Overview
Steel profile roll forming machines are used to convert flat steel strips or coils into customized profiles or shapes through a continuous and progressive rolling process. This eliminates the need for welding or machining, making it an efficient and cost-effective option for large production runs.
Roll formed steel profiles find applications in construction, warehouses, solar panel mounts, furniture, automotive components, railings, door panels and various industrial uses. The flexibility of roll forming allows creating unique cross-sections not possible through extrusion.
This guide covers the key aspects of steel profile roll forming machines:
Types of Steel Profile Roll Forming Machines
Machine Type | Description |
---|---|
Single Profile | Produces profiles of single shape continuously |
Multi-Profile | Switches between different shaped profiles |
Customized | Fully customized to profile design |
Key Components and Features
Component | Function |
---|---|
Uncoiler | Feeds flat strip coil into roll forming line |
Feed Table | Supports and guides strip into forming rolls |
Forming Stands | Progressively shape strip through sets of rolls |
Punches | Cut outs or notches in the profile |
Shearing | Cuts profile to desired lengths |
Stacker | Collects finished cut profiles |
डेकोइलर | Rewinds processed coil strips |
Design and Operational Parameters
Parameter | Description |
---|---|
Material | Cold-rolled steel, stainless steel, or aluminum coils |
मोटाई | Up to 3 mm for steel, 6 mm for aluminum |
Width | 50 mm to 800 mm range |
Speed | Up to 100 m/min |
Lengths | 0.5 to 10 m typical |
Tolerances | +/- 0.5 mm on nominal dimensions |
Process Specifications and Standards
Specification | विवरण |
---|---|
Forming Stations | 10-16 typically for complex shapes |
Roll Materials | High strength alloy steel, induction hardened |
Roll Diameter | 100-150 mm range |
Roll Design | machined, ground, polished |
Roll Pressure | 5-10 tons per stand |
Lubrication | Oil or grease on rolls |
शक्ति | 10-15 kW per forming stand |
Steel Profile Roll Forming Machine Suppliers
Supplier | Location |
---|---|
Company 1 | China |
Company 2 | Europe |
Company 3 | भारत |
Company 4 | United States |
Pricing varies from $50,000 to $500,000 based on size, production rate, automation features and customization. Local suppliers should be evaluated based on experience, service support, production flexibility and cost.
Installation and Operation
- Machines require flat, level concrete foundation for stability
- Electrical, pneumatic and lubrication lines need to be installed
- Trial runs recommended to verify profiles prior to production
- 1-2 operators per shift for setup, feed, quality checks and offloading
- Preventative maintenance as per supplier guidelines
Choosing the Right Supplier
Consider the following when selecting a steel profile roll forming machine supplier:
- Experience and specialization in roll forming machines
- Capability to design tooling and simulate forming process
- Flexibility to handle design changes and short runs
- Quick turnaround on design, tooling and delivery
- Range of machine sizes and production speeds
- Quality control and inspection processes
- Installation support and operator training provided
- Availability of spare parts and service support
- Responsiveness to technical queries and issues
- Total cost of ownership over long term
Advantages of Steel Profile Roll Forming Machines
- Efficient, continuous and automated forming process
- Ability to create complex custom profiles in long lengths
- Consistency and precision with tolerance control
- High production rate for long production runs
- Lower cost compared to extrusion or fabrication
- Minimal material waste – roll formed from coil strips
- Versatile – can use different materials and coatings
Limitations of Steel Profile Roll Forming
- High initial tooling cost for profile design
- Long lead time for design, tooling fabrication
- Not economical for short production runs
- Size limitations based on coil width and thickness
- Limitations on strength compared to extruded profiles
- Does not work well for tapered or stepped shapes
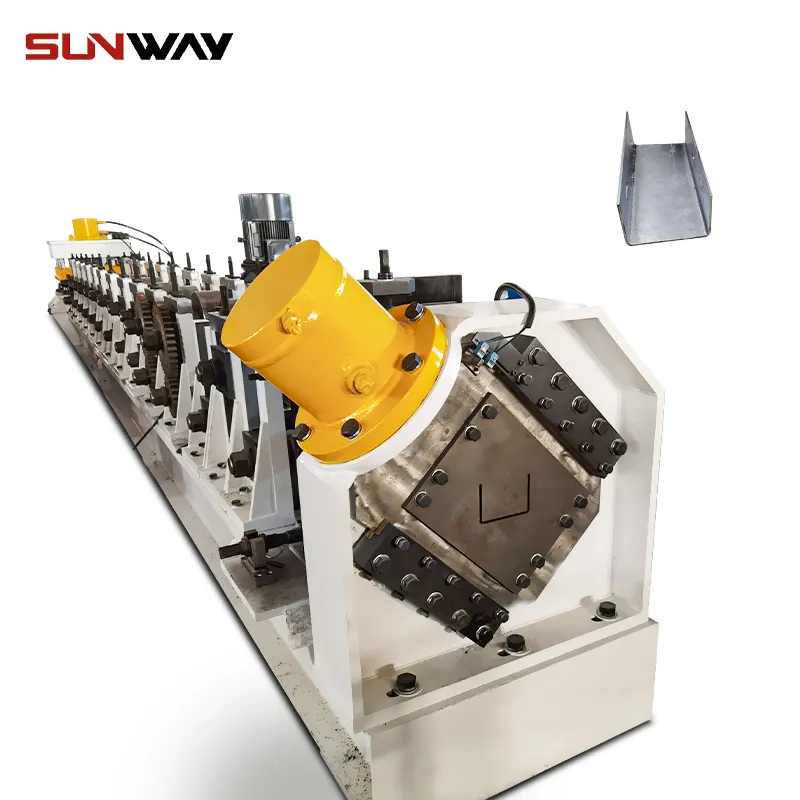
Applications and Uses of Roll Formed Steel Profiles
Roll formed steel profiles find many structural and industrial applications:
Structural Steel Framing
- load bearing wall studs
- roofing purlins and girts
- floor joists
- structural channels
Solar Panel Frames and Mounts
- support structures
- ground mounts
- roof mounting rails
Material Handling Systems
- conveyor side guides
- pallet racking
- mezzanine framing
- equipment guards
Building Exteriors
- wall panels
- roofing
- siding
- canopies
- sun shades
Furniture
- frames
- legs
- brackets
- bases
Automotive Components
- roof bows
- door frames
- reinforcements
- brackets
Railing and Safety Barriers
- balcony railings
- safety barriers
- guard rails
- hand rails
Door Frames
- garage doors
- rolling doors
- sliding doors
- entry doors
Other Applications
- lighting poles
- signage and displays
- enclosure panels
- shelving
- solar heat collectors
- cable trays
- stair stringers
The flexibility of roll forming allows creating optimized profiles for strength, aesthetics and functionality across many structural, mechanical and ornamental applications.
Types of Steel Profile Roll Forming Machines
There are three main types of steel profile roll forming machines:
Single Profile Machines
These produce continuous lengths of one profile shape. The forming rolls are set up specifically for that shape. Typical examples include wall panel lines and roofing lines producing a single repeated shape.
Advantages:
- Simplest design
- Lower cost
- Quick changeovers between production runs
Limitations:
- Can only produce one profile
- Needs roll set change for new shapes
Applications:
High volume production of standardized profiles like wall panels, roofing sheets, racking, purlins, studs etc.
Multi-Profile Machines
These roll formers can switch between different shaped profiles by changing the active roll stand configuration. They have quick change cassette systems for the different roll sets.
Advantages:
- Flexibility to produce variations from same machine
- Quick and easy roll changeovers
- Lower cost than fully customized lines
Limitations:
- Limited to roll set profiles only
- Production rate slower than dedicated lines
Applications:
Low to medium volume production with profile variations. Examples – door frames, structural steel, solar mounts.
Customized Profile Machines
Fully customized roll formers are engineered for the specific profile shape required. All roll stands and components are tailored for the profile design.
Advantages
- Optimized for profile geometry
- Highest quality and tolerances
- Fastest production rate
Limitations:
- High initial tooling cost
- Fixed for one profile design
- Long lead time for design and build
Applications:
High volume production of fully customized profiles. Examples – automotive components, rail carriage parts, specialized structural sections.
Comparison Between Machine Types
Parameter | Single Profile | Multi-Profile | Customized |
---|---|---|---|
Set up time | Fast | Moderate | Slow |
Changeover time | Slow | Fast | Not possible |
Capital cost | Low | Moderate | High |
Running cost | Low | Moderate | Low |
Ideal volumes | High | Low to medium | High |
Profile variations | None | Limited | Unlimited |
Production rate | Fast | Moderate | Fast |
Key Components and Features
Roll forming lines have a number of key components engineered to work together to produce the formed profiles.
Uncoiler
The uncoiler holds the rolled steel coil which gets fed into the roll forming line.
Features required:
- Braking system to provide right tension and prevent uncoiling errors
- Quick loading and unloading of coils
- Easy width adjustment
- Protects coil edges from damage
Feed Table
The feed table guides the steel strip from the uncoiler into the forming section.
Components:
- Roller tables or power roller conveyors
- Guide channels for strip alignment
- Equipment for edge conditioning
- Entry guides for forming stands
Forming Stands
The heart of the roll forming process. Multiple stands progressively shape the profile through successive bending and forming operations.
Key aspects:
- Rolls machined to high precision
- Vertical rolls for major shaping
- Horizontal rolls for calibration
- Quick roll changing ability
- Roll gap and pressure adjustment
- Independent drive for each stand
Punches and Cutouts
Punching units cut notches, holes or complex cutout patterns into the profile strip. Allows creating specialty shapes.
Options available:
- Rotary punch and die sets
- Flywheel punches
- Hydraulic punch presses
- Strippers for punch remnants
- Programmable logic control
Shearing Unit
The shearing unit cuts the continuously formed profile into desired lengths.
Features:
- Guillotine, rotary or flying cutters
- Cuts profiles from 3 to 15 meter lengths
- Servo electric or hydraulic actuation
- Adjustable shear angle
- Scrap choppers and conveyors
Stacker
The stacker collects and stacks the cut profile pieces as per required bundle quantity.
Types available:
- Exit roller tables
- Push-off stackers
- Powered stackers
- Bundling systems
- Automatic stack counting
डेकोइलर
Decoilers are used when a coil recoiling operation is needed after roll forming.
Features offered:
- Precision coil winding
- Tension control for recoiled strips
- Quick loading and unloading
- Integrated into production line
- PLC or CNC control
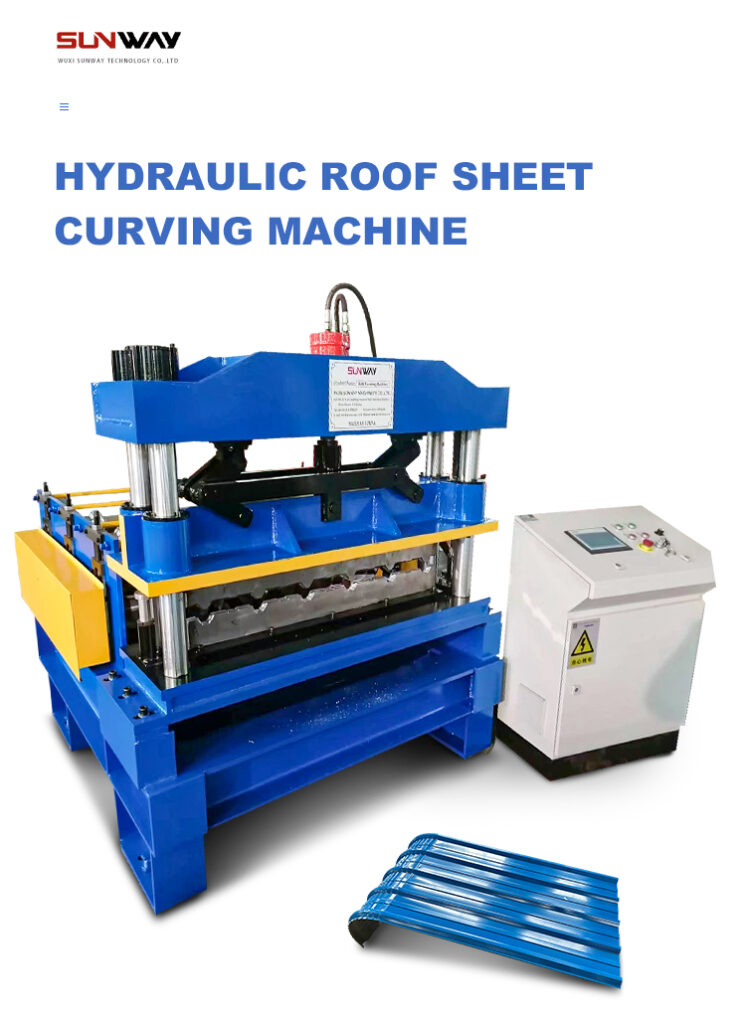
Design and Operational Parameters
Roll forming technology is highly customizable within certain design limits:
Material
- Cold rolled steel coil is the most common. Galvanized or painted coils can also be used.
- Stainless steel strips for specialized anti-corrosion profiles
- Aluminum coils for light weight profiles
मोटाई
- Steel profiles up to 3 mm thickness can be roll formed
- Aluminum coils allow larger thickness up to 6 mm
- Thinner strips allow more compression and shaping
Width
- Common widths from 50 mm to 800 mm
- Wide coils require huge roll tooling
- Narrow strips under 200 mm need edge guiding
Lengths
- Profiles cut from 0.5 meters to over 10 meters
- Typical lengths between 6 to 12 meters
- Longer profiles may need special support
Speeds
- Speeds range from 10 to 100 meters per minute
- Faster speeds require more roll stands
- High speeds increase load on components
Tolerances
- Roll formed parts have tolerance around +/- 0.5 mm
- Tolerances affected by material and process factors
- Secondary operations like correction rolls can improve tolerance
Process Specifications and Standards
Roll forming involves both system design and manufacturing aspects:
Forming Stations
- 10 to 16 forming stands needed for complex shapes
- More stands allow gradual bending
- Typical station spacing of 300 mm
Roll Materials
- Rollers made from high strength alloy steel
- Induction hardened for wear resistance
- Special coatings optional
- Re-ground periodically
Roll Diameters
- Typical roll diameters between 100 to 150 mm
- Larger diameter allows lower pressures
- Smaller rolls used for quick bending
Roll Design
- Machined, ground and polished rolls
- Horizontal, vertical, idler and breakover rolls
- Quick change modular assemblies
- Back-up rolls support main rolls
Roll Pressures
- 5 to 10 tons force per stand
- Roll loads determined by yield strength
- Pressure applied through pneumatic or hydraulic cylinders
Lubrication
- Oil or grease lubrication between rolls and strip
- Prevents scratching and surface defects
- Graphite or boron nitride lubricants also used
Line Power
- 10 to 15 kW installed per forming stand
- Independent drives for main motor and stands
- Servo electric or industrial drives
Steel Profile Roll Forming Machine Suppliers
There are roll forming machine manufacturers across the world. When selecting a supplier, consider factors like:
China
- Large number of manufacturers and competitive pricing
- Medium to high production volumes
- Can be contractual and language barriers
Europe
- High precision and reliability
- More automated features
- Lower volume flexibility often lacking
- Significantly higher cost
भारत
- Cost effective customization possible
- Limited to low-medium production volumes
- Quality and support can be inconsistent
United States
- Advanced controls and easier integration
- Proven longevity and performance
- Highest cost, low volume flexibility
Other considerations include experience with the specific profile, production rate, line automation, quality control, service support, overall cost, and flexibility to handle future requirements and design changes.
Installation and Operation
Proper installation and operation procedures are needed to utilize a roll forming machine’s full potential and lifetime.
Installation
- Requires flat, leveled concrete foundation
- Electrical supply, pneumatic lines, lubrication systems
- Trial runs to confirm profiles before production
- Safety guarding for rotating parts
Operation
- 1-2 operators normally adequate for the line
- Activities involve coil loading, feeding strips, shearing lengths, quality checks, bundling and offloading profiles
- PLC automates settings, speed and parameters
Maintenance
- Schedule preventative maintenance as per supplier manual
- Check roll condition, lubrication and hydraulics
- Monitor vibration, temperature and noise levels
- Replace damaged or worn components proactively
Proper foundations, skilled manpower, upkeep and operating discipline maximize production efficiency and minimizing downtime.
How to Choose the Right Steel Profile Roll Forming Machine Supplier
Choosing the right roll forming machine supplier is critical. Consider the below factors:
Roll Forming Experience
- Years of experience with similar steel profiles
- Exposure to various industries and applications
- Deep knowledge of roll forming process intricacies
Design and Simulation Capabilities
- Engineering expertise for machine design
- Simulation of strip flow and roll stresses
- Design of forming rolls and tooling
Customization Flexibility
- Ability to handle design changes
- Accommodate short production runs
- Modify tooling for variations
Speed and Reliability
- Quick turnaround on design and delivery
- Proven machine reliability over years
- Capacity to handle urgent requests
Range of Machine Sizes
- Offer wide range of production rates and line sizes
- Meet needs from low to high volume scales
Quality Control
- Instrumented testing and inspection
- Integration of quality assurance processes
- Focus on defect reduction and prevention
Service Support
- Installation assistance and training
- Availability of spare parts
- Responsiveness to technical queries
- Preventative maintenance contracts
Total Cost
- Competitive capital pricing
- Consider long term operating costs
- Local support versus offshore supply
Advantages of Steel Profile Roll Forming Machines
Roll forming offers significant benefits that make it the preferred production method for long steel profiles:
Highly Efficient Process
- Automated reel-to-reel process
- Each station progressively forms the profile
- Continuous forming and cutting
Complex Shapes Feasible
- Ability to produce unique cross-sections
- Combination of bends, sweeps and twists
- Creativity in design profiles
Close Dimensional Tolerances
- Consistency of roll formed parts
- Tolerances within +/- 0.5 mm
- High degree of accuracy in production
High Production Volumes
- Forming speeds from 10 up to 100 meters/minute
- Cost efficiency for large production runs
- Just-in-time production possible
Material Savings
- Roll formed from coil strips vs. solid sections
- Yields up to 90% from strip stock
- Reduces weight through optimized designs
Lower Costs
- Eliminates welding, machining, drilling
- Lower equipment cost than extrusion
- Operates with small manpower
Flexible Materials
- Cold rolled, galvanized, stainless and aluminum
- Pre-painted coils can be used
- Even exotic alloys are possible
Wide Applications
- Construction, industrial, automotive, furniture
- Custom profiles for unique uses
- Replaces extrusions in many uses
Limitations of Steel Profile Roll Forming
Like any process, roll forming also has certain limitations:
High Initial Tooling Cost
- Sizable upfront cost for roll dies
- Lead time for design and fabrication
- Financial outlay before production
Long Lead Time
- Months needed for design simulation
- Roll tooling takes weeks to manufacture
- Total timeline up to 20 weeks
Economical Mostly for Big Volumes
- High production rates reduce per piece cost
- Short runs under 5000 pieces not optimal
- Frequent roll changes decrease output
Limitations on Size
- Existing coil stock widths constrain maximums
- Thickness limited to about 3 mm for steel
- Narrow strips prone to edge waviness
Strength Limitations
- Cannot match extruded profiles in strength
- Comparatively lower yield and tensile strength
Geometric Constraints
- Not efficient for tapered or stepped profiles
- Limitations in controlling wall thickness
- Maximum length decided by application
Limitations on Profile Features
- Difficult to include internal ribs or complex details
- Hole patterns usually limited to simple slots or circles
- Certain shapes prone to springback after forming
Secondary Processing Needs
- Often needs deburring, straightening and cutting to final size
- Surface finish affected by quality of strip material
- Post-painting or coating may be required
Special Materials Handling
- Stainless steel and aluminum prone to scratching
- May need non-marking rolled and lubrication
- Aluminum can elongate and tear during forming
Quality Control Needs
- Dimensional checks along the length
- Monitoring for internal stresses or cracks
- Consistent roll pressures and speeds crucial
Skilled Operators Needed
- Specialized knowledge to control the process
- Experience with roll wear, strip guidance, troubleshooting
- Long learning curve for new operators
Noise and Safety Considerations
- High noise levels from rotating equipment
- Safety guarding essential for moving parts
- Need to allow scheduled maintenance downtime
Limitations of Line Capacity
- Existing lines restricted to initial design capacity
- Difficult to modify substantially after installation
- Growing volumes may require new equipment
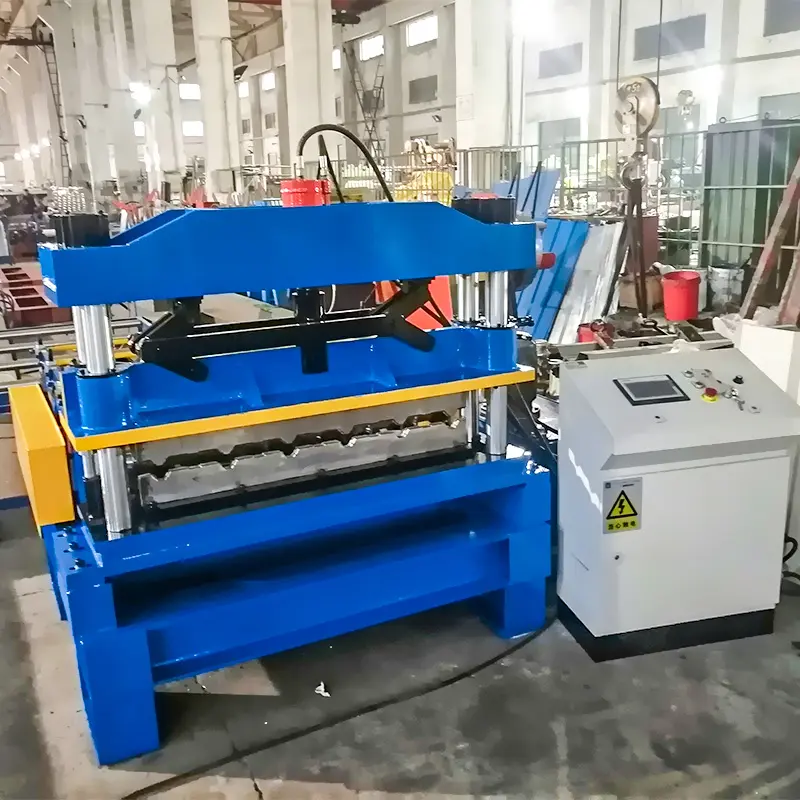
Applications and Uses of Roll Formed Steel Profiles
Roll formed steel profiles have a wide range of structural, industrial and architectural applications:
In Structural Steel Construction
Roll formed sections are used extensively in steel-framed buildings and structures:
- Wall stud framing for curtain walls
- Purlins and girts for roofing and walls
- Structural channels for rafters and supports
- Floor joists and decking sheets
- Light gauge steel trusses
Benefits include high strength, optimized cross-sections, lightweight compared to hot rolled steel, and pre-cut lengths for faster installation.
Solar Panel Framing and Mounting
- Ground and rooftop solar array mounts
- Tilt-up tracker frames
- Racking and railing components
- Panel clipping and support members
Roll formed profiles offer lightweight, corrosion-resistant and high strength solar panel support structures.
Material Handling and Storage Systems
Profiles used in:
- Pallet racking uprights and beams
- Support frames for conveyors
- Mezzanine platforms and walkways
- Industrial shelving frames
- Equipment guarding
Roll formed steel provides durable and customizable solutions for warehouse and factory material handling needs.
In Building Exteriors and Interiors
- Metal roofing and siding sheets
- Canopies, sunshades and porch coverings
- Interior wall cladding and panelling
- Decorative screens and space dividers
- Suspended ceiling sections
Aesthetic and functional building components can be created through roll forming.
Furniture and Displays
- Bed frames and futon frames
- Table and desk legs
- Shelving standards and brackets
- Signage frames and stands
- Decorative screens and dividers
Roll formed parts provide lightweight, high strength support structures for furniture and visual displays.
Automotive Components
- Roof bows and door frames
- Dash panels and reinforcements
- Structural reinforcements
- Pillar sections
- Seating components
- Running boards
Cost-effective automotive sections not requiring extrusion-grade surface finish.
Railing, Safety Barriers and Stairs
- Balcony railings
- Platform railings
- Highway safety barriers
- Warehouse safety guard rails
- Hand rails and supports
- Stair stringers
Roll forming allows customized rail and safety barrier profiles.
Door Frames
- Garage door sections
- Rolling steel doors
- Industrial sliding doors
- Entry doors with steel skins
Economic production of steel door components with high tensile strength.
Roll forming allows optimization of steel profiles for any application requiring linear structural members from 5 to 15 meters length.
Comparison Between Roll Forming and Extrusion
Roll forming and aluminum extrusion are two methods for producing long linear profile sections. How do they compare?
Parameter | रोल बनाना | Extrusion |
---|---|---|
Materials | Steel coil strips | Aluminum logs or billets |
Capital equipment cost | Medium | Very high |
Operating cost | Low | High |
Setup time | Medium | Slow |
Production rate | High | Medium |
Lengths feasible | 5 to 15 m | 5 to 12 m max |
Cross-sections | Customized | Standard shapes |
Strength | Medium | Higher |
Surface finish | Good | Excellent |
Dimensional accuracy | Good | Excellent |
Price per kg | Lower | Higher |
अनुप्रयोग | Industrial, construction | Specialty engineering |
Key Differentiators
- Roll forming is more economical in steel
- Extrusion offers benefits for aluminum
- Roll forming allows more profile customizations
- Extrusion gives superior surface finish and consistency
Overlap Areas
- Solar panel frames
- Railings, safety barriers
- Conveyor and machine framing
- Signage and displays
For overlap applications, choice depends on volumes, price, lead time, and performance needs.
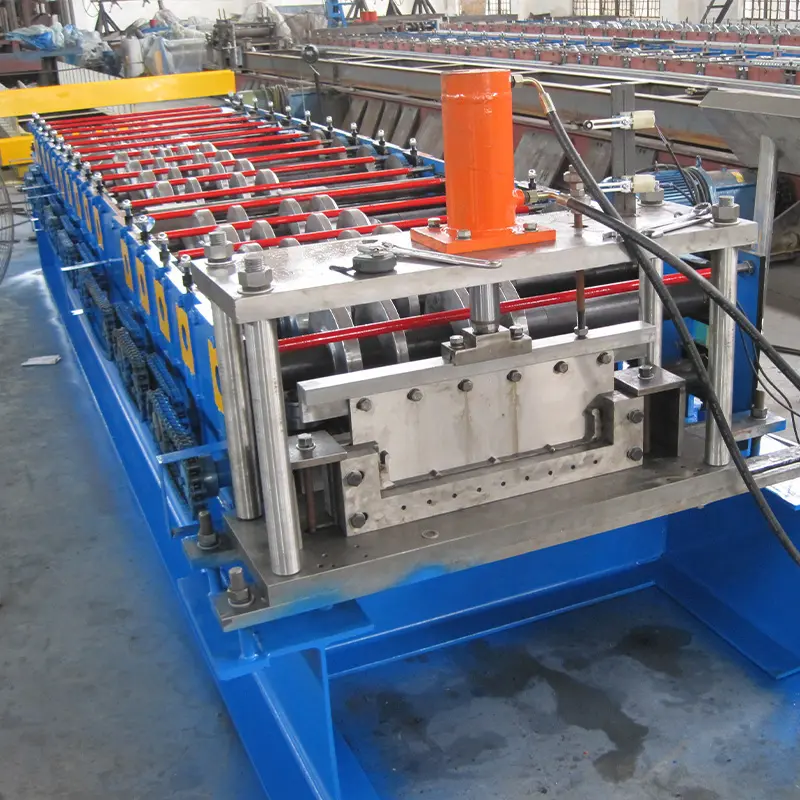
सामान्य प्रश्न
Here are answers to some frequently asked questions about steel profile roll forming:
What thickness of steel can be roll formed?
- For steel, maximum thickness around 3 mm can be reliably formed
- Beyond 3 mm the force required becomes impractical
- Thinner strips around 1 mm thickness are commonly used
What shapes can be roll formed?
- C, U, Z, L, T and angle sections are commonly produced
- Combinations of flanges, ribs, bosses and notches possible
- Cannot make closed hollow shapes or complex internals
How many forming stands are needed?
- Typically 10 to 16 stands for complex shapes
- More stands allow gradual bending and lower pressures
- Simple profiles like studs need 5-6 stands
What tolerances are achievable?
- Roll formed steel profiles achieve +/- 0.5 mm dimensional accuracy
- Tolerances affected by material quality and process factors
- Secondary operations can further improve tolerances
What is the cost of roll forming vs steel fabrication?
- Roll forming is around 15-25% cheaper for long production runs
- Break-even vs fabrication is around 5000-10000 pieces
- Roll forming involves high initial tooling cost
How fast is the production rate?
- Roll forming lines produce around 10 to 100 meters per minute
- Maximum speed depends on profile complexity
- Typical actual production rates are 20-40 m/min
What are common roll forming defects?
- Waviness or camber along the profile length
- Flare or flare scuff at cut ends
- Twist or bow over the length
- Thickness variations
- Surface marks or scratches
What safety is required?
- Enclosing guards for all moving parts
- No operation without guards in place
- E-stop buttons within easy reach
- Nip point markers and instruction plates
- Noise reduction measures
How to reduce roll forming cost?
- Optimize profile design for material and production efficiency
- Use pre-painted coils rather than post-painting
- Re-grind roll dies periodically to increase life
- Level production schedule and reduce quick changeovers
- Prevent unplanned downtime through maintenance
What factors affect quality?
- Consistent roll calibration and pressures
- Strip feed alignment and roll tooling condition
- Type and temperature of lubricant
- Vibration insulation for stands
- Controlling line speed during start/stop
- Regular quality checks and measurement