ক glazed roof tile roll forming machine is an important equipment used for manufacturing interlocking roofing tiles with a protective glazed coating. This guide provides a comprehensive overview of glazed roof tile roll forming machines covering their working, types, applications, specifications, selection factors, installation, operation, maintenance and more.
Overview of Glazed Roof Tile Roll Forming Machine
A glazed roof tile roll forming machine is designed to transform metal coils into formed interlocking roofing tiles which are then coated with a glazed finish.
What are Glazed Roof Tiles?
Glazed roof tiles are interlocking roof covering tiles with a ceramic glazed coat finish. The glaze provides a protective, waterproof and decorative finish on the formed metal roof tile.
Working Principle of Glazed Roof Tile Roll Forming Machine
A glazed roof tile roll forming machine takes metal coil as input and converts it into formed roofing tiles by passing through consecutive roll forming stations. The profiles tiles are then spray coated with glaze before cut-off and stacking.
Key processes:
- Coil sheet feeding
- Progressive roll forming into roof tile profile
- Application of glaze coat on tiles
- Cutting individual tiles as per length
- Stacking of finished tiles
Advanced machines allow quick changeover to different tile sizes and profiles.
Types of Glazed Roof Tile Roll Forming Machines
Glazed roof tile roll forming machines are available in different configurations:
Based on Automation
- Manual
- Semi-automatic
- Fully-automatic PLC controlled
Based on Production Speed
- Low speed: Up to 10 m/min
- Medium speed: 10 – 30 m/min
- High speed: Above 30 m/min
Based on Tile Types
- Interlocking flat tile profile
- Interlocking roman tile profile
- Custom tile profiles
Based on Glazing Method
- Manual spray glazing
- Automatic roller/curtain glazing
- Fluorocarbon glaze coatings for durability
Based on Processing
- Roll forming only
- Roll forming + glazing line
- Roll forming to palletizing integrated system
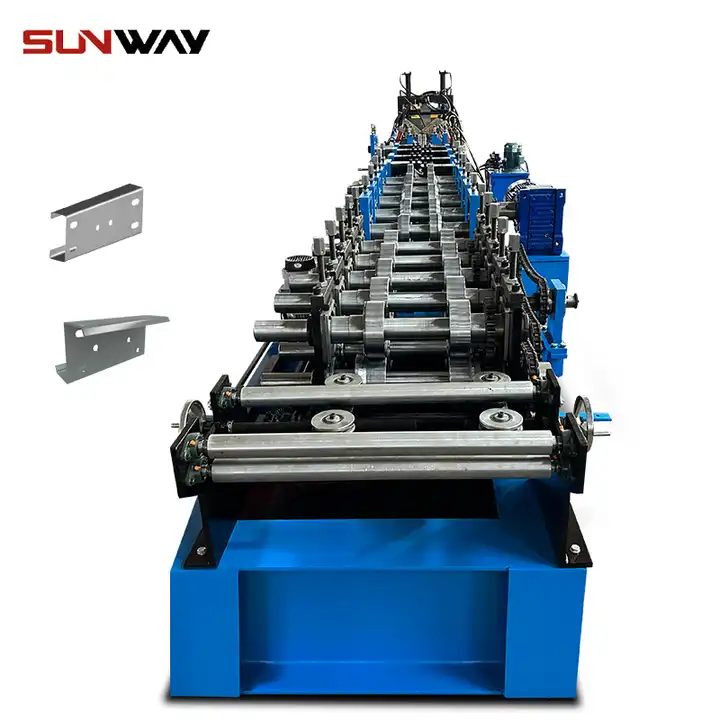
Applications of Glazed Roof Tiles Produced by Roll Forming
Glazed roof tiles made by roll forming find application in:
- Residential roofing for houses, villas, apartments
- Commercial buildings like offices, shops, lodges etc.
- Warehouses, barns, garages roof covering
- Re-roofing and replacement of old roofing tiles
- Temporary structures and exhibition shed roofing
- Decorative roofing accents and housing elements
- Roof rainwater drainage and guttering elements
Glazed tiles offer durability, decorative finish and waterproofing for roofing needs.
Glazed Roof Tile Roll Forming Machine Specifications
Glazed roof tile roll forming machines are available with different specifications based on output and production needs:
Specifications | Typical Range |
---|---|
Production Speed | 10 – 50 m/min |
Tile Width | 300 – 1000 mm |
Tile Thickness | 0.35 – 1 mm |
কয়েল প্রস্থ | Up to 1250 mm |
Coil Thickness | 0.30 – 0.8 mm |
Forming Stations | 16 – 24 |
Power Consumption | 15 – 40 kW |
Voltage | 380V, 50Hz, 3 Phase |
Machine Weight | 8000 – 15000 kg |
Machine Size | 10 – 25 m Long x 3 – 4 m Wide |
These parameters can be customized as per specific production requirements.
Design and Working Standards
Glazed roof tile roll forming machines need to adhere to certain design standards:
- Robust steel frame construction with precision leveled forming beds
- Hardened roll tooling for extended service life
- Multi-axis powered decoiler for smooth feeding
- Independent AC drive motors for controlled forming
- Automatic edge milling and punching stations
- Hydraulic system for tile pressing and punching
- Adjustable forming stations for quick size changeovers
- Safety guarding for operator protection
Suitable framing arrangements should be provided for glazing application modules.
Choosing a Glazed Roof Tile Roll Forming Machine Manufacturer
Here are some tips for choosing a good glazed roof tile roll forming machine manufacturer:
পরামিতি | What to Look For |
---|---|
অভিজ্ঞতা | Number of years in business, proven track record |
উৎপাদন | In-house manufacturing with quality control |
কাস্টমাইজেশন | Ability to customize machine to needs |
Quality | Advanced automation for consistent quality |
Certification | ISO 9001, CE certifications |
Service Support | Installation, commissioning and operator training |
Cost | Competitive pricing and payment terms |
Inventory | Ready models available for faster delivery |
Location | Distance for logistics and service support |
- Check sample tiles from machine for quality assurance
- Ensure availability of spares, service support
- Compare cost, production rate and delivery time
- Inspect machine manufacturing facility if possible
- Choose a reputable manufacturer for reliability
This helps get high performance glazed roof tile roll forming machines as required.
Installation of Glazed Roof Tile Roll Forming Machine
Proper installation is important for smooth functioning of a glazed roof tile roll forming line:
- Prepare level concrete foundation as per layout drawings
- Position the machine components using cranes/forklifts
- Assemble the roll forming sections, decoiler, pressure unit as per drawings
- Install the tile pressing, punching and embossing stations
- Connect the electrical motors, controls, hydraulics per manual
- Wire up the electrical switches, drives and sensors
- Install safety guarding around the moving components
- Check lubrication levels on all gear systems
- Test run the machine and make adjustments as required
Correct installation as recommended by the manufacturer is critical.
Working and Operation of Glazed Roof Tile Roll Forming Machine
Working a glazed roof tile roll forming machine involves these key steps:
Pre-Operation Checks and Settings
- Check electrical wiring, hydraulics, lubrication
- Set up decoiler brake tension as per tile gauge
- Adjust rollers in each station for proper material flow
- Set cutting length based on tile size
- Adjust glazing spray nozzles as per tile width
- Test glaze pump, valves, spray headers for readiness
- Clear any material scrap or residues in the line
Starting the Machine
- Turn on the machine drives in jog mode
- Start the decoiler to feed the metal coil through stations
- Gradually increase production speed to set levels
- Initiate glazing spray system and set paint pressure
- Adjust trim knives for edge cutting if needed
- Check tile quality and optimize forming gradually
- Initiate auto stacker once line is stabilized
During Operation
- Monitor line for any jams, noise issues and stop if arising
- Conduct periodic quality checks on tile dimensions
- Ensure proper lubrication on all moving components
- Monitor the coil diameter and plan decoiler coil change
- Inspect glazing nozzle spray pattern and coverage
- Touch up tile surface finish if required
- Clear any accumulated scrap or tiles from the line
Shut Down
- Stop the decoiler and allow material to clear the line
- Switch off the glazing pumps and blow out the lines
- Gradually reduce speed to zero and shut off drives
- Clean the machine thoroughly before next use
Following recommended procedures is key for optimal functioning.
Maintenance of Glazed Roof Tile Roll Forming Machines
Regular preventive maintenance activities ensure continuous working of the glazed roof tile roll forming line:
Activity | Frequency | Method |
---|---|---|
Cleaning | Daily | Remove tile and glaze buildup, dust, scrap |
Inspection | Daily | Check for leaks, abnormal noise |
Lubrication | Weekly | Grease bearings, gears, apply chain lube |
Roller Inspection | Monthly | Check contour wear, replace if needed |
Drive Inspection | Monthly | Check chains/belts tension, adjust/replace |
Hydraulics | Quarterly | Check cylinders, pipes for leakages |
Electrics | Half-yearly | Check loose connections, insulations |
Calibration | Yearly | Calibrate pressure sensors, controllers |
- Maintain daily, weekly and monthly preventive schedules
- Schedule longer maintenance during shutdowns
- Keep sufficient spares like rollers, seals, belts in stock
- Train technicians on equipment maintenance procedures
- Track machine hours run and maintenance logs
Proper maintenance improves equipment life and avoids downtime.
Troubleshooting Common Issues in Glazed Roof Tile Roll Forming Machines
Some common issues faced in glazed roof tile roll forming machines are:
Issue | Possible Causes | Solutions |
---|---|---|
Coil jamming | Improper decoiler brake setup Worn rollers Edge damage | Adjust decoiler brake Replace worn forming rollers Use edge trimmed coils |
Tile distortion | Improper roller gaps Station misalignment | Reset roller gaps Realign forming section levels |
Glaze dripping | Improper spray pressure Nozzle clogged | Adjust glaze pump pressure Clean nozzles |
Machine vibration | Loose foundation bolts Misaligned gearbox | Tighten foundation bolts Realign gearbox and shafts |
Hydraulic oil leak | Seal damage Hose breach | Identify and replace damaged seal Replace breached hose |
Analyzing root causes and fixing deficiencies can resolve common machine issues.
Improving Productivity of Glazed Roof Tile Roll Forming Machines
Some ways to improve productivity from glazed roof tile roll forming machines are:
- Optimize line speed by reducing bottlenecks
- Schedule quick size changeovers to maximize production runs
- Automate downstream processes like stacking and packaging
- Ensure consistent quality of input metal coils
- Train operators on standard operating procedures
- Perform regular preventive maintenance to minimize downtime
- Use IoT sensors for remote monitoring and diagnostics
- Analyze downtime reasons and address weak spots
- Keep sufficient spares inventory to reduce downtime
- Upgrade machine with latest automated features
The right initiatives can significantly improve the productivity of glazed roof tile roll forming lines.
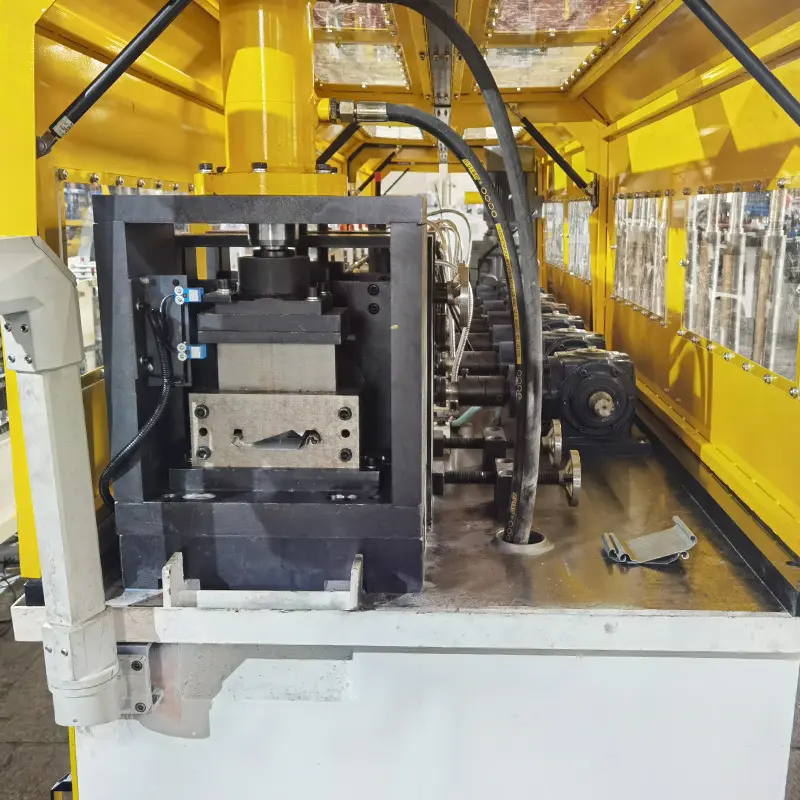
FAQs
Q: What is the production capacity of these machines?
A: Production capacity depends on speed and profiles – typically around 400-800 tiles/hr for medium speed machines.
Q: What are the regular maintenance activities required?
A: Maintenance involves cleaning, lubrication, inspection & replacement of rollers, seals, belts, chains as per schedule.
Q: What is the typical accuracy achieved on these machines?
A: Advanced machines with servo control can achieve dimensional accuracy up to ±0.5 mm and angular accuracy up to ±1°.
Q: What consumables are required during operation?
A: Metal coils, glaze paint, lubricants, hydraulic oil, spare parts like belts, seals are required.
Q: What is the typical lifespan of these machines?
A: Around 15-20 years lifespan can be achieved with proper maintenance.
Q: What factors affect the pricing of these machines?
A: Speed, automation level, tile size range, and optional accessories impact the overall cost.
Q: What is the typical power consumption?
A: Power consumption is typically 15-40 kW depending on the machine size and configuration.
Q: What installation support is provided?
A: Manufacturers provide installation guidelines, drawings, technicians support and operator training.
Q: What is the typical delivery time?
A: Ready standard models take 1-2 months while customized machines take 3-4 months delivery time.
উপসংহার
The glazed roof tile roll forming machine is an efficient equipment enabling automated production of interlocking roofing tiles with protective glazing in various sizes. This guide has provided a comprehensive overview of all relevant aspects of glazed roof tile roll forming machine selection, installation, operation and maintenance to maximize productivity and product quality.