Overview of Cold Bending Roll Forming Machines
Cold bending roll forming machines are used to bend and form metal sheets into customized profiles through an incremental and continuous rolling process. They are ideal for mass production of parts like roofing panels, steel studs, gutters, door panels etc. Key features include:
- Bends sheets up to 3 mm thickness from various materials like steel, aluminum, brass, copper etc.
- Forms complex and accurate profiles through a series of arranged rollers
- Continuous process with adjustable speed for high output
- Computer controlled for automatic precision forming
- Compact footprint suitable for factory integration
- Lower tooling costs than press brakes or other fabrication methods
কোল্ড রোল তৈরির মেশিনের প্রকারভেদ
There are several types of cold roll forming machines that provide different levels of flexibility, automation and output capacities:
Table 1: Cold Roll Forming Machine Types
Type | Description |
---|---|
Standard Roll Former | Basic machine with fixed forming rollers for continuous runs of one profile. Manual material feeding and part cutoff. |
CNC Roll Former | Computer numerically controlled with servo motors for automatic roller adjustment. Allows quick changeovers between different pre-set profiles. |
উৎপাদন লাইন | High output roll formers integrated with decoilers, straighteners, shears and other in-line processes for automated mass production. |
Custom Roll Former | Customized machine with specialty forming rollers for proprietary profiles. Requires engineering of roll dies and tooling. |
Portable Roll Former | Compact and movable cold bending roll forming machine for on-site or workshop use. Limited profile capability. |
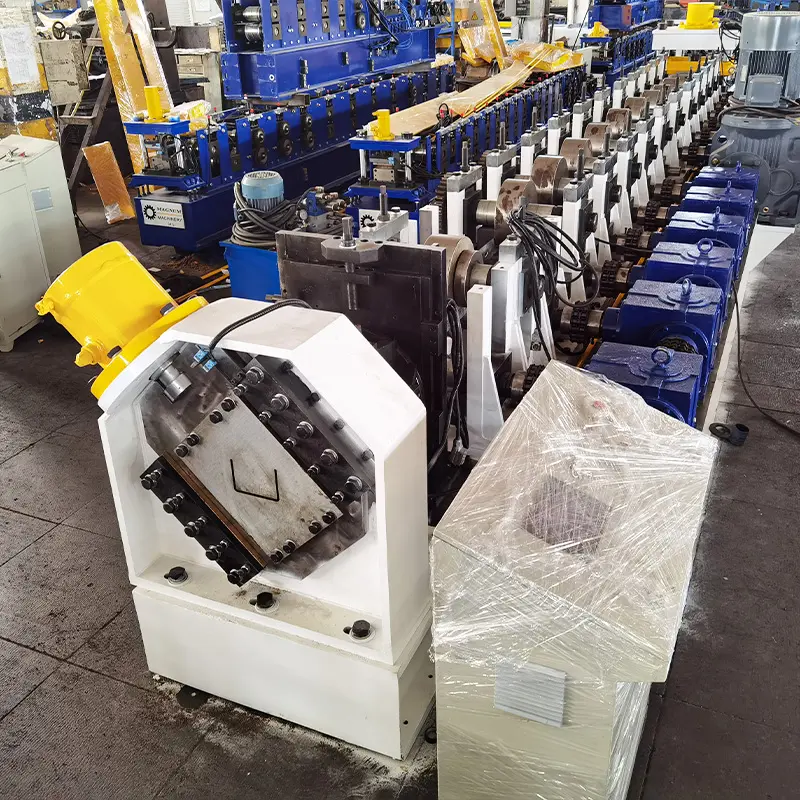
Key Components of a Cold Roll Forming Machine
The main components of a typical cold roll forming machine include:
Table 2: Cold Roll Forming Machine Components
Component | Description |
---|---|
ডিকয়লার | Holds coil of sheet metal to be fed into the roll former continuously |
Feeder | Feeds sheet into rolls at a controlled speed and tension |
Forming Rollers | Special roll dies that progressively bend sheet into desired profile |
Cutter | Cuts formed profiles at set lengths for individual parts |
Control Panel | Controls roller position, material feed, cut-off etc. |
PLC/Computer Control | For programming recipes and automating process parameters |
ফ্রেম | Rigid frame that houses components under tension loads |
Design and Working Principle
Cold roll forming works by continuously feeding a flat strip of sheet metal through a series of roller dies to incrementally form the material into a designed profile. As the material passes through each roller pair, it is gradually shaped until the final profile is achieved.
The rollers are arranged along the progressive forming stations in a sequence that allows material bending without overstressing. The roller design and position is engineered specifically for the profile that needs to be formed. Typically around 12-16 roller pairs may be used depending on part complexity.
Lubricants are applied to the sheet metal to reduce friction as it passes through the rollers at high speeds. The lubricant also helps maintain smooth surface finishes. Chemical coatings may be applied for corrosion resistance or UV protection after forming.
Applications and Profiles Produced
Cold bending roll forming can produce a wide range of formed metal components. Typical applications include:
Table 3: Cold Roll Forming Applications
Industry | Common Profiles Produced |
---|---|
Construction | Roofing panels, decking, purlins, wall studs, floor joists, doors, railings |
Automotive | Body panels, shells, chassis parts, brackets |
Appliances | Panels, housings, enclosures, shells |
Furniture | Legs, frames, desks, wireways |
Packaging | Racks, pallets, boxes, shelves, tubs |
Solar | Mounting rails, clamps, channels |
Nearly any open profile shape can be formed, from simple arcs, ribs and bends to complex geometries with punchouts and embosses. Hollow closed sections may require specialized rollers. Common profiles include:
- C-channels
- Zeds
- Angles
- Hat sections
- Box tubing
- Formed tubes
- Custom ribs, beads
Specifications
Cold roll forming machines are available in a wide range of sizes and specifications to produce small parts to large panels up to 3m wide. Main parameters include:
Table 4: Cold Roll Forming Machine Specifications
Parameter | Typical Range |
---|---|
Forming Length | 1 – 10 m |
Forming Width | Up to 3 m |
Material Thickness | 0.3 – 3 mm |
গঠন গতি | 10 – 80 m/min |
Forming Stations | 10 – 20 |
Roller Diameter | 100 – 250 mm |
বেলন উপাদান | Alloy steel or iron |
Drive Motor | 5 – 15 kW |
Control | PLC, CNC |
পাওয়ার সাপ্লাই | 380V, 3-phase |
Machine Weight | 2000 – 10000 kg |
Larger and more powerful machines are available for specialized high-volume continuous production lines. Customized machines can be engineered for proprietary profiles and specifications.
Roll Tooling Design and Manufacture
The key to successful roll forming is the precision engineering of the roller dies. The roll tooling is designed based on the required profile specifications and the plastic deformation properties of the material.
Roll tooling design must take into account parameters like metal thickness, width, yield strength, bending radius, springback etc. to calculate optimal roller positioning and geometries. 3D CAD and FEA tools are used to simulate material flow and stresses for validating tool paths.
The roll dies are CNC machined from alloy steel. One-piece rolls are used for common shapes like arcs and ribs. Multi-part split rolls allow forming of more complex profiles. Quick-change systems using spacers and shims allow flexibility for different profiles.
Process Design Considerations
Some key process factors to consider during cold roll forming:
Table 5: Cold Roll Forming Process Considerorsations
Factor | বিস্তারিত |
---|---|
Material | Ductility, strength, thickness, coatings, width, microstructure. Yield strength important for calculating bending forces |
Tooling | Roller design, size, materials, surface finish. Precision machining for accurate profiles. |
Lubrication | Reduces friction between sheet and rollers. Allows higher forming speeds. Consider temperature stability. |
Feed Speed | High speeds increase output but can cause defects. Optimal speed depends on material and profile. |
Bending Radii | Larger radii distribute strain and reduce thinning. Minimize radii for strength. |
Springback | Elastic recovery once part leaves rollers. Compensate by overbending. Depends on material. |
Direction | For sheet, bend perpendicular to rolling direction which has higher strength. |
Section Length | Longer sections require support rollers to prevent sagging. |
Wall Thickness | Thicker materials need higher roll forces. Can cause webs to deform. |
Careful design and trials are necessary to fine-tune the interacting parameters for a robust process. Defects like buckling, wrinkling, curling and tearing can occur if not properly controlled.
Manufacturers and Suppliers
Some of the major manufacturers supplying cold roll forming equipment include:
Table 6: Cold Roll Forming Equipment Manufacturers
প্রতিষ্ঠান | Location |
---|---|
Formtek | USA |
স্যামকো মেশিনারি | Canada |
Bradbury Group | UK |
Gasparini | ইতালি |
Shanghai Slitter | China |
T&H Lemont | USA |
Innovative Produktionssysteme GmbH (IPS) | Germany |
In addition to large international suppliers, many regional manufacturers also offer cold roll forming machines. When selecting a supplier, factors like build quality, engineering support, cost, lead time, and maintenance services must be evaluated.
Cost Considerations
Cold roll forming equipment represents a major capital investment, but can pay back through operational efficiencies and reduced labor for high production volumes. Key cost factors:
Table 7: Cold Roll Forming Machine Cost Factors
Parameter | Typical Cost Range |
---|---|
Standard Roll Former | $50,000 – $500,000 |
CNC Roll Former | $80,000 – $800,000 |
উৎপাদন লাইন | >$500,000 |
Custom Roll Former | >$200,000 |
Portable Roll Former | $15,000 – $100,000 |
Roll Tooling | $2000 upwards per profile |
Installation | 10-20% of machine cost |
Freight & Taxes | 5-10% of machine cost |
Larger production lines with decoilers, cut-offs, straighteners etc. can cost over a million dollars. Operating costs include maintenance, spare parts, consumables like lubricants and coatings, and electricity consumption.
Choosing the Right Supplier
Key factors when selecting a cold roll forming machine supplier:
Table 8: Choosing a Cold Roll Forming Machine Supplier
Consideration | বিস্তারিত |
---|---|
Technical Expertise | Experience designing, building, installing similar equipment. Qualified engineers. |
Build Quality | Use of precision components from reputable brands. Robust structural design. |
Flexibility | Ability to handle future custom profiles. Quick changeover systems. |
Production Capacity | Size and power ratings adequate for output volumes. |
Controls | Type of automation, ease of programming new profiles. |
Services | Installation support. Local service for maintenance. Operator training. |
Roll Tooling | In-house tooling design and manufacturing capability. |
Lead Times | Schedule for design, manufacture, shipment, installation. |
References | Track record executing similar projects successfully. Strong testimonials. |
Cost | Pricing in line with market and capabilities. Attractive payment terms. |
Compliance | Meet all applicable safety, electrical, building codes. |
Reputable manufacturers should be willing to provide referrals to previous buyers. Site visits to existing installations are highly recommended during qualification.
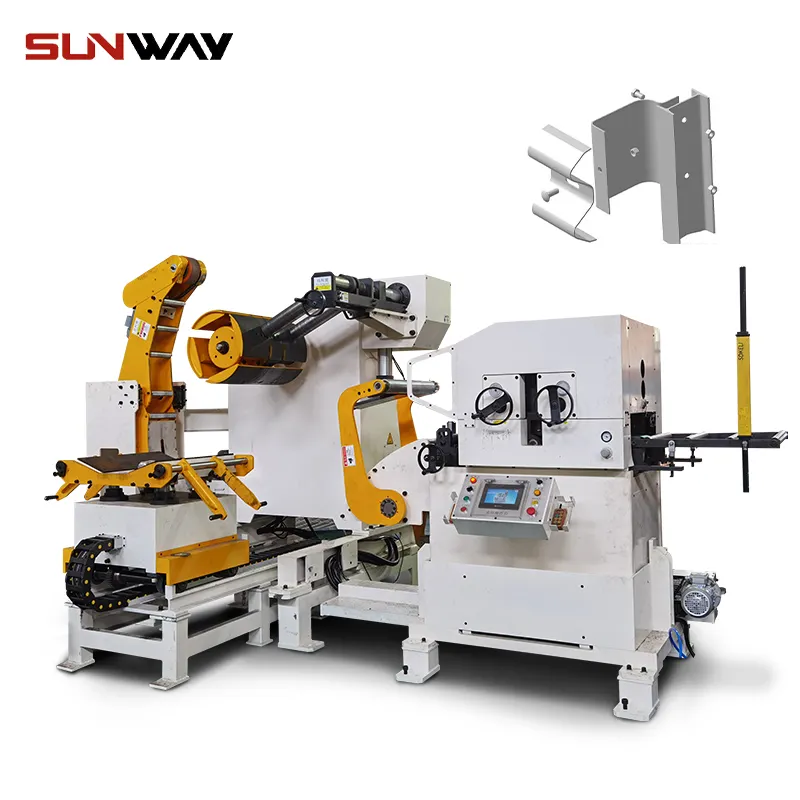
Installation and Operation
Proper installation and operation procedures are necessary for safe, efficient and quality roll forming:
Table 9: Cold Roll Forming Machine Installation & Operation
Activity | Procedure |
---|---|
Installation | Level machine on vibration-isolation foundation Connect electric power, pneumatic lines, lubrication Test run without load to confirm clearances |
Safety | Enclose pinch points, provide guards Ensure operators wear gloves, goggles, non-slip shoes Mark safety zones, provide interlocks |
Setup | Install correctly designed roll tooling Position guide rolls, support and straightening rolls Thread sheet through rollers and align Set feed speed, cut-off length |
Operation | Maintain steady, even feed of sheet Monitor lubrication levels and flow Inspect profile dimensions continuously |
Maintenance | Clean rollers and framing regularly Lubricate bearings and sliding parts Check roll alignment and wear Replace damaged rollers immediately |
Troubleshooting | Adjust roller alignment if profile distorted Increase/decrease bend increment to correct springback Slow speed for wrinkling; increase for tearing Check roll design, material orientation |
Only properly trained personnel should operate the machine after full safety procedures are established. Proper maintenance is crucial for preventing unplanned downtime and defects.
Advantages of Cold Roll Forming
Key benefits of cold bending roll forming machines:
- Highly productive continuous process for mass production
- Consistent and repeatable quality of parts
- Capability to form complex custom profiles
- Low tooling costs compared to other fabrication methods
- Scalable production by adding in-line processes
- Adjustable parameters through CNC control
- Minimal secondary operations required after forming
- Suitable for a variety of materials from thin gauge to thick metals
- Strength and aesthetic appeal of roll formed parts
- Safer operation compared to manual metal bending techniques
Limitations and Challenges of Cold Roll Forming
Some drawbacks and difficulties include:
- High initial capital cost of equipment and tooling
- Long lead times for design and manufacturing of roll dies
- Not economical for very low production volumes
- Size limitations based on machine capacity
- Skill required for proper roll tooling design to avoid defects
- Potential for scratching of material surface during forming
- Noise generation requiring noise reduction measures
- Requirement of sheet in coil form at set widths
Cost Saving Analysis
Here is an example cost analysis for a sample high volume production scenario:
- Monthly volume of 100,000 C-channel roofing parts required
- 12 ft long C-channel with hemmed flanges
- Material is 0.05″ thick 5052 aluminum
Table 10: Cost Comparison – Roll Forming vs. Manual Fabrication
Method | রোল গঠন | Manual Fabrication |
---|---|---|
Equipment Cost | $250,000 | $50,000 |
Tooling Cost | $20,000 | $5000 |
Production Rate | 600 ft/min | 10 ft/min |
Monthly Labor | 100 hrs | 670 hrs |
Labor Rate | $25/hr | $25/hr |
Monthly Labor Cost | $2500 | $16,750 |
Total Monthly Cost | $29,167 | $21,667 |
Payback Period | 5 months | – |
This simple analysis shows that despite higher initial equipment investment, labor savings of roll forming make it economical for such mid to high production volume scenarios. Exact breakeven points can be calculated through more detailed cost modeling.
Cold Roll Forming vs Press Brake Bending
Cold roll forming and press brake bending are two common sheet metal fabrication processes. Here is a comparison between the two methods:
Table 11: Roll Forming vs Press Brake Comparison
Parameter | রোল গঠন | Press Brake |
---|---|---|
Operation | Continuous | Batch |
Automation | High | Low-Medium |
Setup time | Medium | High |
Production rate | High | Low-Medium |
Labor | Low | High |
Capital cost | High | Low-Medium |
Tooling cost | Low | High |
পুরুত্ব | 0.5 – 2 mm | 0.5 – 4 mm |
Strength | High | Medium |
Tolerances | High | Medium |
Surface finish | Good | Fair |
Secondary ops | Few | Many |
অ্যাপ্লিকেশন | Standard profiles, panels | Custom parts, enclosures |
In summary, roll forming is better suited for continuous high volume production while press brakes allow more flexibility for lower quantities and custom components.
Frequently Asked Questions
Q: What sheet metal materials can be roll formed?
A: Most ductile metals including low carbon steel, stainless steel, aluminum, copper, and brass. Best results are achieved with materials in annealed condition. Very high strength alloys may need intermediate annealing.
Q: What thickness range can be cold roll formed?
A: Standard cold roll forming is typically used for metal thickness between 0.3 mm to 3 mm. Thicker materials require higher roll tonnage capacity machines. Thinner foils under 0.2 mm require special handling.
Q: How many forming stations are required for typical profiles?
A: Most common profiles like C and U channels, ribs, gutters require 10-16 stations. More complex or taller profiles may need 20+ stations. Deeper profiles can be formed through a sequence of double pass stations.
Q: What defects can occur during cold roll forming?
A: Defects like wrinkling, warping, flaring, splitting, and scratching can happen if process parameters and tool design are not optimized. FEA simulation and prototyping should be done.
Q: Is lubrication required during cold bending roll forming?
A: Yes, appropriate lubricant must be applied for reducing friction between sheet surface and tooling. It lowers rolling forces required and improves surface finish.
Q: How long does roll forming machine design and manufacture take?
A: For standard catalog machines, lead time can be 4-8 weeks. Custom machines with production lines involve more extensive engineering and estimates up to 6 months should be considered.
Q: What is the typical production rate of cold roll forming machines?
A: Production rate depends on profile complexity and length of formed part. Typical speeds are 10 – 100 ft/min. Very long parts may require slower speeds and support rollers.
Q: Is cold roll forming process suitable for medium production volumes?
A: Yes, machines with quick changeover can be economical for medium volumes of 5,000-10,000 pieces/month by alternating between profiles.
Q: What regular maintenance is required for cold bending roll formers?
A: Maintenance includes lubricating bearing and shafts, inspecting & replacing worn rollers, cleaning deposits on tooling, checking belt tension & alignment.
উপসংহার
Cold roll forming provides an ideal process for continuous high volume production of metal profiles across many industries. Machinery has become highly advanced with controlled automation and quick changeover capabilities between profiles. Precision engineered roll dies capable of intricate shapes combined with television monitored processes ensure consistently high quality standards. With proper machine selection, tooling design and process control, cold bending roll forming offers and efficient fabrication solution for mass producing formed sheet metal components.