Machines de fabrication de rails de guidage pour ascenseurs sont utilisés pour produire les rails de guidage utilisés dans les systèmes d'ascenseurs. Les rails de guidage servent à guider avec précision la cabine d'ascenseur vers le haut et vers le bas du puits.
Machine à fabriquer des rails de guidage pour ascenseurs Détails clés
- Type d'équipement : Machine à former des rouleaux
- Matériaux : Bobines d'acier
- Méthodes de formage : Formage par laminage
- Sorties : Rails métalliques formés
- Applications industrielles : Systèmes d'ascenseurs, systèmes de manutention
Rail de guidage pour ascenseurs Fabrication de machines de guidage
Type | Description |
---|---|
Machine de formage de rouleaux | Forme en continu des bobines de métal en profils de rail personnalisés en pliant progressivement la tôle à travers une série de matrices à rouleaux. |
Dérouleur | Alimentation de la bande de métal en bobine dans la profileuse |
Ciseaux de pré-coupe | Découpe les tôles à la largeur de bobine voulue avant le formage |
Bancs de laminage | Stations successives avec matrices à rouleaux pour le pliage incrémentiel de bandes métalliques |
Ciseaux de post-coupe | Coupe des rails formés aux longueurs requises |
Équipement de soutien | Contrôle PLC, hydraulique, boîtes de vitesses, instruments |
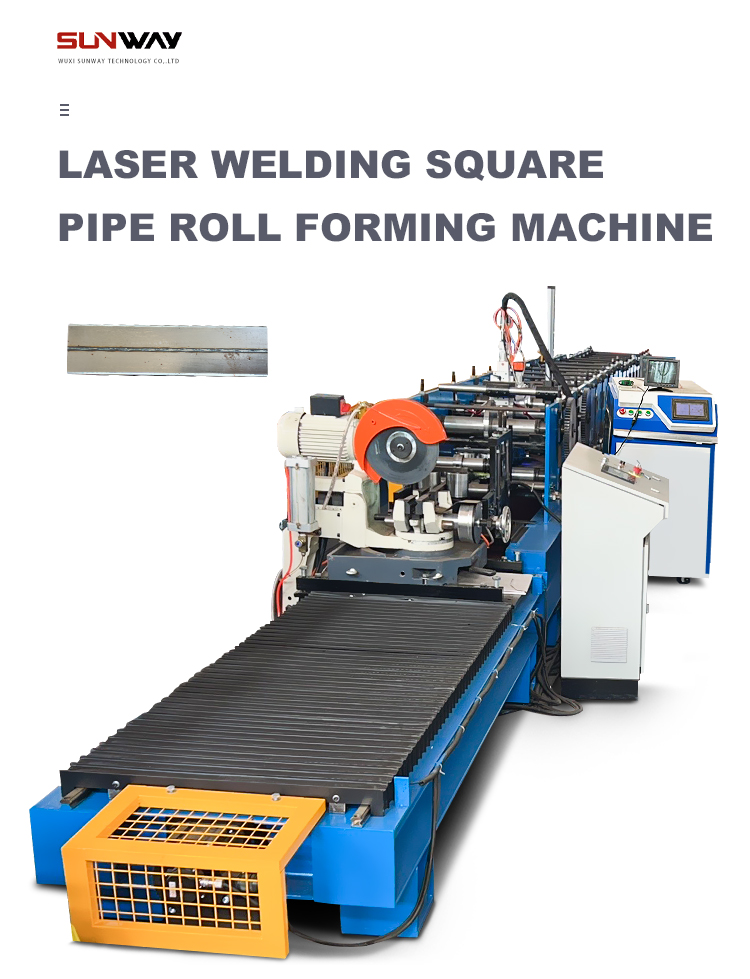
Processus de fabrication de la machine à fabriquer des rails de guidage pour ascenseurs
La Machine à fabriquer des rails de guidage pour ascenseurs fonctionne selon le processus de formage par laminage. La matière première utilisée est une bobine d'acier chargée sur un dérouleur. La bobine passe par des cisailles de prédécoupage où elle est coupée à la largeur spécifiée pour le profil du rail.
La bande de métal découpée passe ensuite dans des matrices à rouleaux successives montées sur des supports de formage. Chaque jeu de rouleaux plie progressivement la tôle pour former graduellement la configuration de rail souhaitée.
Le profil de rail entièrement formé sort de la dernière rangée de rouleaux et est coupé aux longueurs souhaitées par les cisailles de post-formage. Les rails coupés finis sont rassemblés sur les tables de sortie.
Paramètres
Paramètres | Détails |
---|---|
Matériau | Bobines d'acier à faible teneur en carbone, d'acier inoxydable et d'acier galvanisé |
Épaisseur | 1-3 mm en général |
Largeur | 50-100 mm en général |
Longueur | Jusqu'à 6000 mm |
Vitesse | 10-15 m/min |
Tolérances | +/- 0,02 mm |
Finition de la surface | <0,5 microns |
Alimentation en matériaux
- Le dérouleur peut accueillir jusqu'à 5 tonnes de bobines
- Dérouleur équipé de rouleaux d'alimentation de précision
- La largeur est coupée par des cisailles prédécoupées avant le formage.
- La bobine est introduite en continu et à vitesse constante dans les cages de formage à rouleaux.
Formage de profilés
- Formé progressivement par un ensemble de rouleaux qui plient la feuille par incréments
- 6-8 supports de formage réglables avec rouleaux interchangeables
- Les rouleaux ont des rainures usinées pour donner une forme au profil.
- Rouleaux inférieurs actionnés par des motoréducteurs et des entraînements
- Rouleaux supérieurs libres et réglables par vérin hydraulique
Conception du profil
- Le logiciel de conception du passage du rouleau calcule la géométrie correcte de la rainure du rouleau
- La simulation du passage du rouleau valide la forme à travers les stands de formage
- Conception optimisée pour le type de matériau et la configuration souhaitée du rail
- Rouleaux usinés CNC en acier D2 pour la dureté et la durabilité
Longueur Tranchage
- Réalisé par une robuste machine de découpe postformage
- Un couteau robuste avec des lames trempées cisaille les rails formés.
- Mesure de la longueur par codeur rotatif de précision
- Tolérance de longueur +/- 0,5 mm
- Gamme de longueurs 500 mm à 6000 mm
Personnalisation
- Rouleaux de formage conçus et produits pour des dimensions de rail personnalisées
- Le changement de rouleau en 24 heures permet un prototypage rapide
- La simulation de profil permet de valider la forme du rail avant l'usinage des rouleaux
- Soutien au développement de produits pour des applications uniques
Fournisseurs et fourchette de prix
Fabricant | Localisation | Fourchette de prix |
---|---|---|
Machine Mfg Ltd | Chine | $100,000 – $150,000 |
Formmasters Inc | L'Europe | $200,000 – $250,000 |
Équipements de roulage | Inde | $125,000 – $175,000 |
Exigences en matière d'installation
Paramètres | Détails |
---|---|
Localisation | Atelier intérieur |
Puissance | Raccordement 25-30 kW |
Tension | 380-440 V AC 3 phases |
Air comprimé | Pression - 6 bar |
Volume - 10 CFM | |
Cadre de base | Plancher en béton porteur |
Eclairage | Intensité de 500 lux |
Contrôle du climat | Température ambiante 15-35°C |
Humidité : 20%-60% RH |
-
Machine de formage de bornes d'extrémité de glissières de sécurité pour autoroutes
-
Profileuse pour poteaux d'autoroute U/C
-
Machine de formage de rouleaux de glissières de sécurité à 2 vagues pour autoroutes
-
Machine de formage de rouleaux de glissières de sécurité à 3 vagues
-
Machine de formage de rouleaux de panne Sigma à taille variable automatique
-
Machine de formage de rouleaux de panne CZ à taille variable automatique
-
Machine de formage de rouleaux de panne Z à taille variable automatique
-
Machine de formage de rouleaux de panne CU à taille variable automatique
-
Petit pain de cadre d'armoire électrique formant la machine
Fonctionnement
- Minimum 3 opérateurs par équipe
- Un opérateur au dérouleur et à l'alimentation
- Un seul opérateur pour gérer l'outillage de roulage
- Un opérateur à la station de coupe post-formage
- Panneau PLC centralisé pour le contrôle des paramètres
- Écran tactile HMI pour la surveillance et l'enregistrement des données
Maintenance
Tâche | Fréquence | Méthode |
---|---|---|
Inspection du rouleau | Quotidiennement | Contrôle visuel de l'absence de dommages ou d'usure |
Lubrification du rouleau | Hebdomadaire | Graisser tous les roulements |
Huile hydraulique | Mensuel | Vérifier le niveau et faire l'appoint |
Annuel | Remplacer l'huile | |
Pièces de rechange | Selon les besoins | Rouleaux, lames, capteurs et moteurs de rechange recommandés |
Recalibrage du rouleau | Tous les 2 ans | Rectifier les rainures du rouleau si l'usure dépasse 0,15 mm. |
Choix du fournisseur
Paramètres | Importance |
---|---|
Vivre | Haut |
Expertise en matière de conception de rouleaux | Haut |
Qualité de construction | Haut |
Qualité du rouleau | Haut |
Précision du formage | Haut |
Taux de production | Moyen |
Niveau d'automatisation | Moyen |
Soutien au service | Haut |
Délai d'exécution | Faible |
Prix | Faible |
Avantages et inconvénients
Pour | Cons |
---|---|
Processus de formage continu et efficace | Investissement initial élevé en outillage |
Mise en place rapide entre les lots | Nécessite un cadre de base lourd |
Conception compacte par rapport aux presses plieuses | Capacité limitée en épaisseur et en largeur |
Contrôle cohérent de la tolérance | Entretien régulier nécessaire |
Adaptation à des profils personnalisés | Les dommages causés par les rouleaux peuvent interrompre la production |
Avantages par rapport aux presses plieuses
- Pas de marquage de la feuille ni de rayures dues aux matrices
- Taux de production plus élevé pour la production de masse
- Réduction du coût de l'outillage par pièce
- Action de formage continue contre flexion cyclique
- Propriétés uniformes des matériaux sur toute la longueur
Limites par rapport aux presses plieuses
- Coût initial de l'outillage plus élevé
- Capacité d'épaisseur limitée
- Ne peut pas former des formes complexes en 3D
- Certaines formes asymétriques difficiles à former
- Délai d'exécution de l'outillage plus long
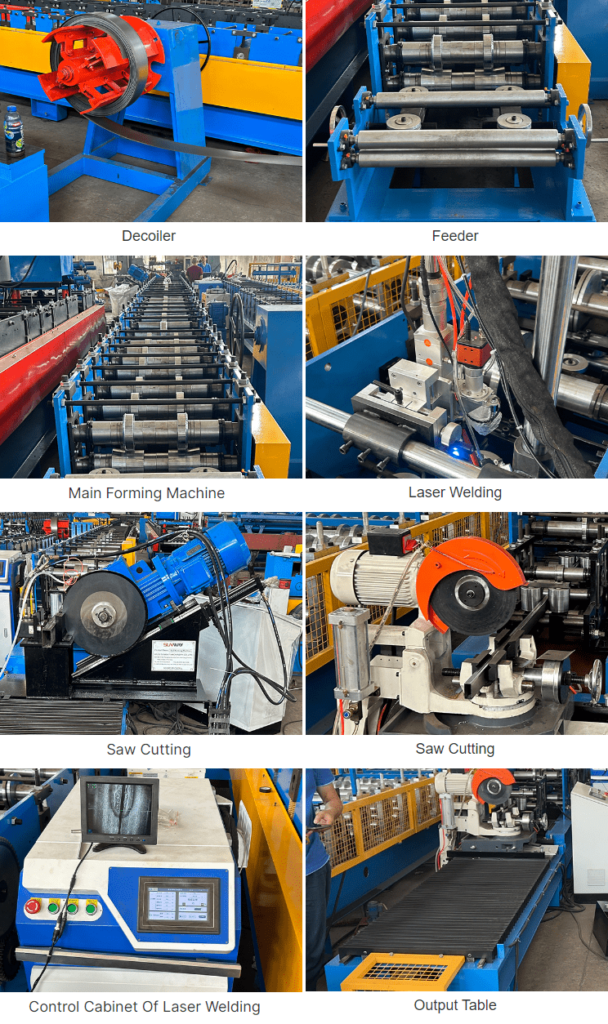
Applications typiques
- Rails de guidage pour ascenseurs
- Rails de tiroirs, glissières
- Rails latéraux du convoyeur
- Chemins de roulement des grues
- Palettes de stationnement automatique
- Pistes de manutention
- Rayonnages industriels
FAQ
Q : Quelle épaisseur d'acier ces machines peuvent-elles traiter ?
R : En général, il est possible d'obtenir des épaisseurs de 1 à 3 mm. La capacité maximale atteint jusqu'à 4 mm d'épaisseur d'acier.
Q : Quelle est la vitesse de production ?
R : La vitesse linéaire standard est de 10 à 15 mètres par minute. Certaines machines à grande vitesse atteignent un taux de production de 30 m/min.
Q : Quelle longueur de rails peut-on produire ?
R : La capacité standard est de 6 mètres. Les machines construites sur mesure peuvent produire des rails jusqu'à 12 mètres.
Q : Quelle est la précision et la qualité de surface possibles ?
R : Les pièces formées par laminage peuvent atteindre des tolérances de +/- 0,02 mm et une finition de surface d'environ 0,5 micron.
Q : Quel est le service après-vente offert ?
R : Aide à l'installation et à la mise en service, formation des opérateurs, garantie sur les pièces, service sur le terrain pour les réparations et assistance technique par téléphone ou par courrier électronique.