Giriş
Bu material thickness in roll forming plays a crucial role in determining profile accuracy, machine settings, die design, and overall production efficiency. Choosing the right material thickness ensures optimal forming performance, minimal defects, and extended machine life.
But how do you select the right thickness for roll forming applications? What are the best practices for adjusting machine settings based on material thickness?
In this guide, we’ll explore:
✅ How material thickness impacts roll forming
✅ Recommended thickness ranges for different metals
✅ How to adjust roll forming machines for different thicknesses
✅ Common problems caused by incorrect material thickness
✅ How to optimize roll forming for thin and thick materials
Let’s dive into the critical role of material thickness in roll forming and how to optimize your production for maximum efficiency in 2025!
How Material Thickness Affects Roll Forming
Material thickness directly influences forming force, bending behavior, die design, and energy consumption in roll forming machines. Below are the key effects of material thickness on roll forming:
1. Bending & Spring-Back Behavior
- Thicker materials gerektirir higher forming force and are less flexible, leading to less spring-back.
- Thinner materials experience more spring-back, requiring additional roller passes for accuracy.
2. Machine Load & Roller Wear
- Thicker metals increase roller pressure, leading to higher wear and tear on dies.
- Proper lubrication is crucial for maintaining roller longevity when forming thick materials.
3. Profile Accuracy & Edge Quality
- Thin materials are more sensitive to roller misalignment, leading to edge waviness or distortions.
- Thicker materials gerektirir precise roller clearance settings önlemek için over-bending or cracking.
4. Energy & Speed Adjustments
- Thicker materials require slower forming speeds önlemek için excessive stress and cracking.
- Thinner materials can be formed at higher speeds, but require tighter control over roller pressure.
Profesyonel ipucu: Correct material thickness selection can improve forming accuracy by up to 30%!
Recommended Material Thickness Ranges for Roll Forming
Different metals have unique forming properties, requiring specific thickness ranges for optimal performance. Below is a comparison of recommended material thicknesses for different metals.
Malzeme Türü | Recommended Thickness Range (mm) | En İyi Uygulamalar |
---|---|---|
Hafif Çelik | 0.3mm – 6.0mm | Structural components, roofing sheets |
Paslanmaz Çelik | 0.5mm – 3.0mm | Automotive, aerospace, medical equipment |
Alüminyum | 0.3mm – 5.0mm | Lightweight structures, HVAC, enclosures |
Galvanizli Çelik | 0.4mm – 4.0mm | Corrosion-resistant frames, construction materials |
Copper & Brass | 0.2mm – 2.5mm | Electrical components, decorative trim |
Profesyonel ipucu: Stainless steel requires tighter roller tolerances due to its higher strength and tendency to spring back!
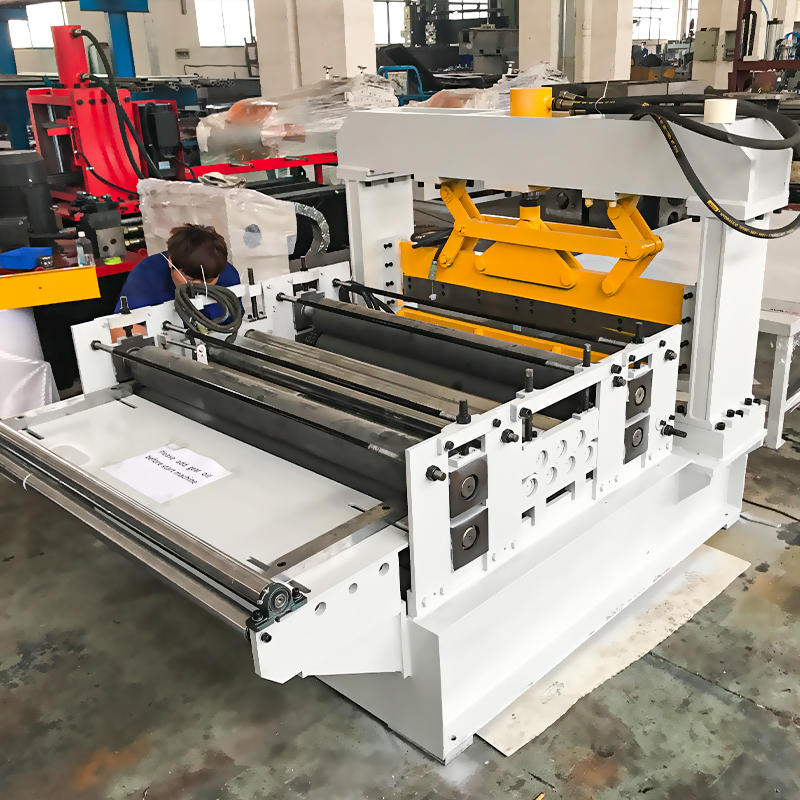
How to Adjust Roll Forming Machines for Different Thicknesses
To ensure optimal roll forming performance, machines must be adjusted based on material thickness. Below are the key machine settings that must be optimized:
1. Roller Clearance Adjustment
✅ Ensure rollers match material thickness önlemek için over-bending or under-forming.
✅ Use adjustable roller stands to fine-tune clearance settings for each thickness.
2. Forming Pressure & Speed Control
✅ Thicker materials require lower forming speeds önlemek için cracking and excessive force buildup.
✅ Thinner materials need precise pressure control önlemek için wrinkles and distortions.
3. Die Design & Pass Configuration
✅ More gradual forming passes are needed for thicker materials to avoid stress concentration.
✅ Thinner materials require additional support rollers önlemek için buckling.
4. Lubrication & Cooling Adjustments
✅ Higher thickness requires increased lubrication to reduce friction and prevent roller wear.
✅ Cooling systems help manage heat buildup when forming thicker metals at slow speeds.
Profesyonel ipucu: Proper machine adjustments for material thickness can extend roller lifespan by 40%!
Common Roll Forming Problems Caused by Incorrect Material Thickness
Incorrect material thickness can lead to production defects, machine wear, and increased scrap rates. Aşağıdakiler common roll forming problems and their solutions.
Problem | Neden | Çözüm |
---|---|---|
Edge Cracking | Forming pressure too high for material thickness | Reduce forming pressure, use more forming passes |
Spring-Back Issues | Thin materials bending beyond tolerance | Adjust roller clearance, add extra support rollers |
Surface Wrinkling | Insufficient support for thin materials | Increase roller contact, adjust forming speed |
Excessive Roller Wear | Thick material generating too much friction | Increase lubrication, use hardened steel rollers |
Incorrect Profile Dimensions | Material too thick or too thin for machine settings | Adjust roller clearance, recalibrate forming passes |
Profesyonel ipucu: 80% of roll forming defects are caused by incorrect material thickness adjustments!
Best Practices for Roll Forming Thick & Thin Materials
Different strategies must be used when roll forming thin and thick materials için optimize forming accuracy and reduce defects.
Roll Forming Thin Materials (0.2mm – 2.5mm)
✅ Use additional support rollers to prevent material buckling.
✅ Increase forming speed, but control forming pressure to prevent distortions.
✅ Apply light lubrication için reduce friction without excessive buildup.
Roll Forming Thick Materials (3.0mm – 6.0mm+)
✅ Use gradual bending angles önlemek için stress concentration and cracking.
✅ Reduce forming speed to allow material to flow smoothly without excessive force.
✅ Apply heavy-duty lubrication için minimize roller wear and heat buildup.
Profesyonel ipucu: Thicker materials require more forming passes to avoid excessive stress buildup!
Advanced Strategies for Optimizing Roll Forming Based on Material Thickness
To maximize efficiency, reduce defects, and ensure high-quality production, manufacturers must implement advanced techniques for handling different material thicknesses. Below are the most effective strategies to improve roll forming performance based on material thickness.
1. Adaptive Roller Design for Different Thicknesses
- Adjustable roller stands allow quick thickness modifications without downtime.
- Multi-stage rollers ensure smooth transitions between forming passes, preventing stress buildup.
- Dynamic roller pressure control optimizes bending accuracy for both thin and thick materials.
2. AI-Powered Thickness Monitoring
- AI-driven sensors continuously measure material thickness in real-time.
- Automatically adjusts roller pressure, forming speed, and die clearance for optimal performance.
- Yardımcı olur detect material inconsistencies early, reducing scrap rates.
3. High-Precision CNC Die Fabrication
- Computer-controlled die manufacturing ensures tight tolerances for different material thicknesses.
- Azaltır human error and improves forming repeatability.
- Şunlar için izin verir quick die changeovers, improving production efficiency.
Profesyonel ipucu: AI-powered thickness monitoring can reduce material waste by up to 25%!
How to Optimize Roll Forming Speed Based on Material Thickness
Bu forming speed must be adjusted based on material thickness önlemek için cracking, distortion, or roller wear. Below is a comparison of optimal forming speeds for different thickness levels.
Malzeme Kalınlığı | Recommended Forming Speed (m/min) | Key Adjustments |
---|---|---|
0.2mm – 1.0mm (Thin Sheet Metal) | 20 – 60 m/min | High-speed forming, reduce roller pressure |
1.0mm – 3.0mm (Medium Thickness) | 10 – 30 m/min | Balanced speed, controlled roller clearance |
3.0mm – 6.0mm (Thick Steel) | 5 – 15 m/min | Slow speed, increased lubrication |
6.0mm+ (Heavy Gauge Steel) | 2 – 10 m/min | Maximum roller pressure, gradual forming passes |
Profesyonel ipucu: Thinner materials can be formed at higher speeds, but require precise roller control to avoid defects!
How to Reduce Material Waste in Roll Forming Based on Thickness
Material waste increases production costs and reduces efficiency. Below are strategies to minimize scrap rates and improve yield based on material thickness.
1. Optimize Roller Gap & Alignment
✅ Ensure roller clearance matches material thickness önlemek için profile distortions.
✅ Use calibrated alignment tools to maintain consistent forming accuracy.
2. Implement Smart Lubrication Systems
✅ Thicker materials require more lubrication to reduce friction and prevent roller wear.
✅ Thin materials need precise lubrication control to avoid excess buildup and contamination.
3. Use CNC Precision Cutting for Accurate Length Control
✅ CNC-controlled cutting systems ensure exact profile lengths.
✅ Reduces material overuse and scrap production.
Profesyonel ipucu: Optimizing roller alignment can reduce material waste by up to 20%!
Common Roll Forming Challenges with Thick & Thin Materials
Handling different material thicknesses can pose various challenges. Aşağıdakiler common problems and their solutions.
Problem | Neden | Çözüm |
---|---|---|
Cracking in Thick Materials | Excessive forming pressure | Use gradual bending angles, reduce pressure |
Wrinkling in Thin Materials | Insufficient roller support | Increase roller contact, optimize forming speed |
Excessive Spring-Back | High-strength materials bending beyond tolerance | Adjust roller clearance, use more forming passes |
Edge Distortion | Makara yanlış hizalaması | Recalibrate rollers, optimize forming pressure |
Roller Wear on Thick Materials | High friction & poor lubrication | Use hardened rollers, apply precision lubrication |
Profesyonel ipucu: 80% of forming defects are caused by incorrect machine adjustments—regular calibration is key!
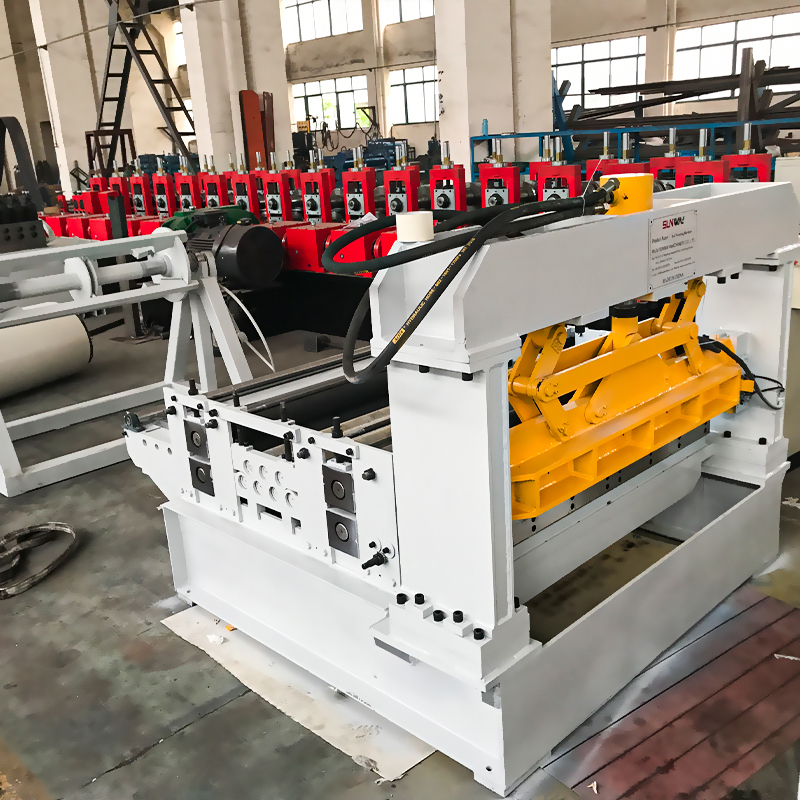
Best Practices for Roll Forming Machines Handling Multiple Thicknesses
To efficiently process materials of varying thicknesses, follow these best practices:
1. Use Variable Roller Pressure Systems
✅ Adjust roller force dynamically based on material thickness.
✅ Prevents over-compression for thin materials and under-forming for thick metals.
2. Implement Quick-Change Tooling Systems
✅ Use modular die designs to switch between thicknesses without excessive downtime.
✅ Reduces production delays and increases efficiency.
3. Invest in Adaptive Forming Technology
✅ AI-driven forming systems automatically adjust roller clearance, speed, and pressure.
✅ Ensures consistent forming quality across different thicknesses.
4. Maintain Proper Cooling & Lubrication Control
✅ Thicker materials generate more heat, requiring advanced cooling systems.
✅ Thin materials need controlled lubrication önlemek için surface contamination.
Profesyonel ipucu: Adaptive forming technology can improve production speed by up to 30%!
FAQ: Roll Forming Material Thickness & Machine Optimization
1. What is the thickest material that can be roll formed?
- Most roll forming machines can handle up to 6.0mm thick steel, while specialized machines can form materials up to 10mm thick.
2. How do I prevent material cracking when forming thick steel?
- Kullanım gradual bending angles, optimize forming pressure, and ensure proper lubrication.
3. What adjustments should I make when switching from thin to thick materials?
- Adjust roller clearance, forming pressureve speed settings based on thickness.
- Kullanım modular tooling for quick adjustments.
4. Why do thin materials wrinkle during roll forming?
- Wrinkling occurs when support rollers are insufficient. Increase roller contact points to stabilize material flow.
5. Where can I buy roll forming machines that support multiple material thicknesses?
İçin özel yapim rulo şeki̇llendi̇rme maki̇neleri̇, visit WUXI SUNWAY MAKİNA A.Ş., LTD.
Son Düşünceler
Doğru seçimi yapmak material thickness is essential for high-precision, defect-free roll forming. By optimizing machine settings, using proper lubrication, and adjusting forming passes, manufacturers can reduce defects, improve production efficiency, and extend machine life.
WUXI SUNWAY MAKİNA A.Ş., LTD bir lider küresel üretici . özel yapim rulo şeki̇llendi̇rme maki̇neleri̇, teklif advanced technology, expert support, and competitive pricing.
Want to optimize your roll forming process? Contact us today!