Overview of Farnham Roll Forming Machines
Farnham roll forming machines are high-quality roll formers used to produce metal roofing panels, wall panels, decking, and related building products. Key details include:
- Offered by the Farnham Sheet Metal division of Carlisle Construction Materials.
- Continuous production of formed parts from coiled metal strip.
- Capable of complex profiles with ribs, embossing and stiffening features.
- Quick changeover between parts by replacing roll tooling modules.
- Range of automation options for material handling, part cut-off, and stacking.
- Typically used by building products manufacturers supplying to construction industry.
- Finished panels made of painted, galvanized, or aluminum coil stock.
Roll Formed Products Using Farnham Machines
- Metal roofing panels like standing seam, batten, lap seam, shake, and more
- Wall panels, liner panels, siding
- Floor and roof decking
- Rainware products like gutters and downspouts
- Structural studs, door frames
- Specialty profiles
Farnham roll formers produce a wide range of building components for residential, commercial, and agricultural applications.
Key Features of Farnham Roll Forming Lines
- Heavy-duty robust steel construction
- Helical gear drives for smooth power transmission
- Electronic servo roll adjustment
- Touchscreen controls with automatic sequencing
- Quick roll change systems reduce down time
- Range of powered conveyors, cutoff, and stackers
- Designed for 24/7 high production
Built with quality components for long service life in high-volume forming operations.
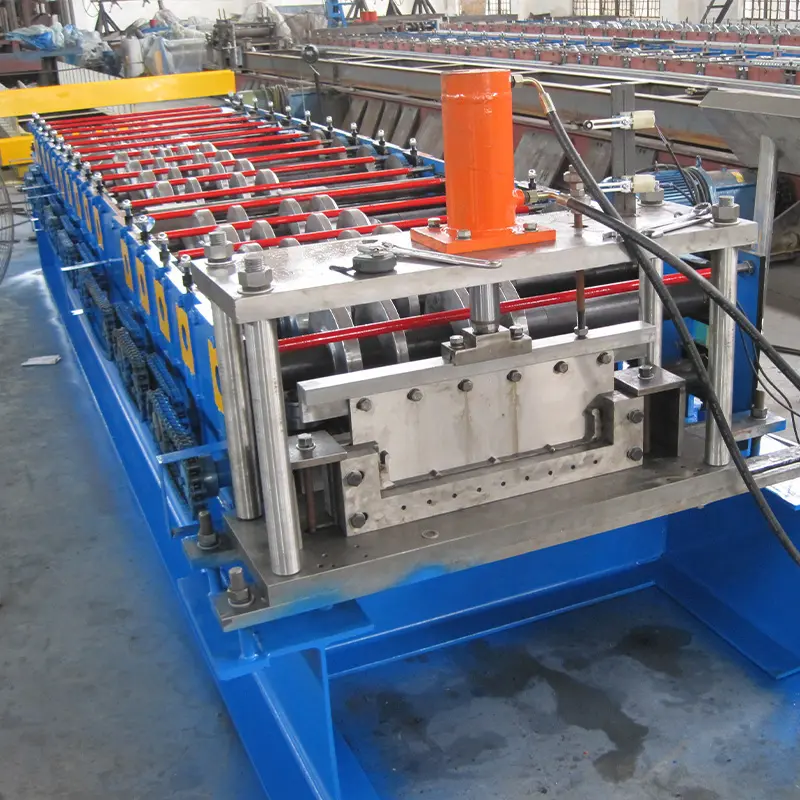
How to Select a Farnham Roll Former
Key factors to consider when selecting a Farnham roll forming machine:
- Production needs – Assess required output rate, coil widths/gauges, and complexity of desired profiles. Choose appropriate Farnham model specifications.
- Automation level – Determine if manual, semi-automatic or fully automatic material handling and part stacking functionality is needed.
- Tooling – Farnham offers a library of standard profile tooling plus custom roll sets for unique profiles. Evaluate availability.
- Technical support – Farnham provides installation assistance, operator training, and ongoing service support. Ensure regional availability.
- কাস্টমাইজেশন – Select any specialized options like pass schematics, safety guarding, and instrumentation.
- Budget – Farnham offers a range of equipment levels and automation. Confirm capital purchase fits within project budget.
- Expandability – Consider if additional future profiles or capacity increases are likely. Select a system that can evolve over time.
Work closely with Farnham application engineers to identify the best equipment configuration for your specific production requirements.
Roll Tooling Design Principles
Proper roll tooling design is key to producing high quality formed parts efficiently on a Farnham machine. Guidelines include:
- Optimize part profiles for stiffness, interlocking, and material utilization. Minimize need for supplemental supports.
- Design symmetrical, gradual roll contours to support uniform material flow and avoid thinning or tearing.
- Engineer roll penetrations and sequences carefully to control material stress and deformation.
- Adjust rolls to provide even controlled pressure across full forming width. Minimize gaps.
- Match top and bottom rolls to ensure consistent profiles and precision tolerances.
- Consider using roll materials with special lubricity coatings that aid forming of harder metals.
- Reduce sharp corners which concentrate stress by using larger radii bends.
- Work jointly with Farnham tooling engineers to develop optimal roll designs and pass schedules.
Effective roll set engineering ensures smooth continuous production of properly formed parts without defects.
Preparing for Farnham Roll Former Installation
To prepare for arrival and setup of a new Farnham roll forming machine:
- Provide electrical supply required – confirm voltage, breaker/fuse capacity. Install disconnect lockout switch.
- Ensure sufficient space for equipment footprint plus safe operator work zones around the machine.
- For fully automated systems, allow for material and part conveyor lengths and overflow/reject collection areas.
- Obtain any necessary permits – electrical, building, local codes and regulations.
- Prepare rigid foundations per Farnham specifications – typically reinforced concrete rated for full machine loads.
- Establish ventilation for any coolant mist or exhaust fumes from lubricants.
- Gather lift truck, cranes, or other means to offload heavy machine components from trucks.
- Arrange for skilled electricians and technicians for installation, wiring, and debugging of machine.
- Schedule well in advance of production startup date to allow adequate preparation time.
Thorough planning and upfront preparation prevents issues during roll former delivery and installation.
Installation and Setup Best Practices
Recommended practices during Farnham roll former installation:
- Carefully offload components from truck using appropriate lifting devices. Avoid damage.
- Follow sequence provided by Farnham documentation for proper assembly and alignment.
- Have qualified electricians complete power, sensor, and control wiring per electrical diagrams.
- Anchor forming machine securely to flooring – dynamic loads can shift an improperly secured machine.
- Install all safety guarding prior to power up. Avoid exposed pinch points.
- Fill gear cases, hydraulics, lubricators, and other reservoirs with recommended fluids.
- Validate proper jog direction of all drives. Reverse as needed.
- Gradually power up the line and exercise all functionality to validate correct operation.
- Make measured roll adjustments in sequential order from infeed to exit end to debug tooling.
- Only start full production after successful commissioning trials prove out the complete line.
Careful installation by qualified technicians ensures a smooth startup and transition to full production operation.
Roll Former Operation and Quality Control
To safely operate a Farnham roll forming machine at optimal quality:
- Monitor line speed, web alignment, and motor loads continuously. Make adjustments as needed.
- Frequently inspect formed part dimensions and check for defects using go/no-go gauges.
- Ensure input coil parameters – width, thickness, lubrication, tensioning – are maintained per Farnham recommendations.
- Change forming roll segments promptly when wear first becomes noticeable before scratches form on parts.
- Schedule machine downtime for preventative maintenance during low production periods.
- Use PLC-based setpoints and interlocks to halt unsafe operating conditions. Safely clear jams.
- Control lubrication by monitoring consumption and topping up reservoirs. Adjust flow rates as necessary.
- Ensure operators are properly trained and adhere to all safety procedures. Supervise new hires until capable.
Consistent operation to proven parameters by skilled staff helps sustain maximum production of quality components.
Common Roll Formed Part Defects and Corrections
Defect | Possible Causes | Corrections |
---|---|---|
Burrs | Roll damage, web misalignment, crossbow | Dress or replace rolls, realign guides |
Wavy sections | Improper roll adjustment, worn rolls | Realign and pen passes, roll grinding/replacement |
Twist | Roll non-parallelism, coil bow | Realign bottom roll, improve coil quality |
Thinning | Excess roll penetration, gaps | Loosen roll pressure, shim gaps evenly |
Variable curl | Inconsistent roll adjustment | Incrementally adjust pass sequence |
Scratches | Grit on rolls, web contamination | Clean rolls, improve coil stock surface |
Carefully observe part features and adjust parameters systematically to resolve forming defects. Consult factory experts for troubleshooting difficult issues.
Roll Former Safety Considerations
Operating Farnham roll formers safely requires:
- Comprehensive training for all operators before running equipment. Review hazards.
- Ensuring adequate guarding around pinch points, gears, and coils.
- Lockout/tagout procedures for maintenance and jam clearing. Zero energy state.
- PPE including snug clothing, gloves, glasses, and hearing protection where loud. Enforce use.
- Clearly marking safety zones around the machine and defining access rules.
- Dust collection if needed to improve air quality in forming area.
- Alarms, signage, and policies prohibiting unauthorized modifications or disabling of safety systems.
- Regular safety reviews as part of maintenance inspections. Document corrective actions.
Farnham provides standard guarding packages but additional precautions may be warranted depending on operation.
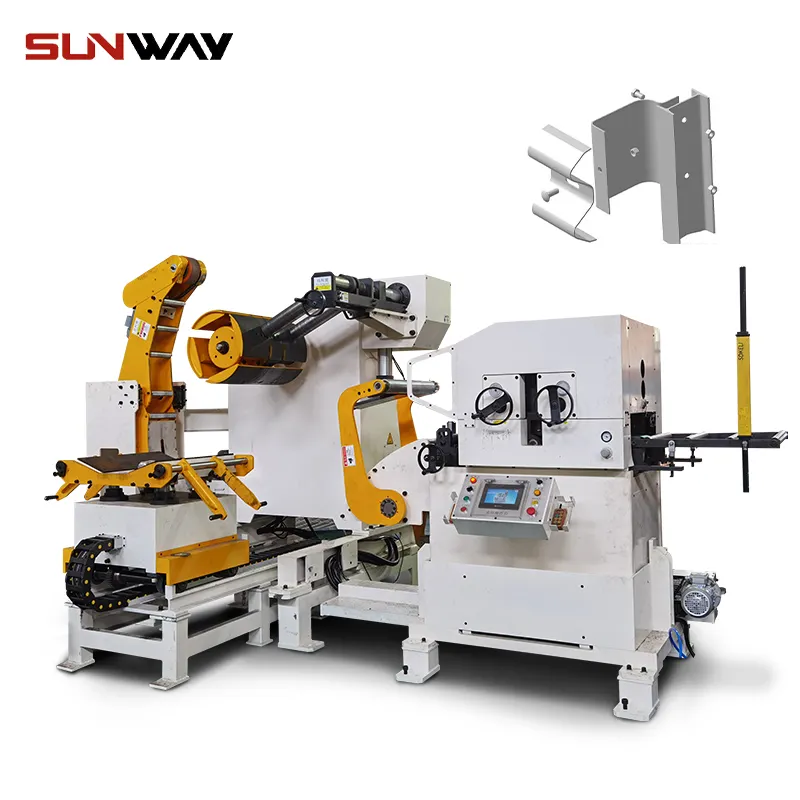
FAQs About Farnham Roll Forming Machines
Q: What types of materials can be roll formed on a Farnham machine?
A: Metals including steel, stainless steel, copper, and aluminum alloys are commonly formed. Material with good ductility and fitness for bending works best.
Q: How long does it take to set up tooling for a new part profile?
A: On Farnham quick change machines, typical setup time is 1-3 hours to swap roll sets and debug forming. More difficult profiles may take longer.
Q: What thickness range is typically run?
A: Standard Farnham models accommodate material thicknesses from 0.6 mm to 2.0 mm (24 ga to 14 ga). Special models can run heavier or thinner material.
Q: What factors affect roll former production speed?
A: Material thickness and hardness, part complexity, available horsepower, and desired quality determine maximum stable line speed. 50-200 ft/min is typical for roofing panels.
Q: How long are typical roll formed parts?
A: Part lengths up to 65 feet are possible depending on the roll former model and material. Lengths are set by part cutoff saws.
Q: What level of precision is possible with roll forming?
A: Roll formed parts can achieve dimensional tolerances around ±0.5 mm when processes are properly controlled and rolls maintained. Tighter tolerances become difficult.
Q: What safety practices are most important?
A: Training, guarding, lockout, PPE, marked safety zones, dust collection, safety reviews, and modification control are key precautions.
Q: How often does roll maintenance need to be performed?
A: Roll grinding or replacement is required on average every 1-3 months for typical high production roofing/siding lines during 24 hour operation.