Strut channel roll forming machines are used to form metal coil into C-shaped strut channels, which have a wide variety of structural applications. This comprehensive guide provides an overview of strut channel roll former equipment, including types, components, specifications, and suppliers. It also covers key considerations for application, installation, operation and maintenance.
Overview of Strut Channel Roll Forming Equipment
Strut channel roll forming machines take flat metal coil stock and form it into U-shaped or C-shaped channels through a series of bending and forming rollers. The continuous channels produced are used for structural framing, supports, braces and studs in construction, racks, scaffolding, trailers, greenhouses, solar panel mounting and more.
Key benefits of using a strut channel roll former include:
- Highly customizable and adjustable channel dimensions
- Efficient, automated production of continuous channel lengths
- Consistent quality and structural strength of formed channels
- Versatile for small, medium or large production requirements
- Cost-effective compared to other forming methods
Strut channel profiles are available in various sizes like 1-5/8”, 2”, 2-1/2″, 3″, 4″, 6″ as per application needs. Common materials used are low carbon steel, galvanized steel and stainless steel in gauges from 16 gauge to 11 gauge.
Types of Strut Channel Roll Forming Machines
Roll Former Type | Description |
---|---|
Manual | Basic machines for small scale production. Require manual feeding and cutting of channels |
Semi-automatic | Have powered forming rollers but require manual feeding of coil |
Fully Automatic | Have powered decoilers, feed tables, forming sections and cut-offs for automated production in a line |
CNC Roll Former | Feature computer numerical control for precision forming and quick changeovers between sizes |
Custom Roll Former | Tailor made to specifications with special forming rollers, controls, speeds etc. |
Main Components of a Strut Channel Roll Former
Component | Function |
---|---|
ডিকয়লার | Holds and uncoils the flat sheet metal coil stock |
Feed Table | Feeds coil into forming section at set speed |
Forming Rollers | Progressively bend and form the coil into channel shape |
Punching Units | Optional for creating holes as per profile design |
Cutoff Knife | Cuts formed channels to length as per product dimensions |
Support Roll Stands | Provide structural support for forming rollers |
Controls | Set and monitor forming parameters like speed, feed, length etc. |
Conveyor | Catches and transports finished channels for storage or packing |
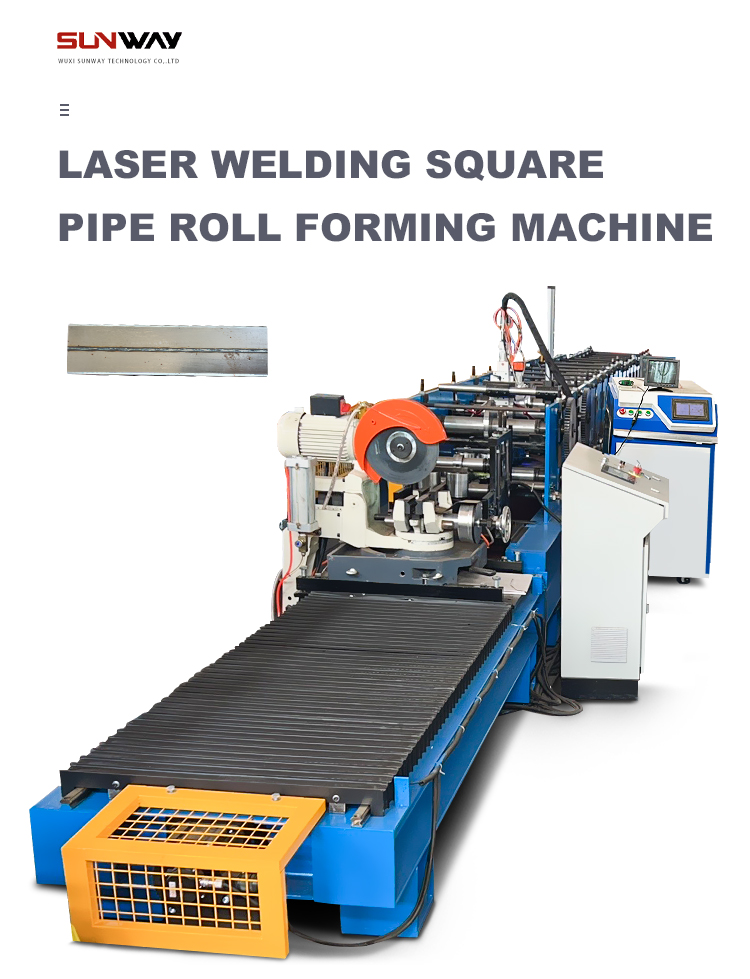
Strut Channel Roll Former Specifications
The key specifications to consider for strut channel roll forming machines include:
Production Speed and Efficiency
Speed Range | Up to 16 feet/min for manual and 100 feet/min for fully automatic roll formers |
---|---|
Coil Width Capacity | Up to 72 inches |
Coil Weight Capacity | Up to 6000 lbs on decoiler |
Formed Channel Length | 6 ft to 24 ft as per cutoff settings |
Roller Power | Up to 20 HP |
Forming Adjustability and Precision
Forming Stations | 10 to 16 progressive bending and forming stations |
---|---|
Roller Diameter | 3 to 5 inches based on channel size |
Roller Adjustability | +/- 0.5 mm for precision channel dimensions |
Roller Hardness | D65 hardened steel rollers |
Forming Accuracy | Within +/- 1 mm of designed profile |
Construction and Durability
Framework | Heavy duty welded steel frames |
---|---|
Sheet Thickness Capacity | Up to 3.2 mm (11 ga) steel sheets |
Machine Weight | 9000 to 25000 lbs depending on model |
Paint Coating | Primer + powder coated paint |
Safety Features | Emergency stops, guarding |
Applications and Uses of Strut Channels
Strut channel profiles produced by roll forming have extensive structural uses across industries:
Construction and Infrastructure
- Building and roof framing
- Scaffolding, shoring systems
- Tower and pole support structures
- Conveyor support systems
- Mezzanine flooring, platforms
Material Handling
- Racking, shelving
- Conveyor framing
- Crane beams
- Warehouse partition framing
Transport
- Truck, trailer framing
- Container frames
- Railway freight structures
Energy
- Solar panel mounting structures
- Pipe support frames
- Wind turbine interior frames
Other Applications
- Greenhouses, polyhouses
- Machinery frames, guarding
- Stage, event structures
- Signage and billboard frames
- Gym, storage shelving
With customized hole punching and bracket insertion, the possible uses of roll formed strut channels are endless!
Choosing Strut Channel Roll Forming Equipment
Selecting the right strut channel roll former involves balancing production needs, part specifications, sizes, budgets and other factors.
Key Considerations for Equipment Selection
Factor | বিস্তারিত |
---|---|
Production Volume | Match speed, automation level and output to hourly/daily needs |
Channel Sizes | Confirm machine can produce required widths and depths |
Material Thickness | Check capacity for forming sheet gauge needed |
Adjustability | Precision rollers for quick size changeovers preferred |
Custom Options | Hole punching, notching, embossing needs |
Budget | Compare initial cost vs production efficiency benefits |
Lead Time | Production urgent or can wait for delivery? |
Space Available | Dimension constraints for new equipment |
পাওয়ার সাপ্লাই | Sufficient electrical load capacity? |
In summary, analyze current and future production needs, type of parts needed, available budget and factory constraints before investing in a strut channel roll former. Getting the key parameters right ensures the machine matches requirements and provides maximum ROI.
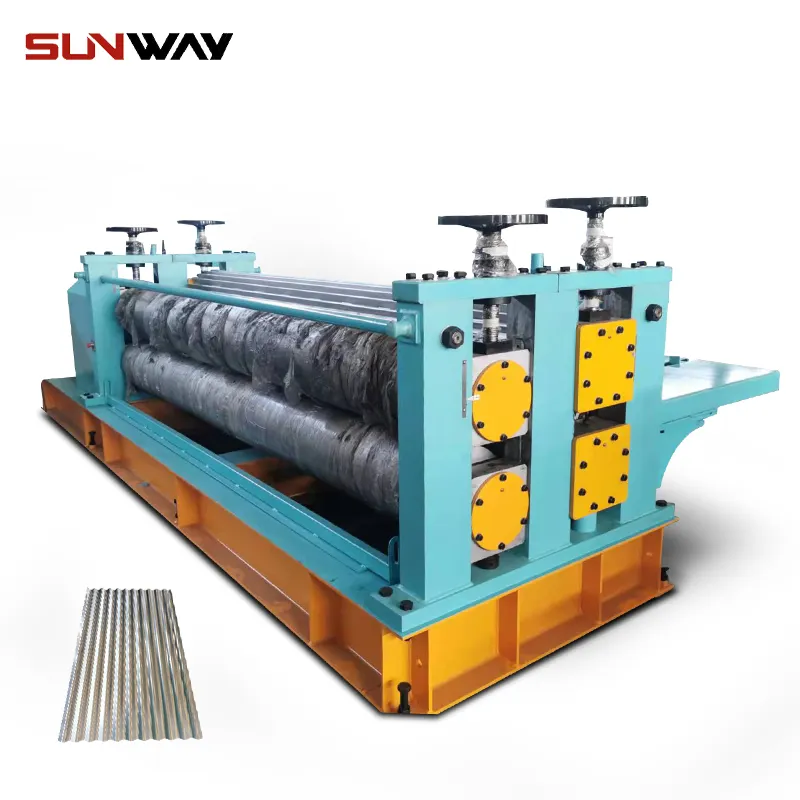
Top Strut Channel Roll Forming Machine Manufacturers
There are many established global suppliers producing quality strut channel roll forming equipment. Some top manufacturers to consider include:
Top Strut Channel Roll Former Brands
ব্র্যান্ড | Locations Served |
---|---|
Dimeco | North America |
Peddinghaus | USA |
Formtek | USA |
Shanghai Etco | China |
Shandong U-Nova | China |
Jouanel Industrie | ফ্রান্স |
Gasparini | ইতালি |
FACCIN | Brazil |
These industry leaders supply machines worldwide and can provide guidance on selecting the right strut channel roll former based on part parameters and production needs. Most offer customization options as well. Reputed manufacturers also provide superior after-sales service support.
Strut Channel Roll Former Price Ranges
Strut channel roll forming machine prices depend on many specifications and can range widely:
Strut Channel Roll Former Cost Considerations
Machine Type | Typical Price Range |
---|---|
Manual Roll Former | $8,000 to $15,000 |
Semi-Automatic Machine | $15,000 to $35,000 |
Fully Automatic Roll Former | $50,000 to $120,000 |
CNC Roll Former | $80,000 to $250,000 |
Custom Roll Former | $100,000+ (application specific) |
The major factors affecting strut channel roll forming equipment cost are:
- Automation level and speed
- Production output rate
- Overall size and roller capacity
- Precision and adjustability features
- Optional customizations like hole punching
- Reputation and quality of manufacturer
Requesting quotes from shortlisted suppliers based on your production requirements is the best way to estimate actual machine costs.
How to Install a Strut Channel Roll Former
Proper installation is key to maximizing the performance of a strut channel roll forming system. Here are some best practices:
- Prepare suitable foundation – level concrete or bolted structural base
- Position machine with enough space around for safe operation
- Lifting equipment may be needed for larger roll former placement
- Align and bolt down machine securely on foundation
- Connect electric power supply and confirm voltages
- Install decoiler, feed table, other unattached components
- Check and set machine parameters – speed, roller gaps etc.
- Test run the roll former and make any adjustments
- Organize the coil loading and finished product offloading flow
Taking the time to correctly install the strut channel roll forming line saves time and prevents issues in the long run. Always follow the manufacturer’s specific guidelines as well.
How to Operate a Strut Channel Roll Former
Learning to properly operate a strut channel roll forming machine maximizes output while minimizing errors and safety risks. Key operation tips:
- Understand the entire forming process flow from decoiler to finished cut channels
- Load coils of the correct width onto the decoiler using overhead crane
- Set forming speed, feed rate and cut length as per product dimensions
- Adjust roller gaps and alignment for precise channel forming
- Monitor strip feed, folding and cutoff operation as it runs
- Inspect quality of initial formed channels and adjust as needed
- Organize efficient offloading of finished product from the line
- Maintain cleanliness around equipment during operation
- Follow all safe working practices provided by manufacturer
With experience, operators learn how to fine-tune an strut channel roll former to produce perfect quality profiles every time.
Strut Channel Roll Former Maintenance
Regular preventative maintenance ensures continuous smooth functioning of strut channel roll forming equipment. Key maintenance tasks:
- Clean machine daily, clear dirt and metal debris
- Lubricate bearings, gears, chains according to schedule
- Check bolts, guards, connections are tight
- Monitor rollers and other wear parts, replace as needed
- Change hydraulic oils and filters periodically
- Inspect electrical wiring for damage
- Confirm emergency stop buttons functional
- Test and calibrate sensors, controls
- Check decoiler arm, brake and strip alignment
- Repair or replace any damaged or worn parts
Plan maintenance shut downs during production breaks. Keep spare parts inventory. Record all maintenance for tracking.
Properly maintained strut channel roll formers operate reliably for decades.
How to Select a Strut Channel Roll Former Manufacturer
Picking the right supplier is crucial when investing in a strut channel roll forming machine. Key selection criteria:
Factors to Consider in a Roll Former Manufacturer
Criteria | What to Look For |
---|---|
Product Quality | Proven reputation, customer reviews, quality certifications |
Reliability | Years in business, strong client base |
কাস্টমাইজেশন | Flexibility to build as per your specifications |
Design Expertise | Solutions to fit production requirements |
Manufacturing Capability | Modern plant, machining and fabrication capacity |
Service Record | Responsiveness to issues, professional support |
Pricing | Competitive pricing for features and production capacity |
Take the time to thoroughly evaluate multiple manufacturers before deciding on the best roll former supplier for your production needs and budget.
Advantages and Limitations of Strut Channel Roll Formers
Key Benefits of Strut Channel Roll Forming Lines
- Highly customizable and adjustable channel profiles
- Automated operation for speed and efficiency
- Consistent quality and structural integrity
- Lower cost than alternate forming methods
- Minimal material waste from coiled raw material
- Flexible production volumes from low to high
- Long lifespan exceeding 20 years
Potential Limitations to Consider
- High initial machine purchase cost
- Regular maintenance required
- Skill needed to set up and operate
- Size limits based on model specifications
- Not ideal for low volume or prototype parts
- Can require plant space and infrastructure
When utilized for suitable applications and production scale, strut channel roll formers provide excellent ROI through continuous, efficient forming of top-quality metal channels.
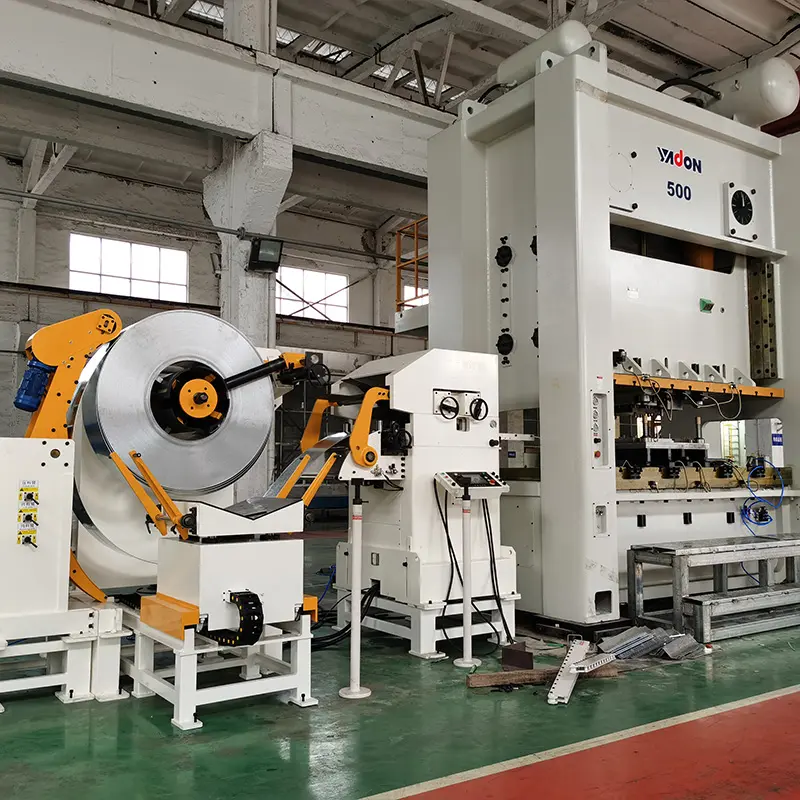
FAQ
Strut Channel Roll Former FAQs
Q: What sizes of strut channel can be formed on these machines?
A: Common strut channel sizes from 1-5/8″ up to 8″ width can be produced, depending on machine capacity. Channel depth is adjustable as well.
Q: How long does it take to changeover to run a different size channel?
A: On automated CNC machines with precision rollers, size changeover takes 15-30 minutes. For manual machines, it may take 1-2 hours.
Q: What power supply do strut channel roll formers require?
A: Most industrial roll formers require a 380V to 480V, 3 phase power supply. Exact voltage and amps depend on the machine motor size.
Q: What is the typical production rate of strut channel roll formers?
A: Production rates range from 10 ft/min on manual machines to 100 ft/min on high speed automated lines, depending on model.
Q: How should finished strut channels be handled and stored?
A: Use non-marring slings and avoid dropping. Store on racks in clean, dry area to prevent damage.
Q: What safety measures are recommended for strut channel roll former operation?
A: Install machine guards, employee PPE, safety mats, and follow lockout/tagout procedures. Only trained personnel should operate.
Q: Should strut channels be painted or coated after roll forming?
A: Yes, applying paint or zinc galvanization is recommended to protect from corrosion over time.
উপসংহার
Strut channel roll forming provides an ideal processing method to efficiently mass produce cold formed metal channels with high dimensional accuracy, finish quality and structural strength.
This detailed guide summarizes all the vital information needed – from types of machines and technical specifications to practical benefits, applications, operation, maintenance and selection criteria.
Whether you are looking to purchase your first strut channel roll former or add capacity to existing lines, this overview helps identify the optimum equipment configuration and manufacturer for your production scale, part parameters and business needs.
With these insights, manufacturers can utilize strut channel roll forming technology to gain significant competitive advantages in construction, infrastructure, material handling, transportation and diverse industrial markets.