Roll forming is a metal working process in which sheet metal is progressively formed into a desired cross-sectional profile through a series of consecutive bending operations. Roll forming machines are used to create uniform, high-precision metal parts with complex cross-sections at high speeds.
Cheap roll forming machines provide an affordable option for small to medium factories and workshops to adopt roll forming technology without costly investments. This guide covers everything you need to know about cheap roll formers from types, working principles, key components, specifications, applications, installation, operation and maintenance.
Overview of Cheap Roll Forming Machines
Roll forming machines can be expensive, with advanced industrial models costing upwards of $500,000. However, various manufacturers offer budget roll forming machines in the range of $10,000 to $50,000 targeting small and medium enterprises.
While these cheap roll formers have limitations on maximum rolling width, thickness, speed and precision compared to premium models, they offer an economical solution for low to medium volume production. They are ideal for small workshops and factories looking to adopt roll forming in-house for the first time.
Cheap roll forming machines use the same working principles and processes as industrial roll formers. The key difference is in build quality, precision, durability and automation features. However, with proper operation and maintenance, cheap roll formers can deliver quality parts for small batch manufacturing.
Key Benefits of Cheap Roll Formers
- Low capital investment – Allows small businesses to adopt roll forming without high cost
- Versatility – Ability to create varied custom profiles with quick rolling die changeovers
- High productivity – Forming is a continuous operation with high outputs
- Material savings – Low material wastage compared to other processes
- Simple operation – Easy to operate after minimal training
- Compact size – Small footprint suitable for tight spaces
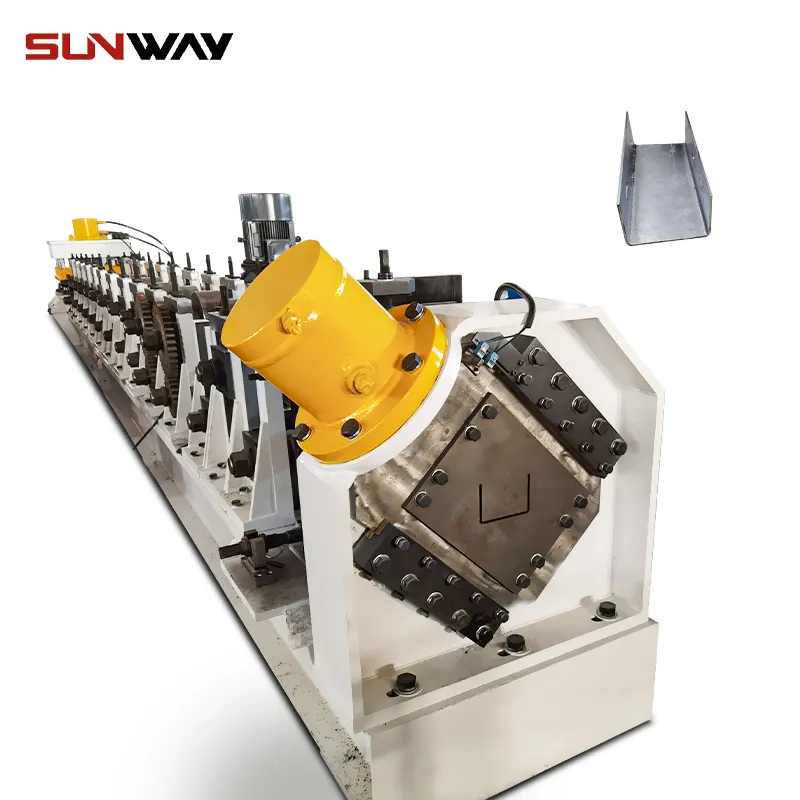
Types of Cheap Roll Forming Machines
There are two main types of cheap roll forming machines:
Manual Roll Forming Machines
As the name suggests, manual roll formers involve manual feeding and part offloading. An operator has to feed the sheet metal coil into the machine and collect formed parts from the other end. These are the most basic and affordable roll forming machines.
Features:
- Entry-level pricing from $10,000
- Smaller footprint
- Simpler mechanical design
- Manual controls for basic operations
- Lower production rates
Limitations:
- Labour intensive operation
- Inconsistent feeding affects output
- Higher risk of safety incidents
- Frequent operator intervention required
Semi-Automatic Roll Forming Machines
Semi-automatic roll formers automate the material feeding process but still require manual offloading of formed parts. These represent a good middle-ground offering faster production with lower labour.
Features:
- Pricing from $15,000 to $50,000
- Automated coil loading and feeding
- Touchscreen controls for programming
- Higher output of up to 10 m/min
- Reduced labour requirements
Limitations:
- Still batch style production
- Part offloading is manual
- Size limits on coil payoff and formed parts
- Limited programming flexibility
Working Principle of Roll Forming Machines
The working principle involves gradually bending the sheet metal strip through consecutive sets of rollers until the desired cross-section is formed.
The key processes are:
- Sheet metal coil is loaded into a payoff reel
- The strip is fed into the forming section
- Forming rollers progressively bend the strip
- Cutting blades shear finished parts to length
- Formed parts are offloaded manually or automatically
The longitudinal bending happens gradually as the material passes through each roller station. The rolling dies apply precise bending force to incrementally form the profile.
Correct roller design along with precise gap spacing between top and bottom rollers is crucial for profile accuracy. The rollers can create a wide range of geometries like C & U channels, angles, square and rectangular tubes etc.
Key Components of Roll Forming Machines
Cheap roll forming machines have simplified designs but include these key components:
Coil Payoff: Holds the sheet coil and feeds strip into the rollers through a decoiler
Forming Section: Consists of several roller stations for bending the metal into profile
Roller Stations: Each station has a top and bottom roller for incremental bending
Rolling Dies: Shaped dies mounted on the rollers to form the profile
Cutting Unit: Shears the finished parts to desired length after forming
Controller: Controls machine speeds and operations. Can be basic or touchscreen.
Frame: Provides a rigid platform and mounts for components
Drives: Electric motors and gearboxes driving the rolling shaft
Specifications of Cheap Roll Formers
Here are typical specifications of cheap roll formers:
Specification | Capability Range |
---|---|
Maximum Rolling Width | 800-1500 mm |
Minimum Rolling Thickness | 0.3-0.5 mm |
Maximum Rolling Thickness | 1.5-2 mm |
Rolling Speed | 6-10 m/min |
Maximum Coil Weight | 1-3 tons |
Maximum Part Length | 3-6 meters |
Rolling Accuracy | ±1 mm over 3 m length |
बिजली की आपूर्ति | 220V/380V, 3 Phase |
Motor Power | 3-7.5 kW |
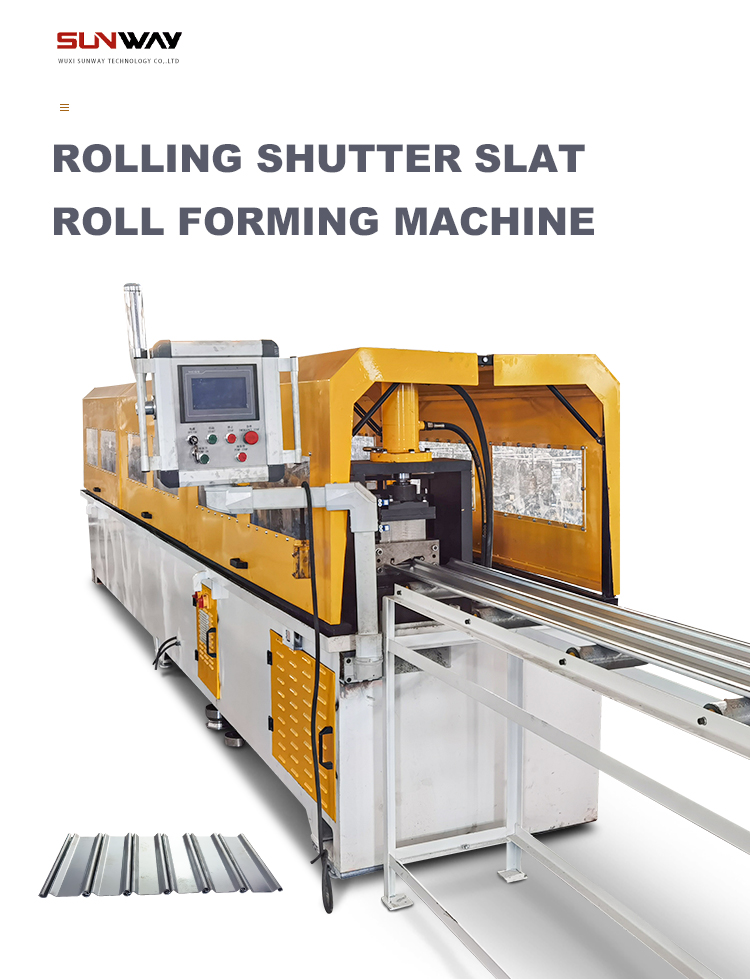
Applications and Suitable Industries
Cheap roll forming machines are suitable for producing metal parts up to 10 tons per month including:
- Solar panel frames – C & U channels
- Roofing and siding – Standing seam and other specialty profiles
- Structural sections – Angles, tubes, open channels
- Furniture tubing – Square and rectangular tubes
- Agricultural parts – Corrugated and trapezoidal sheet metal
- Automotive components – Brackets, small chassis parts
- HVAC parts – Heat exchanger fins, ventilation ducts
Suitable industries include:
- Small job shops
- Furniture and appliance manufacturing
- Solar equipment manufacturers
- HVAC contractors
- Agricultural equipment OEMs
- Custom metal fabricators
- Automotive aftermarket suppliers
Installation and Handling of Roll Forming Machines
Proper installation is key to achieving high forming quality and output from cheap roll formers. Here are some guidelines:
- Install on a flat leveled concrete floor for stability
- Bolt down the machine securely to prevent movement
- Leave adequate space around for loading coils and unloading parts
- Level roller shafts properly and eliminate any skew
- Position electrical panels for easy access
- Provide sufficient power supply, at least 20% over requirement
- Arrange coil payoffmand formed part exit for efficient workflow
- Ensure machine is easily accessible for operation and maintenance
The machine and components should be handled carefully during transportation and installation using lifting straps, avoiding knocks or damage. Engage experienced riggers and technicians for installation.
Operation of Cheap Roll Forming Machines
While cheaper roll formers are designed for easy operation, proper worker training is still essential. Key operating steps include:
1. Preparation
- Check electricals, mechanisms, lubrication and alignments
- Program machine settings and speeds
- Stage sheet coil, slitting machine, part catcher
2. Loading coil
- Bring coil to payoff using coil car
- Mount coil on mandrel ensuring tight fit
- Feed strip end through machine
3. Initial setup
- Adjust decoiler tension and angle for smooth payout
- Set cutting blade gap for clean shearing
- Jog machine and check formed profile without load
- Establish stable rolling speed
4. Production
- Run machine in automatic mode monitoring operation
- Periodically check profile accuracy with gauges
- Adjust feeding tension and speed if issues arise
- Oil and clean forming rollers as needed
- Offload finished parts from exit end
5. Coil changeover
- Prepare next coil while existing runs out
- Stop machine when coil is exhausted
- Remove depleted coil from payoff
- Mount next coil and thread strip into machine
- Restart rolling after resetting tensions
6. Shut down
- Stop machine when production completed
- Clean machine and clear any scrap
- Turn off electricals and perform visual inspection
- Address any issues for next production run
Maintenance of Cheap Roll Forming Machines
Regular preventive maintenance is key to prolong the productivity of cheap roll forming machines. Key maintenance activities include:
Daily:
- Clean rollers, clear scrap and keep area tidy
- Check alignment of shafts, gears, rollers
- Lubricate bearings, shafts, gears as needed
- Monitor noise or temperature rise of motors
Weekly:
- Inspect electrical, hydraulic and pneumatic systems
- Check machine foundation bolts for tightness
- Verify cutting blade sharpness and gap
- Monitor wear on bearing housings, seals
- Test emergency stop button functioning
Monthly:
- Thorough clean inside cabinets, conduits
- Check belt tension, vibrations and pulley alignment
- Inspect rollers for wear and parallelism
- Test all machine safety interlocks and sensors
- Verify electrical contactor, breaker condition
- Check hydraulic system leaks if applicable
Yearly:
- Complete inspection of all parts, structures
- Schedule preventive maintenance from OEM
- Replace any severely worn components
- Calibrate sensors, controllers and instruments
- Update machine software/firmware if needed
Regular maintenance as per above schedule and OEM guidelines will minimize unplanned downtime and keep overall TCO low.
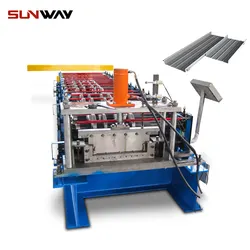
How to Choose a Cheap Roll Forming Machine Supplier
When selecting a supplier for cheap roll forming machines, consider these factors:
Product Quality
- Use proven designs for robust performance
- Quality components – motors, bearings, hydraulics
- Precision machined parts and alignments
- Good track record and client reviews
अनुकूलन
- Flexibility to customize for profiles
- Quick turnaround on design changes
- Experience with varied applications
- Easy programming and set up
Services
- Installation, commissioning support
- Operator training provided
- Maintenance contracts offered
- Local presence for prompt service
Pricing
- Clear breakdown of pricing
- Reasonable spare parts rates
- CAM software tools included
- Shipping, taxes, duties handled
Reliability
- Quick response to issues
- Sufficient regional inventory of spares
- Established supply chain for components
- Financial stability of supplier
Choosing the right supplier can help maximize the value and return on investing in cheap roll forming machines.
Pros and Cons of Cheap Roll Forming Machines
Pros
- Low capital investment cost
- Quick set up and changeovers
- Simple operation and maintenance
- Compact footprint suitable for small shops
- Ability to create varied custom profiles
- Higher throughput than other processes
- Reduced material waste versus cutting or stamping
Cons
- Limited thickness and width capacity
- Lower maximum rolling speeds
- Reduced precision and accuracy
- Frequent manual adjustment required
- Higher skill needed for complex profiles
- Not ideal for very high volume production
- After-sales support may be inadequate
Cost Analysis of Cheap Roll Forming Machines
Here is an overview of the typical cost factors for cheap roll forming machines:
Pricing Range:
- Manual machines: $10,000 to $30,000
- Semi-automatic machines: $20,000 to $50,000
Key Price Drivers:
- Maximum rolling width capacity
- Level of automation
- Maximum rolling speed
- Type of motor and drives
- Overall build quality and durability
Typical Base Pricing:
- Manual 1000 mm machine: $15,000
- Semi-auto 1300 mm machine: $35,000
Additional Cost Items:
- Design of rolling dies: $2,000
- Shipping and taxes: 10-15%
- Installation and commissioning: $2,000
- Training: $1,500
- Spare parts kit: $2,000
Total Cost of Ownership:
- Machine cost
- Operating costs – labour, power, maintenance
- Cost per piece produced
- Overall ROI
Cheap roll forming machines allow even small workshops to adopt roll forming at reasonable upfront investment. When operated optimally, they offer low cost per piece and rapid ROI.
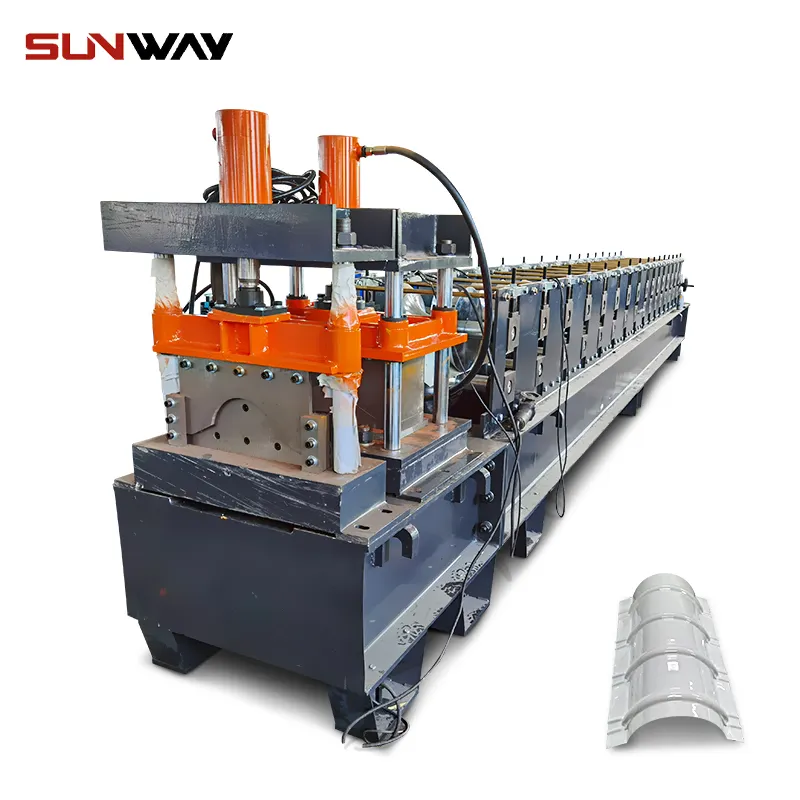
FAQs
Q: What thickness of sheet metal can cheap roll forming machines handle?
A: Cheap roll formers can typically process sheet metal from 0.3 mm to 2 mm thickness. Maximum thickness capacity depends on machine rating.
Q: Are cheap roll forming machines easy to operate?
A: Cheap roll formers are designed for easy operation with manual controls or touchscreen programming. Quick die changeovers facilitate profile adjustments. Workers require 1-2 weeks training to become proficient.
Q: What safety precautions are important for roll forming?
A: Key safety aspects are – enclose danger areas, use safety interlocks, ensure proper electrical grounding, provide operator training, implement lockout/tagout, supply personal protective equipment.
Q: How quick is the ROI when using cheap roll forming machines?
A: Depending on volumes, the typical ROI period for cheap roll formers is 9-15 months. Optimizing production planning, operations and minimizing downtime is key to rapid payback.
Q: What regular maintenance is critical for roll formers?
A: Vital maintenance includes lubricating rollers, inspecting alignments, checking electrical and hydraulics, cleaning scrap, monitoring wear on bearings, pulleys, blades. This prevents unplanned outages.
Q: What design support is required for custom profiles?
A: The supplier’s engineering team can provide profile design services based on product drawings. CAD software creates roller layouts and die profiles for precision forming.
Q: What factors affect productivity of roll forming lines?
A: Key factors are consistent material feeding, forming accuracy, line speed optimization, reliable part discharge, minimized coil changeover time, preventive maintenance and skilled operators.
Q: How does roll forming compare to other metal forming processes?
A: Roll forming offers higher production rates versus pressing or stamping. It has lower tooling costs than stamping and provides superior quality compared to brake forming. Material savings are higher over cutting or machining.
Q: What are some innovations in roll forming technology?
A: Recent innovations include inline process monitoring, quick die change systems, servo-motor driven rolls, advanced software for simulation and control, variable speed lines, and integration of secondary operations.