Машины для формовки софитов являются необходимым оборудованием для производства металлических кровельных панелей, стеновых панелей, водосточных систем и различных других строительных изделий. В этом подробном руководстве представлен подробный обзор рулонных формирователей софитов: их работа, типы, основные характеристики, применение, установка, эксплуатация, обслуживание, поставщики, цены и многое другое.
Обзор оборудования для формовки софитов
Машины для формовки рулонов софитов, также известные как линии формовки рулонов, предназначены для преобразования рулонов металла в индивидуальные профили панелей путем прохождения их через последовательные формовочные станции. Станции формовки постепенно изгибают полосу до нужного профиля поперечного сечения.
Рулонные панели обеспечивают эффективные, легкие и экономичные варианты кровли и облицовки для современного строительства. Линии рулонного формования производят панели в непрерывном режиме, что обеспечивает высокую производительность по сравнению с другими производственными процессами.
К основным преимуществам использования рулонных софитов относятся:
- Высокоавтоматизированное и эффективное производство панелей большой длины
- Возможность создания сложных и настраиваемых профилей
- Постоянное качество и точность размеров панелей
- Низкие затраты на оснастку по сравнению с другими процессами
- Минимальные отходы материалов
- Снижение затрат на материалы и рабочую силу в расчете на одну деталь
- Гибкие объемы производства
Рулонная формовка софитов позволяет компаниям удовлетворять растущий спрос на металлические панели на рынках жилых, коммерческих и промышленных зданий.
Как работают машины для формовки софитов?
Принцип работы заключается в разматывании металлической ленты с рулона, прохождении ее через ряд последовательных формовочных станций с прецизионными роликами и постепенной холодной формовке ленты в требуемый профиль панели.
Основные компоненты линии по производству софитов включают в себя:
- Разматыватель: Подача ленты из рулона в валкообразователь
- Механизм подачи: Протягивает полосовую ленту через станцию формирования валков с соответствующей скоростью
- Станции формовки: Последовательная гибка полосы по профилю панели с помощью прокатных штампов
- Перфоратор: При необходимости пробивает отверстия для смещения панелей
- Пресс для резки: Разрезает панели на отрезки заданной длины
- Вспомогательные элементы: Направляющие, управление контуром ленты, устройства и т.д.
Полоса подвергается пластической деформации при прохождении через каждый ролик без нагрева материала. Прокатные штампы проникают в металл на небольшую глубину, что позволяет избежать разрушения материала. Правильное согласование скорости подачи с различными станциями имеет решающее значение для качественной формовки профиля.
Рулонные формирователи софитов обычно может обрабатывать рулоны стали толщиной от 0,4 мм до 2 мм и шириной до 1250 мм. Скорость линии составляет от 10 до 25 метров в минуту в зависимости от профиля.
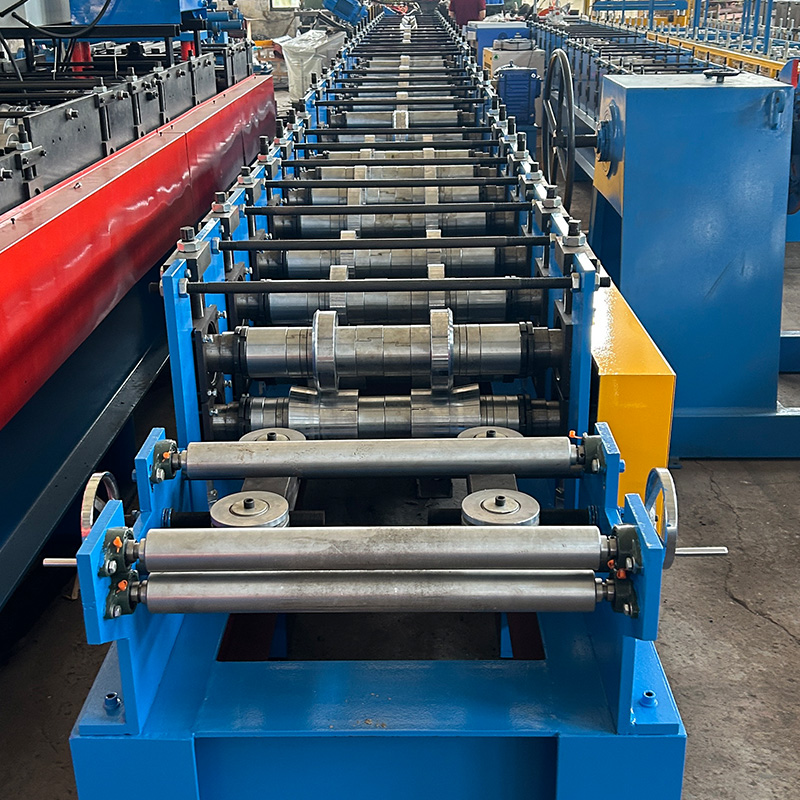
Типы машин для формовки софитов
Существует два основных типа оборудования для формирования софитов:
Формирователь софитов типа C
Это наиболее распространенный тип с С-образными станциями вертикальной формовки, расположенными в линейной конфигурации. Полоса проходит горизонтально от разматывателя через станции по прямой линии.
Преимущества:
- Компактная компоновка
- Более низкая стоимость
- Более простая обработка материалов
- Простота эксплуатации и обслуживания
Ограничения:
- Ограниченные возможности профиля
- Не подходит для применения в условиях высокой грузоподъемности
Формирователь софитов O-Type
В этой конструкции прокатные штампы установлены в О-образных станциях, через которые полоса проходит вертикально по U-образной траектории.
Преимущества:
- Возможность производства более сложных и высокопрочных панелей
- Большие диаметры валков обеспечивают большую силу изгиба
- Лучший контроль над натяжением и толщиной ленты
Недостатки:
- Требует больше места на полу
- Более высокая стоимость
- Обработка материалов стала более сложной
Рулонные формовщики гибридного типа
Некоторые современные линии прокатки сочетают в себе станции типа C и O, чтобы получить лучшее из обеих конструкций. Начальные станции могут быть С-типа для предварительной гибки, в то время как более поздние клети - О-типа для окончательного профилирования.
Основные характеристики станков для формовки софитов
Основные параметры и характеристики, которые необходимо учитывать при выборе рулонного устройства для софитов, включают в себя:
Таблица 1: Основные характеристики машин для формирования софитов
Технические характеристики | Типовые значения |
---|---|
Скорость производства | 10 - 25 м/мин |
Мощность по толщине металла | 0,4 - 2 мм |
Ширина полосы | До 1250 мм |
Минимальный радиус окончательного изгиба | 1-2 x толщина металла |
Количество роликовых станций | 15 - 20 стендов |
Мощность главного привода | 15 - 45 кВт |
Диаметр ролика | 150 - 250 мм |
Регулировка роликов | +/- 5 мм |
Формовочное усилие на станцию | До 400 кН |
Высота линии | 2000 - 2500 мм |
Длина машины | 15 - 25 m |
Скорость производства, размеры полосы и мощность линии должны быть подобраны в соответствии с требуемым размером панели, толщиной металла, формой профиля и объемом производства.
Основные области применения оборудования для формовки софитов
Линии прокатки софитов позволяют эффективно производить широкий спектр металлических панелей со специализированными сечениями. Типичные области применения включают:
Таблица 2: Основные области применения рулонных машин для формирования софитов
Продукция | Описание |
---|---|
Кровельные панели | Трапециевидные, гофрированные, коробчатые, ступенчатые и т.д. кровельные профили |
Стеновые панели | Декоративные, изолированные, структурные стеновые панели |
Облицовки | Для крыш, стен, парапетов и т.д. |
Рамы для солнечных батарей | U-образные профили для солнечных батарей |
Стальной настил | Для мезонинных полов, опалубки и т.д. |
Стальные шпильки | С- и U-образные профили в качестве элементов конструкции |
Металлическая черепица | Взаимосвязанные панели, напоминающие глиняную черепицу |
Дверные панели | Профилированные металлические двери, перегородки |
Дорожные изделия | Шумозащитные панели, панели для железнодорожных вагонов и т.д. |
Усовершенствованные конструкции оснастки позволяют рулонным линиям производить сложные асимметричные и тисненые профили панелей.
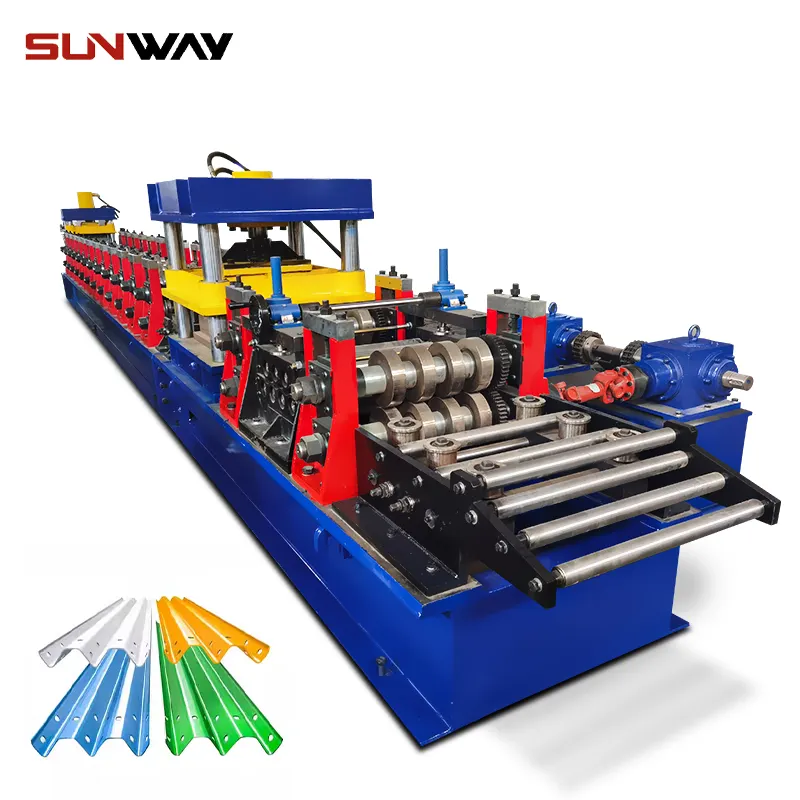
Как спроектировать линию для формовки софитов?
Проектирование эффективной системы рулонного формирования софитов требует большого инженерного опыта. Основные этапы включают:
- Оценка чертежей и спецификаций продукции
- Выбор материала и оптимизация толщины
- Определение технологического процесса, количества стендов и типа станций
- Проектирование прокатных штампов и оснастки для каждой станции
- 3D-моделирование и моделирование процесса формования
- Анализ напряжений в полосе с помощью программного обеспечения FEA
- Конструирование рамы машины, приводов и систем обработки ленты
- Интеграция защитных блокировок и элементов управления
- Заводские приемочные испытания перед отгрузкой
Конструкция оснастки имеет решающее значение для предотвращения таких дефектов, как пружинящая спинка, скручивание и трещины в готовых панелях. Правильная последовательность формовки и профили штампов должны быть разработаны с учетом характеристик материала и формы изделия.
Как выбрать подходящего поставщика оборудования для формовки софитов?
Поскольку на рынке представлено множество производителей валковых машин, выбор надежного поставщика является жизненно важным для получения высококачественного оборудования. Вот ключевые факторы, которые необходимо учитывать:
Таблица 3: Как выбрать подходящего поставщика оборудования для формирования софитов
Параметры | На что обратить внимание |
---|---|
Техническая экспертиза | Обширное ноу-хау в области проектирования валковой оснастки, технологического инжиниринга |
Опыт | Доказанный послужной список ранее выполненных проектов |
Производственные мощности | Современный завод, обрабатывающие центры, контроль качества |
Настройка | Возможность изготовления специализированной оснастки и проектирования линий |
Дизайн рулона | Новейшие технологии 3D-моделирования и FEA-симуляции |
Послепродажное обслуживание | Поддержка при установке, обучение операторов, контракты на техническое обслуживание |
Сертификаты | ISO 9001 и другие международные стандарты качества |
Отзывы покупателей | Отзывы о предыдущих проектах по формовке валков |
Линейные испытания | Возможность пробной аренды перед покупкой |
Предпочтение следует отдавать авторитетным производителям, предлагающим индивидуальные разработки, качественное оборудование и надежное послепродажное обслуживание. Рекомендуется посещать объекты и проверять рекомендации.
Цены на оборудование для формовки софитов
Цены на валковые машины значительно варьируются в зависимости от скорости производства, ширины линии, количества станций, типа оснастки и уровня автоматизации. Типичные ценовые диапазоны составляют:
Таблица 4: Диапазон цен на оборудование для формирования софитов
Технические характеристики | Диапазон цен |
---|---|
Макс. Ширина: 1000 мм <br> Скорость: 15 м/мин | $40,000 – $60,000 |
Макс. Ширина: 1250 мм <br> Скорость: 18 м/мин | $55,000 – $80,000 |
Максимальная ширина: 1500 мм <br> Скорость: 25 м/мин | $75,000 – $120,000 |
Максимальная ширина: 1500 мм <br> Скорость: 40 м/мин | $150,000 – $250,000 |
Крупные валковые формовщики О-типа с высокой грузоподъемностью и скоростью производства могут стоить более $300 000. Сложная оснастка, разматыватели, системы отрезания и автоматизация увеличивают общую стоимость линии.
Как установить станок для формовки софитов?
Правильная установка крайне важна для бесперебойной работы линии прокатки. Вот несколько основных рекомендаций:
- Подготовьте фундамент и пол к нагрузке на машину
- Обеспечьте достаточное пространство для безопасного перемещения оператора по линии
- Подъем и размещение оборудования с помощью кранов/вилочных погрузчиков
- Монтаж и выравнивание машин на фундаменте
- Сборка и выравнивание валковой оснастки на станциях
- Установка оборудования для подачи и направления ленты
- Подключение гидравлических, электрических и контрольных панелей
- Интеграция с разматывателем, ножницами, укладчиком и т.д.
- Пробные партии для подтверждения качества профиля перед полным производством
Поставщик должен предоставить руководство по установке, содержащее пошаговые процедуры, меры предосторожности и контрольные списки проверок.
Как управлять линией для формовки софитов?
Для безопасной и оптимальной работы вальцовых станков очень важны обученные операторы. Основные правила эксплуатации включают:
- Понимание процесса формовки, координация скорости линии
- Управление разматывателем, подающим устройством, пуансоном и отрезным прессом
- Контроль выравнивания полосы на каждой станции
- Проверка качества формованных панелей
- Оптимизация параметров технологического процесса для уменьшения количества дефектов
- Правильная обработка и укладка готовых панелей
- Соблюдение стандартных процедур безопасности
- Периодическое обслуживание и регулировка валов
- Сообщайте о любых аномальных шумах, вибрациях или неисправностях
- Регистрация производственных данных для анализа
Поставщик предоставляет руководства по эксплуатации для всей линии с подробным описанием процедур запуска, остановки, устранения неисправностей, технического обслуживания и техники безопасности.
Рекомендации по техническому обслуживанию машин для формовки софитов
Чтобы максимально увеличить время работы и продлить срок службы оборудования, необходимо регулярно проводить профилактическое обслуживание валковых формовочных машин:
Ежедневно:
- Очистка полосы от мусора и пыли
- Проверка уровня смазки
- Осмотр фильтрующих элементов
- Контроль утечек масла, температуры
Еженедельно:
- Подтягивание ослабленных деталей и крепежных элементов
- Проверка натяжения и выравнивания ремня
- Проверка состояния валков и зазоров
Ежемесячно:
- Смазка подшипников и поверхностей скольжения
- Проверка гидравлического масла
- Замена изношенных роликов/подшипников
- Функциональное тестирование блокировок и тормозов
Ежегодно:
- Замена масла в коробке передач
- Замена гидравлических шлангов
- Проверка электропроводки
- Проверка центровки, калибровка
- Шлифование валков или жесткая шлифовка
В руководстве по обслуживанию поставщика содержатся подробные графики и процедуры профилактического обслуживания.
Как выбрать правильную машину для формовки софитов?
Выбор оптимального устройства для изготовления софитов включает в себя учет ключевых факторов:
Таблица 5: Как выбрать подходящую машину для формовки софитов
Параметры | Руководство |
---|---|
Дизайн продукта | Оцените размер, форму, толщину, прочность панелей. |
Объем производства | Определите месячное/годовое количество для планирования мощностей |
Скорость линии | Высокая скорость до 25 м/мин для больших объемов |
Пропускная способность по ширине | Максимальная ширина рулона в зависимости от размеров изделия |
Количество станций | Для сложных профилей требуется больше станций |
Инструментальный материал | Прочные материалы, такие как сталь D2, обеспечивают долгий срок службы |
Потребности в автоматизации | Размотчик, штабелер, конвейеры для сокращения трудозатрат |
Мониторинг линии | SCADA для мониторинга производственных данных |
Послепродажная поддержка | Контракты на установку, обучение, техническое обслуживание |
Бюджет | Сравните цены разных поставщиков |
При выборе учитывайте как текущие, так и будущие производственные потребности. Для получения оптимального решения по формовке валков рекомендуется сотрудничать с экспертным поставщиком.
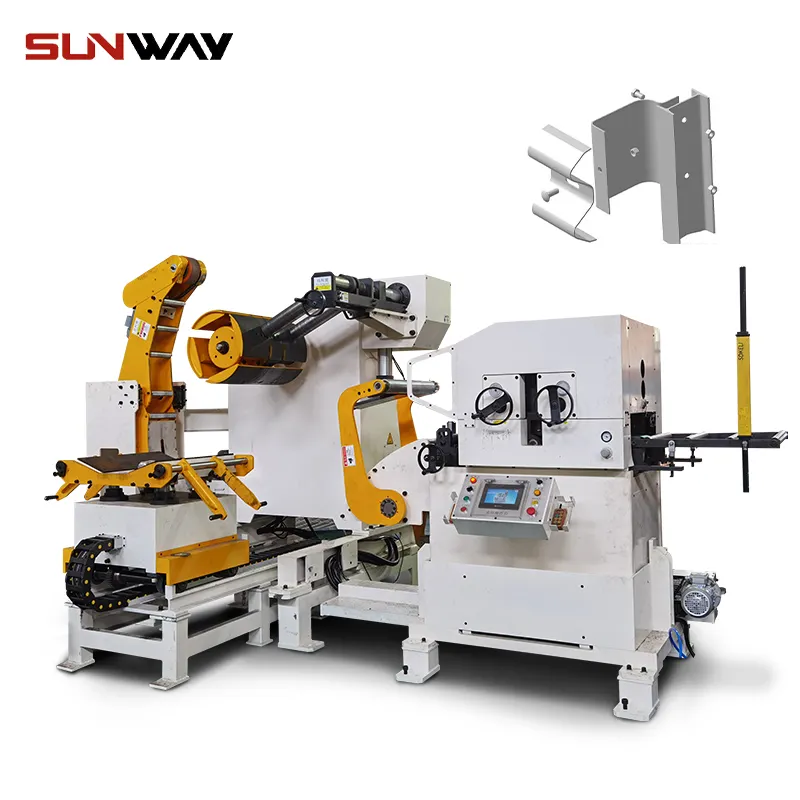
Плюсы и минусы станков для формовки софитов
Преимущества
- Высокоэффективное непрерывное производство
- Возможность создания сложных пользовательских профилей
- Постоянное и превосходное качество продукции
- Низкие эксплуатационные расходы на одну панель
- Возможность производства точно в срок
- Минимальные потери материала
- Быстрая переналадка между профилями
- Компактность оборудования
Ограничения
- Высокая первоначальная стоимость инвестиций
- Требуется тщательная разработка оснастки
- Требуются квалифицированные операторы
- Требуется регулярное обслуживание валов
- Ограничивается мягкими металлами, такими как сталь, алюминий
- Не идеальны для малосерийного производства
Часто задаваемые вопросы
Вопрос: Какой толщины металлический лист может быть подвергнут прокатке?
О: Большинство роликовых формовщиков могут обрабатывать рулоны металла толщиной от 0,4 мм до 2 мм. Некоторые тяжелые машины могут формировать полосы толщиной до 3 мм.
Вопрос: Как долго служит вальцовочная машина?
О: При надлежащем уходе и эксплуатации срок службы валковой машины обычно составляет 15-20 лет и более. Срок службы зависит от условий эксплуатации, качества обслуживания и условий окружающей среды.
В: Какие аспекты безопасности следует учитывать?
О: Ключевые элементы безопасности включают кнопки аварийной остановки, световые завесы на входе и выходе, защиту от защемления, блокировку дверей, замки для обслуживания роликов и обучение операторов.
В: Как быстро можно заменить валковую оснастку?
О: На хорошо спроектированных валковых формовщиках время замены оснастки для валков обычно составляет 1-3 часа. Быстрая смена оснастки сводит к минимуму время простоя между прогонами различных профилей.
В: Можно ли с помощью валкообразователя изготавливать конические прямоугольные профили?
О: Да, благодаря независимой регулировке кромочных роликов можно получить прямоугольный профиль с различной шириной по всей длине. Для предотвращения блуждания полосы используются специальные направляющие.
Вопрос: Какой должна быть отделка поверхности панелей, изготовленных методом роликовой формовки?
О: Детали, изготовленные методом рулонного формования, обычно имеют чистовую отделку, пригодную для последующих процессов, таких как окраска или ламинирование. При необходимости критические поверхности могут быть обработаны щеткой.
Вопрос: Как исправить скручивание панелей при роликовой формовке?
О: Скручивание можно свести к минимуму, используя направляющие против скручивания между клетями, регулируя давление валков, выпрямляя узлы, уменьшая скорость подачи и изменяя последовательность формовки.
В: Какие меры предосторожности необходимы при обслуживании валов?
О: Рекомендуемые методы включают в себя электрическую блокировку, изоляцию машины, блокировку поднятых частей, высвобождение накопленной энергии, предотвращение случайных запусков, надлежащее освещение и использование правильных инструментов.
Вывод
Линии рулонной формовки софитов представляют собой универсальный и экономичный способ производства длинных профилей металлических панелей по индивидуальному заказу. Оптимизированная конструкция формовки и надежное оборудование позволяют эффективно производить высококачественные панели. Сотрудничество со знающим поставщиком валковых формовочных машин и регулярное техническое обслуживание являются ключевыми факторами для достижения максимальной производительности. В данном руководстве рассматриваются важнейшие факторы, которые необходимо учитывать при покупке, установке, эксплуатации и обслуживании валковых формовочных машин для софитов.