Mini perfiladoras son un importante tipo de equipo utilizado para conformar chapas y bobinas de metal en perfiles y piezas personalizadas. Este artículo proporciona una visión detallada de las mini perfiladoras, cubriendo sus características clave, especificaciones, proveedores, aplicaciones, funcionamiento y mucho más.
Visión general de las mini máquinas perfiladoras
Las mini perfiladoras, también conocidas como líneas de bobinado o curvadoras de perfiles, están diseñadas para producir perfiles metálicos de diferentes geometrías y tamaños a partir de bobinas.
He aquí los detalles clave sobre estos versátiles sistemas de conformado de metales:
- ¿De qué se trata? Máquina de perfilado que convierte chapas planas y bobinas en perfiles abiertos y cerrados personalizados doblando gradualmente el material a través de conjuntos consecutivos de rodillos.
- Componentes clave: Desenrollador, alimentador, precortador, estaciones de perfilado, postcortador, apilador.
- Tipos: Perfiladoras estándar y personalizadas de 4-14 rodillos para perfiles de hasta 120 mm de ancho.
- Materiales utilizados: Chapas y bobinas de acero, acero inoxidable y aluminio de hasta 3 mm de grosor.
- Aplicaciones: Ángulos, canales, tubos cuadrados/rectangulares, paneles para tejados, sistemas de estanterías, marcos de puertas, etc.
- Industrias: Construcción, infraestructuras, logística, transporte, agricultura, automoción, fabricación de electrodomésticos, etc.
- Ventajas: Alta precisión, consistencia, velocidad, flexibilidad y rentabilidad para la producción en serie.
- Limitaciones: Tamaño y grosor de perfil limitados, tolerancias inferiores a las de las prensas plegadoras o el corte por láser.
Las minihormigoneras ofrecen el equilibrio perfecto entre versatilidad, tamaño reducido, facilidad de manejo y precio asequible. Veamos en detalle las especificaciones clave y los aspectos de diseño.
Especificaciones de las mini líneas de perfilado
La tabla siguiente resume las especificaciones técnicas típicas de las mini perfiladoras:
Característica | Descripción |
---|---|
Capacidad de formación | 50-120 mm de anchura de perfil, hasta 3 mm de grosor |
Estaciones de rodillos | 4-16 |
Velocidad de formación | 10-25 m/min |
Potencia de accionamiento principal | 3-7,5 kW |
Tensión | 220-480 V, trifásico |
Sistema de alimentación | Cadena o servomotor |
Intercambio de rollos | Manual o automático |
Peso de la bobina | Hasta 3000 kg |
ID de bobina | 400-600 mm |
Espacio | 4×2 metros |
Controlar | PLC con pantalla táctil HMI |
Estas perfiladoras están disponibles en anchuras estándar como 50 mm, 75 mm, 100 mm, 120 mm y anchuras personalizadas. El número de estaciones de rodillos puede oscilar entre 4 para perfiles básicos y 16 o más para geometrías complejas.
La mayor potencia del accionamiento principal, entre 5,5 y 7,5 kW, permite velocidades de producción más rápidas. Los sistemas automatizados de cambio de rodillos y engaste de bordes facilitan el cambio rápido de perfiles.
Aspectos clave del diseño de miniformadoras
Algunos elementos de diseño notables que influyen en el rendimiento de las minilíneas de perfilado son:
- Material del rodillo - Rodillos de acero forjado de alta resistencia o de adamita.
- Unidades - Servomotores o motores normales para las secciones de bobinado, alimentación y conformado.
- Rodamientos de rodillos - Rodamientos de rodillos de alta resistencia para millones de ciclos de rotación.
- Diseño de rollos - Rodillos cóncavos/convexos de acero endurecido para un plegado óptimo.
- Ajuste de la separación entre rodillos - Ajuste motorizado o manual de las separaciones entre rodillos.
- Soporte para rodillos - Las carcasas reforzadas y los soportes de rodillos evitan la flexión.
- Sistema de alimentación - Pinzas de goma o cadenas de oruga para tracción.
- Decoilers - Potentes desbobinadores hidráulicos, neumáticos o motorizados.
- Seguridad - Cortinas fotoeléctricas, paradas de emergencia y protecciones garantizan la seguridad de funcionamiento.
- Marco - Robusto bastidor en C construido con canales de acero o vigas en I para minimizar las vibraciones.
La mejor calidad de los componentes y la construcción robusta garantizan piezas perfiladas de alta precisión, un procesamiento más rápido del metal y fiabilidad incluso con cargas pesadas.
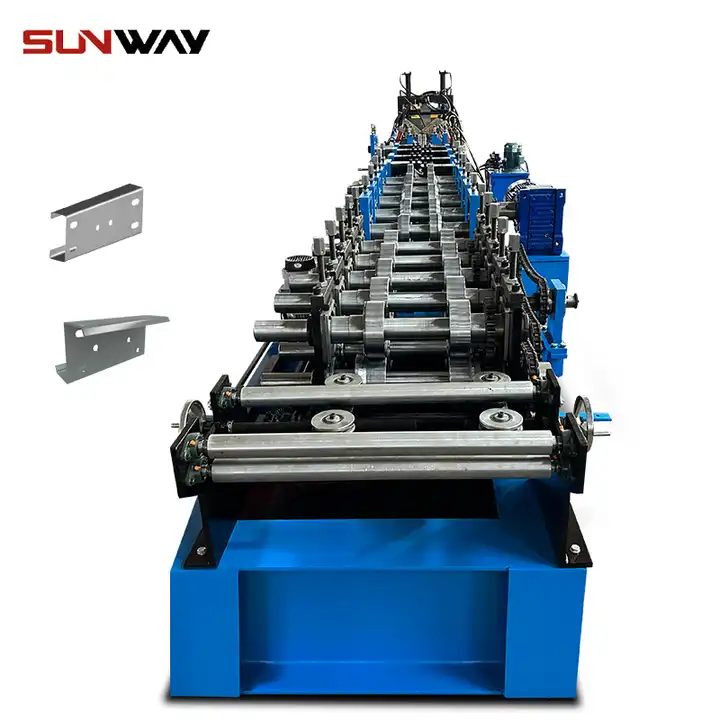
Tipos de mini perfiladoras
Existen dos tipos principales de sistemas de mini perfilado:
Perfiladoras estándar
Estas máquinas más sencillas de 4 ó 6 rodillos pueden producir perfiles regulares como cuadrados, rectángulos y ángulos básicos en anchuras fijas como 50 mm o 75 mm.
- Se utiliza para la producción de grandes volúmenes con cambios mínimos.
- Flexibilidad limitada: para producir nuevos perfiles es necesario cambiar los rodillos.
- Funcionamiento típicamente manual con menores costes.
Líneas de perfilado personalizadas
Estas avanzadas perfiladoras disponen de 10 o más estaciones de rodillos secuenciales que pueden personalizarse para producir complejos perfiles a medida.
- Altamente flexible y ajustable para cambios rápidos de perfil.
- Produce formas de perfil ilimitadas, incluidos nervios complejos, relieves, etc.
- Funciones automatizadas para cambios de tamaño rápidos y tiempos de inactividad mínimos.
- Ideal para variaciones frecuentes de producto y tiradas de menor volumen.
- Mayor coste de la máquina debido a la personalización.
Especificaciones principales de las mini máquinas perfiladoras
A continuación se indican las especificaciones y parámetros fundamentales que deben tenerse en cuenta a la hora de seleccionar una miniformadora:
Tabla - Especificaciones principales de las mini perfiladoras
Especificación | Descripción |
---|---|
Anchura del perfil | De 50 mm a 120 mm en incrementos estándar. Posibilidad de anchuras personalizadas. |
Material Grosor | De 0,5 mm a 3 mm para chapas y bobinas de MS. Hasta 4 mm para aluminio, latón, etc. |
Estaciones de rodillos | Determina la complejidad del perfil. Normalmente, de 4 a 16 estaciones. |
Velocidad de formación | Las velocidades más altas, entre 15 y 25 m/min, aumentan la productividad. |
Potencia de accionamiento principal | 5,5 kW-7,5 kW para un par y una velocidad de conformado óptimos. |
Tensión | Se requiere una fuente de alimentación trifásica de 400 V o 480 V. |
Diámetro de la bobina | Las bobinas de 1000 mm a 1500 mm de diámetro garantizan una producción continua. |
Peso de la bobina | Capacidad de hasta 3 toneladas métricas de peso de bobina. |
Capacidad del desbobinador | Desenrolladores hidráulicos o motorizados con capacidad de 2-3 toneladas. |
Sistema de alimentación | Cadena Caterpillar, rodillos de agarre, servomotor para estabilidad. |
Diseño de rollos | Rodillos de acero endurecido cóncavos/convexos de varios diámetros. |
Ajuste de la separación entre rodillos | Ajuste motorizado manual o NC para cambios rápidos. |
Rodamientos de rodillos | Rodamientos de rodillos de alta resistencia para millones de pasadas. |
Marco | Robusto bastidor en C de acero con bancadas mecanizadas de precisión para los rodillos. |
Seguridad | Cortinas fotoeléctricas, paradas de emergencia, protecciones para la seguridad de funcionamiento. |
Controlar | PLC con interfaz de pantalla táctil HMI para un manejo sencillo. |
Tenga en cuenta los volúmenes de producción, las especificaciones del material y la complejidad del perfil para seleccionar las especificaciones correctas de la laminadora.
Componentes clave de las minilíneas de perfilado
Las miniformadoras de rodillos constan de varias secciones clave diseñadas para funcionar en sincronía y formar perfiles de calidad de forma continua:
Tabla - Componentes principales de una mini formadora de rollos
Componente | Descripción |
---|---|
desbobinador | Desenrolla la bobina plana y la alimenta a la línea. Dispone de sistema de desenrollado motorizado y mandril porta-bobinas. |
Unidad de alimentación | Sujeta la chapa mediante rodillos/cadenas y la introduce a velocidad constante en la sección de conformado. |
Precortadora | Cizalla la bobina en tiras precortadas antes de formarlas según la longitud del perfil. |
Estación de formación | Serie de troqueles de rodillo de estilo piramidal que doblan gradualmente la banda a través de cada estación para formar el perfil. |
Armario de control | Alberga el PLC, la HMI, los accionamientos y los componentes eléctricos. Permite la programación y la supervisión. |
Unidad principal | Motorreductor que acciona el desenrollador, la alimentación y las secciones de formado de forma sincronizada. |
Post-cutter | Corta el perfil conformado a la longitud deseada según los requisitos de producción. |
Apilador | Apila o recoge ordenadamente los perfiles acabados. |
La interacción fluida entre estos subsistemas da como resultado un perfilado continuo, de alta velocidad y precisión.
Principio de Trabajo de las Mini Máquinas Perfiladoras
He aquí las etapas clave del funcionamiento de las minilíneas de perfilado:
- Desaceitado - La chapa metálica enrollada se sujeta en un mandril de desenrollado motorizado. Se desenrolla y se libera en la sección de alimentación.
- Alimentación - Los rodillos/cadenas de agarre enganchan la banda y la introducen a velocidad constante en la sección de conformado.
- precorte - La longitud de avance se precorta a la longitud de la pieza final mediante cuchillas de cizallado incorporadas.
- Formando - La longitud precortada se desplaza a través de estaciones de enrollado consecutivas de estilo piramidal. Cada estación dobla progresivamente la tira hasta conseguir la forma de perfil deseada.
- Post-corte - Las cortadoras de extremos recortan el perfil a la longitud final requerida según las necesidades de producción.
- Apilado - Las piezas conformadas se apilan ordenadamente para facilitar su manipulación y embalaje.
La velocidad de alimentación, las separaciones entre rodillos y la secuenciación se programan en el PLC, que coordina el proceso para una producción continua. Se utilizan avanzados programas de simulación en 3D para visualizar la secuencia óptima de los rodillos y la disposición de las matrices antes de fabricar los rodillos.
Aplicaciones y perfiles producidos en miniformadoras de rodillos
Estos son algunos de los perfiles, piezas y aplicaciones más comunes que se laminan en líneas de mini laminado:
Tabla - Perfiles típicos y aplicaciones de las minirrebobinadoras
Forma del perfil | Aplicaciones típicas |
---|---|
Tubo cuadrado | Enmarcado de muebles, equipamiento de tiendas, rótulos |
Tubo rectangular | Puertas, ventanas, rejas |
Canal angular | Bastidores, estanterías, vigas de techo |
Perfil Omega | Falsos techos, entramado de tabiques |
Perfil de Sigma | Piezas de automóviles, vagones de ferrocarril |
Perfil de baldosa escalonada | Láminas para tejados, revestimientos murales |
Perfiles trapezoidales | Tejados, paredes y revestimientos |
Marcos de puerta | Marcos metálicos para puertas de viviendas y edificios comerciales |
Paneles conformados | Carcasas de electrodomésticos, paneles de ascensores |
Perfiles personalizados | Curvado de perfiles según especificaciones del cliente |
La lista de ámbitos de aplicación es enorme: construcción, infraestructuras, logística, agricultura, automoción, electrodomésticos, mobiliario de oficina y muchos más.
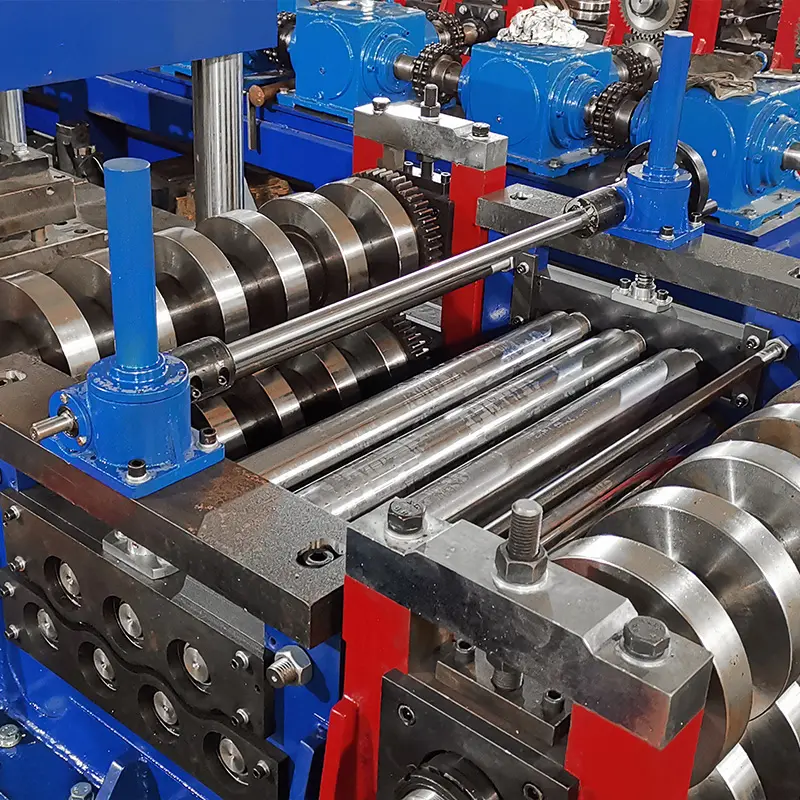
Ventajas y beneficios de las minilíneas de perfilado
Éstas son algunas de las principales ventajas de utilizar mini perfiladoras:
- Flexibilidad - Posibilidad de producir perfiles ilimitados cambiando las matrices de los rodillos.
- Eficacia - Alto rendimiento de producción de hasta 18.000 piezas por turno.
- Coherencia - Piezas de precisión con tolerancias estrechas y repetibilidad.
- Rentable - Menor coste que otros procesos alternativos como las prensas plegadoras.
- Ahorro de mano de obra - Producción automatizada con una necesidad mínima de mano de obra.
- Espacio eficiente - Su tamaño compacto ahorra espacio en la fábrica.
- Versatilidad - Capacidad para trabajar con una amplia gama de materiales y espesores.
- Escalabilidad - Aumento sencillo de la producción mediante turnos adicionales.
- Productividad - Producción continua con un tiempo de inactividad mínimo.
- Durabilidad - Máquinas robustas construidas para funcionar 24 horas al día, 7 días a la semana.
- Seguridad - Los avanzados mecanismos de seguridad evitan lesiones en el lugar de trabajo.
- Sostenibilidad - Reduce el desperdicio de material.
Las miniformadoras de rodillos son una solución ideal para producir perfiles y piezas metálicas en cantidades medias y altas para diversas industrias.
Limitaciones de las mini perfiladoras
Aunque las minilíneas de perfilado ofrecen muchas ventajas, algunas de sus limitaciones son:
- Tamaño del perfil - Limitado a perfiles más pequeños y anchuras inferiores a 120 mm.
- Espesor - Por lo general, capacidad inferior a 3 mm de grosor.
- Tolerancias - Tolerancias más estrictas difíciles de mantener en comparación con el plegado por láser o plegadora.
- Alargamiento - Puede producirse cierto alargamiento o estiramiento del material.
- Productividad - Menor rendimiento que las perfiladoras de tamaño normal construidas para producciones de gran volumen.
- Plazo de entrega - Los juegos de rollos personalizados tardan entre 4 y 6 semanas en fabricarse.
- Cambios - Los frecuentes cambios de perfil reducen los volúmenes de producción.
- Opciones de material - Limitado a metales procesables como acero, aluminio, etc. No es adecuado para materiales compuestos, plásticos, etc.
- Operaciones secundarias - Las piezas finales pueden requerir cortes, perforaciones, soldaduras, etc. adicionales.
- Mantenimiento - Es necesario engrasar y limpiar regularmente para mantener los rodillos y evitar atascos.
Comprender estas limitaciones ayuda a seleccionar las aplicaciones adecuadas en las que las mini-formadoras de rodillos proporcionan la solución de producción óptima.
¿Cómo elegir un mini rollo que forma MachineSupplier?
Estas son las consideraciones clave para elegir un fabricante de mini perfiladoras de confianza:
Tabla - Cómo seleccionar su proveedor de mini perfiladoras
Parámetro | En qué fijarse |
---|---|
Perfil de la empresa | Décadas de experiencia en perfilado. Certificación ISO. |
Calidad de la máquina | Uso de componentes de primera calidad. Fabricación de alta precisión. |
Habilidades de personalización | Capacidad para personalizar perfiles y funciones. |
Experiencia en herramientas para rodillos | Diseño propio de utillaje para rodillos. Plazos de entrega más cortos. |
Gama de máquinas | Varios tamaños y capacidades para ampliar posteriormente. |
Instalaciones de producción | Infraestructura de fabricación de vanguardia. |
Capacidades de ensayo | Controles de calidad de parámetros como la precisión, la velocidad, etc. |
Soporte de instalación | Asistencia in situ para la instalación y puesta en marcha. |
Capacitación | Formación de operadores para obtener la máxima productividad. |
Documentación | Manuales de instrucciones bien documentados. |
Servicio posventa | Rápida entrega de piezas de repuesto y asistencia. |
Costo | Precios competitivos y valor del producto. |
Elija fabricantes que ofrezcan funciones personalizadas, plazos de entrega rápidos para las herramientas, fiabilidad demostrada y un servicio posventa receptivo.
Coste y precio de las mini perfiladoras
El precio de las mini perfiladoras depende de las especificaciones, el nivel de automatización y la personalización. He aquí un resumen de los rangos de precios típicos:
Tabla - Consideraciones sobre el coste de la mini formadora de rollos
Capacidad | Especificaciones | Precios indicativos |
---|---|---|
Serie de 50 mm | 4 rodillos, manual | $4,000 – $7,000 |
Serie 75 mm | 6 rodillos, manual | $7,000 – $10,000 |
Serie de 100 mm | 10 rodillos, semiautomático | $15,000 – $20,000 |
Serie de 120 mm | 12 rodillos, automático | $20,000 – $30,000 |
Serie personalizada | 14+ rodillos, CNC | $30.000 en adelante |
- Las perfiladoras estándar de 50-75 mm con especificaciones básicas empiezan por menos de $10.000.
- Las series de 100-120 mm con más funciones de automatización y control cuestan entre $15.000 y $25.000.
- Las perfiladoras personalizadas construidas a medida con características especiales, utillaje, automatización y controles pueden costar más de $30.000.
Los costes adicionales incluyen el envío, los aranceles de importación, la instalación y la formación. Compare precios, pero céntrese en la calidad de la producción a largo plazo y en el coste por pieza producida.
¿Cómo manejar y mantener las mini perfiladoras?
Estas son algunas de las mejores prácticas para operar y mantener su mini línea de perfilado de forma óptima:
Tabla - Guía de uso y mantenimiento de la mini formadora de rollos
Actividad | Instrucciones | Frecuencia |
---|---|---|
Configuración de la línea | Programar los parámetros del perfil en el autómata programable. Consulte los planos de disposición de las herramientas. | Antes del inicio de la producción. |
Carga de materiales | Asegúrese de que el desenrollador sujeta bien la bobina. Ajuste la longitud de alimentación correcta. | Antes de cada cambio de bobina. |
Ajuste del balanceo | Ajustar las holguras del rodillo inferior según las instrucciones del utillaje. Volver a comprobar las presiones de conformado. | Antes de cada cambio de perfil. |
Prueba de funcionamiento | Haga funcionar la máquina a baja velocidad para probar el perfil recién configurado. Compruebe si hay vibraciones o problemas. | Después de la configuración o el ajuste. |
Producción | Aumentar gradualmente la velocidad hasta alcanzar la velocidad de conformado óptima. Supervise de cerca las primeras piezas producidas. | Producción diaria. |
Inspección en curso | Comprobar aleatoriamente que las piezas formadas tienen las dimensiones correctas. Asegúrese de que el apilador está alineando las piezas. | Periódicamente durante la producción. |
Lubricación de herramientas | Aplicar grasa de litio en rodamientos, engranajes, cadenas. Engrasar los rodillos formadores. | Semanal. |
Limpieza | Limpie el polvo y el polvo metálico de todas las secciones con aire comprimido. | Semanal. |
Apriete de pernos | Compruebe y apriete los pernos, abrazaderas y conexiones que se hayan aflojado utilizando una llave dinamométrica. | Mensual. |
Inspección del desgaste | Inspeccionar los cojinetes de los rodillos, los engranajes y las almohadillas del desenrollador en busca de desgaste. | Trimestral. |
Sustitución de piezas | Sustituya las piezas desgastadas, como cojinetes, almohadillas del desenrollador, rodillos formadores, etc. | Según sea necesario. |
Seguir procedimientos estandarizados y programas de mantenimiento preventivo maximizará la producción y prolongará la vida útil de los equipos.
Resolución de problemas comunes en las mini perfiladoras
Algunos problemas potenciales y acciones correctivas para las mini-formadoras de rodillos:
Tabla - Consejos para la resolución de problemas de las mini perfiladoras
Edición | Posibles causas | Medidas correctoras |
---|---|---|
Atasco del rodillo | Espesor excesivo del material Longitud de alimentación demasiado larga Huecos de los rodillos demasiado estrechos | Utilizar material inferior a 3 mm Reducir la longitud de alimentación Aumentar la distancia entre rodillos |
Deslizamiento de la banda | Rodillos de agarre desgastados Aceite/grasa en los rodillos | Sustituir los rodillos de agarre Limpiar bien los rollos |
Distorsión del perfil | Rodillos formadores desgastados Baja presión de conformado Rodillos desalineados | Revestimiento o sustitución de los rodillos Aumentar la presión del cilindro superior Volver a alinear los rodillos de conformado |
Defectos repetibles | Rollos dañados/rayados Acumulación de residuos | Pulir o sustituir los rodillos rayados Limpieza periódica de finos metálicos |
Vibración excesiva | Pernos de cimentación sueltos Componentes desequilibrados/desgastados | Apriete todos los tornillos de la base Sustituir rodamientos/engranajes defectuosos |
Perfilado desigual | Separaciones inadecuadas entre rodillos Rodamientos desgastados | Restablecer los huecos de los rollos paso a paso Sustituir los rodamientos desgastados |
Sobrecalentamiento del motor | Alimentación de baja tensión Alimentación demasiado rápida Contactos eléctricos sueltos | Comprobar la tensión de entrada Reducir la velocidad de alimentación Apriete todas las conexiones eléctricas |
Una inspección minuciosa y prestar atención a ruidos o comportamientos inusuales puede ayudar a identificar y rectificar los problemas a tiempo.
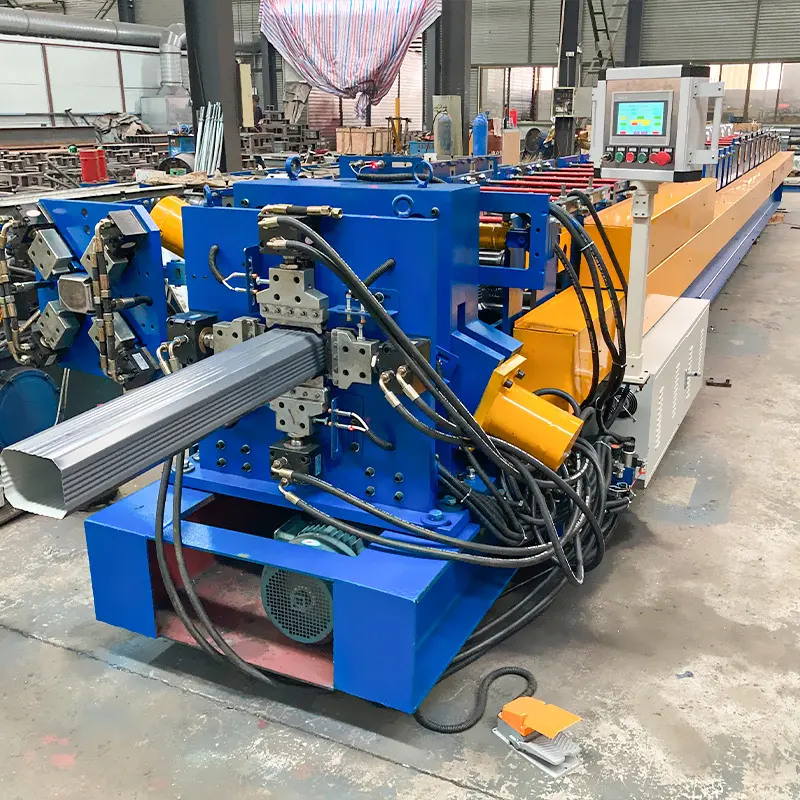
Consejos de seguridad para el manejo de mini perfiladoras
Trabajar con seguridad es fundamental cuando se utiliza cualquier maquinaria de fabricación de metales. Estas son algunas pautas de seguridad clave para los equipos de perfilado:
- Todos los operarios deben estar plenamente formados y autorizados para utilizar la laminadora.
- La máquina debe colocarse en una zona restringida para evitar el acceso de personas sin formación.
- Todas las piezas móviles, como engranajes, cadenas o rodillos, deben estar protegidas. Las protecciones deben mantenerse completamente cerradas.
- Los botones de parada de emergencia deben instalarse cerca de la máquina, al alcance de los operarios.
- Pueden instalarse cortinas fotoeléctricas en los puntos de entrada y salida del material para detener la máquina si el operario se acerca demasiado.
- Los paneles y las puertas de las máquinas deben tener enclavamientos de seguridad que deshabiliten el funcionamiento cuando se abran.
- Las zonas de los rodillos deben estar protegidas para evitar que los dedos queden atrapados entre los rodillos.
- La zona del laminador debe estar bien iluminada para poder ver todas las zonas con claridad.
- La máquina debe conectarse a tierra correctamente mediante el terminal de tierra suministrado.
- El cableado eléctrico debe revisarse con regularidad y los cables dañados deben sustituirse inmediatamente.
- Los aceites para engranajes y otros lubricantes sólo deben aplicarse con la corriente desconectada.
- En caso de que se produzcan ruidos fuertes, deben utilizarse protectores auditivos, como tapones para los oídos.
- Quítese la ropa suelta, las joyas, el pelo largo, etc. que puedan engancharse en las piezas móviles.
- Asegúrese de que la zona del suelo se mantiene libre de aceite, herramientas u otros peligros de resbalones o caídas.
Análisis comparativo: Perfilado frente a plegado con plegadora
Las plegadoras y las perfiladoras ofrecen dos alternativas habituales para el plegado y la fabricación de perfiles. He aquí una comparativa de las principales diferencias:
Tabla - Comparación entre perfilado y plegado con plegadora
Parámetro | Perfilado | Plegado con plegadora |
---|---|---|
Principio de funcionamiento | Material formado continuamente a través de estaciones de rodillos consecutivas | Material estampado entre las matrices superior e inferior |
Productos típicos | Perfiles abiertos, por ejemplo, canales, ángulos | Perfiles cerrados, por ejemplo, cajas, paneles |
Productividad | Mayor rendimiento, funcionamiento continuo | Menor producción, producción por lotes |
Requisitos laborales | Menor debido a la automatización | Mayor debido a la manipulación manual de materiales |
Duración del ciclo | Tiempos de ciclo mucho más rápidos, mayores velocidades | Más lento debido a la carga/descarga manual |
Precisión y tolerancias | Precisión y tolerancias moderadas | Control de alta precisión y tolerancia |
Limitaciones de tamaño | Anchuras inferiores a 200 mm | Conformado más ancho hasta 2000 mm o más |
Espesor Capacidad | Material de calibre fino inferior a 4 mm | Puede manejar material más grueso 10mm+ |
Tiempo de preparación | Cambios más rápidos entre perfiles | Cambios de troquel más lentos |
Costes de utillaje | Juegos de rodillos de menor coste | Caros troqueles rectificados de precisión |
Volúmenes de producción ideales | Volúmenes medios a altos | Cantidades de producción bajas o medias |
Coste de capital inicial | Menor precio de la máquina | Coste de la prensa plegadora significativamente superior |
Flexibilidad de diseño | Puede crear un número ilimitado de perfiles abiertos | Limitado a troqueles cerrados prefabricados |
Operaciones secundarias | Puede necesitar desbarbado, acabado | Mejor acabado de los bordes |
Requisitos de fuerza | Menor fuerza debido a la flexión gradual | Gran fuerza de flexión instantánea |
En resumen, el perfilado por rodillos es ideal para una alta productividad y un conformado continuo de perfiles abiertos, mientras que las plegadoras ofrecen una precisión y un control superiores a escala de producción media.
Software de perfilado para el diseño y la simulación de formas de rollo
Se dispone de sofisticados programas de software para el diseño y la simulación de formas de rodillos. Entre las principales funciones se incluyen:
- Creación de modelos 3D de diseños de perfiles CAD deseados por el cliente.
- Simulación virtual del proceso de laminado y secuenciación de puestos de laminado.
- Comprobación de posibles problemas como grietas o recuperación elástica.
- Modelado del flujo correcto de material a través de los rodillos.
- Calcular con precisión las fuerzas de rodadura.
- Visualización de la forma del patrón plano antes del plegado.
- Simulación de la ubicación y rotación correctas de cada rodillo en 3D.
- Comprobación de interferencias entre cualquier componente del utillaje.
- Comprobación del perfil que se desarrolla a través de las estaciones.
- Optimización del diseño del paso de rodillos.
- Generación de planos de fabricación para la producción de rollos.
- Creación de documentos de configuración con los espacios correctos entre rodillos para cada estación.
- Estimación del tiempo de producción por pieza.
Principales ventajas del software de simulación:
- Permite iteraciones rápidas de diseño a un coste muy inferior al de los prototipos físicos.
- Elimina las conjeturas en el diseño de secuencias y utillajes.
- Reduce el tiempo de diseño de herramientas de semanas a días.
- Evite piezas desechadas debido a una configuración incorrecta de las herramientas.
- Optimiza la geometría de la matriz del rodillo para un flujo uniforme del material.
- Comprueba los diseños digitalmente en lugar de mediante ensayo y error.
El avanzado análisis por elementos finitos garantiza un diseño óptimo del paso de rodillos antes de la producción.
Últimas innovaciones en tecnología de perfilado
Algunas innovaciones notables que transforman el perfilado moderno incluyen:
- Punzonado y corte en línea - El corte y la perforación integrados antes de las estaciones de perfilado aumentan la eficacia y minimizan los pasos secundarios.
- Cabezales de conformado de cambio rápido - Los cabezales modulares permiten intercambiar rápidamente diferentes juegos de rodillos para cambiar rápidamente de perfil.
- Accionamiento servoeléctrico - Los servomotores y accionamientos proporcionan un control de velocidad rápido y preciso para una mayor precisión.
- Tratamiento térmico en línea - El precalentamiento por inducción integrado mejora el conformado de aceros de ultra alta resistencia.
- Control de la fuerza - Los sensores supervisan las cargas de los rodillos y ajustan automáticamente las presiones para obtener una producción de calidad.
- Soldadura en línea/adhesivo - Operaciones de unión y llenado integradas en el proceso de laminado.
- Simulación 3D avanzada - Modelado más realista del proceso de laminación mediante AEF y potencia de computación en nube.
- Detección inteligente - Sistemas de visión para inspección dimensional y mantenimiento predictivo.
- Conectividad IoT - Supervisión remota, resolución de problemas y análisis de datos para minimizar el tiempo de inactividad.
- Control de calidad automatizado - Visión artificial para la detección de imperfecciones superficiales tras el laminado.
- Minifábricas a medida - Líneas de rodillos compactas que producen diferentes perfiles según la demanda del cliente.
Estas tendencias permiten fabricar componentes laminados de mayor complejidad, calidad y automatización.
Normas de seguridad para el perfilado
La maquinaria de perfilado debe cumplir estrictas normas de seguridad para el cumplimiento de la normativa y la protección de los empleados. Entre las principales normas figuran:
- ISO 12100 sobre principios generales de seguridad para el diseño de maquinaria.
- EN 1010 sobre los requisitos de seguridad de las perfiladoras y prensas.
- ANSI B11 sobre protección de máquinas para trabajar el metal.
- OSHA 1910 sobre la normativa estadounidense de seguridad de la maquinaria en el lugar de trabajo.
- Cumplimiento de la marca CE para las normas de seguridad de la UE.
- Dispositivos de seguridad con enclavamiento según ISO 14119 que impiden el acceso a las zonas peligrosas.
- ISO 13857 sobre posicionamiento seguro y espacios libres para el acceso y el mantenimiento.
- ISO 16090 sobre dispositivos de parada de emergencia.
- ISO 4413 sobre normas de seguridad para máquinas accionadas hidráulicamente.
- ISO 4414 para la seguridad de los sistemas neumáticos.
- Normas de compatibilidad electromagnética para una correcta conexión a tierra y aislamiento.
- La norma ISO 13850 establece los requisitos que deben cumplir los botones de parada de emergencia.
Es obligatorio disponer de protecciones, enclavamientos de seguridad, paradas de emergencia y conexión a tierra de acuerdo con estos códigos.
Asociaciones de la industria de perfilado
Asociaciones mundiales del sector que ofrecen conocimientos, normas tecnológicas y plataformas de trabajo en red:
- Asociación Europea de RMI - Representa a las empresas de perfilado en Europa.
- Asociación de Fabricantes de Transformados Metálicos - Asociación estadounidense de la industria del perfilado y otras tecnologías metalúrgicas.
- Asociación Japonesa de Perfilado - Asociación de la industria japonesa de perfilado.
- APROFAC - Consejo de la Asociación de Laminadoras de Asia y el Pacífico.
- Asociación Australasiana de Chapa Metálica - Organismo industrial de los fabricantes de chapas metálicas de Australia y Nueva Zelanda.
Organizan conferencias, publican conocimientos del sector, apoyan la formación de los trabajadores y representan los intereses de los miembros. Ser miembro activo ayuda a conocer las últimas tecnologías y las mejores prácticas del sector.
Requisitos de formación para operarios de perfilado
La formación adecuada de los operadores de máquinas es clave para maximizar la productividad y la calidad. Aspectos típicos de la formación:
- Procedimientos de seguridad: tolerancia cero al riesgo, paradas de emergencia, equipos de protección.
- Visión general de los controles de la máquina: modos de desplazamiento, velocidad, sensores de bordes, etc.
- Manipulación de materiales: carga y alimentación de bobinas, apilado de perfiles.
- Cambio de rodillos: extracción y sustitución de los rodillos de conformado.
- Inspecciones del primer artículo: verificación de la calidad de la producción.
- Aparatos de medición: micrómetros, calibres, galgas.
- Lubricación y mantenimiento preventivo.
- Solución de problemas comunes: atascos, deslizamientos, distorsiones, etc.
- Buena limpieza: limpieza de multas, aceites derramados, etc.
- Normas de calidad para los perfiles acabados.
- Utilización de instrucciones de trabajo y manuales técnicos.
- Almacenamiento y manipulación adecuados del material.
- Equilibrado de la línea para obtener el máximo rendimiento.
- Apilado y empaquetado eficaces de las piezas acabadas.
Una formación eficaz se traduce en una mayor utilización de la máquina, menos desechos, un entorno de trabajo más seguro y una mayor vida útil de los equipos.
Oportunidades profesionales en perfilado
He aquí algunas trayectorias profesionales prometedoras en el sector del perfilado:
- Operadores de máquinas - Manejo y ajuste de maquinaria de perfilado.
- Fabricantes - Fabricación de perfiles laminados para armarios, estructuras, etc.
- Técnicos de mantenimiento - Resolución de problemas y reparación de líneas de laminado.
- Diseñadores de herramientas - Diseño de secuencias óptimas de paso de rodillos.
- Ingenieros de procesos - Optimización de los procesos de perfilado y de la calidad.
- Jefes de producción - Gestión de las operaciones del taller de perfilado.
- Inspectores de calidad - Inspeccionar los perfiles conformados y garantizar su cumplimiento.
- Ingenieros de ventas - Asistencia técnica comercial para soluciones de perfilado.
- Diseñadores CAD - Modelización de perfiles y simulación de procesos.
- Directores de compras - Adquisición de materias primas e inventario de maquinaria.
El sector ofrece buenas perspectivas dado el crecimiento de la demanda de piezas perfiladas en todas las industrias.
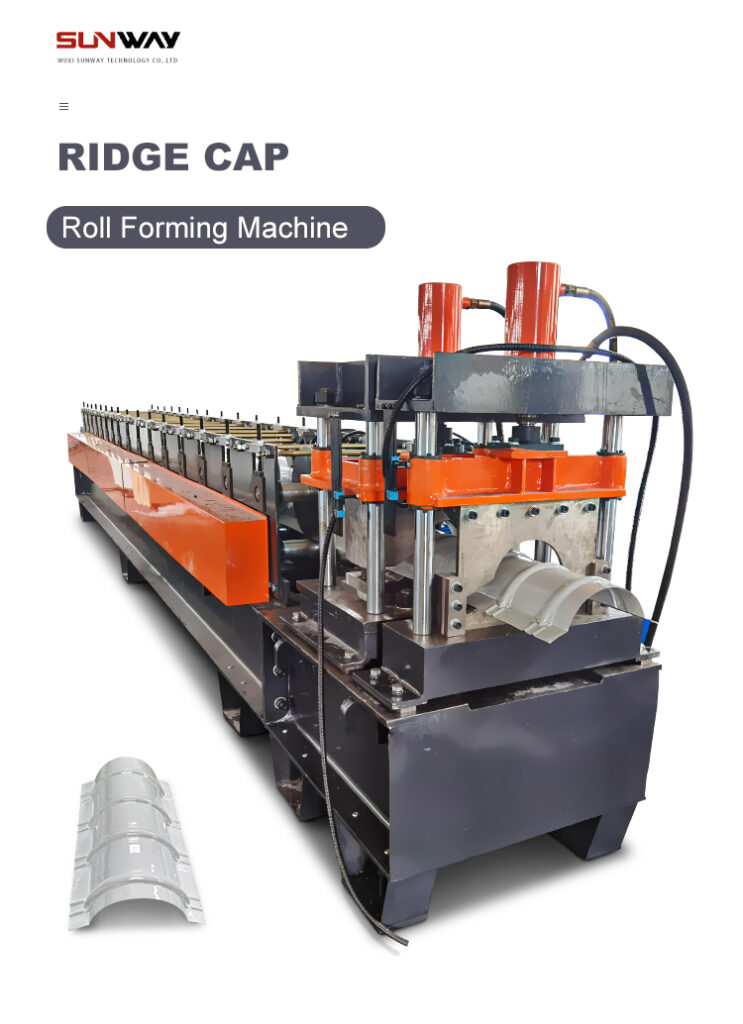
Fabricantes de perfiladoras
Algunos de los principales fabricantes mundiales de maquinaria de perfilado son:
- Samco Machinery (Reino Unido)
- LAPCO (Taiwán)
- Gasparini (Italia)
- Knuth (Alemania)
- Form Process Engineering (EE.UU.)
- Bradbury (EE.UU.)
- Dimeco (Países Bajos)
- Botou Xianfa (China)
- Jouanel Industrie (Francia)
- JIDET (India)
- Laminadoras de rodillos Zani (Italia)
- Shanghai Rollforming (China)
- Metform (EE.UU.)
A la hora de adquirir equipos de perfilado, asóciese con fabricantes que dispongan de una amplia gama de productos, una fiabilidad demostrada y un servicio ágil.
Aspectos clave - Guía de mini perfiladoras
- Las miniformadoras de rodillos ofrecen un método ideal para producir perfiles metálicos de hasta 120 mm de anchura a partir de bobinas y chapas.
- Constan de secciones de desbobinado, alimentación, precortado, perfilado y poscortado de chapas para una producción continua.
- Las perfiladoras ofrecen ventajas de consistencia, velocidad y coste en comparación con otras tecnologías alternativas.
- La secuenciación de las pasadas se optimiza mediante avanzados programas de simulación en 3D.
- El mantenimiento preventivo periódico y la formación de los operarios son vitales para obtener el máximo rendimiento.
- Los sistemas de protección y los procedimientos de formación deben aplicarse con diligencia.
- Con la selección de la máquina y las prácticas de utilización adecuadas, las mini perfiladoras ofrecen una solución de fabricación versátil y rentable.
Preguntas frecuentes
P: ¿Cuáles son los costes típicos de mantenimiento de una mini perfiladora?
R: Los costes anuales de mantenimiento suponen una media de 2-4% del coste de la máquina en función de la intensidad de uso. Esto incluye consumibles como aceites, grasas, piezas de repuesto para cojinetes, cadenas, engranajes, almohadillas de desbobinado, etc., además de los gastos de mano de obra de los técnicos. Un funcionamiento correcto y unos cuidados preventivos pueden minimizar los costes de mantenimiento.
P: ¿Qué nivel de habilidad del operario se necesita para las mini perfiladoras?
R: Las miniformadoras de rodillos están diseñadas para un manejo sencillo. La configuración de la máquina se simplifica mediante sistemas PLC controlados por menús. Los operarios medios pueden recibir una formación completa sobre el funcionamiento correcto de la máquina en 1-2 semanas. Las habilidades clave necesarias son la capacidad de interpretar planos, juzgar la calidad del perfil, la resolución de problemas básicos y las prácticas de seguridad diligentes.
P: ¿Cuál es la tasa de producción de las mini perfiladoras?
R: La tasa de producción depende de la velocidad de la máquina, la complejidad del perfil y la habilidad del operario. Las tasas de producción típicas son:
- Perfiles sencillos - Hasta 25 metros por minuto
- Formas complejas - 10 - 15 metros por minuto
Por lo tanto, en un turno normal de 8 horas se pueden producir aproximadamente de 15.000 a 20.000 pies lineales.
P: ¿Qué perfiles y tipos de productos pueden laminarse?
R: El perfilado es ideal para perfiles abiertos como canales, ángulos, tubos cuadrados/rectangulares que pueden conformarse de forma continua. Los perfiles cerrados, como bandejas, paneles, etc., son posibles mediante técnicas especiales como la soldadura por calor. Se fabrica una amplia gama de productos mediante perfilado, como puertas, paneles, tejados, estanterías, piezas de vagones de tren, guardarraíles de autopistas, etc.
P: ¿Cuál es la capacidad de espesor de las pequeñas perfiladoras?
R: Las perfiladoras estándar pueden procesar chapas de entre 0,5 mm y 3 mm de grosor. Existen perfiladoras especiales para procesar materiales más gruesos de hasta 6 mm utilizando herramientas más robustas. El aluminio y otros metales más blandos también pueden conformarse en espesores mayores. Los niveles máximos de dureza que pueden manejarse con fiabilidad son de unos 300 BHN.
P: ¿Cuáles son las averías más comunes del laminador y cómo corregirlas?
R: Los defectos como la torsión, el abocardado o la rotura se deben a problemas como rodamientos desgastados, espacios desiguales, desalineación de la alimentación, etc., y pueden solucionarse ajustando las presiones de conformado, la lubricación, la velocidad de alimentación del material y realineando los componentes. La inspección y el mantenimiento periódicos minimizan estos fallos.
P: ¿Cuál es el peso de envío de una mini formadora de rollos típica?
R: El peso del envío varía en función de la configuración, pero suele oscilar entre 1.000 y 2.500 kg para una máquina con 10 estaciones y 5 metros de longitud. Esto incluye embalaje, palés, materiales de embalaje, etc. Requiere remolque cubierto, buque de carga o flete marítimo para el transporte.