Sheet roll forming is a metal working process that forms metal coils into customized profiles with a continuous flow. Sheet roll forming machines are used to produce longitudinal parts with constant profile like roofing sheet, wall panel, door frame etc. This article provides a comprehensive overview of sheet roll forming equipment.
Overview of Sheet Roll Forming
Sheet roll forming is a continuous and efficient way of producing large volumes of custom metal parts with uniform cross-sections. A coil of sheet metal is fed through a series of consecutive rolling stands containing rollers that bend the metal progressively until the desired cross-section profile is achieved.
Some key advantages of sheet roll forming:
- Highly automated process with fast production rates
- Ability to form complex and customized profiles
- Consistent and high quality finished parts
- Low tooling costs compared to other processes like stamping
- Minimal material waste
Sheet roll forming is ideal for producing metal parts like roofing sheets, wall panels, track beams, rails, angles, channels, studs, door frames etc. It is commonly used in construction, infrastructure, transportation, appliance manufacturing and other industrial applications.
Types of Sheet Roll Forming Machines
There are several types of sheet roll forming machines available to produce different kinds of formed profiles.
Portable Roll Forming Machines
- Compact and movable machines with fast set-up
- Used directly at site for on-demand fabrication
- Limited profile shapes and sizes
- Lower capacities around 10-20 units per hour
Production Roll Forming Lines
- High capacity automated lines for mass production
- Produce up to 40,000 units per hour
- Require fixed installation space in factory
- Capable of complex custom profiles in different materials
- Require higher investment
C-Type Vertical Roll Forming Machines
- Rollers are arranged in a C-shaped vertical configuration
- Floor space saving design
- Suitable for long length linear profiles
- Limitation on profile complexity
O-Type Horizontal Roll Forming Machines
- Rollers are arranged in a O-shaped horizontal configuration
- Larger forming area and capacity
- Able to make more complex and unusual shapes
- Require more floor space
Pyramid Type Roll Forming Machines
- Rollers arranged in a four-sided pyramid shape
- Achieve very high dimensional accuracy
- Ideal for high precision parts like rail tracks
- Require significant floor space
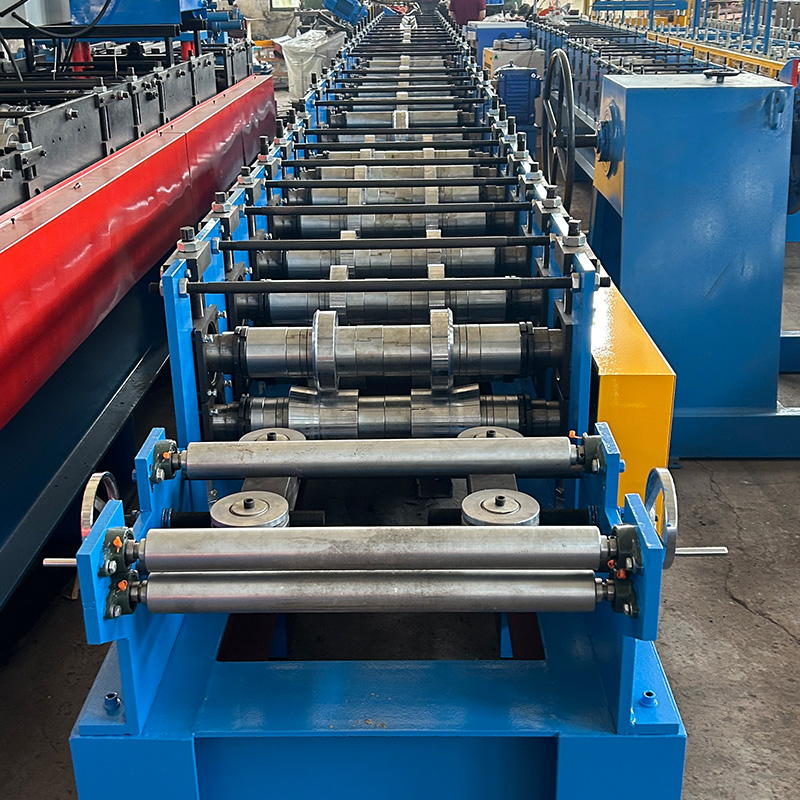
Main Components of Sheet Roll Forming Machines
Sheet roll forming lines have three main sections – the decoiler, forming section, and cutoff area.
- ডিকয়লার – Feeds raw coil strips into the forming section
- Forming Section – Contains series of rolling stands to progressively form the profile
- Cut off – Cuts finished profiles to required lengths
Other components like loop control, pre-punching unit, post-cutting unit, stacker etc. may be added based on application requirements.
The main considerations when choosing components are:
- বেলন উপাদান – Carbon steel, alloy steel or titanium alloy based on forming loads
- Roller Size – Diameter and width determine bending force capacity
- Roller Type – Hexagonal, spherical or crowned rollers used as per profile
- Roller Bearings – Antifriction bearings to handle high speed rolling loads
- Forming Stands – Rigid housings that support and position rolling assemblies
- Punches & Dies – For pre-cutting holes or notches in the strip
- নিয়ন্ত্রণ ব্যবস্থা – PLC based controls for automatic operation
Key Specifications of Sheet Roll Forming Machines
The main parameters and specifications considered while selecting sheet roll formers:
Specification | Typical Range |
---|---|
গঠন গতি | 10 – 120 m/min |
Raw Material Thickness | 0.3 – 2 mm |
Finished Part Width | 50 – 3000 mm |
Part Thickness | 1 – 10 mm |
Part Length | 500 – 20000 mm |
Forming Stands | 10 – 50 numbers |
Drive Power | 3 – 75 kW |
Higher the number of stands, greater the profile complexity that can be achieved. More driven stands provide higher forming forces.
Typical Applications and Suitable Materials
Sheet roll forming is used produce linear profiles across many industries:
আবেদন | Materials Used |
---|---|
Roofing Sheets | Prepainted steel, zinc-aluminum alloy coated steel |
Wall Panels | Galvanized steel, aluminum |
Door Frames | Stainless steel, Mild steel |
Rack & Shelving | Mild steel, stainless steel |
Highway Guards | Galvanized steel |
Railway Tracks | Heat treated alloy steel |
Materials that can be effectively roll formed include mild steel, stainless steel, galvanized steel, aluminium and its alloys.
Sheet Roll Forming Machine Suppliers
There are many manufacturers supplying sheet roll forming equipment and lines:
Supplier | Location | Starting Price Range |
---|---|---|
ECeCo Ltd | ইতালি | $150,000 to $500,000 |
Formtek | USA | $200,000 to $750,000 |
Shanghai Slitt Equipment | China | $50,000 to $250,000 |
Sanket Machinery | ভারত | $60,000 to $200,000 |
ROLLFORM S.A. | Poland | $100,000 to $350,000 |
Pricing varies based on specifications like part width, material thickness, line speed, and profile complexity affecting number of stands. Complete high capacity lines are costlier.
Key Considerations for Buying Sheet Roll Forming Machines
Here are the main factors to evaluate when purchasing sheet roll forming equipment:
- Part Profiles – The shape and dimensional accuracy required
- Production Volume – The throughput rate based on demand
- Material Specs – Type, thickness, width and tensile properties
- Space Available – To decide footprint and layout
- Power Source – Compatibility with available electrical supply
- Control Interface – Operator controls, automation and data monitoring needs
- Safety Features – Emergency stops, guards, alarms etc.
- Operating Costs – Energy use, maintenance needs etc.
- Future Flexibility – Ability to change tooling for new profiles
- Availability of Support – Installation assistance and after sales service
Reviewing capabilities of different manufacturers as per the above considerations will help select the right sheet roll forming system.
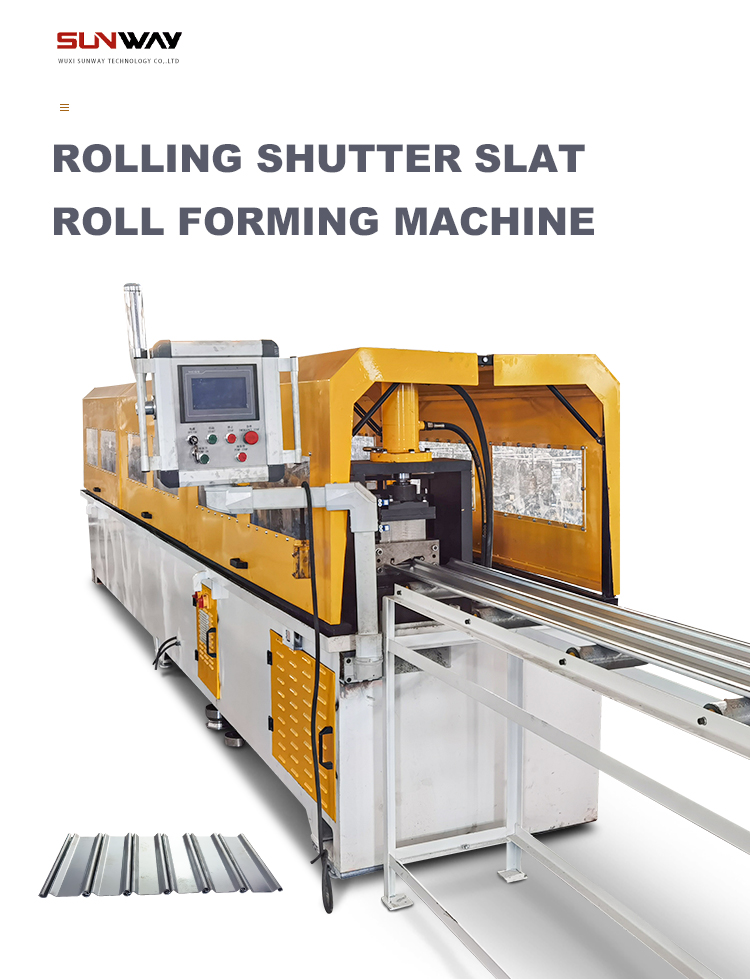
Installation and Operation of Sheet Roll Formers
Proper installation and operation procedures are vital for optimum performance of sheet roll forming machines. Here are some guidelines:
- Carefully inspect all components received for any damage during transit
- Install machine on sturdy, level foundation allowing clear access on all sides
- Ensure sufficient space around for safe material loading and unloading
- Connect electric power supply as per specified rating and frequency
- Provide adequate earthing connection
- Mount tooling and adjust components to achieve designed forming profile
- Check lubrication levels of bearings and gearboxes
- Verify all safety mechanisms and interlocks are functional
- Run initial tests at low speed with incremental ramp up to full speed
- Monitor current draw by motors during operation
- Use material of recommended specifications for trouble-free running
- Periodically inspect formed profiles for accuracy
- Follow recommended maintenance schedule
Getting technical support from the supplier during installation and initial runs ensures optimal setup. Proper operation and maintenance will maximize uptime and extend lifespan.
Maintenance of Sheet Roll Forming Lines
To sustain high efficiency and productivity, sheet roll formers require regular maintenance:
- Clean the line of metal dust and oil accumulation
- Lubricate bearings and inspect for wear
- Check belt tension and gearmesh of gear trains
- Verify tightness of all bolts, nuts and fasteners
- Monitor rollers for surface wear and repair/replace as needed
- Examine decoiler and straightener for defects and damage
- Inspect guards and interlocks for functionality
- Check hydraulic systems and pumps for leaks if applicable
- Verify electrical connections are tight and panels are clean
- Monitor drive components like motors and gearboxes
- Schedule preventive maintenance during planned shutdowns
- Maintain detailed logs of all inspections and parts replacements
Establishing standard maintenance procedures and checklists will help ensure reliable functioning of the roll forming system.
Choosing the Right Sheet Roll Forming Machine Manufacturer
Selecting the right supplier is key to getting a high quality sheet roll forming machine. Here are important factors to consider:
- Technical expertise – Experience designing roll form tooling and machines
- Proven track record – Years in business, customer testimonials
- Product range – Offer machines catering to diverse needs
- Customization skills – Ability to design special profiles
- Quality standards – Use of high precision components
- Production capability – Capacity to deliver machines on schedule
- Service support – Installation assistance and maintenance staff
- Global presence – Sales and service network for easy access
- Pricing – Competitive pricing fitting your budget constraints
- Responsiveness – Quick turnaround on queries and issues
A manufacturer well established in the industry with the above characteristics can supply machines that meet requirements cost effectively with good after sales support.
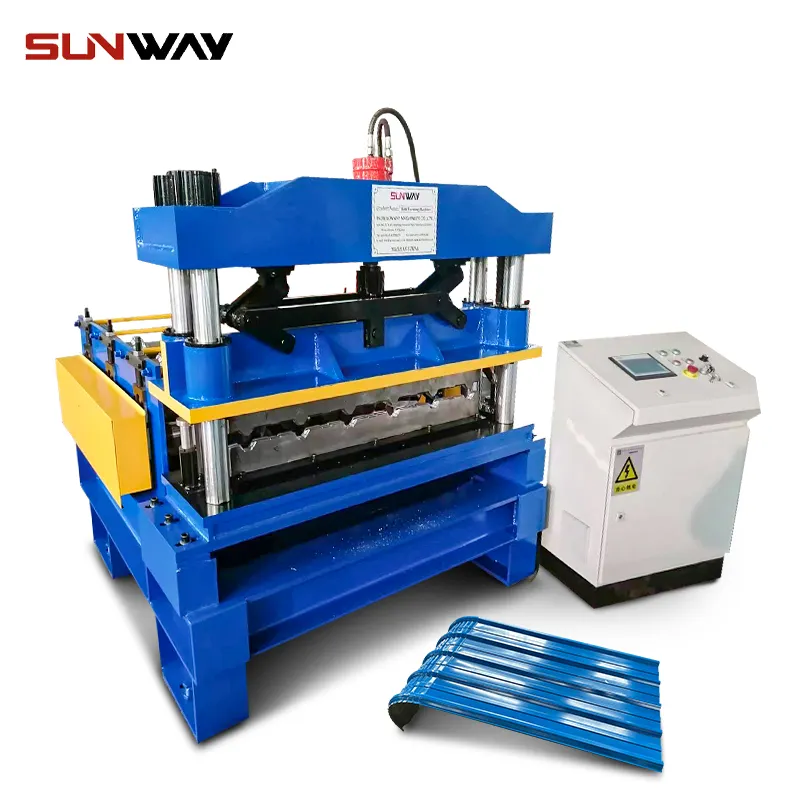
Pros and Cons of Sheet Roll Forming Process
Advantages
- High production rates with continuous forming
- Consistent and dimensionally accurate parts
- Versatile process capable of complex profiles
- Low tooling investment and quick changeovers
- Minimal material wastage compared to stamping
- Lower costs compared to other processes
- Ability to use coils enables very long uninterrupted lengths
- Finished aesthetic appearance, no further processing needed
Limitations
- Not the most suitable process for small batch production
- Limitations on material thickness and hardness that can be formed
- Higher initial machine investment cost
- Requirement of large operating space
- Limited to making linear symmetrical profiles
- Profiles prone to springback unless proper allowance is provided
FAQ
What materials can be roll formed?
Sheet roll forming is suitable for ductile materials like low carbon steel, stainless steel, aluminium and its alloys, copper alloys and titanium alloys. Hardened metals cannot be reliably formed.
What thickness range of materials can be roll formed?
Standard sheet roll formers can process material thickness from 0.3 mm to about 3 mm. Special roll formers are available to work with up to 8 mm thick strips.
What accuracy and tolerance can be achieved?
Roll formed parts can achieve a dimensional accuracy up to +/- 0.5 mm over length. The process is capable of holding very tight tolerances.
How many rolling stands are needed for a profile?
The number of stands needed depends on complexity of the profile. Simple profiles require 6-8 stands while complex shapes need 16-22 stands. More stands allow more gradual bending.
Is surface finish an issue with roll forming?
Profiles formed using hardened polished rollers can achieve surface roughness values up to Ra 0.4 μm, comparable to fine mill finish.
What is the typical production rate of sheet roll forming lines?
Production rates vary from 10 to 40 units per minute based on part size. High speed lines produce over 2000 units per hour.
What degree of automation is used in sheet roll formers?
Sheet roll formers utilize a high degree of automation with features like automatic size changeover and material feeding. The lines can run lights-out with minimum supervision.
What safety aspects need to be considered?
Safety elements like emergency stops, guards, interlocks, alarms, protective covers and overload protection need to be incorporated in the design. Safe material handling is also vital.
How much maintenance do these machines need?
Other than regular cleaning and lubrication, sheet roll formers require minimal maintenance if high quality components are used and properly operated within ratings.
উপসংহার
Sheet roll forming is an efficient, high speed metal working process enabling mass production of custom longitudinal profiles. The automated forming lines with a series of rolling stands can produce a variety of parts like roofing sheets, panels, door frames etc. to tight tolerances using coiled raw material.
Careful selection of equipment based on production needs and with support from reputed manufacturers can ensure high productivity and quality results. Proper installation, operation and maintenance procedures help maximize the machine effectiveness and lifecycle. Overall, sheet roll forming presents an economical solution for metal fabricators to meet just-in-time demands with flexibility.