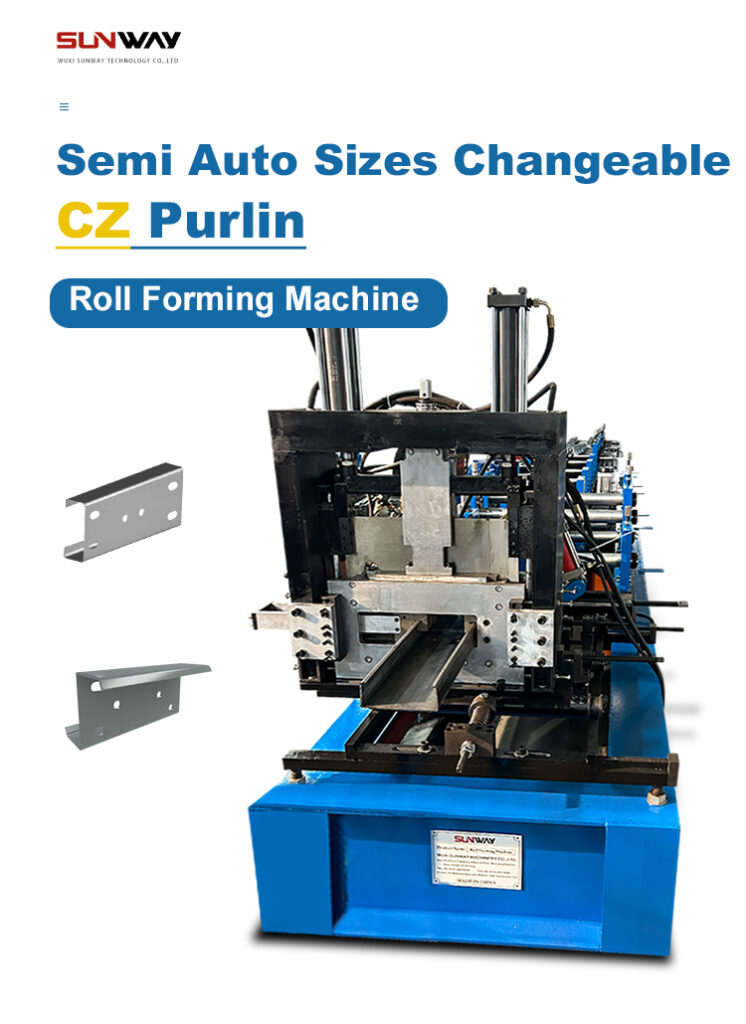
Preguntas más frecuentes
¿Qué materiales pueden laminarse?
- Los materiales más comunes son el acero con bajo contenido en carbono, el acero inoxidable y el aluminio. También pueden procesarse otras aleaciones conformables como el latón o el cobre. La dureza del material no debe ser superior a la dureza total.
¿Cuáles son los productos laminados más comunes?
- Paneles de construcción, canalones, tejados, revestimientos, tuberías de desagüe, estanterías, bastidores, componentes de chasis, perfiles para puertas, ventanas y muros cortina son algunos ejemplos.
¿Cómo se compara el perfilado con el plegado o el plegado en prensa?
- El plegado crea piezas discretas aplicando una deformación focalizada, mientras que el perfilado crea perfiles continuos mediante la progresión gradual de un plegado más ligero distribuido en múltiples incrementos pequeños.
¿Qué tolerancias se pueden conseguir en el perfilado?
- El perfilado permite tolerancias competitivas de +/- 0,5 mm , que pueden mejorarse aún más con una supervisión adecuada del proceso y controles automatizados.
¿Qué determina la longitud mínima y máxima de la pieza en el perfilado?
- Normalmente se pueden conseguir longitudes de 1 a 15 metros. La longitud máxima depende de las propiedades del material, el soporte de la chapa y el diseño de la pieza. La longitud mínima necesaria es de entre 8 y 10 puestos de conformado para completar la secuencia de perfilado.
¿Con qué rapidez puede cambiarse el utillaje de laminación para nuevos perfiles?
- Con los sistemas modulares de cambio rápido, los tiempos típicos de cambio oscilan entre 20 minutos y 1 hora. Para cambios de perfil frecuentes, los soportes programables CNC ayudan a minimizar los cambios.
¿Qué defectos pueden presentar las piezas perfiladas?
- Los defectos potenciales son la torsión, la curvatura, el ensanchamiento, la deformación, las arrugas y la ondulación de los bordes. Pueden evitarse con un mantenimiento adecuado de la máquina, el diseño del rodillo, la calidad del material y el control del proceso.
¿Qué factores influyen en el precio de las perfiladoras?
- Parámetros como la longitud en pies lineales, el tonelaje, el nivel de automatización, las velocidades, la capacidad de la bobina, la gama de espesores del material, los accionamientos y los controles influyen en el coste. La gama típica oscila entre $100.000 y $1 millón.
¿Cuáles son las necesidades de mantenimiento de las perfiladoras?
- El mantenimiento preventivo básico incluye la limpieza, la lubricación, la inspección del desgaste de los rodillos, la estanqueidad de la transmisión, los rodamientos, el sistema hidráulico y el sistema eléctrico. Las averías se reducen al mínimo con un mantenimiento programado.
¿Cuánto duran los componentes de las perfiladoras?
- Con un uso y mantenimiento adecuados, los principales componentes mecánicos pueden funcionar de forma fiable entre 15 y 25 años. Los sistemas de control pueden necesitar actualizaciones antes. Los consumibles, como ejes, cojinetes y herramientas, deben sustituirse cada 4-5 años o según el desgaste.
Conclusión
Principales conclusiones
- El perfilado permite una producción económica y continua de perfiles metálicos de calidad uniforme
- Adecuado para grandes volúmenes gracias a su rápida producción y bajo coste
- Amplias capacidades para conformar formas diversas, materiales de alta resistencia y
- Los factores de diseño de los equipos, como la transmisión, el nivel de automatización o el utillaje, afectan a las capacidades y al precio.
- Seguir los principios de diseño optimiza el conformado y minimiza los defectos
- El perfilado es excelente para piezas largas, pero tiene limitaciones para tiradas cortas o formas complejas.
- Junto con el control de precisión y la automatización, proporciona una fabricación eficiente y competitiva.
En resumen, las máquinas de perfilado ofrecen una producción de alta velocidad y alta calidad de componentes metálicos. Cuando se aplica adecuadamente, el perfilado proporciona un valor excelente para largas series de producción en muchas industrias. Con la innovación continua en diseños de rodillos, herramientas y controles inteligentes, el perfilado sigue ampliando sus capacidades e impulsando la productividad metalúrgica.