Slip roll forming machines are used to shape and bend metal sheets and plates into circular, conical, or cylindrical parts. This efficient technology transforms flat blanks into precisely formed components vital for manufacturing industries.
This comprehensive guide will provide a detailed overview of slip roll forming machine working principles, types, components, specifications, design factors, installation, operation, suppliers, costs, advantages, limitations, and more.
Introduction to Slip Roll Forming Machines
Slip roll forming, also known as pyramid roll forming, is a metal bending process that gradually curves sheet metal blanks into circular or conical shapes. The blank is progressively passed through three adjustable rollers to produce uniform bending without deforming the material.
As the blank enters the rollers, it takes on a curved profile. By adjusting the roller spacing and angle, different diameters and conical shapes can be formed. Slip roll forming provides efficient bending of sheets into rings, cones, elbows, and various geometric forms.
Key benefits of slip roll forming technology:
- Ability to make concentric bends and compound curves
- Form gradual contours without material deformation
- High dimensional accuracy and bend quality
- Minimal thinning and thickening of metal
- Applicable for wide range of materials and thicknesses
- Low setup times between different components
Based on configuration, different types of slip roll forming machines are available.
Major Applications of Slip Roll Forming Machines
Slip roll forming systems are ideal for high precision bending of sheets, plates, blanks into:
অ্যাপ্লিকেশন | বিস্তারিত |
---|---|
Round tubes and pipes | For structural and hydraulic uses Diameters from few inches to several feet |
Conical sections | For hoppers, bunkers, pipelines Gradual slopes |
Elbows and bends | For HVAC ducting Smooth contours |
Metal rings | Bearing races, flanges Circular and non-circular |
Rolled cylinders | Drums, storage tanks Large diameter cylinders |
Dished ends | For pressure vesselsSpherical profiles |
These components find wide applications in mechanical engineering, process equipment, infrastructure, and metal fabrication.
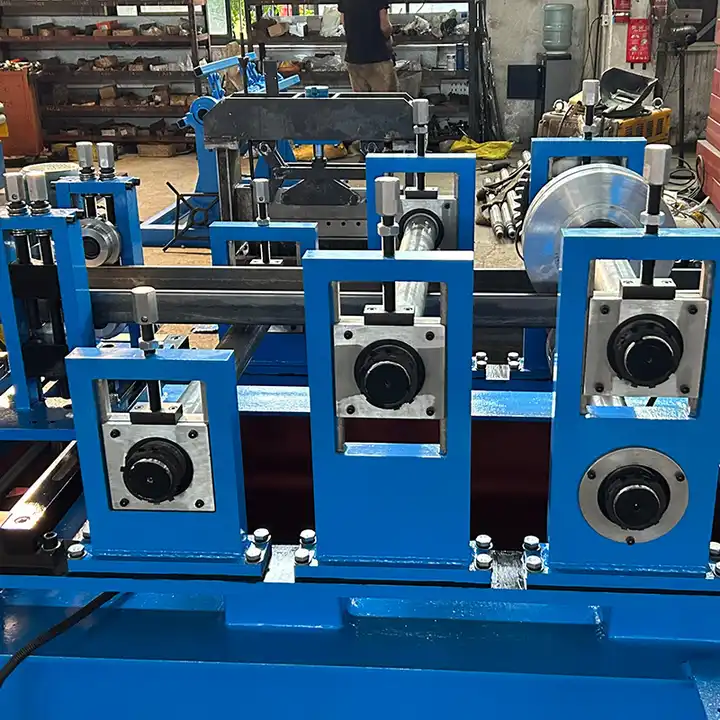
Types of Slip Roll Forming Machines
Slip roll forming machines are classified based on roller configuration:
Types | Description |
---|---|
Pyramid 3-roll | Three adjustable forming rolls Manual or power driven Basic design |
Pinch 4-roll | Four rolls for better control Motorized rolls Faster production |
Cluster 3-roll | Cluster of three adjustable rolls Independent lateral control For complex profiles |
CNC roller bender | CNC controlled rolls Precision bending Advanced features |
More rollers and CNC control allow complex shapes, higher precision, and efficient production.
Main Components of Slip Roll Forming Machines
Major components of slip roll forming systems:
Components | Function |
---|---|
Forming rolls | Bend sheet progressively |
Roll adjustment system | Adjust roll spacing, angle |
Sheet holding knobs | Grip sheet securely during bending |
Decoiler unit | Holds sheet coil for continuous bending |
Control panel | Controls machine operation |
Base frame | Provides rigid support |
Additional attachments like mandrels, gauges, and guides can be integrated for specialized bending applications.
Technical Specifications of Slip Roll Forming Machines
The main technical parameters for slip roll forming machines:
Specifications | Typical values |
---|---|
Maximum sheet width | 1 – 8 ft |
Minimum sheet thickness | 26 gauge (0.5 mm) |
Maximum sheet thickness | 1⁄4 – 1⁄2 inch (6 – 12 mm) |
Roll adjustment range | 1 – 10 inch spacing |
Roller diameter | 4 – 10 inches |
Roller drive | Manual or motorized |
Roll speed | 10 – 25 rpm |
Roller capacity | 3 – 20 tons |
Control | Manual or CNC |
The diameter, spacing, and drive capacity determine the size and thickness of metal that can be formed.
Design Aspects for Slip Roll Forming Machines
Key design factors for slip roll forming systems:
Design Factors | Description |
---|---|
Roller diameter | Affects minimum bending radius |
Roller adjustment | Range of diameter and taper |
Drive type | Power requirements |
Roller capacity | Sheet thickness and hardness |
Controls | Manual, semi-auto, CNC |
Automation level | Loading/unloading, part handling |
Added features | Mandrels, gauges, etc. |
Safety | Guards, emergency stops |
The machine is designed based on bending needs, material properties, precision, and production requirements.
Standards and Codes for Slip Roll Forming Machines
Slip roll forming equipment must comply with:
Standards | Description |
---|---|
ISO 9001 | Quality management system |
CE | Safety certification for Europe |
ANSI | Machine safety standards in USA |
ASTM | Metal properties and testing |
ASME | Design codes for roll frames |
These regulations ensure the equipment meets quality benchmarks and safety needs.
Installation of Slip Roll Forming Machines
Proper installation is vital for efficient functioning:
Installation Steps | Requirements |
---|---|
Site preparation | Flat, leveled flooring Enough working space Crane availability |
Positioning | According to layout drawings Align machine sections Anchor machine body |
Assembly | Assemble parts as per manual Check alignments Install safety guards |
Electricals | Power cable connections Earthing points Lighting |
Trial runs | Test functioning Set process parameters Initial sample runs |
Sufficient space is required for blank loading/unloading and formed part handling.
Operation and Maintenance of Slip Roll Forming Machines
Efficient functioning requires:
Operation | Maintenance |
---|---|
Skilled operators Safe material handling Set process settings Inspect formed parts | Daily cleaning Lubricate bearings Check belt tension Gearbox oil levels Replace worn parts |
Preventive maintenance activities as per schedule optimize performance.
How to Select a Slip Roll Forming Machine Supplier
Key factors for choosing reliable equipment suppliers:
Parameter | Criteria |
---|---|
Machine range | Models matching requirements |
Production capacity | Required output rates |
কাস্টমাইজেশন | Flexibility for special profiles |
Quality | ISO certified manufacturing |
অভিজ্ঞতা | Years in business, clientele |
Expertise | Technical support for design |
After-sales service | Installation, training, maintenance |
Spare parts | Availability of wear parts |
Pricing | Competitive and transparent |
Select a technologically capable manufacturer who can provide the right solution.
Costs of Slip Roll Forming Machines
Typical price range:
Machine Type | Price Range |
---|---|
Manual 3-roll pyramid | $5,000 – $15,000 |
Powered 4-roll pinch | $15,000 – $35,000 |
CNC cluster roll bender | $50,000 – $150,000 |
Fully automatic line | $200,000+ |
Costs vary based on roll capacity, automation level, precision, and overall capabilities.
Pros and Cons of Slip Roll Forming Machines
Advantages | Limitations |
---|---|
Gradual uniform bending No material deformation Dimensional accuracy Low setup times High flexibility | Higher initial investment Size limits per machine Skilled labor needed Large space requirement Lower speeds than press brakes |
Automated slip roll forming improves efficiency and quality but requires significant capital expenditure initially.
FAQs about Slip Roll Forming Machines
Question | Answer |
---|---|
What materials can be formed? | Low carbon steel, stainless steel, aluminum, copper alloys |
What are the size limits? | Up to 8 ft wide sheets, 1/4 – 1/2 inch thick |
What profiles are possible? | Circles, cones, elbows, dished heads |
What motors are used? | AC induction motors typically |
What controls are used? | Manual, semi-automatic, CNC |
What maintenance is required? | Daily cleaning, lubrication, and wear parts replacement |
What safety aspects are needed? | Guards, emergency stops, safety mats |
What floor space is optimal? | Around 400 sq.ft for a standard machine |
What affects the machine cost? | roller capacity, level of automation, precision |
উপসংহার
Slip roll forming machines enable efficient bending of metal sheets and plates into circular or conical shapes to high dimensional accuracy. With the ability to form various profiles without deformation, they are ideal for rolling rings, tubes, vessel heads, elbows, and custom components.
Choosing the right roller capacity and features based on part sizes and production needs is important. With competitive pricing, slip roll forming improves quality and productivity for metal fabrication industries.