ক deck roll forming machine is an important piece of equipment used in the metal fabrication industry. It is designed to form metal sheets into corrugated panels that can then be used for various applications such as roofing, siding, and decking. In this article, we will take an in-depth look at what exactly a deck roll forming machine does and how it works.
Overview of Deck Roll Forming Machines
A deck roll forming machine takes flat metal coils or sheets as input and converts them into corrugated panels as output. The process involves gradually bending the sheet metal into the desired corrugated profile as it passes through a series of roller stations within the machine.
The rollers are designed to apply pressure and create bends at strategic locations across the width of the sheet. As the sheet metal passes through each roller station, the profile becomes more defined until the final corrugated shape is achieved towards the end of the machine.
Roll forming allows for continuous and efficient production of corrugated panels. It is a cost-effective alternative to other processes like pressing or stamping. The rollers can be easily customized to produce panels with different dimensions and profiles.
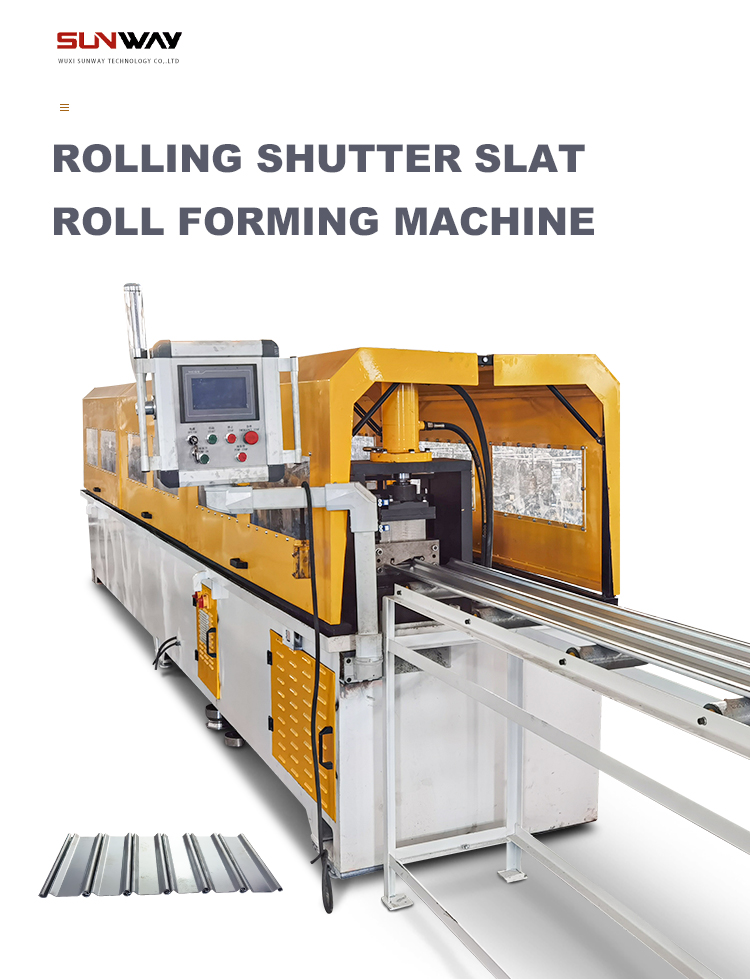
Main Components of a Deck Roll Forming Machine
A deck roll forming machine consists of three main sections:
আনকোয়লার
This is where the flat metal coil is loaded. The uncoiler then feeds the coil sheet into the roll forming section at a uniform speed and tension. It ensures the sheet enters the first forming rollers smoothly.
Forming Section
This is the main section where the actual roll forming takes place. It consists of several roller stations that gradually shape the metal into the required corrugated profile. The number and configuration of rollers vary based on the profile design.
Cutter
Once the corrugated sheet exits the last roller station, it reaches the cutter. The cutter shears the panel to the desired length as per the specifications entered into the control system. The cut panels are then collected on the exit side.
How Deck Roll Forming Machines Work
The working principle of a deck roll forming machine involves three key phases:
1. Sheet Feeding
The uncoiler at the entry end holds a coil of flat sheet metal that needs to be formed. It steadily feeds the sheet into the first roller station to initiate the roll forming process. The feed rate is controlled electronically to match the speed of the forming section.
2. Profile Forming
As the sheet enters the forming section, it passes between a series of roller stations. Each station has a set of rollers designed to bend the sheet incrementally to the profile being produced. The rollers apply localized pressure across the sheet width to create precise bends.
The stations are aligned so the sheet passes from one set of rollers to the next. As it travels through each station, the degree of bending increases gradually until the final corrugated shape is achieved. The roller design, their positioning, and sequence are critical to achieving the correct profile.
3. Cutting to Length
After passing through the final roller station, the formed sheet reaches the cutter. Based on the length entered, the cutter shears the sheet transversely into the required panel dimensions. The panels then exit the machine where they can be collected for further processing if needed.
Programming and Controls
Modern deck roll forming machines are equipped with programmable logic controllers (PLCs). This allows operators to enter key parameters like sheet width, sheet thickness, corrugation profile, and desired panel length.
The PLC automatically adjusts the roller positioning and cutting sequence as per the input. On some machines, the operator can save forming recipes for quick recall based on regular panel sizes.
Precise electronic controls monitor and regulate the sheet feeding rate, roller pressure, and cut length. This improves efficiency, minimizes errors, and gives consistent output.
Key Factors in Profile Forming
There are some critical aspects that determine the quality of profile forming:
- Roller design – The roller contour must match the shape being formed across the full sheet width. Any mismatch can cause distortion.
- Roller pressure – Sufficient pressure must be applied by the rollers to bend the metal without damaging it. Pressure levels are adjusted electronically.
- Roller alignment – Rollers must be precisely aligned across each station to ensure uniform bending. Even minor misalignment can affect profile accuracy.
- Roller lubrication – Roller bearings must be well lubricated to reduce friction as the sheet passes through. Insufficient lubrication can markings on the sheet.
- Forming speed – The machine speed must coordinate with material feed rate and roller pressure. High speeds can impact quality.
- Material properties – Factors like sheet thickness, grade, coating, and internal stresses affect how easily it can be formed. Machines are programmed accordingly.
Applications of Roll Formed Deck Panels
Deck roll forming allows efficient production of corrugated metal panels that have several structural applications:
- Roofing – Corrugated roofing panels made of galvanized steel, aluminum, or other metals provide strength, weather protection, and drainage.
- Siding – Architectural wall cladding using fluted siding panels is an attractive and durable exterior solution.
- Flooring – Corrugated metal floor decking is extensively used in mezzanines, walkways, platforms, and staircases.
- Ceilings – Decorative corrugated ceiling panels enhance aesthetics and can conceal wiring, ducting, and piping.
- Wall partitioning – Fluted metal wall panels are a convenient way to create partitions and enclosures.
- Structural decks – In buildings, roll formed decking acts as formwork for concrete slabs and provides composite strength.
Benefits of Using a Deck Roll Forming Machine
There are several advantages to using a deck roll forming machine:
- Continuous processing with high production volumes compared to other methods.
- Ability to create different corrugation profiles by changing rollers.
- Adjustable to handle metal coils/sheets of varying width and thickness.
- Automated controls and recipe storage improves efficiency and consistency.
- Lower cost compared to processes like pressing or stamping.
- Minimal scrap generation since profile is formed gradually.
- Safer enclosed forming with lesser hazards than open operations.
- Compact footprint requiring less floor space.
- Easy to integrate with other downstream processes like cutting, printing, punching etc.
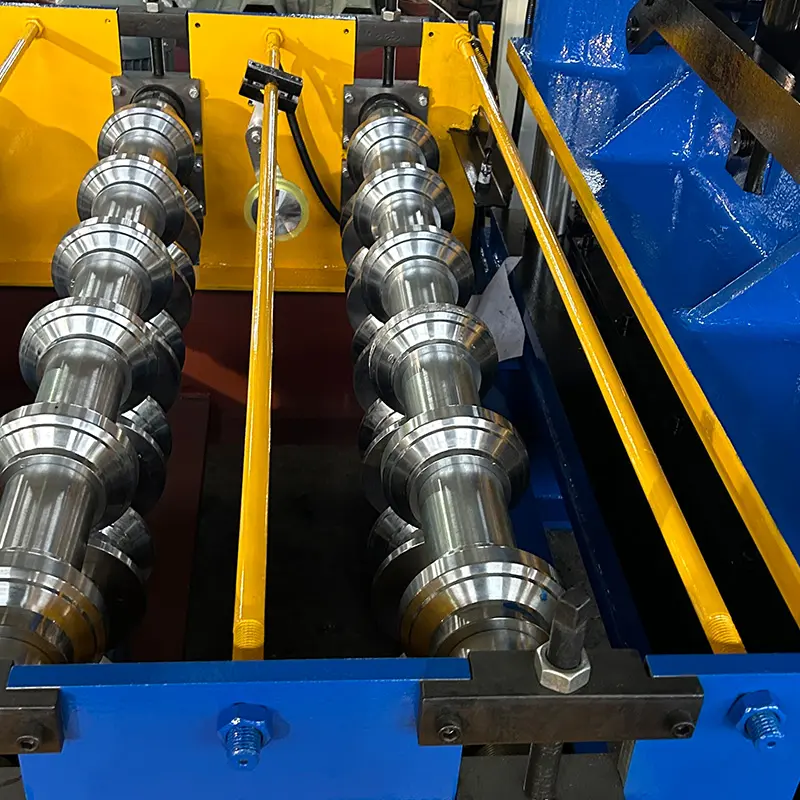
উপসংহার
A deck roll forming machine is indispensable equipment for efficiently producing corrugated metal panels. It can handle large production volumes and offers flexibility in terms of material thickness, profile design, and panel size. Automated controls allow pre-programmed recipes for different profiles that operators can quickly select. The gradual roll forming process results in excellent profile accuracy with minimal scrap generation. With advantages like low cost, high productivity, and process flexibility, deck roll forming is widely used across industries to manufacture corrugated roofing, siding, flooring and structural decking.
FAQ
What materials can be formed on a deck roll forming machine?
Deck roll forming machines can handle a wide range of metals including mild steel, stainless steel, aluminum, copper, and titanium. The most common materials used are galvanized steel, zinc-aluminum coated steel, and aluminum.
What is the thickness range of metals that these machines can process?
A standard deck roll forming machine can easily process metal coils and sheets ranging from 0.4 mm to 3 mm thickness. Heavy-duty machines are available that can form up to 6 mm thick materials.
What are some common corrugation profiles produced on these machines?
Some popular profiles include trapezoidal or inverted U shape, sine wave or arched shape, angular corrugations like V or U shapes, curved ribbed profiles, and many more customized shapes.
How are rollers changed to create different corrugation profiles?
Most deck roll forming machines allow quick roller changeovers using cassette systems. Pre-assembled roller stations with different profiles can be swapped in or out from the side using guide rails and locks. This reduces downtime between profile changes.
Can a deck roll forming machine be integrated with a slitting line?
Yes, many manufacturers offer integrated solutions combining a coil slitting line for metal coils with the deck roll forming machine. This allows preprocessed narrower coils to be directly used for roll forming.
How much maintenance is required for a deck roll forming machine?
Routine maintenance involves lubrication of rollers, inspection of forming rolls, checking electronic systems, and recalibrating sensors. Annual maintenance requires a more thorough inspection of components and any repairs or replacements needed. Proper maintenance enhances longevity and performance.
What safety aspects need to be considered when operating a deck roll forming machine?
Critical safety measures include – installing guarding around moving parts like rollers, ensuring proper machine grounding, activating interlocks on doors, testing emergency stop buttons, and providing operators with protective gear. Only properly trained personnel should operate the machine.
What is the typical production rate of these machines?
Production speed depends on the profile design complexity but generally varies from 10 to 45 meters per minute. Higher speeds are possible on machines with more robust construction. Simple profiles can be produced faster than highly complex designs.
How is the cut length controlled in a deck roll forming machine?
The machine operator enters the desired cut length through the touch screen interface. This data is fed to the programmable controller which signals the cutter to shear the panel to length at the specified dimension. State-of-the-art systems allow cutting lengths to be entered for each individual panel.
What are the advantages of automated programmable controls?
Automated controls through a PLC allow the operator to quickly select pre-programmed recipes. Operating parameters are instantaneously adjusted for different profiles and material thicknesses. This improves efficiency, accuracy and reduces set-up times. Consistent quality output is achieved through electronic monitoring of all critical forming and cutting functions.