Overview of c section c frame roll forming machine
C section C frame roll forming machines are used to produce structural steel members with a C-shaped cross section for the construction industry. The C section profiles provide excellent strength for framing applications.
This guide covers C frame roll former working principles, main components, specifications, production line configurations, tooling accessories, applications in construction and pre-engineering building, benefits, top manufacturers, cost analysis, purchasing considerations, maintenance tips and FAQs.
Working Principle of C Frame Roll Forming
The operating sequence of a C section C frame roll forming line is:
- Coil of steel sheet loaded into the de-coiler
- Sheet enters leveler machine for initial flattening
- Leveled sheet fed into the entry guides
- Sheet passes through sequential rolling stations
- Forming rollers gradually bend the steel sheet into C shape
- Finished C section exits on to the cutting table
- Cutter shears the profile to desired length
- Conveyor stacks cut parts for bundling
- Hydraulic motors coupled to gearboxes drive the roll stations
- PLC automated control synchronizes the components
The gradually bending steps produce uniform C sections with excellent surface finish and dimensional accuracy.
Main Components of C Frame Roll Former
Key components of a C section C frame roll forming machine include:
- De-coiler – Holds and feeds the steel coil
- Feeder – Feeds sheet into the line
- Leveler – Flattens sheet prior to forming
- Roll forming stations – Bend sheet in steps
- Roll tooling – Machined to C profile shape
- Cutting unit – Shears cut profiles to length
- Stacking table – Collects finished C sections
- Bundling system – Straps cut parts into bundles
- Electrical controls – PLC, HMI, AC drives
- Safety guarding – For operator protection
Precisely aligned components produce uniform, quality C sections.
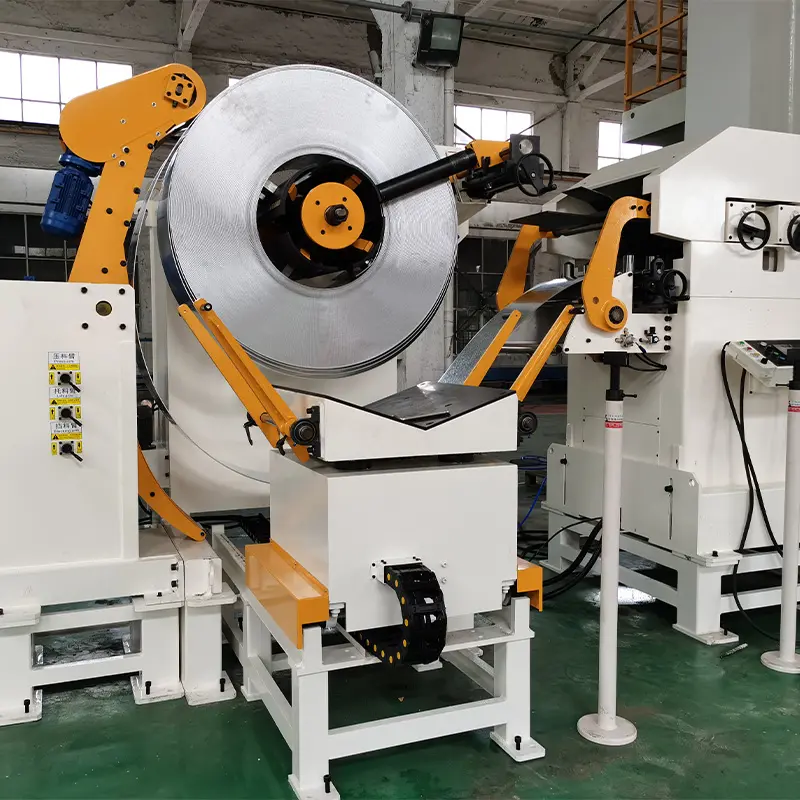
Specifications of C Frame Roll Formers
Typical specifications of C frame roll forming machines:
Parameter | Specification |
---|---|
Roller diameter | 100-180 mm |
Max. line speed | 35 m/min |
Min sheet thickness | 1.2 mm |
Max sheet thickness | 3 mm |
Sheet width | 750-1250 mm |
C section height | 100-300 mm |
Cut lengths | 2-12 meters |
Main motor | 11-55 kW |
Voltage | 380-415V, 50/60Hz, 3Phase |
Larger roller diameters allow forming heavier material. More powerful motors yield higher production rates.
Types of C Frame Sections Produced
Common C frame section sizes produced on these roll formers:
- C purlins – 100 to 300 mm
- Metsec Metric C sections – 2MC to 14MC
- A/HBox beams – All standard sizes
- Miscellaneous – Custom C profiles
Quick roll change systems allow various C section sizes to be interchanged easily.
C Frame Roll Former Configurations
Typical C frame roll former line configurations:
- Compact – Entry guides to cutter in one frame
- Modular – Separate modules bolted together
- In-line – Straight from one end to other
- L-shaped – Saves space
- Double decoiler – For quick coil change
- Closed-loop – Exits to coiler side
- Servo-electric – Precision servo motor drives
- Custom – Tailored layouts to needs
Layouts are designed to optimize material flow, space and production requirements.
Tooling Accessories for C Frame Rollers
Tooling enhancements for C frame roll forming machines:
- Quick change – Fast roll set swaps
- Punching – Hole punching attachment
- Embossing – Pattern rolls for decorative finishes
- Notching – Edge notching attachment
- Bending – Rails for bending into arcs
- Double sheet – Split rolls for dual sheets
- Roll protection – Guards against damage
- Roll ramps – Ease feeding of thick sheets
- Roll levellers – Ensure concentricity
Tooling expands the range of profiles and features possible.
Applications of C Frame Sections
Typical applications of C frame profiles:
- Roof joists – Rafters, purlins, eaves
- Wall studs – External and internal framing
- Structural supports – Columns, braces
- Mezzanine flooring – Platforms, walkways
- Building frames – Shell structure
- Trusses – Roof and floor truss chords
- Solar racking – Mounting structure members
- Shelving – Uprights, braces
- Stair stringers – Supports, handrails
C sections provide excellent strength-to-weight ratio for structural applications.
Benefits of C Frame Roll Forming
Key benefits of C frame roll forming lines:
- High productivity – Up to 35 meters per minute
- Material savings – Zero scrap from C-shaped structure
- Consistency – Dimensional accuracy better than other methods
- নমনীয় – Produce wide range of C sections
- Cost-effective – Lower investment than structural mill
- Compact – Small footprint, easy installation
- Safety – Fully enclosed guards for protection
- Sustainable – Major energy and carbon reduction
C sections produced on roll formers rival structural mills in quality and performance at a fraction of investment cost.
Leading Manufacturers of C Frame Roll Formers
Prominent global suppliers of C section C frame roll forming machines include:
- Cloudnine – Feature rich heavy-duty roll formers
- Zhongfu – Advanced German engineering standards
- Jupiter Roll Forming – Customized production lines
- RollMax – Precision C sections up to 550 mm
- Formtek – Servo-electric lines for speed and accuracy
- Gasparini – Robust Italian-made roll forming machines
Cost Analysis
Typical cost considerations for C frame roll forming lines:
- Type and size – Larger, automated lines cost more
- Speed and efficiency – Directly affects pricing
- Material thickness – Machines for thicker sheets cost extra
- Quick change features – Adds expense but saves time
- Additional tooling – Varies based on profiles needed
- Installation and training – Often included in price
- Freight and logistics – Extra depending on delivery location
Total Acquisition Cost – $80,000 to $500,000+
Higher production capability warrants bigger investment to maximize productivity gains.
Buying Considerations
Key factors to consider when buying C frame roll forming machines:
- Size and thickness range of C sections required
- Estimated production volume and annual output
- Level of automation features preferred
- Available installation space for the line
- Planned operating shifts per day
- Operator skill level and training needs
- Expected part dimensional precision
- Future tooling needs and line expansion
- Local technical support capability
Thoroughly analyzing present and future needs ensures ideal equipment selection.
Maintenance Tips
Recommended maintenance practices for C frame roll formers:
- Daily cleanup of metal debris and excess lubricant
- Checking oil levels in gearboxes and hydraulics
- Inspecting roll tooling condition and replacing worn items
- Verifying hydraulic seals, hoses, fittings are not leaking
- Confirming electrical wiring and connections are tight
- Monitoring belt tension and chains for stretch
- Testing emergency stop and safety circuits
- Documenting maintenance activities and part changes
Proper maintenance improves uptime, output consistency and operator safety.
Troubleshooting Common Problems
Troubleshooting tips for C frame roll forming issues:
Profile distortion
- Check roll alignment and spacing
- Replace any damaged or worn rolls
- Adjust roll pressure as needed
Cut sections out of alignment
- Check alignment of cutting blade
- Inspect sensor positioning
Uneven line speed
- Test servo motors and drives
- Check for slipping belts or chains
Hydraulic power loss
- Inspect cylinders, valves and pumps
- Check oil level and filter
- Tighten any leaking fittings
Machine jamming
- Increase lubrication
- Clear any debris in stations
- Verify no loose machine parts
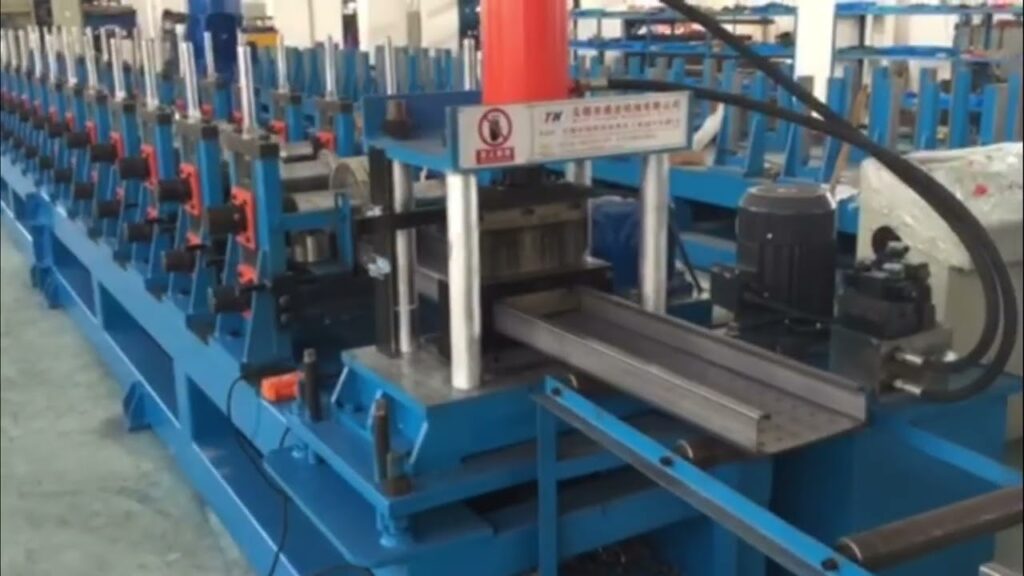
FAQs
What sizes of C sections can be produced?
Common ranges are 100 to 300 mm height, 1.5 to 3 mm thickness, and 750 to 1250 mm width capacities. Larger sizes are also possible.
What materials can the C frame roll former process?
Most commonly galvanized steel, also pre-painted steel, stainless steel or aluminum. Mild steel is the most cost-effective choice.
What thickness of sheets can be formed?
Standard C frame roll formers accommodate 1.2 to 3 mm material thickness. Special models for thicker sheets are available.
What is the typical output speed?
25-35 meters per minute is standard for most C frame roll forming lines. Speeds vary based on part size and features.
What length of C sections can be produced?
Standard roll former cutting lengths range from 2 to 12 meters. Extended lengths can be achieved by adding additional rolling stations.
উপসংহার
C section C frame roll forming lines deliver high precision structural steel profiles at productivity rates unmatched by other methods. When specifying C frame roll forming equipment, manufacturers must assess both current and future part needs in terms of sizes, thicknesses, volumes, and tooling flexibility. Investing in a roll former sized appropriately for production demand can yield rapid payback through material savings, reduced labor, and energy efficiency versus other fabrication approaches.