Roll forming is a metal forming process used to produce long sheet metal parts with constant cross-sections. A roll forming machine progressively forms metal strips into the desired cross-sectional profile by passing them through consecutive sets of rolls.
Small roll forming machines are designed for low to medium production volumes and smaller part sizes. They offer an economical solution for small manufacturers to create custom rolled metal parts in-house versus outsourcing.
This guide provides a comprehensive overview of small roll forming machines covering types, specifications, applications, installation, operation, suppliers, costs, and more.
Overview of Small Roll Forming Machines
Roll forming machines are available in a wide range of sizes from small machines for low volume production to large high-speed lines for mass manufacturing.
Key factors distinguishing small roll formers:
Small Roll Former Characteristics:
Parameter | বিস্তারিত |
---|---|
Production Volumes | Low to medium volumes, usually under 500 pieces per shift |
Part Sizes | Narrow width up to around 800 mm, thinner gauges |
Line Speed | 10 – 45 feet/min typical |
Forming Stations | Up to 10 forming stands depending on part complexity |
Main Drive Power | Usually under 15 kW |
Machine Weight | Under 10,000 lbs footprint |
Cost | $50,000 to $500,000 price range |
Small roll forming equipment provides an affordable in-house production solution for businesses with lower output requirements and smaller parts like brackets, panels, tubes, and channels.
Types of Small Roll Forming Machines
There are two main categories of small roll formers:
Standard Roll Forming Lines
- Consist of modular in-line forming and cutting stations
- Offer flexible roll tooling that can be set up for different profiles
- Production volumes around 100-500 pieces per shift
- Part lengths typically up to 25 feet
- Used for short to medium runs
Rotary Table Roll Formers
- Compact design with forming stands arranged in a circle
- Sheet metal is formed as table rotates it through the stands
- Lower output around 50-200 pieces per shift
- Shorter maximum part lengths, usually under 15 feet
- Suited for high mix, low volume production
Roll Former Types Comparison:
Machine Type | Standard Roll Line | Rotary Table |
---|---|---|
Production Volume | Medium | Low |
Max Part Length | Long | Short |
Changeover Time | Longer | Faster |
Flexibility | High Mix | Lower Mix |
Cost | Higher | Lower |
Both designs offer advantages for small production scale roll forming with flexible quick change tooling. Standard in-line machines have higher output while rotary table systems enable faster changeovers.
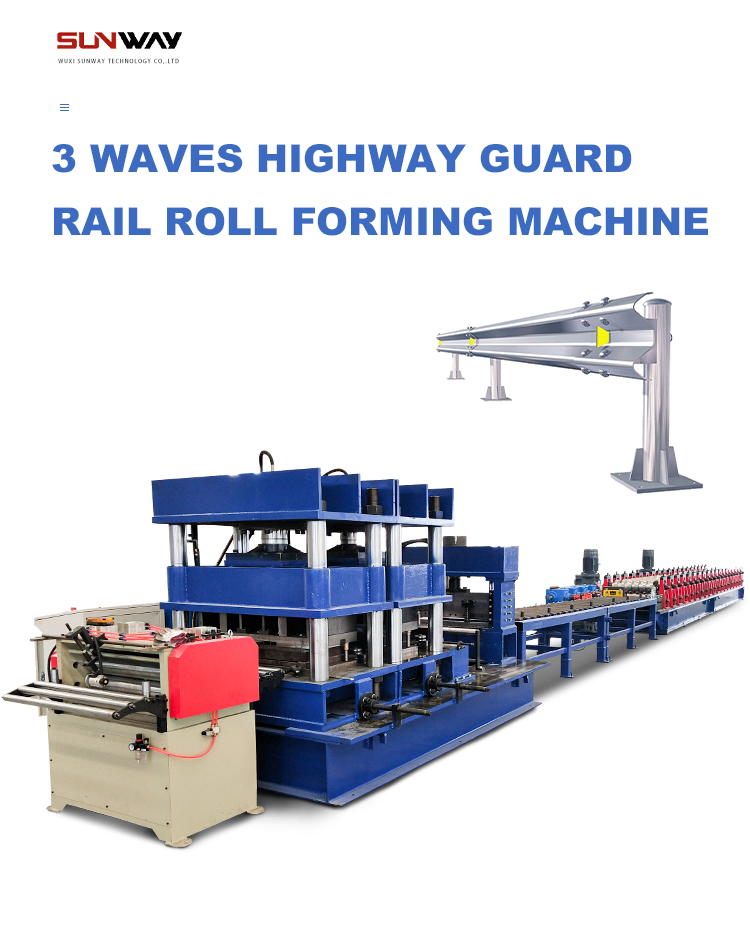
Small Roll Former Specifications
Key specifications to consider for purchasing or designing a small roll forming system include:
Small Roll Former Design Specifications:
Parameter | Typical Range |
---|---|
Forming Stations | 4-10 stands |
Line Speed | 10-45 ft/min |
Main Drive Power | 5-15 kW |
Material Thickness | 20-16 gauge (0.8-1.5 mm) |
Material Type | Carbon steel, stainless steel, aluminum |
Part Width | Up to 800 mm |
Part Length | Up to 25 ft (in-line), 15 ft (rotary) |
Roll Tooling | Quick change cassette style |
Controls | PLC with HMI touchscreen |
Machine Weight | < 10,000 lbs |
Machine Size | 10-30 ft length |
The number of forming stands, max strip width, and main drive power determine the range of part sizes and material gauges the roll former can produce. Quick change tooling allows flexible set up for different profiles.
Small Roll Former Design Considerations
Key factors to consider when selecting and integrating a small roll forming system:
Roll Former Design Considerations:
Parameter | বিস্তারিত |
---|---|
Production Volume | Size machine for expected output rates |
Part Sizes | Choose width and power to suit part dimensions |
Material Type | Tooling and machine construction for material used |
Part Design | Profile complexity impacts stations required |
Secondary Operations | Add stations for punching, cutting, bending, welding if needed |
Quick Change Tooling | Reduces changeover time for high product mix |
Controls | Automated for easy operation and data tracking |
Safety | Guards, e-stops, interlocks for safe operation |
Line Integration | Material handling and automation level |
The production application determines how the roll former is designed, equipped, and integrated into the manufacturing process.
Roll Forming Process Overview
Roll forming creates parts by gradually bending sheet or coil material through a series of forming stands:
Roll Forming Process Steps:
- Sheet/coil material enters the roll former
- Progressive stations bend the material incrementally
- Contour matched roll tools shape the profile
- Cut-off saws cut parts to length
- Formed parts exit the line
Roll Forming Advantages:
- Efficiently mass produces long parts with constant profile
- Good dimensional accuracy and surface finish
- Wide range of material sizes and types
- Lower tooling costs versus stamping
- Ideal for high production volumes
Roll formed parts require lower press tonnage versus stamping, but do need longer machines for the forming stations.
Small Roll Former Applications
Small roll forming machines produce metal parts for a wide range of applications:
Industry Applications:
- HVAC and ventilation – ducts, vents, louvers
- Building and construction – studs, track, roofing, siding, gutters
- Furniture – legs, frames, handles
- Transportation – panels, tubes, brackets
- Material handling – rails, conveyors, guards
- Agriculture – panels, structural parts
- Industrial equipment – guards, frames, enclosures
Typical Part Shapes:
- C and U channels
- Square and rectangular tubes
- Angles and L braces
- Panels and plates
- Rails and tracks
- Formed tubes and pipes
- Custom structural shapes
Small flexible roll formers produce short to medium production runs of parts used across many industries.
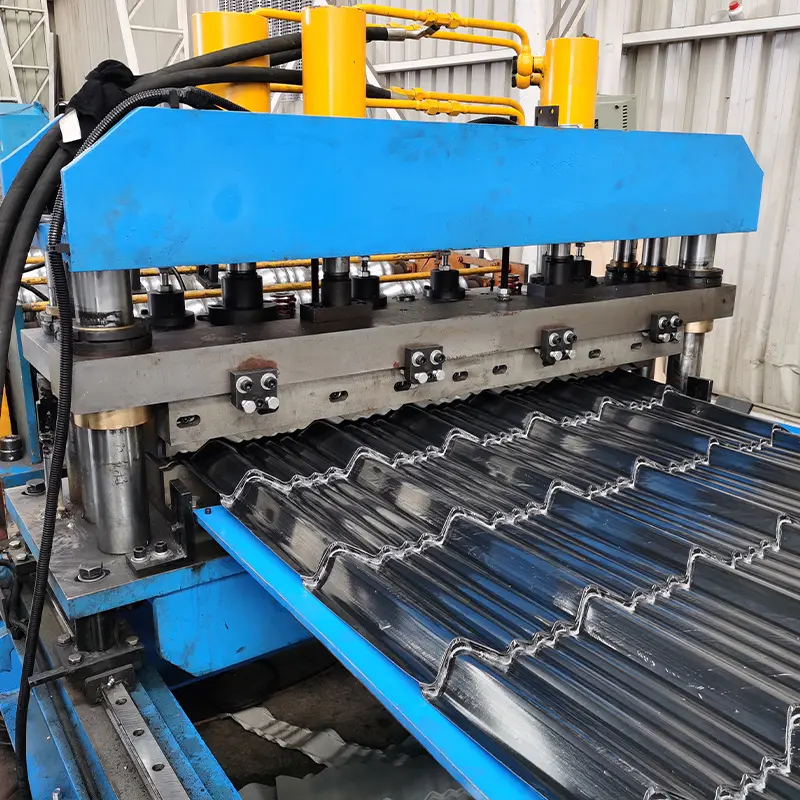
Choosing a Small Roll Forming Machine
Key considerations when selecting a small roll former:
Roll Former Selection Factors:
Parameter | বিস্তারিত |
---|---|
Production Volume | Size for expected output rate |
Part Sizes | Choose max width and length capability |
Material Type | Construction and tooling suits material used |
Part Complexity | Number of forming stands required |
Secondary Operations | Adding punching, cutting, bending stations |
Quick Change Tooling | Reduces changeover time |
Controls | Level of automation and data monitoring |
Safety Systems | Guards, safety circuits, e-stops |
Line Integration | Material handling and part flow |
Supplier Experience | Company expertise and support |
Operating Costs | Power, maintenance, consumable factors |
Analyzing the production application and specifications determines the type, size, and configuration of roll former required.
In-Line Roll Forming Machine Design
Standard in-line roll formers consist of entry and exit tables, forming stands, punching and cutting stations, part collection, and roll tooling:
In-Line Roll Former Components:
Station | Function |
---|---|
ডিকয়লার | Feeds strip into machine |
Entry Table | Aligns and guides strip |
Forming Stands | Incremental bending stations |
Punching/Notching | Secondary operations |
Shearing/Sawing | Cuts parts to length |
Exit Table | Collects finished parts |
Roll Tooling | Forms profile contour |
In-line roll formers produce parts up to 25 feet long at speeds around 10-45 feet per minute depending on the machine size. More forming stands allow more complex part shapes. Rotary and shuttle tables index shorter parts through the stands.
Rotary Table Roll Forming Machines
Rotary table roll formers arrange forming stands in a circle around a rotary table:
Rotary Table Roll Former Components:
Station | Function |
---|---|
Coil Reel | Holds strip coil |
Straightener | Removes coil curvature |
Feed Unit | Feeds strip into machine |
Rotary Table | Indexes part through stands |
Forming Stands | Incrementally form part |
Punch Press | Secondary operations |
Shear/Saw | Cuts parts to length |
Part Conveyor | Carries finished parts out |
Tooling | Forms profile contour |
The rotary table indexes the part through each station like the stations were in-line. Typical max part lengths are around 15 feet.
Roll Forming Tooling
Specially contoured roll tools form the sheet metal into the desired part profile:
Roll Forming Tooling:
- Made from machined steel or aluminum
- Upper and lower mating sets match part contour
- Quick change cassette designs for fast changeover
- Hardened surfaces for wear resistance
- Multiple sets for each profile and size
Roll tools must withstand high loads and speeds. Quick change cassettes utilize guide rails or cartridges to enable fast profile changeovers.
Accurate tool design and manufacturing is critical for producing quality roll formed parts. Roll tools require sharpening and repair over time from wear.
Secondary Processing Stations
Small roll formers can integrate secondary processing operations:
Secondary Processing Stations
Process | Description |
---|---|
Punching | Punches holes using flat or rotary press |
Notching | Cut outs notched sections |
Embossing | Forms raised or recessed shapes |
Bending | Hemming and angle bends |
Welding | Resistance seam and spot welding |
Hardware Insertion | Installs nuts, bolts, clips |
These additional operations are done in-line prior to cutting finished parts to length. They expand the range of part features that can be completed in one machine.
Cutting and Sawing Equipment
A cut-off station cuts the formed strip into individual parts:
Roll Former Cutting Methods:
Method | Description |
---|---|
Shearing | Guillotine shear cuts parts |
Circular Saw | Carbide saw blade cuts parts |
Abrasive Saw | Cut-off saw with abrasive disk |
Laser Cutting | CNC laser cuts profiles |
Shearing leaves a square cut edge but has higher force requirements. Saws produce curved edges but require blade maintenance. Lasers cut complex profiles without contact.
Cutting Station Considerations:
- Positioned after last forming stand
- Determines max part length capacity
- Adds slight taper to start/end of parts
- Scrap pieces can be automatically separated
Saws produce better cut edge quality while shears have higher force requirements. Cutting method affects part end finish and length accuracy.
Roll Former Drives and Controls
Key mechanical and electrical components:
Roll Former Drives and Controls:
System | Description |
---|---|
Main Drive | Powers the line with AC motor and gearbox |
Hydraulics | Used for cut-off press on some models |
PLC | Controls stations and automation |
HMI | Touchscreen interface for programming |
Sensors | Measure strip position and feed |
Safety Circuits | For e-stops, interlocks, compliance |
The PLC coordinates all machine movements and automation. The HMI allows operators to control the line and store job set ups.
Advanced controls enable quick changeovers between profiles and monitoring of machine performance.
Roll Former Line Integration
Roll formers can be integrated into automated production lines:
Line Integration Systems
- Coil handling equipment
- Feeder tables
- Conveyors and transfers
- Part collection tables
- Robotic material handling
- Part inspection systems
- Data monitoring software
- Packaging equipment
Automating the material flow increases throughput. Inspection checks part quality. Data systems track production. Robots can handle parts for secondary processing.
Roll Former Safety Equipment
Roll formers utilize a range of safety mechanisms:
Roll Former Safety Equipment:
Safety Item | Description |
---|---|
Guards | Encloses hazards areas |
Interlocks | Stops motion if opened |
E-Stops | Immediately stops all motion |
Safety Relays | Monitors status |
Safety Mats | Stops motion if stepped on |
Sensors | Detects operators in zones |
Brake Systems | Quickly stops hazardous motions |
Proper guarding eliminates contact with moving parts. E-stops, safety relays, and interlocks stop the machine if tripped. Other devices sense operator position and add redundant protection.
Small Roll Former Suppliers
There are many manufacturers of small roll forming equipment:
Small Roll Former Manufacturers:
প্রতিষ্ঠান | Location | Models |
---|---|---|
স্যামকো মেশিনারি | Toronto, Canada | In-line and rotary table up to 800mm wide |
Bradbury Group | Moundridge, USA | In-line machines up to 1000mm wide |
Formtek | Cleveland, USA | Rotary table and custom roll lines |
Brown Precision Tool | Utica, USA | Custom roll formers |
Comet Machines | Maharashtra, India | Standard and custom machines |
Botou Xianfa | Hebei, China | More basic rotary table and shuttle models |
Many builders offer standard platforms that can be customized for specific applications. Larger suppliers have decades of industry experience designing roll forming equipment.
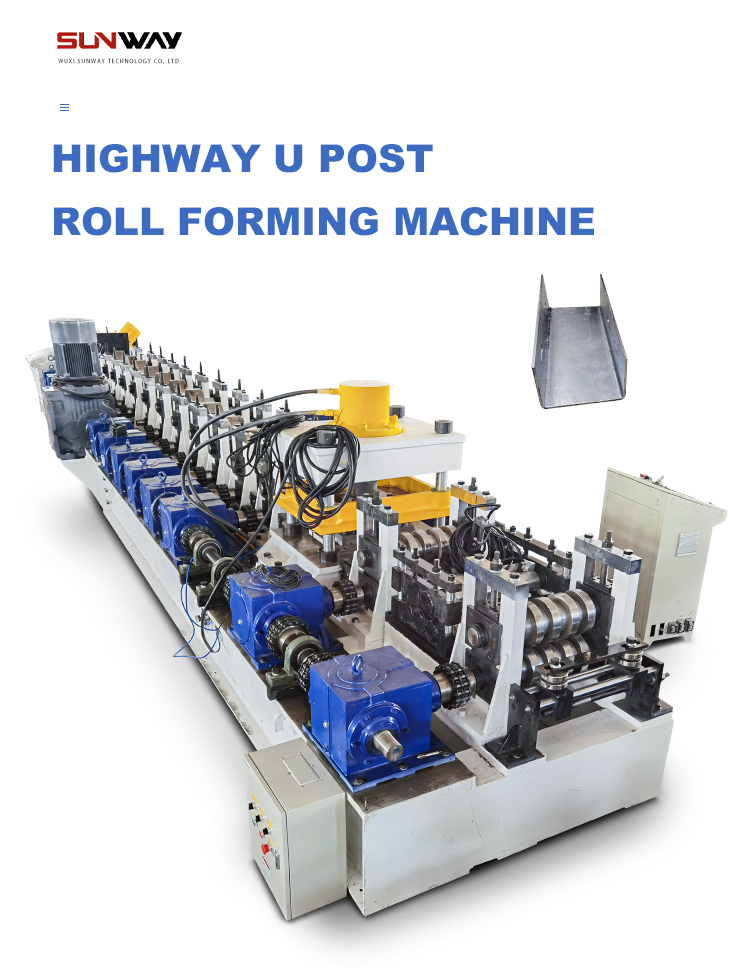
Buying Considerations for Roll Forming Machines
Key purchasing factors when investing in a small roll former:
Roll Former Buying Considerations
- Production volume requirements
- Available plant space and layout
- Part sizes, materials, and features
- Tooling design support offered
- Controls and automation level
- Safety systems and compliance
- Line integration options
- Shipping, installation, training
- Documentation and manuals
- Warranty and service support
- Ongoing maintenance and parts
Thoroughly analyzing the production goals and specifications allows proper selection of size, features, and options. Support for tooling design is also important.
Small Roll Former Costs
Like most metalworking machinery, roll former prices correlate to production capacity:
Small Roll Forming Machine Price Ranges:
Machine Type | Price Range |
---|---|
Basic Rotary Table | $50,000 – $150,000 |
Standard In-Line | $100,000 – $300,000 |
Customized Lines | $200,000 – $500,000 |
Costs vary based on:
- Width capacity
- Number of forming stands
- Level of automation
- Secondary processing capability
- Material handling integration
Larger and more automated lines with extra capabilities cost more. Simple rotary table models are most economical.
Other Roll Former Cost Factors:
- Tooling: $10,000 – $50,000 per profile
- Installation: $5,000 – $20,000
- Training: included – $5,000
- Shipping: $5,000 – $15,000
Tooling, shipping, installation, training, and service contracts can add significantly to initial purchase cost.
Operating Small Roll Forming Machines
Basic operation steps for roll formers:
Roll Former Operation Overview
- Stage material coil at unwind reel
- Thread strip through machine stations
- Install properly sized roll tooling
- Program job parameters at control panel
- Run sample part to test set up
- Adjust roll tools and settings as needed
- Launch production cycle
- Periodically inspect part quality
- When order complete, purge from line
- Remove roll tools to changeover
Key operation tasks:
- Careful set up of tooling and feeds
- Programming machine speeds, feeds, stops
- Qualifying first piece before run
- Monitoring production quality
- Changeovers for new profiles
Worker training and adherence to procedures is critical for quality roll formed parts.
Roll Former Maintenance
Regular maintenance activities:
Roll Former Maintenance Schedule
Task | Frequency |
---|---|
Inspect/tighten fittings, mounts | Daily |
Lubricate bearings, slides | Weekly |
Check belt tension and wear | Monthly |
Inspect electrical connections | 3 Months |
Hydraulic oil testing | 6 Months |
Gearbox oil change | Yearly |
Bearing replacement | 2-3 Years |
Full machine inspection | Yearly |
Roll tools require sharpening or replacement when wear reaches unacceptable levels.
Thorough maintenance procedures ensure maximum production uptime and part quality.
Roll Forming Safety Precautions
Key safety tips for roll former operation:
- Enclose the machine or restrict access with barriers
- Ensure proper guarding of all hazardous areas
- Make certain all safety circuits and devices function
- Follow lockout procedures during maintenance
- Use carts/conveyors to move heavy tooling
- Wear ear protection against machine noise
- Allow only trained personnel to operate
- Never reach into machine during operation
- Be cautious handling thin sharp strip stock
Roll formers contain many heavy parts moving at high speeds. Awareness of hazards and using proper safeguards prevents injuries.
Roll Forming Machine Troubleshooting
Common roll former issues and remedies:
Roll Former Troubleshooting
Problem | Possible Causes |
---|---|
Strip jamming | – Misaligned guides<br>- Worn/damaged tooling<br>- Strip lubrication issue |
Profile distortion | – Worn roll tools <br>- Improper roll adjustment |
Machine vibration | – Loose foundation |
Roll Former Troubleshooting (continued)
Problem | Possible Causes |
---|---|
Machine not starting | – Power supply issue<br>- Emergency stop engaged<br>- Faulty start switch |
Formed part defects | – Worn or damaged roll tools<br>- Incorrect roll tooling spacing<br>- Strip feed issue |
Excessive tooling wear | – Abrasive/thick material <br>- High machine speeds<br>- Infrequent lubrication |
Hydraulic leaks | – Damaged hoses/fittings<br>- Worn seals/gaskets |
Electrical failures | – Loose wiring connections<br>-Water ingress into cabinets<br>-Faulty components |
Excessive machine noise | – Worn bearings/gears<br>-Loose parts or guards<br>-Imbalanced drivetrain |
Troubleshooting roll formers requires methodically checking forming tools, strip feed, sensors, hydraulics, electrics, and controls until the root cause is identified.
Following preventive maintenance procedures minimizes machine downtime and defects.
Roll Formed Part Quality Checks
Inspecting produced parts verifies quality:
Roll Formed Part Inspection Checks
- Profile dimensions and tolerances
- Twist or bow defects
- Flange width and straightness
- Surface defects or scratches
- Corner and bend radii
- Cut edge condition
- Hole size, location, and finish
- Welds or hardware properly assembled
- Part length accuracy
- Material thickness consistency
Automated inspection systems can check critical dimensions. Workers also do visual and hand checks of samples.
Real-time monitoring allows early detection of issues before many bad parts are made.
Roll Forming Process Optimization
Methods for optimizing roll former production:
- Analyze downtime or slow cycles to identify bottlenecks
- Adjust strip feed speeds and forward strokes
- Check tooling wear and replace sooner if needed
- Improve quick changeover procedures between jobs
- Update tooling design for problem profiles
- Refine preventive maintenance plan and practices
- Add automation to improve material handling
- Provide training to workers on best practices
- Track key performance data to guide improvements
The best results come from a holistic focus on machine, tooling, personnel, quality control, and data-driven optimization.
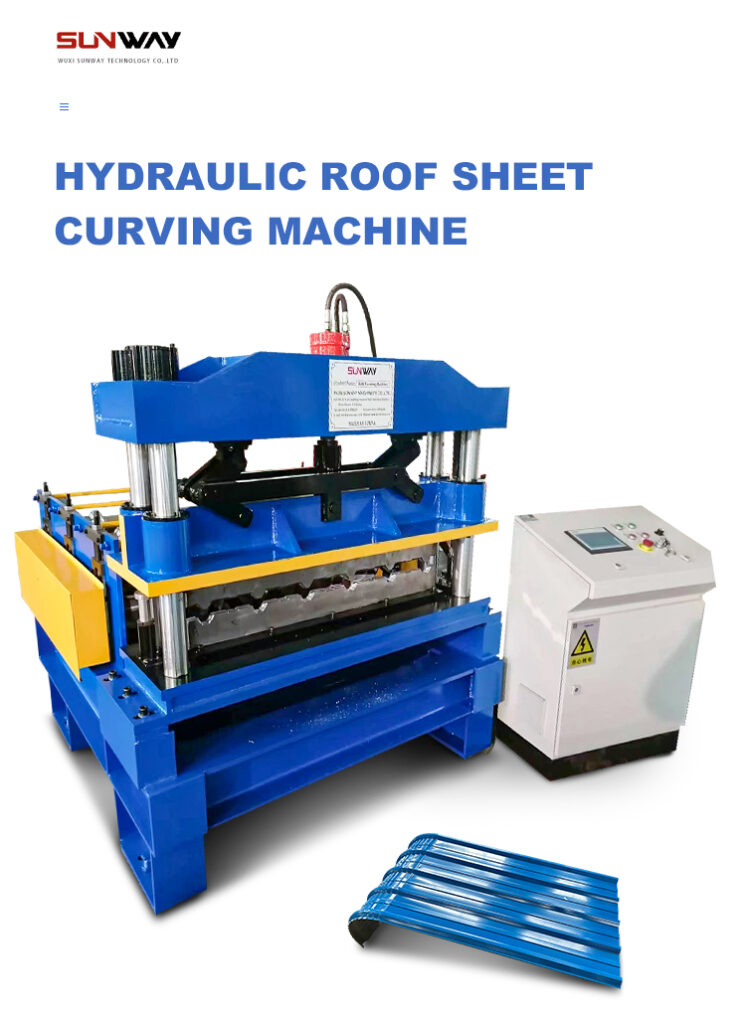
Roll Forming Industry Resources
Useful industry associations and resources:
- North American Steel Roll Forming Association: Standards, conferences, training programs
- European ROLLFORMING Association: European roll forming group
- Progressive Metalworking Magazine: Article archive on roll forming
- FAB Help: Roll forming questions forum
- The Tube & Pipe Journal: Publication on tube manufacturing
- Modern Metals: Magazine with roll forming articles
- The Roll Former: Rolling blog by Metform International
- Roll Forming Handbook: Reference book by David A. Smith
These organizations, publications, and references provide helpful information on roll forming processes, machinery, and best practices.
FAQ
Frequently asked questions about small roll forming machines:
Q: What thickness of sheet metal can small roll formers accommodate?
A: Most small roll forming machines can form sheet metal from 20 gauge (0.8 mm) down to around 26 gauge (0.5 mm). Maximum capacities depend on the machine power and roll tooling.
Q: How long does it take to set up a roll former for a new profile?
A: With quick change roll tooling cassettes, an experienced operator can complete a profile changeover in 30-90 minutes typically. The initial set up for a new profile takes longer.
Q: What motors and drives are used on small roll formers?
A: Typically AC induction motors in the 5-15 kW power range coupled to gearbox reducers. Servo motors allow more precise speed control.
Q: What controls are optimal for easy roll former operation?
A: Most modern machines use a central PLC with an HMI touchscreen interface. This allows flexible programming and data monitoring capabilities.
Q: How fast can small roll formers produce parts?
A: Production rates depend on part size and complexity, but around 10 – 50 feet per minute line speed is typical for small roll forming machines.
Q: What tolerances can roll forming hold on part dimensions?
A: Roll forming can achieve +/- 0.5 mm dimensional accuracy on profiles when machines and tools are properly set up.
Q: How long do roll forming machine tools last before needing replaced?
A: With proper use and maintenance, quality roll tooling can last 1-2 years before needing sharpened or replaced. Hardened tooling lasts longer.
Q: What safety precautions are important for roll formers?
A: Enclosing hazardous areas, e-stops, interlocked guarding, safety mats, and strict procedures are critical to protect operators. Lockout for maintenance.
Q: How are roll formed parts typically handled post production?
A: Conveyors, tables, or robots automatically move finished parts to inspection areas, packaging, or downstream processes.