Metal tile roll forming machines are an efficient way to manufacture metal roofing tiles and panels. This advanced manufacturing process uses rolls to bend and shape flat metal coil into desired roofing profiles. Metal tile roll forming offers many benefits over traditional metal roofing production methods.
This comprehensive guide will cover everything you need to know about metal tile roll forming machines. We’ll discuss how the roll forming process works, the different components and features of a roll former, design considerations, and common applications. We’ve also included frequently asked questions at the end to further help you understand this transformative metalworking technology. Let’s get started!
How Does Metal Tile Roll Forming Work?
Roll forming is a continuous bending process that forms sheet metal into constant cross-section parts. The sheet metal passes through a series of roller dies that progressively shape the material into the desired profile. As the material moves through the rolling mill, each set of rolls impart incremental bends until the final shape is achieved.
The rolls apply pressure vertically to bend the metal and horizontally to feed the sheet through the machine. The roll forming process allows for longitudinal curves and bends to create complex geometries. It’s an efficient, one-step process capable of high production volumes.
Step-by-Step Process
Here is an overview of the metal tile roll forming process:
- Feeding – Coiled metal sheet is placed on an unwinding device at the entry of the roll former. The stock is fed into the machine at a constant speed.
- Forming – The sheet enters the succession of roller dies that bend the metal incrementally to the specified profile.
- Cutting – After the full profile is formed, the finished part is cut to length by a cutting component.
- Counting/Stacking – Formed parts are automatically counted and stacked for easy handling.
The roll forming process is continuous with each step happening simultaneously. This automation allows for high production rates and consistent quality parts.
Roll Forming vs Press Brake Bending
Roll forming should not be confused with press brake bending. While both processes shape sheet metal, there are some key differences:
- Press braking – Uses a male and female die to form parts in a press. Better suited for low or medium production volumes.
- रोल बनाना – Roller dies shape the material gradually through the machine. Ideal for high production volumes.
- Roll formed parts have consistent profiles and quality since parts are formed in a continuous process. Press braking can lead to some variations from batch to batch.
- Roll forming exerts less stress on the metal, reducing chances of cracking in longer parts. Press brakes can damage material with heavier contact.
For long, high-volume metal roofing components, roll forming is generally the preferred process.
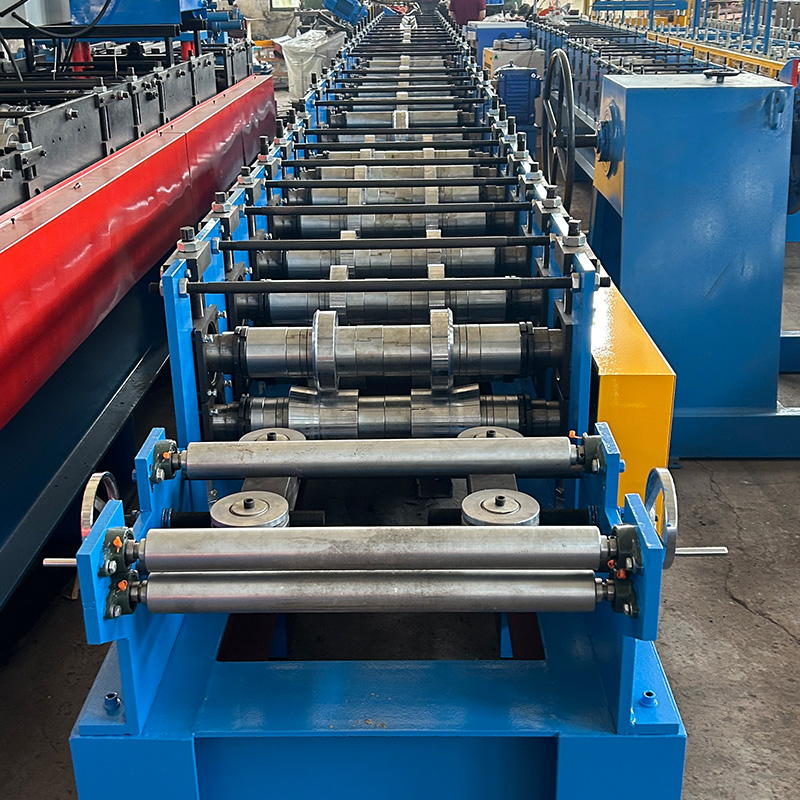
Components of a Metal Tile Roll Forming Machine
A metal tile roll former consists of several fundamental components that work together to create the formed parts:
Uncoiler
The large coil of flat sheet metal is loaded onto an uncoiler at the start of the line. The uncoiler allows the sheet to be fed into the roll former at a fixed speed and tension. Common uncoiler types include mechanical, hydraulic, and pneumatic.
Feed Table
This is a table-like component that guides the flat metal sheet into the roll forming section. It ensures the stock enters the first forming rolls smoothly and evenly.
Forming Stations
The core of the machine, the forming section contains the roller dies that progressively bend the metal to the desired shape. The number of roller die stations varies based on part geometry. Simple profiles may have as few as 5-10 stations while complex profiles may need 15 or more forming stations.
Cutoff Knife
Once fully formed, the cutoff knife shears the finished profile to length. Roll formers can have Punching or sawing style cutoffs. Automatic cutoff helps streamline the process for maximum throughput.
Counting System
The counting or stacking system organizes the cut parts for easy handling. Counters may stack pieces or drop them into organized bins. This improves part flow from the roll former.
नियंत्रण प्रणाली
The controls coordinate the speed, feed rate, cut length, and other parameters. Modern roll formers have programmable PLCs that offer precise control and monitoring.
Exit Ramp
A sloped exit ramp releases the formed and cut parts from the machine. Some smaller machines may have exit chutes rather than ramps.
In addition to these primary components, roll formers can also integrate pinch rolls, heating, hole punching, embossing, and other in-line processes for added functionality.
Roll Former Configurations
Metal tile roll forming machines come in a range of configurations and types. The main styles include:
Stationary
Stationary or in-line roll formers have all components fixed in position. The sheet lineally travels through each section of the machine. This is the most common and economical type of roll former. Production rates typically reach 15-20 feet per minute.
Portable
Portable roll formers are designed for mobility and flexibility. All components are mounted to a frame with wheels, allowing the machine to be moved easily. Portable rolling mills take up less space and can be transported for on-site forming. However, production speeds are slower than stationary machines.
Vertical
A vertical roll former orients the process on a vertical plane. The metal sheet feeds vertically through top and bottom rollers rather than horizontal. Vertical rolling takes up minimal footprint and allows vertical curves in profiles. But it comes at a higher cost and slower speeds than stationary horizontal machines.
Serpentine
Serpentine roll formers snake the sheet back and forth horizontally through multiple forming stands. This gives the advantage of a compact footprint while maintaining high production rates. Serpentine machines require more complex material handling but maximize space efficiency.
Custom
For unique part geometries, custom roll formers can be built to specification. These machines incorporate specialized features and tooling for proprietary profiles. Common in metal roofing systems, custom roll formers ensure optimal forming of signature products.
Careful consideration of part geometry, production needs, and budget helps determine the ideal roll former arrangement.
Key Design Factors
Roll forming machines are engineered specifically based on the metal roofing panel profile design. Several factors must be accounted for in the equipment design:
Material Type
The gauge, grade, coating, and width of the sheet metal being formed impacts the rolls and machine parameters. Equipment is designed according to material specifications.
Part Length
Maximum part length determines the size and layout of the machine line. Longer profiles often require a serpentine configuration. Shorter parts may allow for portable mills.
Geometry
The complexity of the panel shape – including ribs, curves, and angles – dictates the number of roller stations required. Simpler shapes need fewer stands.
Production Volume
Higher volume requirements call for faster equipment with automated features. Lower volumes may permit simpler manual machines. Speed and productivity needs influence specifications.
Budget
Roll forming equipment ranges from low-cost manual machines to sophisticated high-speed lines. The budget ultimately determines which capabilities are feasible. Priorities balance cost with production needs.
Careful planning must be done to choose roll formers suited for the intended metal roof panels. Consultation between the designer and manufacturer optimizes the equipment.
Metal Roofing Applications
Thanks to its efficiency and flexibility, roll forming is ideal for producing popular metal roofing building products. Common metal roofing profiles produced on tile roll forming machines include:
Standing Seam
Standing seam panels with vertical ribs are roll formed to provide concealed fastening. This gives an attractive, watertight metal roof.
Corrugated
Iconic corrugated panels with sinusoidal shapes are easily formed on a roll former. Corrugated is used for roofing and siding.
Shake & Shingle
Simulating the look of shake or asphalt shingles, these profiles feature small, overlapping ribs that mimic shingle designs in metal.
Metal Tiles
Sheet metal can be roll formed intoshapes replicating clay, concrete, or slate roof tiles. Lightweight metal tiles maintain aesthetics with easier installation.
Clip Lock Panels
For faster install, clip lock panels feature built-in fastening tabs. The clips interlock adjoining panels and secure to the roof deck.
Rainware Products
Gutters, downspouts, and collector heads are fabricated using roll forming technology. Rainware parts benefit from rolling’s consistency.
Narrow Width Coil
To reduce waste and cost, narrow width strip metals from 5″- 24″ can be roll formed into panels. Available in different metals and finishes.
Nearly any long metal roofing product can be produced by roll forming machines with the proper tooling design.
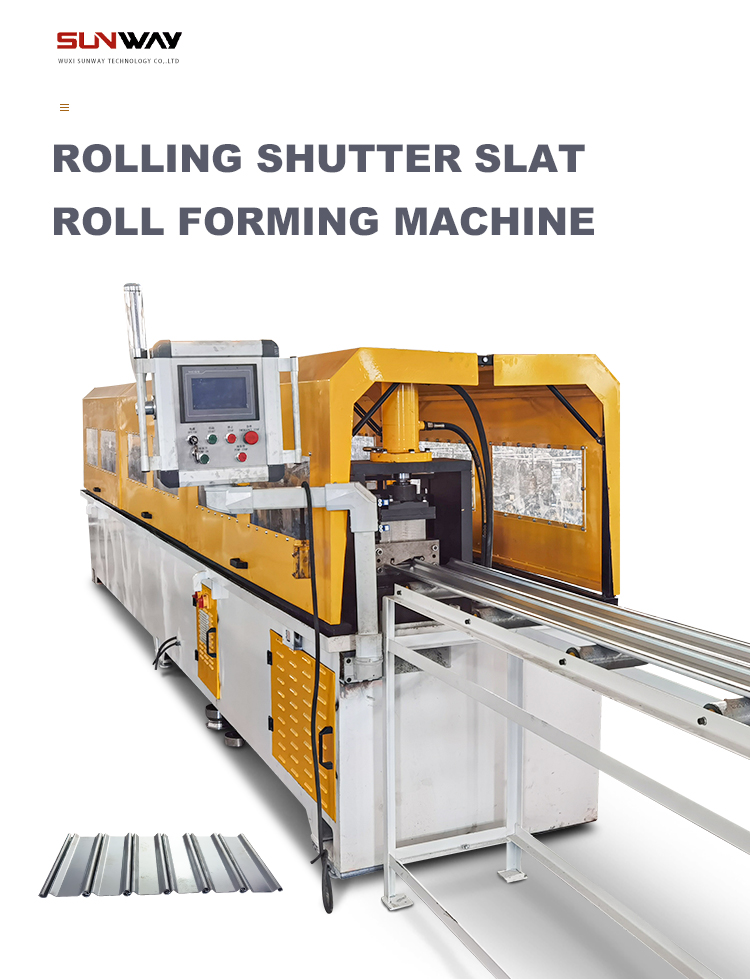
Roll Former Tooling
At the heart of the roll forming mill are the roller dies that progressively shape the metal profile. Called roll tooling or roll sets, these precision machined tools mount onto the forming stands. The roll tools convert the flat metal strip into the desired panel geometry.
Roller Dies
The roller dies are machined from hardened steel to withstand the pressures of steel rolling. Male and female roller pairs mount opposite each other to bend the sheet as it feeds through. The rollers have matching contours engineered to the part shape.
Roll dies typically last from 1-2 years before needing refurbishment. Spare sets allow for quick changeouts to minimize downtime.
Breakdown Rolls
The initial roller stations that start to bend the flat sheet are called breakdown rolls. They gradually bend the metal to open up the profile.
Finishing Rolls
The final few stations contain finishing rolls that complete the geometry and fine tune the shape. Finishing rolls generate the critical details and tight tolerances.
Bottom Roller Drive
To propel sheet through the mill, the bottom rollers connects to a gear drive unit. Friction between the driven lower rolls and sheet pulls the stock through the forming stands.
Roll Alignment
Keeping the rollers aligned correctly is crucial for quality parts. Improper alignment causes profile distortion and scrap. Precision roll mounts, bearings, and housings maintain alignment during operation.
The roll tooling makes up a considerable part of the equipment cost, but it’s indispensable for achieving the desired panel profile.
Advantages of Roll Forming Metal Tiles
There are many benefits to using roll forming over other manufacturing methods for metal roof tiles:
High Productivity
Roll forming has very high material throughput, typically around 15-20 feet per minute. Long panels up to 60′ can be produced continuously. The automated process enables enormous production quantities.
Dimensional Accuracy
Roll formed parts achieve excellent dimensional precision and accuracy compared to other bending methods. Tolerances down to +/- 0.5 mm are possible. This reduces waste and rework.
Consistent Quality
The continual forming process ensures uniformity from piece to piece with no variability between batches. Roll formed tiles offer reliability and consistency.
Reduced Labor
Automated roll forming minimizes direct labor requirements. After initial setup, the machine produces parts with minimal supervision. Labor is focused on material handling rather than production.
Ideal for Long Parts
Roll forming handles long length panels more effectively than alternate processes like press braking or stamping. There are virtually no limits to part length.
Lower Investment Costs
Though design and tooling costs are high, the equipment investment for rolling mills is relatively low. Roll formers offer quick ROI compared to other technologies.
Flexible Production
Quick roller changeouts allow fast profile changes for mixed product output. Rolling mills handle short run orders with ease.
For most long metal roofing components, roll forming delivers the productivity, quality, and flexibility manufacturers need.
Design and Fabrication of Roll Forming Machines
Creating a custom roll forming machine is an involved process requiring careful collaboration between the profiling design team and equipment manufacturer. Here are the key steps:
Product Design
The profile geometry is engineered based on application requirements and roofing standards. CAD software models the complex shapes.
Tool Design
The roll tooling is designed based on the CAD profile models. Precision tool drawings and models are created. Roll materials, treatments, and bearings are specified.
Machine Design
Using the tooling models, the rolling equipment is designed. Frame size, forming stands, drives, controls, and material handling features are all engineered.
Prototype Tooling
Prototype tooling is machined to test and verify the profile design. Test samples are evaluated before final tooling production.
Fabrication
The roll sets, machine frames, controls, and components are built to the engineering designs. Weldments, hydraulics, electronics, and drives are completed.
Testing & Installation
The machine and tooling are calibrated and trial runs conducted to ensure performance. The equipment is certified before shipping to the facility.
Training & Support
To ensure smooth operation, the manufacturer provides training for machine operation and maintenance. Continued support is supplied for the lifespan of the equipment.
The entire process takes around 12-16 weeks from design to completion. Close coordination at every phase is critical for roll former success.
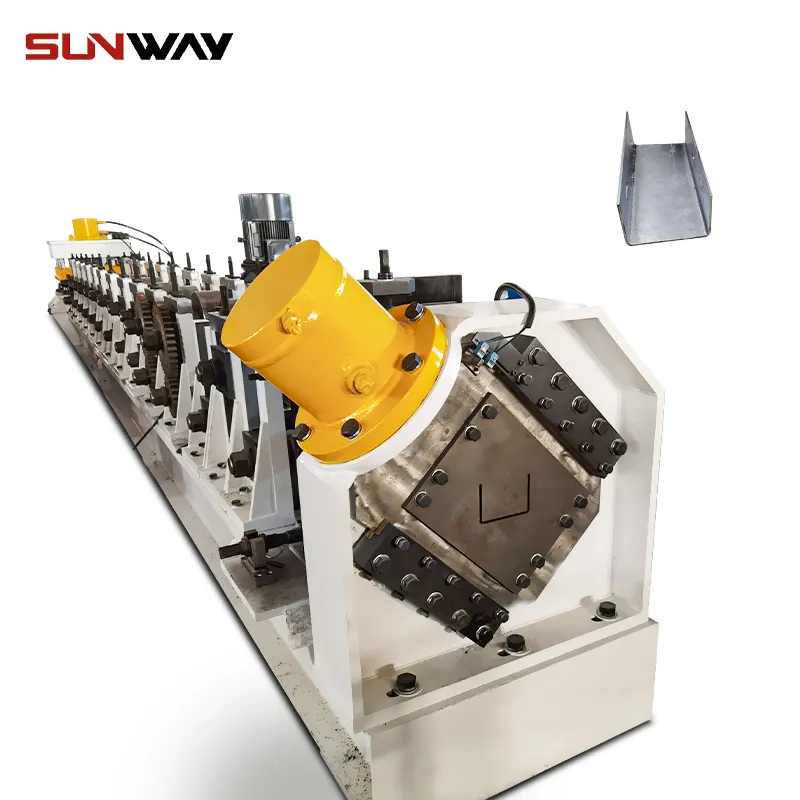
Maintenance of Roll Forming Equipment
Like any manufacturing technology, roll forming equipment requires regular maintenance to keep it running optimally. Here are key maintenance tips for roll formers:
Clean Rolls
Debris on the roller dies can mark or scratch the metal. Keeping rolls clean of dirt and grime should be part of daily cleanup.
Lubricate Moving Parts
The bearings, chains, drives, and other moving components need regular lubrication per the manual. This prevents premature wear and seizure.
Inspect Weldments
Over time, vibration can crack weld seams on the frame, stands, and sections. Inspect thoroughly and repair any found failures.
Replace Worn Components
Belts, bearings, seals, and wear items deteriorate over time. Have spares on hand and replace before failures occur.
Check Alignment
Improper roll alignment affects part quality. Periodically check alignment and re-align if necessary. Alignment is especially critical after tooling changeovers.
Examine Finished Parts
Inspecting rolled profile samples helps spot potential issues like wear, alignment, or damage. Address any problems found.
Train Operators
Ensure operators understand proper operation, safety, and care. Proper operation reduces misuse that leads to equipment damage.
By following manufacturer guidelines and professional maintenance practices, roll formers provide years of trouble-free metal tile production.
निष्कर्ष
Roll forming technology provides metal roofing manufacturers with an extremely efficient method for producing metal shingles, tiles, and panels. The automated process delivers high volumes of finished product with accuracy and reliability. While roll former equipment requires an initial investment, the long-term payoff is substantial.
This guide covered all aspects of metal tile roll forming – how it works, machine configurations, design factors, tooling considerations, and applications. When designed and operated properly, metal tile roll formers will provide years of productivity for roofing fabricators.
If you’re interested in implementing roll forming in your operation, consult an experience manufacturer early in the planning process. Their expertise can help you develop effective solutions tailored for your particular product line and production needs. The strategic use of roll forming promises a faster, lower cost way to stay competitive in the metal roofing and wall panel market.
सामान्य प्रश्न
What types of metals can be roll formed?
Roll forming works on a wide range of metals: steel, stainless steel, aluminum, copper, brass and more. Mild steel is the most commonly roll formed material.
What size coils can be used?
Roll formers accommodate standard coil widths from 12” to 24”. Large dies and decoilers can also process jumbo coils up to 60”. Maximum coil weight ranges 10,000 – 25,000 lbs.
How long are the finished metal tiles?
Standard roll formed lengths are from 6 – 20 ft., but lengths exceeding 60 ft. are possible for standing seam panels. Finished tile length depends on installation method and panel design.
What thickness metals can be formed on a roll former?
Roll forming handles thin to thick gauges. Standard metal roofing gauges from 24 ga. to 16 ga. (0.6 mm to 1.6 mm) are commonly produced. Thicker metals may require greater roll tonnage.
How are complex roof tile shapes made?
Roll tooling can be engineered to produce highly complex shapes and embossments. Undercutting or multistage operations may be needed for extreme shapes.
What safety measures are required?
Roll formers contain many safeguarding devices – safety fences, light curtains, E-stops, interlocks, etc. Only trained personnel should operate machinery while wearing proper PPE.
Can a roll former make trim and flashings?
With additional tooling, many roll formers can produce matching trim, rake, ridge, eave, and flashing components for a complete roofing system.