Overview
Steel sheet roll forming machines are used to transform steel coils or sheets into customized profiles with precise dimensions and uniform quality. This is done by passing the sheet metal through consecutive sets of rollers that progressively shape the material as required.
Roll forming is one of the most economical ways to manufacture metal parts with long lengths and large production volumes. The process is versatile, fast and efficient compared to other methods like extrusion or pressing. It enables continuous and automated production lines resulting in low operational costs per piece.
Roll formed components have wide applications across industries like automotive, construction, agriculture, furniture, appliances and more. Common examples are roofing and wall panels, racks, metal studs, roof gutters, highway rails, door frames and car chassis parts among many others.
This guide provides a comprehensive look at various aspects of steel sheet roll forming machines from working principles, capabilities, components, parameters and configurations to design considerations, cost economics and supplier selection.
Types of Steel Sheet Roll Forming Machines
Roll forming machines are classified based on arrangement of rolls, number of operations, automation level and more. The main types include:
Inline Roll Forming Machines
- Known as straight-line or continuous roll formers
- Sheets pass through consecutive stands in longitudinal direction
- Suitable for long parts like panels, rails, channels with constant profile
- Limited ability for profile variations
Rotary Roll Forming Machines
- Rollers arranged in circular fashion for rotary forming
- Sheet is coiled around central mandrel
- Used for making rings, cylinders, cones and varied cross-sections
- High throughput and dimensional consistency
Combination or Modular Machines
- Hybrid machines with both inline and rotary stands
- Offers profile flexibility and high productivity together
- Allows forming helical shapes and tapered components
CNC Roll Forming Machines
- Roll tooling adjustable via computerized controls
- Quick changeover between profiles
- Advanced monitoring, precision and process control
- Ideal for rapid prototyping and custom profiles
Servo Motor Driven Machines
- Servo motors independently control each roller
- Enables real-time adjustments during production
- Reduces equipment and maintenance costs
- Improves forming accuracy and repeatability
Portable Roll Forming Machines
- Compact and portable units with fast setup
- Used directly at construction sites
- Limited to simple, low-volume applications
- Cost-effective for producing long single pieces
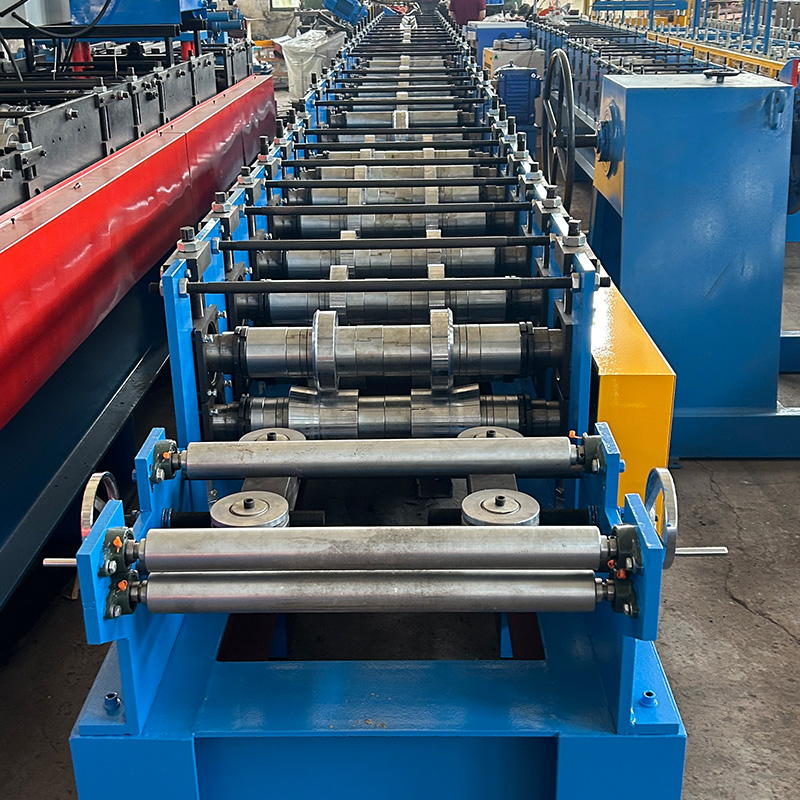
Main Components of a Roll Forming Machine
Roll forming machines, whether inline or rotary, comprise of the following fundamental components:
Roller Stands
These house the top and bottom rollers between which the sheet passes. Stands are arranged consecutively as per profile sequence. They contain:
- Roller shafts mounted on bearings
- Housings to support shafts and enable vertical adjustment
- Drive mechanisms to rotate shafts
Forming Rollers
These do the actual bending and shaping of sheet via calibrated contours. Various roller types:
- Breakdown – initial shaping
- Finishing – final profiling
- Pair – top and matching bottom roller
- Sizing – for thickness reduction
- Idler – no contours, for support
Entry Guides
First set of straight rollers that guide sheet into machine. Minimizes misalignment.
Process Rollers
Additional rollers for embossing, punching, cutting, notching or drilling sheets during forming.
Support Rollers
Provide support and maintain sheet alignment between forming stands. Prevent sagging.
Exit Guides
Final straight rollers that stabilize and guide finished profile out of machine.
Decoiler or Coil Car
Holds coil stock and feeds sheet into machine via powered unwinding. Has tension control.
Feed Table
Supports sheets between decoiler and entry guides. May have sheet position sensors.
Forming Drives
Motors coupled via gearbox to a line shaft driving all roller shafts via chains or belts.
Hydraulic System
Powers the vertical opening of roller stands for quick tooling changes.
नियंत्रण प्रणाली
Automated controls for precise roller speeds, process monitoring and safety features.
Key Specifications and Design Factors
Roll forming machines are customized for specific production needs. The table below summarizes the main parameters and factors considered during equipment selection and design:
Specifications | विवरण |
---|---|
बनाने की गति | Production rate in feet/min or m/min. Higher speeds need more horsepower. |
Line Shaft Speed | Rotational speed of main drive shaft in rpm. Determines roller speeds. |
Forming Stations | Number of roller stands required for complete profile sequence. |
Roller Size | Diameter and face width. Larger for heavy gauge sheets. |
रोलर सामग्री | Steel grades with hardening for strength, longevity and wear resistance. |
Roller Bearings | Withstand high loads. Sealed types prevent lubricant loss. |
Drive Type | Electric servo, hydraulic, mechanical etc. Affects control and energy efficiency. |
Feed System | Decoiler capacity, feed table design, sheet positioning. |
Tooling System | Easy and quick changeover to new profiles. |
Automation Level | Operator involvement vs precision programmable control. |
Gauges Handled | Thickness range of sheets to be formed. Need appropriate roller size, power. |
Materials | Steel, aluminum, other alloys. Need suitable roller materials and strengths. |
Part Dimensions | Width, length, complexity of desired profile shape. |
Production Volume | Short run vs high volume. Impacts automation level. |
Floor Space | Machine length. Rotary more compact than inline. |
Proper selection of above parameters ensures smooth and efficacious roll forming that maximizes output while delivering required quality and precision.
Working Principle and Process Flow
The fundamentals of how roll forming machines work are outlined below:
- Sheet Loading – Coils loaded onto powered de-coiler. Sheet fed into entry guides.
- Feeding – De-coilerunrolls sheet which is pulled through consecutive roller stands.
- Progressive Forming – Sheet passes through subsequent stands, each further shaping it incrementally.
- Roller Contouring – Upper and lower rollers have matching profiles for gradual bending.
- Dimensional Precision – Roll gaps, rotations and progression precisely controlled.
- Support and Stabilizing – Idler and support rollers stabilize sheet during forming.
- Additional Operations – Embossing, punching or cutting done in between stands.
- Profile Completion – Final stand finishes profile shape. Exit guides stabilize sheet.
- Formed Part Exit – Continuous length of completed profile exits machine for downstream processes.
Roll forming involves continuous and synchronized feeding, bending and calibrating of sheets longitudinally to achieve desired cross-sections. The incremental profiling allows large deformations without overstressing the material.
Roll Forming Advantages
Roll forming offers several benefits that make it ideal for high production volumes:
High Speed Processing
- Forming speed up to 100 m/min possible
- Automated, continuous production
- Capable of meeting large volume demands
Dimensional Consistency
- Programmable process with precision control
- Repeatable and accurate profiles
- Relatively low tolerances
Profile Flexibility
- Wide range of achievable shapes
- Parts with varied cross-sections
- Ability to form complex geometries
Material Savings
- No material waste from cutting
- Lean processing improves yield
- Lower scrap rates
Cost Efficiency
- Highly productive and fast process
- Lower equipment investment than presses
- Reduced operating costs
- Low cost per piece produced
Finished Appearance
- Smooth, aesthetically pleasing finishes
- Consecutive forming avoids flats
- No need for post-processing
These factors make roll forming suitable for producing metal components in large volumes across many industries.
Typical Applications and Products
The versatility of roll forming allows it to produce diverse profiles from simple to complex. Typical applications include:
Construction and Infrastructure
- Roofing, siding and wall panels
- Steel studs for framing
- Metal roof gutters and drainage pipes
- Highway crash barriers
- Guard rails, hand rails and balustrades
- Doors, windows and curtain wall frames
- Various structural sections
Automotive and Transportation
- Chassis frames and cross members
- Pillars, rails, crossbars
- Seat frames
- Wheels, rim profiles
- Truck bodies
- Utility trailer parts
- Railway carriage sections
Furniture and Appliances
- Shelving, racks, cabinets
- Boxes, enclosures, frames
- Panels, housings, covers
- Tubes, handles, support arms
- Custom profiles and trims
Agriculture and Machinery
- Boom sections, loader arms
- Guards, shields,Platforms
- Conveyors, hoppers
- Silo parts, augers
- Machine frames, brackets
Commercial and Retail Spaces
- Checkout counters
- Display stands, racks
- Signage and lighting
- Cladding, partitions
- Decorative trims
Roll formed components improve both structural properties and aesthetics across many products.
Roll Forming Process Capabilities
Modern roll forming machines offer broad capabilities that enhance flexibility:
High Strength Materials
- Ability to shape high strength steels up to 80 ksi yield strength
- Forming of stainless steel, titanium and aluminum grades
- Roll materials matched to sheet material
Thickness Range
- Can process sheets between 0.5 mm to 8 mm thickness
- Roll face widths sized appropriately for thickness
Profile Features
- Forming of different bead styles, embossing, ribs, etc
- Punching and drilling inline
- Special edge treatments like hemming possible
Dimensional Range
- Width up to 2500 mm and lengths over 15 m possible
- Rotary machines for rings over 3 m diameter
Quick Changeovers
- Modular tooling systems for fast profile switches
- Computer aided positioning systems
Integrated Fabrication
- Additional operations like punching, cutting, welding
- Integration with downstream processes
Flexible Automation
- Options for manual to fully automatic operation
- Easy integration of feeding, stacking, bundling
Precision and Control
- Force monitoring for quality assurance
- Servo electric drives for accuracy
- CNC for advanced monitoring and control
With such wide-ranging capabilities, roll forming can adapt to produce a vast range of component designs.
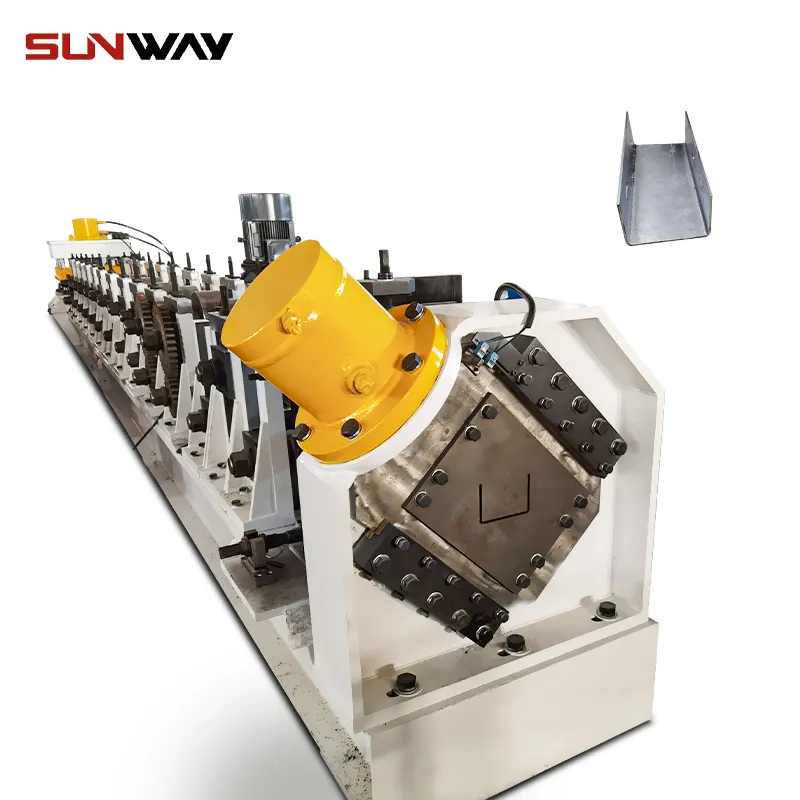
Design Principles and Process Optimization
Roll forming offers broad capabilities but requires optimal design to fully utilize its potential while avoiding defects. The main design principles are:
Profile Location
Determine the neutral axis – the forming sequence must advance from neutral axis outwards. This minimizes stresses.
Bend Sequence
First complete all full-length longitudinal bends. Follow with any edge bends or end features.
Sectional Forming
Best to avoid very different multi-plane bends in one pass. Do it in sections for stability.
Roll Contours
Must match sheet thickness. Too much clearance causes instability while too little jams sheet.
Roller Size
Roll barrel diameter size affects grip. Width determines support for sheet during forming.
Number of Passes
More passes allow larger bends with less stretching. But increases number of stands required.
Force Requirements
Estimate force per stand to determine line power needs. Excessive force damages roll tooling.
Grain Orientation
Align sheet metal grain parallel to feed direction. This prevents cracking during bending.
Sheet Support
Use adequate idler/support rolls to prevent sagging and maintain flatness.
Following proven design principles results in reliable processing and high quality outputs from roll forming machines. Additionally, the overall process can be optimized by:
- Correct coil placement and unwinding line layout
- Generous entry and exit zones for proper tracking
- Adjustable feed system for different sheet widths
- Quick change modular tooling for fast changeovers
- Precise process control via sensors, servos and automation
- Real-time monitoring of forces, speeds and tolerances
- Proper roller maintenance to sustain performance
- Operator training for efficient working and safety
Thoughtful design and line layout coupled with process improvements ensure smooth roll forming with maximum efficiency and quality.
Roll Forming Equipment Cost Economics
Roll forming can involve considerable upfront investment but offers very economical per piece production costs.
Equipment Purchase Cost
- Machine cost from $100,000 to over $1 million
- Customization, automation and size increase cost
- Cost per foot ~$800 to $1500 for average machines
Tooling Cost
- Around $3000 upward per forming station
- Profile-specific rolls must be purchased
- Quick change systems allow tooling re-use
Operating Cost
- Labor, maintenance and consumables
- ~10% of equipment cost annually
- Lower than other processes like stamping
Piece Price Economics
- Ideal process for volumes over 100,000 pieces
- Cost per piece can be as low as $1 to $5
- Saves over $100 per piece vs other processes
- Lead times and logistics costs also minimized
With effective planning and design, roll forming lines offer excellent return on investment while minimizing production costs.
Supplier Evaluation and Selection Criteria
Choosing the right roll forming equipment supplier is key to a successful project. Some key selection criteria include:
Company Reputation and Experience
- Years in business and industry experience
- Proven track record of installations and support
- Client testimonials and case studies
Quality and Reliability
- Use of premium components
- Stringent manufacturing and testing processes
- Installations operating without issues
Customization Expertise
- Capability to engineer customized solutions
- Range of machines and features offered
- Familiarity with diverse applications
Technical Capabilities
- In-house engineering and manufacturing
- Latest technology equipment and controls
- Proven machine designs for performance
Services Offered
- Design support and simulation/modeling
- Operator training and maintenance contracts
- Upgrade, retrofit and relocation services
Delivery and Support
- Manufacturing lead times
- Installation, commissioning and support
- Post-order service and long-term spare parts supply
Evaluating roll forming machine suppliers on above parameters minimizes project execution risks and ensures optimized equipment performance.
Pros vs Cons and Limitations
Roll forming offers many benefits but also has some inherent limitations:
Advantages
- Highly productive continuous process
- Low equipment capital investment
- Very low cost per piece
- No material waste
- Dimensional precision and repeatability
- Broad size range capability
- Suitable for high strength materials
Disadvantages
- Initial tooling cost per profile
- Size and weight constraints for parts
- Lead time for roll design and manufacture
- Limited ability for cross-section variations
- Not ideal for low production volumes
- Complex reverse profiles difficult
- Risk of defects like twist or bow
The advantages make roll forming ideal for high volumes. For lower volumes, other processes may be more suitable and economical depending on part size and complexity.
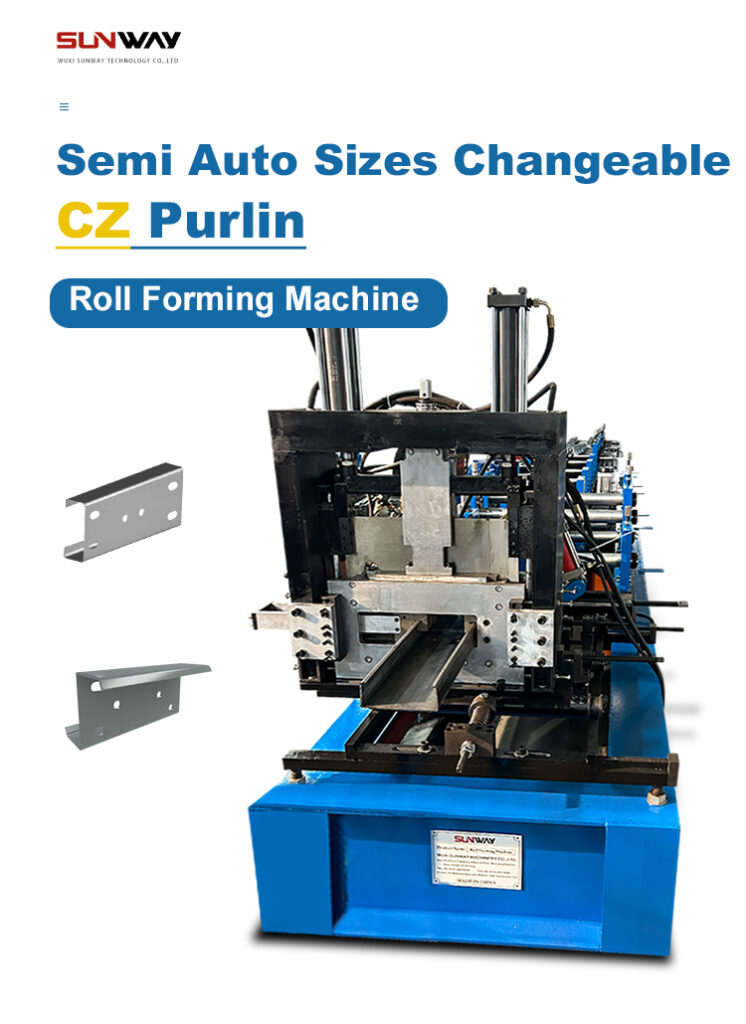
सामान्य प्रश्न
What materials can be roll formed?
- Common materials are low carbon steel, stainless steel, aluminum. Other formable alloys like brass, copper can also be processed. Material hardness should not exceed full-hard tempers.
What are common roll formed products?
- Construction panels, gutters, roofing, siding, drainage pipes, shelves, racks, chassis components, profiles for doors, windows and curtain walls are some examples.
How does roll forming compare with bending or press braking?
- Bending creates discrete parts by applying focused deformation whereas roll forming creates continuous profiles via gradual progression of lighter distributed bending in multiple small increments.
What tolerances are achievable in roll forming?
- Roll forming allows competitive tolerances of +/- 0.5 mm , which can be further enhanced with proper process monitoring and automated controls.
What determines the minimum and maximum part length in roll forming?
- Typically lengths of 1 to 15 meters are possible. The maximum length is influenced by material properties, sheet support and part design. Minimum length required is for about 8 to 10 forming stands to complete the profiling sequence.
How quickly can roll tooling be changed for new profiles?
- With modular quick change systems, typical changeover times range from 20 minutes to 1 hour. For frequent profile changes, CNC programmable stands help minimize changeover.
What defects can occur in roll formed parts?
- Potential defects are twist, bow, flare, warp, wrinkles, edge waviness. These can be prevented with proper machine maintenance, roll design, material quality and process control.
What factors affect roll forming machine pricing?
- Parameters like linear feet length, tonnage, automation level, speeds, coil capacity, material thickness range, drives, and controls impact cost. Typical range is $100,000 to $1 million.
What are the maintenance needs of roll formers?
- Basic preventive maintenance involves cleaning, lubrication, inspection for roll wear, drive tightness, bearings, hydraulics, electrics. Breakdowns are minimized with scheduled maintenance.
How long do roll forming machine components last?
- With proper use and maintenance, major mechanical components can reliably function for 15 to 25 years. Control systems may need upgrades sooner. Consumables like shafts, bearings, and tooling require replacement every 4-5 years or as wear demands.
निष्कर्ष
Key Takeaways
- Roll forming allows economical, continuous production of metal profiles with uniform quality
- Suitable for high volumes due to fast production rates and low costs
- Broad capabilities to form diverse shapes, high strength materials and
- Equipment design factors like drivetrain, automation level, tooling affect capabilities and pricing
- Following design principles optimizes forming and minimizes defects
- Roll forming excels for long parts but has limitations for short runs or complex shapes
- Coupled with precision control and automation, it provides efficient and competitive manufacturing
In summary, roll forming machines deliver high speed, high quality production of metal components. When applied appropriately, roll forming provides excellent value for long production runs across many industries. With ongoing innovation in roll designs, tooling, and smart controls, roll forming continues to expand its capabilities and drive metalworking productivity.