Steel gas tube cold roll forming machines are industrial equipment used for bending and forming steel strips into hollow tube sections for gas conduction applications. These machines are highly customizable and fully automated to produce steel gas tubes in various sizes and profiles efficiently.
This comprehensive guide will provide a detailed overview of steel gas tube cold roll forming machinery covering:
Overview of Steel Gas Tube Cold Roll Forming Machines
Steel gas tube cold roll forming machines form steel strips into round, square, or rectangular hollow tubes using a series of progressively arranged rollers.
Key features:
- Highly automated, precision forming
- Customizable for various tube sizes and profiles
- Efficient and cost-effective tube production
- Suitable for mass production applications
- Forms tubes with excellent surface finish and dimensional accuracy
- Reduce material waste compared to other forming processes
Main Components:
Component | Function |
---|---|
Uncoiler | Feeds raw steel coil strip |
Feeder | Controls strip feed speed |
Forming stations | Progressively bend strip into tubular shape |
Welding machine | Welds formed tube longitudinally |
Cutoff device | Cuts formed tubes to length |
Control system | Controls and automates the process |
Working Principle:
The steel strip from the coil is fed into the machine at a constant speed. It passes through a series of forming rollers that gradually bend it into the desired tubular shape. The joining edges are then welded together longitudinally to form a closed section tube. The formed tube is cut to the required length by cutoff dies. The whole process is automated by the control system.
Main Benefits:
- High production efficiency and speeds
- Low operational costs
- Minimum material waste
- Consistent product quality
- Lower energy consumption
- Simple design and ease of use
- Low maintenance requirements

Types of Steel Gas Tube Cold Roll Forming Machines
Machine Type | Description |
---|---|
Vertical | Roller stations arranged in a vertical inline configuration |
Horizontal | Rollers stations in horizontal configuration |
Rotary | Tube formed by rotating strip around fixed mandrel |
Spiral | Helical forming stations to produce spiral welded tubes |
Vertical Steel Gas Tube Cold Roll Forming Machine
- Inline vertical forming stations
- Floor space efficient design
- Ideal for long length tubes
- Limited size and section variations
Horizontal Steel Gas Tube Cold Roll Forming Machine
- Forming stations arranged horizontally
- Larger size range capabilities
- Wider product variations possible
- Requires more floor space
Rotary Steel Gas Tube Cold Roll Forming Machine
- Strip wrapped around fixed mandrel
- Compact installation, flexible production
- Fast production speeds
- Limited to round tubes
Spiral Steel Gas Tube Cold Roll Forming Machine
- Helical forming stations
- High production speeds
- Suitable for submerged arc welding
- Limited size range
Key Specifications
पैरामीटर | Range |
---|---|
Tube sizes | 10 – 250 mm |
मोटाई | 0.3 – 3 mm |
Forming speed | 10 – 40 m/min |
Production capacity | 10 – 120 tubes/min |
Main drive power | 3 – 55 kW |
Overall dimensions | 10x3x3 – 50x8x6 m |
Machine weight | 2000 – 20000 kg |
Applications of Steel Gas Tube Cold Roll Forming Machine
Steel gas tubes from these machines find uses in:
- Gas pipelines for distribution
- Structural sections for constructions
- Mechanical and automotive parts
- Furniture and storage systems
- Agricultural, fencing, and sports sectors
Choosing a Suitable Steel Gas Tube Cold Roll Forming Machine
Consider the following when selecting a suitable steel gas tube cold roll forming machine:
Tube specifications: Size, section profile, length, thickness, dimensional accuracy
Production requirements: Output rate, line speed, automation level
Space constraints: Floor area available for installation
Power requirements: Main drive motor capacity and power source
Raw material: Steel coil strip properties and availability
Budget: Investment costs, operational costs
Production scale: Low, medium or high volume needs
Product variations: Range of tube sizes and sections needed
Future expansion scope: Potential increase in output or product range
Supplier reputation and support: Machine warranty, after-sales service
Leading Steel Gas Tube Cold Roll Forming Machine Manufacturers
कंपनी | Location |
---|---|
ABS Industries | इटली |
Gasparini | इटली |
Formtek | UK |
Hangzhou Roll Forming Machinery | China |
Lebranc | China |
LT Industries | भारत |
Metform | Turkey |
सैमको मशीनरी | China |
Jinan Paxtec | China |
Cost Analysis and Pricing Range
Equipment Cost:
- Small machine: $35,000 to $60,000
- Medium machine: $60,000 to $150,000
- Large machine: $150,000 to $300,000
- Additional charges for customization
Operational Costs:
- Labor: 1-2 operators
- Power consumption: up to 20 kW
- Maintenance: approx. 2% of machine cost
Tube Price Range:
- Small sections: $2 – $4 per meter
- Medium sections: $4 – $8 per meter
- Large sections: $8 – $12 per meter
- Prices vary based on order quantity and specifications
Key Considerations for Steel Gas Tube Cold Roll Forming Machine Selection
- Determine tube size range, dimensions, profiles required
- Production output rate in meters/minute
- Level of automation and precision needed
- Available space for machine installation
- Power supply and utilities available
- Estimated annual operating hours
- Coil strip properties and availability
- Options for edge welding and tube cutting
- Budget constraints for equipment purchase
- After-sales support from the supplier
- Possibilities for future upgrades or expansion
Comparing the pros and cons, capacity, features, and prices of different machine models will help select the optimal cold roll forming line.
Installing a Steel Gas Tube Cold Roll Forming Machine
Proper installation is key for optimum performance of a steel gas tube cold roll forming machine:
Site preparations:
- Level concrete or steel foundation
- Sufficient space around the machine
- Proper lighting and ventilation
- Power and utility supply arrangements
Receiving inspection:
- Check machine parts against packing list
- Look for any damage during transportation
Positioning:
- Use crane or forklifts to place machine at prepared location
- Anchor machine properly to foundation
Levelling and alignment:
- Level forming sections and rollers precisely
- Align machine components and drives
- Verify parallelism of rollers
Connections:
- Connect hydraulic, pneumatic, lubrication, and electrical supply lines
- Install safety guarding around moving parts
Trial runs:
- Set up machine without load as dry test
- Check working motions and interlocks
- Confirm designed forming operations
How to Operate a Steel Gas Tube Cold Roll Forming Machine
Pre-checks:
- Inspect raw material coil dimensions and quality
- Verify lubrication levels on all moving components
- Examine all machine parts for wear or damage
- Ensure all safety guards are in place
Startup:
- Switch on main power supply to control panel
- Activate hydraulic power pack and lube oil pump
- Jog machine drive to check direction of rotation
- Set line speed, tube length, and other parameters
Operation:
- Fix coil reel on uncoiler mandrel
- Feed strip through leveler/straightener
- Thread strip through forming sections
- Adjust hold-down rolls for stable feeding
- Start automatic running at set speed
- Monitor tube forming process and quality
- Inspect welded tubes
- Stack finished tubes by overhead crane
Shutdown:
- Stop the line by pushing emergency stop button
- Switch off hydraulic power pack and main motor
- Clean machine by removing metal scrap and dust
- Lubricate all moving parts as per schedule
Safety:
- Wear protective gloves, goggles, and helmet
- Keep hands away from running machinery
- Ensure proper machine guarding is in place
- Follow standard safety procedures at all times
Maintenance Tips for Steel Gas Tube Cold Roll Forming Machines
- Clean machine daily to prevent dust buildup
- Lubricate bearing, gears, chains as per manual
- Check hydraulic oil and top up if needed
- Monitor wear on forming rollers and guides
- Verify pneumatic system for air leakages
- Examine welder condition and electrode wear
- Confirm tightness of all bolts, fasteners, couplings
- Check electrical wiring and control circuits for issues
- Verify machine alignment and roller parallelism
- Repair or replace any damaged or worn out components
- Schedule preventive maintenance during plant shutdowns
- Keep maintenance records for analysis and improvements
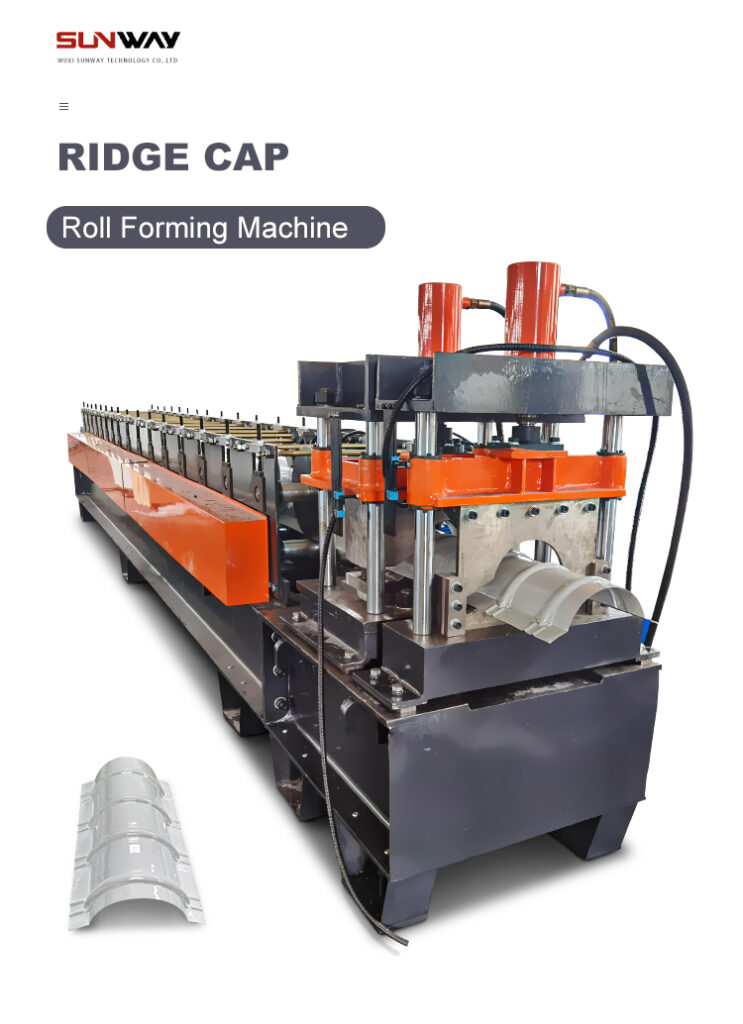
Steel Gas Tube Cold Roll Forming Machine Troubleshooting
Issue | Possible Causes | Corrective Actions |
---|---|---|
Strip slippage | Worn gripper rolls, low friction | Replace gripper rolls, improve lubrication |
Uneven strip movement | Misaligned forming sections | Realign machine properly, level foundation |
Strip tears during forming | Worn/damaged forming rolls | Repair or replace forming rolls |
Dimension errors in tubes | Incorrect roller adjustment | Re-set rollers to design gap settings |
Bad tube welds | Improper weld settings, worn welder | Adjust welder parameters, replace welder tips |
Tube shape defects | Misaligned forming stations | Realign forming sections, verify parallelism |
Excessive machine vibration | Loose parts, unbalanced rotation | Tighten loose parts, balance rotating parts |
Control malfunctions | Electrical faults, sensor issues | Check wiring, replace faulty components |
Careful troubleshooting and maintenance helps maximize uptime and extend service life of the machine.
How to Choose a Steel Gas Tube Cold Roll Forming Machine Manufacturer
When choosing a steel gas tube cold roll forming machine manufacturer, check for:
- Industry experience and reputation
- Range of machine capacities offered
- Technological expertise and innovation
- Quality focus and process maturity
- Customization and modification capabilities
- Reasonable pricing and shipment lead times
- Responsiveness to technical queries
- Own manufacturing facilities
- Quality control and testing procedures
- After-sales service and spare parts supply
- Installation, training and documentation support
- Local presence and global footprint
Selecting an established manufacturer with proven know-how, quality focus and good after-sales support reduces project risk and ensures long-term equipment performance.
Steel Gas Tube Cold Roll Forming Machines: Pros vs Cons
Advantages:
- High production speeds and output rates
- Excellent dimensional precision and tube finish
- Minimal material wastage
- Low operating costs
- Automated and efficient process
- Flexible production capabilities
- Compact equipment size
Limitations:
- High initial purchase cost
- Complex design and customization
- Require skilled maintenance and operation
- Limited tube shape and profile options
- Restricted raw material properties
Frequently Asked Questions
Q: What materials can be used for steel gas tube production?
A: Low carbon steels, HSLA steels, galvanized and stainless steels of suitable properties can be roll formed into gas tubes.
Q: What is the typical tolerance on tube dimensions?
A: Dimensional accuracy within ±0.5 mm can be achieved for tube diameters and ±1 mm on tube length.
Q: What is the maximum length of tubes produced?
A: Standard lengths up to 12 meters can be produced. Extended lengths possible with customized machines.
Q: Are square and rectangular tube sections possible?
A: Yes, square, rectangular, and oval tubes are possible with customized tooling.
Q: What safety measures are required?
A: Safety guarding, emergency stops, operator training, protective gear, and safe working practices are essential.
Q: How are the tube ends prepared after cutting?
A: Tube ends are deburred and beveled to enable proper fittings and welding.
Q: What is the typical production rate?
A: Production rate ranges from 10-120 tubes per minute based on machine capacity.
Q: How to determine correct machine capacity for production needs?
A: Consider current and future tube requirements, production volumes, line speed, and shifts per day. Oversize machine by 20% for flexibility.
Q: What maintenance is required?
A: Daily cleaning, lubrication, periodic roll replacement, hydraulic system care, electrics and wiring checks are key.
Q: What is the typical machine lifetime?
A: Properly maintained machines will deliver over 15 years of reliable production.