Siding roll forming machines are used to create various profiles of sidings from coil strips of metal. They form the flat metal coils into custom shapes through a series of rollers that bend and fold the material. Siding roll formers produce roofing panels, wall panels, decking, fencing and various architectural claddings.
Overview of Siding Roll Forming Machines
Siding roll forming machines are an efficient way to form metal coil into custom siding profiles for various applications. Here is an overview of siding roll formers:
What are Siding Roll Forming Machines?
- Siding roll forming machines continuously form metal coil strips into desired siding panel shapes through a series of rollers.
- The process cold forms the material through a progressive die without heat or welding.
- Rollers bend and fold the strip into custom profiles like roofing panels, wall sidings, decking etc.
- Siding roll formers can process various metals like steel, aluminum, copper, zinc into different architectural shapes.
How Do Siding Roll Forming Machines Work?
- Coiled sheet metal is fed into the roll former at one end.
- The strip passes through a series of roll stations that progressively bend the material.
- Upper and lower rollers apply pressure to form the strip into the custom profile.
- Cutoff knives slice the formed strip into required lengths as per the application.
- Formed siding sheets are collected at the other end for downstream processes.
Benefits of Siding Roll Forming
- Highly efficient continuous process with low labor requirement.
- Consistent quality and dimensional accuracy of formed parts.
- Flexibility to create customized profiles easily.
- Lower tooling cost compared to sheet metal fabrication.
- Minimal material waste due to roll forming process.
- Applicable to high production volumes and long part lengths.
Limitations of Siding Roll Formers
- Higher machine cost compared to other methods.
- Limited to profiles with mostly 90 degree bends.
- Not suitable for small batch or prototype production.
- Roll changeover required for new profiles affecting downtime.
- Potential for scratches or marks on surface from rolls.
Typical Capabilities of Siding Roll Machines
- Sheet width up to 1500 mm
- Material thickness from 0.3 to 3 mm
- Forming speed around 10-15 m/min
- Tensile strength up to 550 MPa
- Hardness up to 450 HV
- Roll changing time within 2 hours
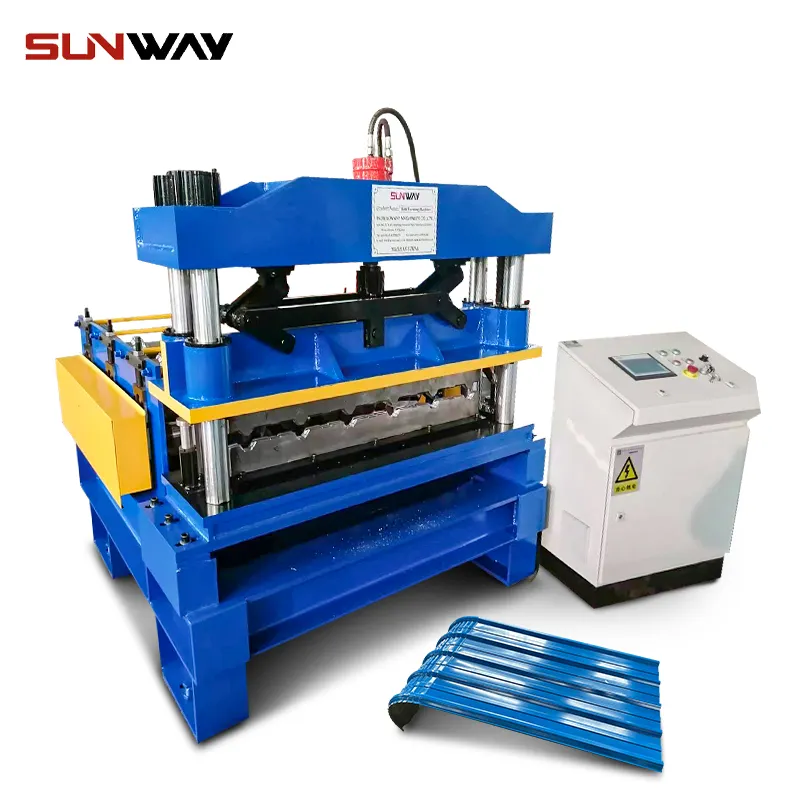
साइडिंग रोल बनाने की मशीन के प्रकार
There are several types of siding roll formers used for different applications and production volumes:
Portable Siding Roll Formers
- Lightweight, compact and mobile roll formers.
- Used at construction sites for on-site fabrication.
- Limited in speed and complexity of profiles.
- Low production around 10-30 units per hour.
- Manual operation and material handling.
Standard Siding Roll Forming Lines
- Complete production lines with uncoiler, roll former, cutter.
- For medium production volumes.
- Speeds up to 45 m/min.
- Automated material flow and controls.
- Quick roll changing ability.
High-Speed Siding Roll Forming Machines
- Heavy-duty roll formers for high production rates.
- Speeds exceeding 100 m/min possible.
- Servo motor-driven, high-precision machines.
- Automated production monitoring and control.
- Complex profiling possible.
Customized Siding Roll Forming Systems
- Tailor-made roll former and material handling solutions.
- Integrated with other processes like punching, welding.
- For specialized high-volume needs.
- Particular profile, size, speed and automation requirements.
Examples of Common Siding Profiles
- Trapezoidal sheets for roofing and wall cladding.
- Corrugated metal panels.
- Standing seam roof panels.
- Various architectural facade panels.
- Steel decking sheets.
- Fencing, railing and balcony balustrades.
Main Components of Siding Roll Forming Machines
Siding roll forming machines consist of several components that work together to shape the material:
Coil Handling Equipment
- Uncoiler hold the coil strip and feeds into roll former.
- Brake applies tension and corrects coil line curvature.
- Guide keeps strip alignment at entry.
Roll Forming Stations
- Series of top and bottom roll sets that bend metal.
- Rolls mounted on gearbox shafts linked to main drive.
- Number of stands as per profile complexity.
Forming Dies and Rolls
- Rolls machined with contours matching desired profile.
- Quick die change design for flexible production.
- Rolls available in various materials like steel, rubber, urethane.
Cutoff Unit
- Flying cutoff shear to slice formed panels at length.
- Servo motor-driven for speed and accuracy.
- Conveyor table to collect cut sheets.
नियंत्रण प्रणाली
- PLC automates production monitoring and control.
- HMI touchscreen for machine interface and programming.
- Sensors for measuring sheet length, tooling protection.
Safety Equipment
- Safety barriers, access interlocks for operator protection.
- Emergency stop buttons to halt machine motion.
Siding Materials Used in Roll Forming
Siding roll forming machines can process various metal materials including:
Aluminum
- Lightweight panels for walls, fascia, soffits.
- Finishes like natural, pre-painted, anodized.
- Alloys 5xxx and 6xxx series commonly rolled.
Galvanized Steel
- Zinc coated sheets resist corrosion.
- Used for roofing, walls, fencing.
- G90, G60, AZ50 zinc coating grades.
Cold Rolled Steel
- Carbon steel strips without heat treatment.
- Painted afterward for color finishes.
- Applications in decking, cladding, roofing.
Stainless Steel
- Profiled stainless sheets for decorative facades.
- Finishes like mirror, embossed, colored.
- Grades 304, 316 commonly roll formed.
Copper
- Architectural copper panels for aesthetics.
- Natural patina look surface.
- Also brass, zinc strip can be roll formed.
Siding Roll Forming Process Explained
The siding roll forming process continuously forms metal coil strip into custom profiles through a series of graduated forming stations:
Decoiling
- Coil loaded on a powered unwind mandrel.
- Strip fed into roll former through an alignment guide.
- Constant tension applied by a brake system.
Graduated Bending
- Sheet passes through sequential roll stands.
- Top and bottom rolls apply pressure in steps.
- Strip gradually formed into shape through 90 degree bends.
Calibration and Finishing
- Final roll stations fine-tune profile dimensions.
- Surface finishing rolls can also be included.
Cutting
- Formed strip cut at specified length by rotating knives.
- Servo motors allow high-speed and precision cutting.
Collection
- Conveyor tables collect freshly cut parts.
- Offline processes like hole punching done if needed.
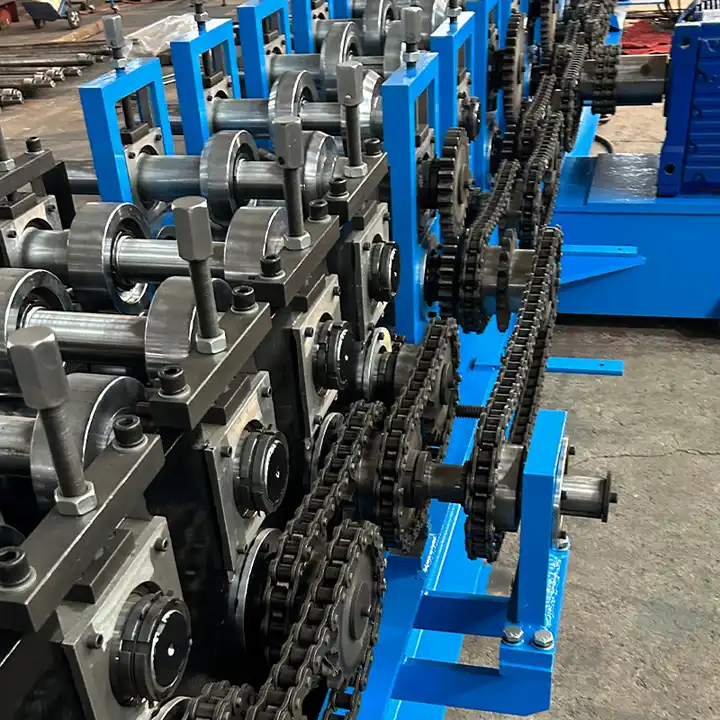
Features of Siding Roll Forming Machines
Modern siding roll forming machines offer various features and capabilities:
Quick Die Change Design
- Modular tooling for fast die changeover.
- Enables frequent profile variations.
- Reduces machine downtime.
Robust and Rigid Construction
- Heavy-duty mill duty frames withstand high loads.
- Precision machined components for roll alignment.
- Vibration dampening bases for smooth operation.
Pre-punching Integration
- Built-in punching before roll forming allows holes in the final product.
- Eliminates secondary punching operation.
Automatic Dimensional Check
- Laser or optical systems to check critical dimensions.
- Real-time feedback for quality assurance.
- Controls to adjust process parameters if needed.
Remote Access Mobile Control
- Smart remote monitoring of production data.
- Parameter changes can be made from mobile devices.
- Improves operational efficiency.
Automated Material Handling
- Coil loading/unloading, part stacking by robots or manipulators.
- Reduces manual handling requirements.
Applications and Uses of Siding Roll Forming
Siding roll forming machines are used across residential, commercial and industrial applications:
Metal Roofing
- Trapezoidal, corrugated, standing seam roofing.
- Commercial, industrial, agricultural roof cladding.
Wall Paneling
- Interior and exterior architectural cladding.
- Decorative metallic wall coverings.
Architectural Facades
- Geometric facade designs made from metal.
- Provides unique visual appearance.
Steel Decking
- Fluted decking sheets for floor slabs.
- Composite floor deck construction.
Railing and Fencing
- Balustrades, balcony railings, gates.
- Decorative or security fence panels.
Silo and Tank Construction
- Cylindrical wall cladding for silos, gas tanks.
- Conical reducer profiles.
Scaffold Planks
- Formed steel planks used in scaffolding.
- Replace traditional wooden scaffold boards.
Electronic Enclosures
- Metal sheets for electronics housings.
- Provides EMI/RFI shielding.
How to Choose Siding Roll Forming Equipment
Selecting optimal siding roll forming machinery depends on factors like production needs, product variation, and budgets:
Intended Production Volume
Higher volumes demand heavier and faster machines like high-speed roll formers. Lower quantities suit smaller portable or standard roll lines.
Range of Siding Profiles Needed
More profile variations require quick changeover ability and flexible tooling. Standard machines can handle simpler profiles.
Level of Process Automation
Automated material flow and handling improves efficiency but costs more. Manual processes are suitable for low budget applications with less complexity.
Available Space
Larger roll forming lines need more floor space. Consider space constraints for layouts, infeed/outfeed, coil storage etc.
Production Speed Targets
High volumes need high speed capability of over 100m/min. Most standard lines operate between 10-45m/min for normal outputs.
Quality and Precision Requirements
Applications needing tight tolerances demand advanced machines with automatic gauging and feedback control. Standard machines can suffice for regular architectural cladding.
Cost Factors for Siding Roll Forming Equipment
Siding roll former cost depends on:
- Number of roll stands – more stands for complex profiles
- Type of material handling
- Production speed and precision requirements
- Level of automation like auto coil loading etc.
- Additional secondary operations – punching, marking, packaging
- Brand and manufacturing scale – made-to-order vs mass produced
Here are some typical price ranges:
उपकरण | Price Range |
---|---|
Portable Manual Roll Former | $8,000 – $15,000 |
Standard Roll Forming Line | $50,000 – $150,000 |
High-Speed Roll Forming System | $200,000 – $750,000 |
Custom Roll Forming Solution | Application Specific |
Pros and Cons of Siding Roll Forming
Pros | Cons |
---|---|
Highly efficient continuous production | Relatively high machine cost |
Consistent dimensional accuracy | Limited to mostly 90 degree bend profiles |
Minimal material waste | Roll changing downtime for new profiles |
Flexibility for design profiles | Potential for surface defects |
Lower cost than fabricating | Not ideal for small batch or prototype runs |
Applicable for high volumes | Requires skilled specialists for complex programming |
Automated process needs little labor | Significant initial investment |
Siding Roll Forming Machine Suppliers
There are many siding roll former manufacturers globally. Here are some of the major suppliers:
China
- Foshan YSD Roll Forming Machinery
- Botou Xianfa Roll Forming Machine Factory
- Jiangsu New Hongyuan Roll Forming Machinery
Taiwan
- Fonmac Rollforming Machinery
- bailemachinery Machine Manufacture Co.
- Honor Seiki Co
भारत
- Anant Engineering Works
- Sree Balaji Engineering Works
- Ajanta Manufacturing Limited
United States
- New Tech Machinery
- Roll Form Group
- Metform International
Turkey
- Murat Machine
- Erkstil
- Burmaksan Makina
Buying Considerations for Siding Roll Forming Equipment
Here are some factors to evaluate when selecting siding roll forming machinery suppliers:
Technical Expertise
- Experience producing the types of profiles you need
- Capability for special features like pre-punching
- Knowledge to program complex profiles
Customization Ability
- Flexibility to customize the line and tooling
- Integration of additional processes like punching, stamping
Quality and Performance
- Consistent and high production speeds
- Dimensional accuracy of formed parts
- Use of quality components like gearboxes, motors, controls
Reputation and Reliability
- Proven track record delivering similar projects
- Strong client references and testimonials
- Professional and responsive customer service
Value for Money
- Competitive pricing for robust and high-performance equipment
- Good quality to cost ratio
Siding Roll Forming Machine Maintenance
Proper maintenance is key to optimum performance and reliability of siding roll forming systems:
Daily Maintenance
- Clean machine, clear dirt and debris especially from tooling
- Check oil levels on gearboxes, lubricate moving parts
- Verify hydraulic pressure and fluid levels
- Inspect all safety devices are functional
Periodic Maintenance
- Roll tooling inspection and realignment if needed
- Fastener tightening on guards, connections, roll shafts
- Lubricate chains, bearings, slides, actuators
- Clean filters on hydraulics, coolant and air systems
Predictive Maintenance
- Vibration monitoring for early failure detection
- Thermal imaging to check overheating issues
- Regular oil analysis on gearboxes and hydraulics
Preventative Maintenance
- Scheduled replacement of wear parts like seals, belts, hoses
- Planned roll changes, alignment and refurbishment
- Software updates and control system health checks
Proactive maintenance and operator training helps maximize uptime and extend service life.
Siding Roll Forming Machine Operation
Correctly operating siding roll forming equipment is vital for safety and optimal performance:
Safety
- Allow only trained operators to run the machine
- Ensure proper safeguards and barriers are in place
- Staff must wear applicable PPE like safety goggles, gloves
- No loose clothing, jewelry or long hair near moving parts
Startup Sequence
- Turn on main power and control power supply
- Start hydraulic pumps and check oil pressure
- Jog machine to verify correct motion direction
- Set operating speed and trial run uncoiled material
Loading Coils
- Use proper equipment to load heavy coils safely
- Ensure strip end is straight before feeding into the machine
- Set the tension brake appropriately
Monitoring
- Observe strip flow through the rolls during operation
- Check for defects or markings on formed parts
- Monitor produced length counters and line speed
Parameter Adjustments
- Make measured and incremental adjustments to machine settings
- Modify parameters like speed, strip feed, roll pressure, etc.
Shutdown
- Stop the line safely when production is complete
- Clean the machine and tooling thoroughly
- Inspect equipment condition and log any observations
Proper operating techniques maximize output while preventing damage.
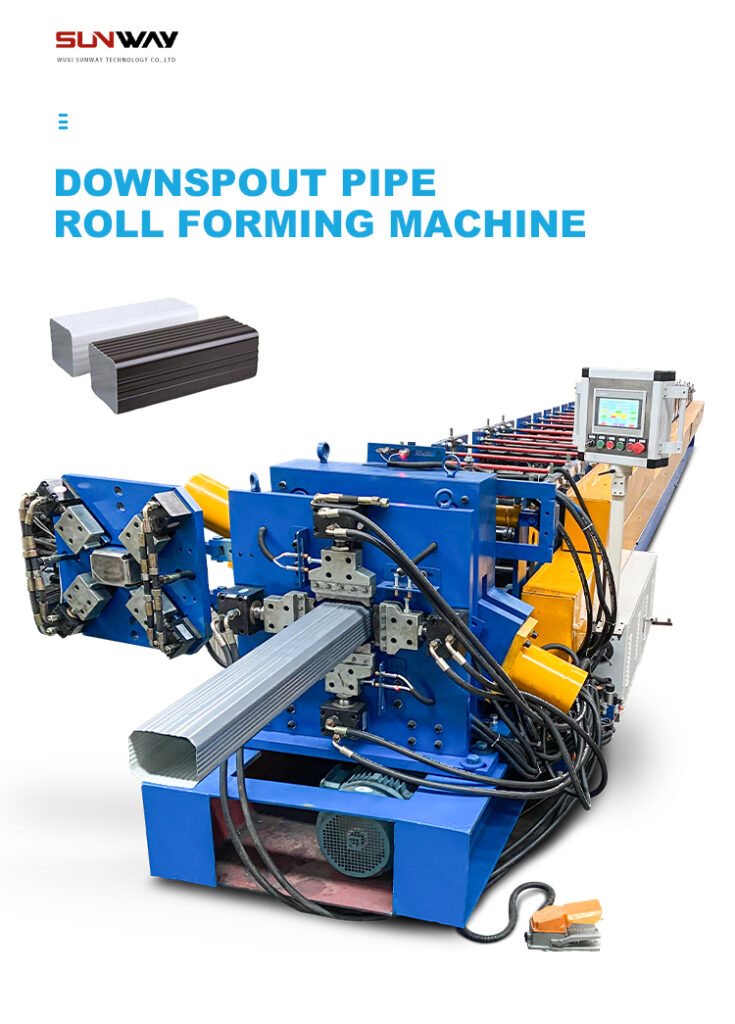
Troubleshooting Common Siding Roll Forming Problems
Issue | Possible Causes | Corrective Actions |
---|---|---|
Inconsistent profile dimensions | Worn or damaged tooling Misaligned rollers Improper machine settings | Inspect, realign or replace tooling Reset machine parameters Recalibrate sensors and controls |
Scrap pieces due to incorrect cut lengths | Encoder slippage Worn cutoff blades Control calibration error | Check encoder, realign if needed Replace worn blades Recalibrate length controls |
Scratches or marks on formed panels | Debris buildup on rolls Damaged roll surface Insufficient lubrication | Clean rollers and remove chips Refinish or replace damaged rolls Increase lubricant flow rate |
Excessive strip curl at entry | Improper coil curvature Inadequate tension brake | Straighten coil prior to loading Adjust brake tension settings |
Overheating gearboxes | Low oil level Misaligned bearings Worn gears | Top up gearbox oil Realign shafts, bearings Inspect and replace gears if needed |
Hydraulic system pressure or flow loss | Dirty filters Leaking fittings/hoses Pump issue | Clean or replace filters Tighten connections, replace hoses Inspect pump, couplings and motors |
Proper troubleshooting methodology helps identify root causes and prevent prolonged downtime.
Siding Roll Forming Machine Safety
Working safely is crucial when operating powerful roll forming equipment:
- Restrict access for only trained personnel
- Ensure guards are in place around moving parts
- Follow lockout/tagout procedures during maintenance
- Keep work area clean and free of obstructions
- Do not wear loose clothing, gloves, jewelry near the equipment
- Use proper lifting equipment for handling heavy tooling or coils
- Ensure electrical boxes and wiring are sealed and contained
- Have clearly marked emergency stops at accessible locations
- Install safety mats and barriers around the infeed/outfeed areas
- Provide sufficient lighting around the work zones
- Follow safe coil loading/unloading procedures
- Implement a hearing protection program for high noise areas
- Conduct regular safety inspections and risk assessments
- Provide specialized operator training on machine hazards
- Encourage reporting of unsafe conditions and near-misses
- Document safety procedures and responsibilities clearly
- Investigate all incidents to prevent recurrence
- Ensure personnel follow safety rules at all times
Siding roll forming equipment is essential for efficiently producing metal siding panels and profiles. With proper machine selection, operation, maintenance and safety practices, manufacturers can maximize their investment in these systems while keeping workers secure. Careful planning and management of the roll forming process leads to improved quality, productivity and profitability.