Storage grain silo roll forming machines are essential equipment for the agricultural and bulk material handling industries. This guide provides a comprehensive overview of grain storage silo roll formers, including types, characteristics, applications, specifications, suppliers, installation, operation, maintenance, and more.
Overview of Storage Grain Silo Roll Forming Machines
Storage grain silo roll forming machines create corrugated metal silos for storing bulk materials like grains, animal feeds, fertilizers, etc. The roll forming process transforms flat metal sheets into cylindrical or conical silo panels.
Key benefits of using grain storage silo roll formers:
- Highly customizable design – diameter, height, slope, panel shape can be adjusted
- Fast production of silo components
- Consistent quality and dimensional accuracy
- Cost-effective automated process
- Durable all-weather construction
- Quick and easy assembly on site
Roll formed silos are widely used for grain handling on farms, in bulk terminals, and food/feed processing plants. Their modular design allows creating small or mega-ton capacity silos as per storage needs.
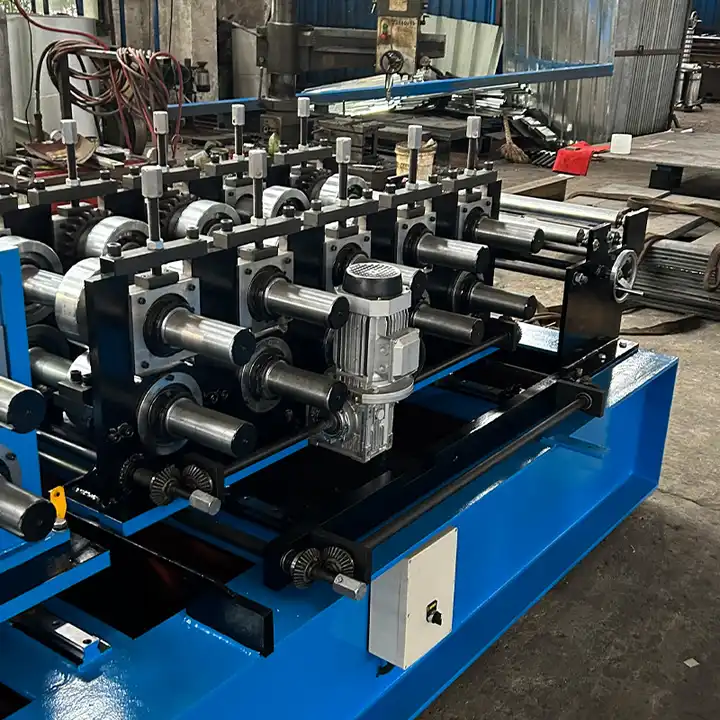
Types of Grain Storage Silo Roll Forming Machines
Based on Automation
Machine Type | Description |
---|---|
Manual | Basic roll former with manual controls for sheet feeding and forming adjustments |
Semi-Automatic | Automated sheet feeding but requires manual operation for roll gap settings |
Fully Automatic | Computerized controls for sheet feeding, roll adjustment and PLC automation |
Based on Silo Panel Shape Produced
Machine Type | Silo Panel Formed |
---|---|
Radial Rib | Corrugated panels with radial ribs for extra strength |
Trapezoid Corrugated | Trapezoidal wavy panels for greater volume |
Half Corrugated | Single wavy panels with lower cost |
Based on Production Capacity
Capacity | Silo Panels Produced |
---|---|
Low Volume | Up to 300 sheets per day |
Medium Volume | 300 – 800 sheets per day |
High Volume | 800+ sheets per day |
Higher automation levels and production volumes reduce labor and improve efficiency. Capacity is determined by roll former width and speed.
Key Specifications
Storage grain silo roll forming machines are customized but typical parameters are:
Machine Dimensions
- Length: 15 – 50 feet
- Width: 6 – 15 feet
- Height: 6 – 12 feet
Roller Specifications
- Roller Material: Steel or alloy
- Roller Diameter: 150 – 250 mm
- Roller Width: 2.5 – 6 feet
- Number of Rollers: 16 – 25
Sheet Metal Properties
- Sheet Width: 2 – 6 feet
- Thickness: 0.4 – 1 mm
- Material: Galvanized steel, aluminum
Silo Diameter Produced
- 3 feet to 80 feet
Production Speed
- Manual: 10 feet per minute
- Automatic: 16 – 30 feet per minute
Power Consumption
- 10 – 50 kVA
Applications and Uses
Storage grain silo roll forming machines are used to produce:
Silo Use | Key Considerations |
---|---|
Grain Storage | Conical bottom, unloading outlets, aeration, fumigation access |
Feed Storage | Dust control, load-bearing strength, ease of cleaning |
Fertilizer Storage | Corrosion resistance, minimized caking, weather protection |
Sand Storage | Abrasion resistance, maximum volume, low cost |
Grain silos have the widest range of specialized design options like temperature and moisture monitors, grain rotational systems, safety platforms, etc.
Choosing a Silo Roll Former Supplier
Consider the following when selecting a storage grain silo roll forming machine supplier:
- Experience in silo industry
- Custom design capabilities
- Range of machine capacities offered
- Availability of spare parts
- Maintenance and service support
- Installation assistance
- Operator training provided
- Cost of machine and tooling
- Production speed and efficiency
- Durability and lifespan of equipment
- Compliance with safety standards
Reputable manufacturers like Mecano, GME, Formtek, Metform offer customized grain storage silo roll forming solutions suitable for unique needs and budgets.
Storage Grain Silo Roll Former Price
Capacity | Price Range |
---|---|
Low Volume | $8,000 – $15,000 |
Medium Volume | $15,000 – $35,000 |
High Volume | $35,000 – $100,000 |
Cost depends on automation level, production speed, width, and customization. Additional costs for design, shipping, installation.
Get price quotes from multiple vendors before deciding.
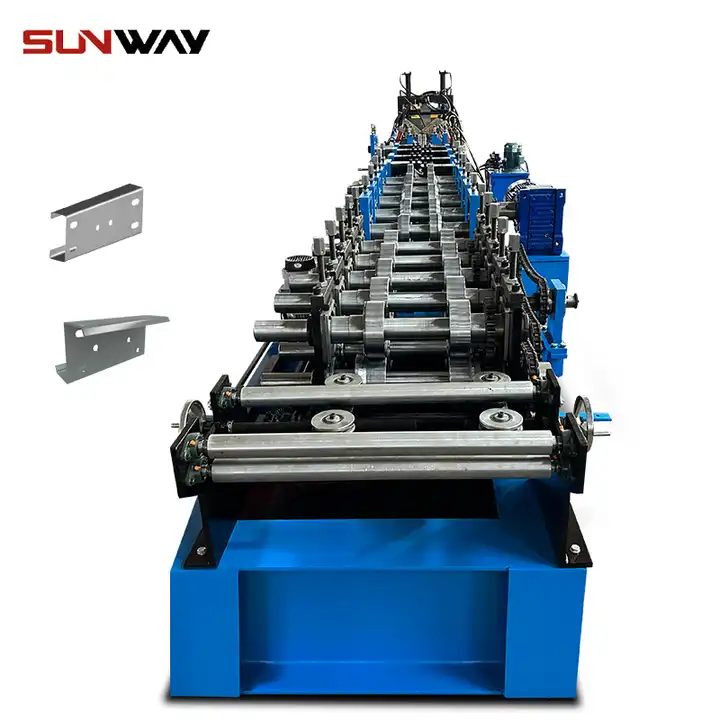
How to Install and Operate
Proper installation and operation ensures optimum performance and longevity of storage grain silo roll forming machines.
Installation Tips
- Mount machine on flat, level concrete base
- Align to sheet coil feed line
- Anchor securely to floor
- Connect electric power supply
- Install safety guards and controls
- Test run without load
Operation Guidelines
- Adjust roller gap as per sheet thickness
- Set speed in correlation with sheet feed
- Use edge guides to center sheets
- Set forming angles to achieve desired corrugation
- Ensure lubrication and cooling systems work
- Inspect rollers and guides periodically
- Clean collected metal debris frequently
- Follow preventive maintenance schedule
Take supplier assistance for initial installations. Train workers thoroughly on procedures.
Maintenance and Precautions
Regular maintenance is vital for storage grain silo roll formers to deliver high production yields and avoid breakdowns.
Maintenance Activities
Task | Frequency |
---|---|
Inspect rollers and guides | Daily |
Check electrical wiring | Weekly |
Lubricate roller bearings | Monthly |
Adjust drive chain tension | Quarterly |
Clean or replace air filters | 6 months |
Inspect and realign rollers | Annually |
Safety Measures
- Ensure proper machine grounding
- Keep emergency stops accessible
- Wear protective eye glasses and gloves
- Avoid loose clothing or jewelry
- Manage and segregate metal scrap
- Follow lockout procedures before maintenance
Troubleshooting Tips
- Uneven sheet feeding – realign edge guides
- Sheet jamming – check roller gap, reduce speed
- Excessive noise – lubricate bearings and joints
- Blurry corrugations – replace worn out rollers
- Power fluctuations – install voltage regulator
Proactive care combined with preventive maintenance enhances the performance and lifespan of grain storage silo roll forming machines considerably.
Pros and Cons of Roll Formed Silos
Advantages
- Lower material cost vs welded silos
- Uniform quality and dimensional accuracy
- Higher corrosion resistance
- Faster assembly with bolted construction
- Lower maintenance requirement
- Modular expandable design
- Customizable height and diameter
Limitations
- Not suitable for small capacities below 2000 tons
- Limited number of unload-fill cycles
- Not fully airtight like welded silos
- Penetration by rodents needs prevention
- Monitoring systems require separate installation
For grain storage above 5000 tons and 20-30 year lifespan, roll formed silos present a cost-effective solution.
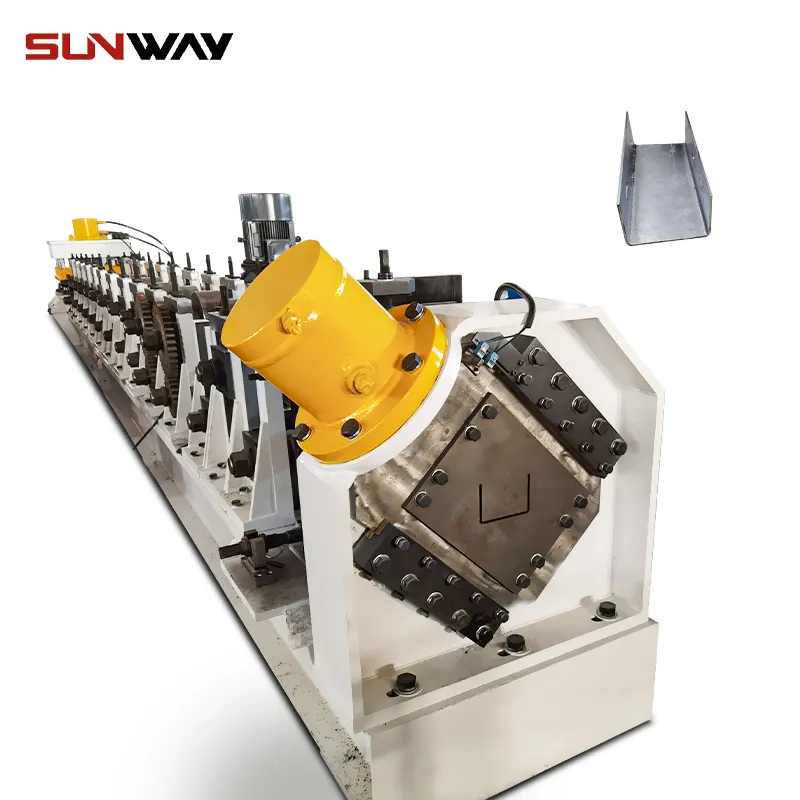
উপসংহার
Storage grain silo roll forming machines enable efficient production of corrugated metal silo panels customized for diverse agricultural bulk storage needs.
With appropriate machine selection, installation, operation and maintenance, substantial benefits in silo construction speed, cost optimization, weather protection, and durable long-term storage can be realized.
Careful comparison of specifications and reputation of leading roll former manufacturers is advised to get the best value equipment. With some design limitations, roll formed silos present a worthwhile investment for most grain handling operations compared to conventional welded silos.
FAQs
Q: What metals can be used to make grain silos via roll forming?
A: Galvanized steel and aluminum sheets are commonly used. Steel offers strength while aluminum provides weather resistance. Required sheet thickness is 0.5-1mm.
Q: What factors affect the load bearing capacity and strength of roll formed silos?
A: Rib patterns, sheet thickness, steel grade, corrugation profiles, and bolt connections determine the load capacity. Radial rib silos offer the highest strength.
Q: How long does it take to install a roll formed grain silo on site?
A: A typical 50 feet diameter, 45 feet tall silo would require 3-4 days for roll forming the panels and 3 days for installation by a trained crew.
Q: What is the expected lifespan of roll formed grain silos?
A: With proper maintenance and upkeep, roll formed silos will easily last 20-30 years. The galvanized coating provides long-term corrosion protection.
Q: How to decide on the diameter for grain silos?
A: Diameter choice depends on storage capacity needed, available space, filling/unloading rates required, land constraints, and discharge cone dimensions. Typical range is 20 to 60 feet.
Q: What are some key accessories needed for grain storage silos?
A: Essential accessories include temperature cables, grain spreaders, access ladders, safety cages, inspection doors, unload equipment, aeration fans and ducting.
Q: Is on-site operator training provided for grain silo roll forming machines?
A: Reputed suppliers offer 2-3 days of on-site training to customers for proper machine operation, maintenance and troubleshooting.
Q: How much space is needed to install a storage grain silo roll forming machine?
A: Approximately 1200 square feet of floor space is required for a standard roll former with some additional space for raw sheet coils.