Metal siding is a popular exterior wall material used in both residential and commercial buildings. It offers durability, customization options, and a sleek look. Metal siding is manufactured through a process called roll forming. A metal siding roll forming machine takes flat strips of metal and forms them into various profiles through a series of rollers.
What is Metal Siding?
Metal siding, also known as metal wall panels, refers to exterior wall cladding made from metal sheets. It is used as an exterior wall covering to protect buildings from weather and provide aesthetic appeal.
Some common types of metal siding include:
- Aluminum siding
- Galvanized steel siding
- Copper siding
- Zinc siding
- Stainless steel siding
Metal siding is available in a variety of colors, textures, and profiles. The most common profiles are vertical panels, horizontal panels, shakes, and tiles. The panels interlock to create a weathertight exterior wall surface.
Compared to other sidings like wood, fiber cement, or vinyl, metal siding offers exceptional durability and resistance to rot, fire, insects, and impact. With proper installation and maintenance, metal siding can last over 50 years.
Other benefits of metal siding include:
- High strength-to-weight ratio
- Resistance to denting and cracking
- Low maintenance
- Customizable panels, colors, and finishes
- Sleek, modern appearance
- Sustainable and recyclable
Metal siding has become a popular choice for modern homes and buildings due to its sleek look and extreme durability.
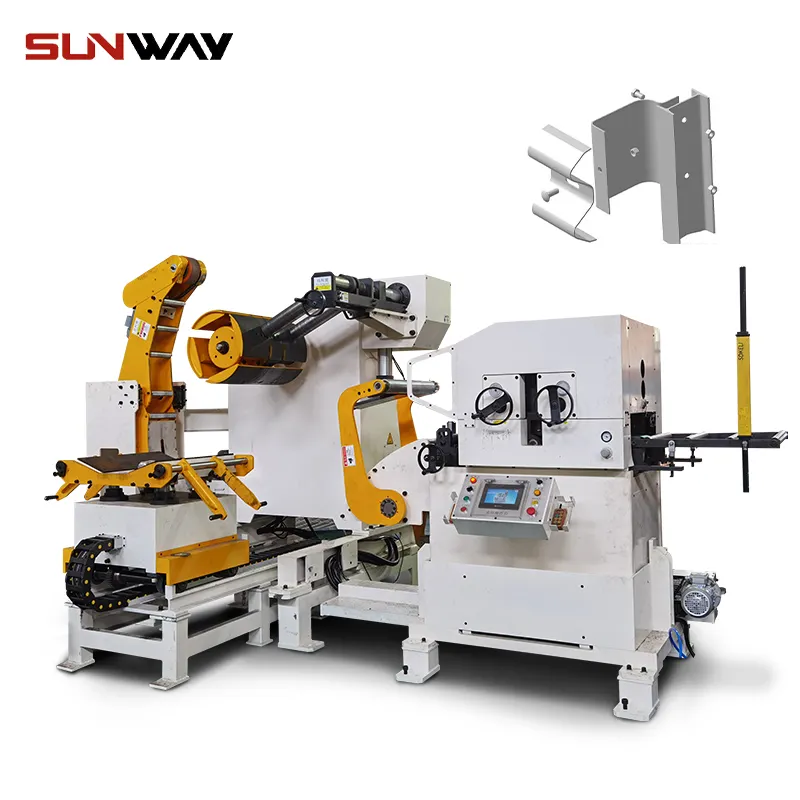
How is Metal Siding Made?
Metal siding is manufactured through an industrial process called roll forming. It involves passing flat metal sheets through a series of roller dies to bend and form the sheet into various profiles.
The major steps in roll forming metal siding include:
1. Design and Fabrication of Roller Dies
The first step is to design and fabricate roller dies that will shape the metal into the desired profile. The profile design depends on the look and dimensions required. CAD software is used to design precision roller dies. The dies are then machined from alloy steel.
2. Decoiling and Feeding Metal Coils
Thin metal coils are loaded onto a decoiler which unrolls and straightens the coil. The sheet then passes through feeder rollers which align and feed the sheet into the roll forming machine at a constant speed. Aluminum and galvanized steel are common metals used.
3. Rolling and Forming the Profile
As the sheet passes through sequential sets of roller dies, it is progressively bent and shaped into the final profile whether it’s vertical panels, shakes, or tiles. The roller dies only bend the metal, they do not stretch or cut it.
4. Cutting to Length
After forming the profile, the siding passes through a cutoff die which cuts it to the specified length. The scrap metal gets recycled.
5. Additional Production Line Processes
Additional inline processes may include hole punching, embossing textures, or hemming the edges. The profiles may be brushed, painted, or finished through a coating line.
6. Packaging and Distribution
Finally, the formed metal siding panels are packaged and shipped to distributors or installation sites. Custom packaging protects the finishes and edges during transportation.
By using roll forming technology, manufacturers can mass produce metal siding in various lengths, colors, and designs cost effectively. The roll formed profiles are lightweight, high strength, and uniform.
Metal Siding Roll Forming Machine
A metal siding roll forming machine is an industrial machine that roll forms metal coils into specific profiles for metal siding. Here are the key components of a metal siding roll forming line:
Roll Forming System
This is the core roll forming section where the process of bending metal strips into shaped profiles occurs. A typical roll former may have 5-15 rolling stations each with an upper and lower roller die. As the coil sheet passes through sequential roll stations, it gains its final shape.
Common roll forming profiles for metal siding include boards, panels, shakes, and tiles. Rollers can form complex profiles, emboss patterns, and punch holes if needed.
Decoiler or Uncoiler
This device holds a large coil of thin metal sheet weighing up to 10 tons. It continuously unrolls the coil and feeds the sheet into the roll former at a controlled speed and tension. Decoilers may be turntable or reel type.
Feeder or Servo Feeder
The feeder consists of a set of rollers that straighten the coiled metal sheet and feed it into the roll forming sections at the required speed. Servo feeders provide precise speed control and synchronization.
Shear or Cutoff
A shear or cutoff die cuts the continuously formed metal siding into lengths as per specifications (2 ft to 20 ft). The scrap metal is recycled. Rotary shears and flying cutoffs are common.
Hydraulic System
Hydraulics power the up/down movement of roll dies to set the gap distance. They provide the pressing force required during rolling.
नियंत्रण प्रणाली
An integrated control system automates the entire roll forming process. It controls equipment speed, die position, and material feed.
Conveyors
Conveyors transport the finished siding products from the roll former to the exit or for further processing if required.
Safety Equipment
This includes guards, covers, emergency stops, and sensors to ensure operator safety.
In addition, the line may have punching units, notching equipment, embossing rollers, coating units, and inspection systems if producing finished siding.
Types of Metal Siding Roll Forming Machines
There are two main types of metal siding roll forming machines:
1. C-Type Roll Former
C-type or cantilevered roll formers have a C-shaped frame where the rolls are mounted horizontally. This is the most common design. C-type machines produce simple profiles for wall panels, boards, and tiles cost-effectively.
[image]
2. O-Type Roll Former
O-type or overhead roll formers have an O-shaped frame where rolls are arranged in a vertical inline configuration. O-type formers produce complex profiles and long parts. They require less space than C-type machines.
[image]
Roll forming machines may further be classified by:
- Number of roll stations
- Type of drive – chain or individual motors
- Production speed
- Type of control system
- Additional capabilities like punching, notching, or cutoff
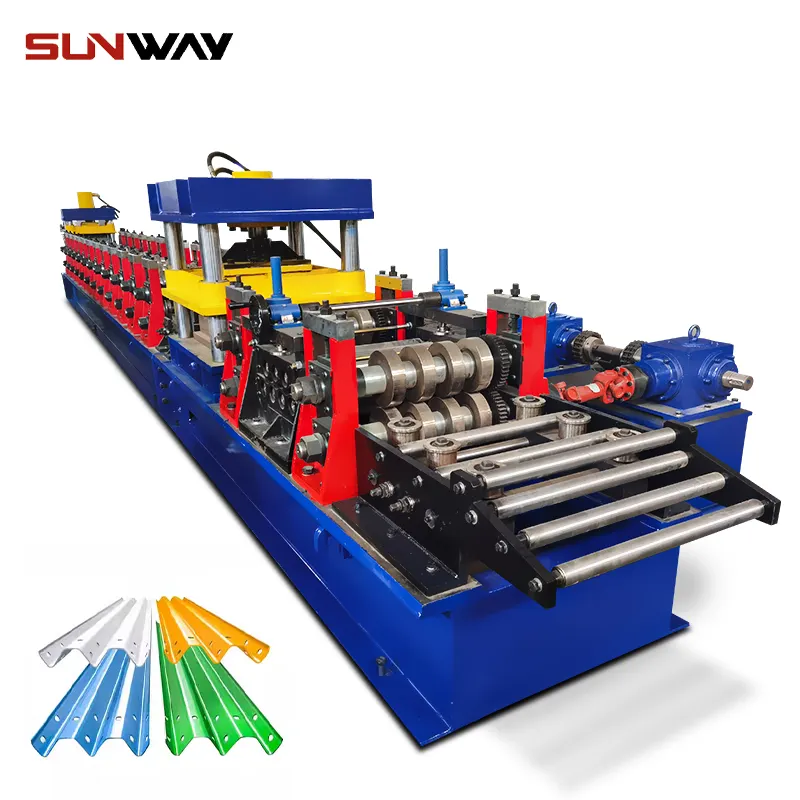
Key Components of a Metal Siding Roll Forming Machine
The main components of a metal siding roll forming line include:
- Roller dies – Made of machined alloy steel. Progressive dies bend the metal incrementally to form the profile.
- डेकोइलर – Holds up to 10-ton metal coils. Feeds sheet into the roll former.
- Feeder – Sets of rollers that straighten and feed the sheet at a controlled speed.
- Roll forming sections – Bend and form the metal sheet into designed profile. 5-15 stations typically.
- Cutoff/Shear – Cuts formed siding panels to specified length.
- Conveyors – Transport finished products out of the line.
- Hydraulic system – Provides power to roll stations for bending and pressure.
- Control system – Automates the speed, feed, and functions of the line.
- Safety covers and guards – Ensures operator safety.
How Does a Metal Siding Roll Forming Machine Work?
A metal siding roll forming machine works in the following manner:
- A large metal coil of galvanized steel or aluminum is loaded on the decoiler.
- The decoiler feeds the flat metal strip into the servo feeder.
- The servo feeder has rollers that straighten the coil sheet and feed it into the roll form station at a constant speed.
- The sheet passes through several (5-15) rolling stations in sequence.
- At each station, counter-rotating rollers progressively bend the sheet a few degrees to form the desired profile.
- Hydraulics apply pressure on the rollers to bend the metal without scratching or crimping it.
- After passing through all stations, the sheet achieves the final shape whether it’s a wall panel, board, or shingle profile.
- The continuously formed profiles pass through a shear/cutoff to cut them to specified lengths as per the product design.
- Conveyors transfer the cut metal siding pieces to the exit or for further processing.
- An automated control system coordinates the decoiler, feeder, rollers, cutoff, and conveyors.
- Sensors monitor the process and ensure consistent high quality production.
This continuous process allows mass production of metal siding components in different shapes, sizes, and finishes.
Key Factors in Metal Siding Roll Forming
To produce strong, uniform metal siding profiles, the roll forming process requires attention to the following key factors:
- Quality of raw material – Metal coil properties like thickness, width, flatness, and hardness.
- Die design – Precision ground roll dies that bend metal incrementally without defects.
- Roller adjustment – Proper gapping between top and bottom rollers.
- Feed speed – Constant feed rate for uniform bending across the sheet width.
- Roller lubrication – Reduces friction between coil and dies to prevent scratching.
- Shearing – Clean cutoff to required length without deformities.
- Tool maintenance – Keeping roll dies, decoiler, and shears in top condition.
- Process monitoring – Sensors to monitor pressure, speed, and temperature.
- Finished product quality control – Inspection of profile shape, holes, finish.
By controlling these factors, roll formers can produce high quality metal siding efficiently.
Applications and Final Products
The profiles produced by metal siding roll forming machines are used for various exterior construction applications:
- Metal wall panels – For exterior walls of residential and commercial buildings. Most common application.
- छत की चादरें – Standing seam metal roof panels.
- Siding tiles or shakes – Resemble tile, wood shake, or slate profiles. Used on building exteriors.
- Roof shingles – Interlocking metal roof shingles.
- Flashing and trim – Used around windows, corners, eaves.
- Gutters and downspouts – For drainage.
- Soffits and fascia – Covers underside of eaves and roof edges.
- Shutters – Decorative external window covers.
- Garage doors – Metal door skins.
Roll formed metal siding offers architects, contractors, and homeowners a durable and aesthetic exterior cladding solution.
Benefits of Using a Metal Siding Roll Forming Machine
Investing in an automated metal siding roll forming line has many benefits for manufacturers:
High Productivity
- Produces over 100 feet of siding per minute.
- Continuous operation with minimal downtime.
- Requires 2-3 operators only.
Consistent Quality
- Automated processes ensure dimensional precision.
- Uniform profile and hole/notch formation.
- No deformities or defects.
Flexibility
- Quick roll die changeover to make new designs.
- Able to produce various profiles, widths, and lengths.
Low Labor Costs
- Automated lines need minimal manual work.
- Reduction in labor expenses.
Scalability
- Add additional rolling stations or capabilities easily.
- Scale production according to demand.
Low Costs
- Mass production brings down per unit costs.
- Raw material savings from high yield.
- Low maintenance costs.
By investing in an efficient roll forming machine line, metal siding manufacturers can reap the benefits of automated, high speed production of top-quality products.
How to Choose a Metal Siding Roll Forming Machine
Here are important factors to consider when selecting a roll forming machine for metal siding production:
Type of Machine
Choose between C-type or O-type frame configuration based on space constraints and profile complexity.
Production Speed
Higher speeds like 100-200 ft/min reduce production time.
Metal Thickness Capacity
Choose capacity between 0.3 mm to 1 mm based on products.
Profile Width Capacity
Wider coil widths result in higher yields and productivity.
Quick Changeover Design
Easy roll die changeover allows fast profile changes.
Roller Design
Robust gear or servo drives prevent roller slippage.
Automation Features
PLC-controlled processes improve efficiency and precision.
Additional Capabilities
Integrated punching, notching, embossing increase product range.
Safety Features
Emergency stops, barriers, sensors improve operator safety.
Service Support
Look for responsive technical support from machine supplier.
Choosing the right metal siding roll forming equipment with the production capabilities aligned to your products will help maximize manufacturing productivity, efficiency, and profitability.
Trends in Metal Siding Roll Forming Technology
Some key technological trends shaping metal siding roll forming include:
- Servo-powered rollers – Improve speed and force control during bending.
- Programmable controllers – Provide precision automation of all line functions.
- Flexible quick-change tooling – Allow fast profile and product changes.
- Inline processing – Additional capabilities like punching, branding, perforating.
- Advanced sensors – Monitor processes in real-time to improve quality control.
- Automatic lubrication systems – Maintain consistent roller lubrication.
- Safety upgrades – New physical guards, interlocks, and monitoring systems.
- Virtual commissioning – Simulate machine setups and control logic before installation.
- Internet-connected systems – Enables remote monitoring and data analytics.
With such technological enhancements, modern roll forming machines offer metal siding producers the efficiency and agility needed to stay competitive.
Metal Siding Roll Forming Machine Maintenance
To sustain high production efficiency, quality, and safety, metal siding roll forming machines require regular maintenance in these key areas:
Rollers and Die Blocks
- Inspect rollers and dies periodically for wear, scratches, or damage. Refinish or replace as needed.
- Lubricate rollers regularly based on production frequency.
- Verify roller parallelism and die block alignment.
Decoiler and Coil Feed
- Check decoiler brakes, clutches, and guides.
- Inspect coil hold-down devices and straighteners.
- Ensure proper coil feed into roll former.
Cutoff Systems
- Sharpen cutoff blades when worn.
- Check shear blade gaps are correct.
- Verify cut length accuracy.
Hydraulic Systems
- Check hydraulic fluid levels monthly.
- Inspect pumps, valves, cylinders for leakage.
- Confirm applied pressure at each roller station.
Conveyors
- Inspect conveyor belts and drives.
- Check belt alignment and tension.
Control Systems
- Diagnostic checks on PLCs, sensors, drives, and HMIs.
- Test emergency stop circuits.
- Verify electrical connections.
Proper maintenance as per the manufacturer’s schedule will maximize the production life of the roll forming equipment.
Troubleshooting Common Problems in Metal Siding Roll Forming Machines
Some common problems faced in metal siding roll forming machines and remedies are:
Roller Slippage
Cause – Insufficient grip between rollers and sheet metal.
Solution – Check roller wear, pressure settings, lubrication, and material feed.
Profile Distortion
Cause – Improper roller alignment, die clearances, or metal feed.
Solution – Realign rollers, adjust die gaps, control feed speed.
Metal Scratching
Cause – Debris buildup on rollers, lack of lubrication.
Solution – Clean rollers, improve lubrication frequency.
Flared Ends on Profile
Cause – Excessive horizontal pressure from rollers.
Solution – Reduce horizontal clearance between rollers.
Irregular Cutoff Length
Cause – Worn shear blades, inconsistent feed speed.
Solution – Sharpen or replace shear blades. Control feed speed.
Regular inspection and maintenance will minimize defects and downtime on a roll forming line.
Safety Tips for Metal Siding Roll Forming Machine Operators
Working with powerful roll forming equipment containing fast-moving parts requires vigilance. Here are some key safety tips:
- Wear personal protective equipment – safety glasses, shoes, gloves, and hearing protection.
- Ensure all safety guards are in place before starting the machine.
- Check for roller trapping points and pinch areas. Keep hands away from them.
- Do not make any adjustments when the machine is running.
- Follow lockout/tagout procedures before die changeovers or maintenance.
- Keep work area clean and free of oil spills or debris.
- Monitor material infeed and outfeed during operation.
- Be aware of emergency stop buttons and procedures.
- Report any abnormal noise, vibration or safety issues immediately.
- Adhere to the manufacturer’s operating instructions.
- Take proper training before operating the roll forming machine.
With training and safe work practices, operators can avoid accidents on a metal siding production line.
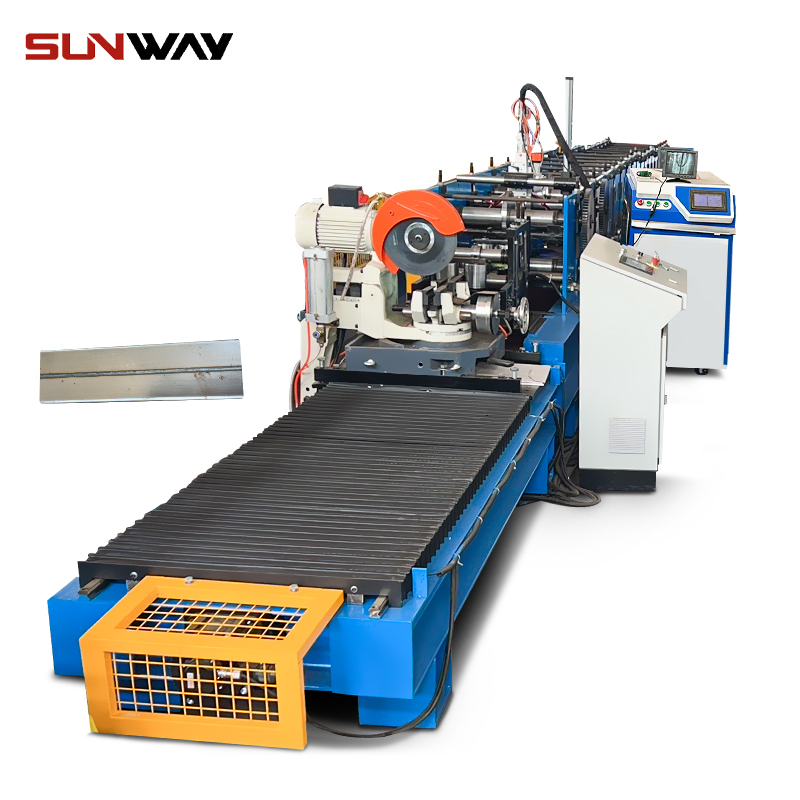
सामान्य प्रश्न
What is the process of roll forming for metal siding?
Roll forming creates metal siding by passing flat sheet metal through a series of rollerCopy dies that progressively bend the sheet into the desired profile. The key steps include feeding the metal coil into the roll former, rolling it through multiple stations to shape the profile, cutting to length, and transferring finished parts out of the line.
What types of metals can be roll formed into siding?
The most common metals roll formed into siding are steel, aluminum, copper, and zinc. Steel is used for galvanized, stainless, and pre-painted steel siding. Aluminum alloys are also popular for residential and commercial siding applications.
What are some common profiles produced by metal siding roll formers?
Typical siding profiles include vertical wall panels, horizontal lap siding, board & batten, shake/shingle patterns, interlocking tiles, and V-groove panels. Architectural profiles like brick and stone can also be simulated through roll forming.
How long does a metal siding roll forming machine last?
With proper maintenance and operation, a good quality metal siding roll former can reliably produce siding for 15-25 years. Key factors affecting longevity include initial machine build quality, ongoing maintenance, wear item replacement, and avoiding misuse through improper setups.
How much does a metal siding roll forming machine cost?
Costs vary based on production speed, width capacity, automation features, and additional capabilities. A standard 10-12 station 25-50 feet/min roll former for wall panels may cost $60,000 to $120,000. Larger automated lines with integrated punched openings or texturing can cost over $200,000.
What safety precautions should be taken when operating a roll former?
Important safety tips include wearing protective gear, keeping away from trapping points, verifying guards are in place, following lockout procedures, keeping work area clear, being aware of emergency stops, reporting issues immediately, and getting proper operator training.
What are some common defects in roll formed metal siding?
Defects can include twisting, bowing, flare, waviness, and uneven cutoffs. These are often caused by issues like misaligned rollers, worn tooling, poor metal feed, or inappropriate roller pressure. Proper setup and maintenance reduces defects.
How often should roll forming machines be maintained?
Roll formers should be maintained daily, weekly, and monthly based on a schedule from the manufacturer. Key tasks include checking rollers, lubrication, hydraulics, conveyors, guards and keeping the machine clean. This prevents unplanned downtime and quality issues.
Can a roll forming machine be set up to produce a new profile?
Yes, with a quick die change system, roll forming machines can be set up with new dies to produce different profiles in 1-2 hours. Programming may be needed to adjust process parameters. This provides manufacturers with the flexibility to switch profiles based on demand.