Overview of arch building panel roll forming machine
Arch building panel roll forming machine refers to continuous cold roll-forming equipment engineered to produce lightweight metal panels with embossed ribbed profiles. These high-efficiency roll formers shape flat aluminum or steel coil into arched panels serving aesthetic and structural purposes in modern buildings.
Key features:
- Efficiently mass produce linear panel sections with ribs
- Widths from 1000mm up to 3000mm possible
- Metal thickness from 0.5mm to 1.2mm
- Materials: pre-painted steel, anodized aluminum etc.
- Support various rib configurations and spacing
- Quick changeover rolles modify profiles
- Automatic run-out tables for finished arches
Let’s explore the working principle, main components, capabilities and selection criteria for arch panel roll formers in greater detail.
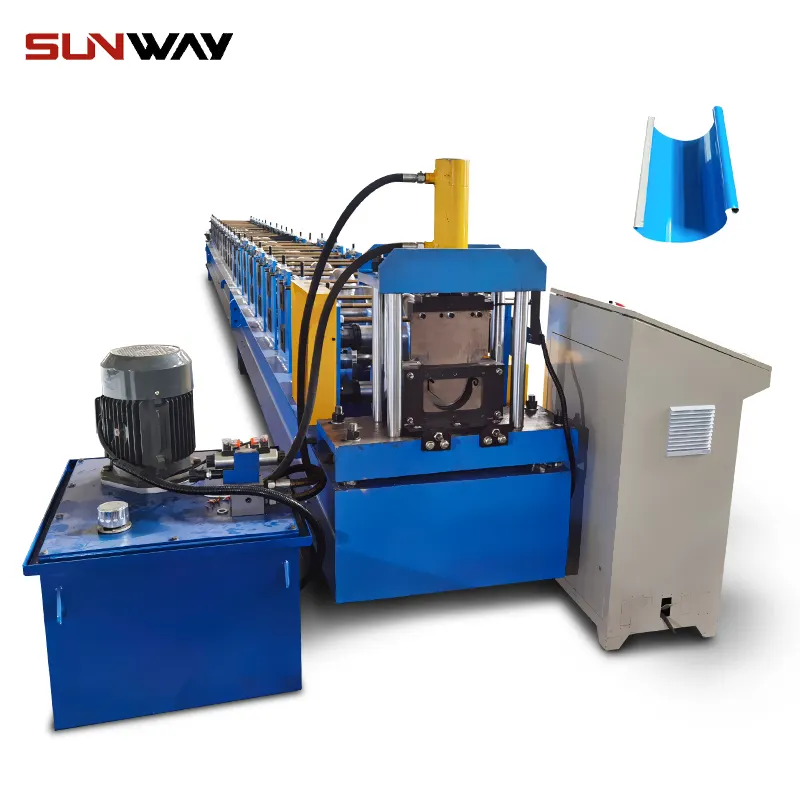
Machine Types
Type | Description |
---|---|
Fully Automatic | Complete inline coil processing with transfers |
Structural Section | Heavy frames suit widest sheet gauges |
Standard Section | For 0.7mm to 1.2mm metals |
Customized | Tailor strip feeding and runouts |
Table 1: Main arch panel roll former types by automation level and construction
Larger structural roll formers provide the highest throughput while customized options adapt for unique infeeds and factory layouts. Fully automatic machines minimize labor.
Working Principle of arch building panel roll forming machine
The progressive cold roll-forming process shapes arch panel profiles:
- Coil strip pretreated for color/finish enters machine
- Gradually formed by a series of bending & shaping stations
- Rib configuration defined by male/female roller dies
- Final station establishes complete panel cross-section
- Formed arches exit on powered conveyors
- Operators bundle finished panels for inventory
Servo feed controls combined with PLCs precisely index strip through equipment synchronizing multi-step forming into arch.
Machine Components
Component | Description |
---|---|
डेकोइलर | Feeds strip from coil payoff keeping tension |
Feed Table | Handles strip positioning and rate pacing |
Forming Stands | Progressively cold-work metal via bending |
Runout tables | Supports formed arches for cooling and exit |
Control Panel | HMI sets forming parameters plus monitoring |
Table 2: Overview of main functional modules in an arch panel roll former line
Latest CNC roll lines integrate decoiler, forming heads, exit transfers and controls for synchronized automation.
Materials, Finishes and Sizes
Common architectural panel specifications covered:
Parameter | Capabilities |
---|---|
Width | 1000mm to 3000mm+ |
Material Thickness | 0.5mm to 1.2mm |
Materials | Pre-painted steel, anodized aluminum etc |
Rib Height | 15mm to 50mm |
Rib Pitch | 150mm to 400mm variable |
Table 3: Overview of typical architectural metal panel dimensions
Discuss requirements with roll former manufacturers to specify compatible coils for minimum bending radii, grain orientation and environmental exposure resilience.
Customization Options
Capabilities accommodating customer-specific architectural elements:
- Width changes through quick-change flow drill heads
- Multi-thickness prepainted aluminum/steel coils
- Various rib configurations by changing top/bottom rollers
- Custom panel inner reinforcements
- Continuous vs fixed length panels
- Logos/patterns/perforations by changing top rolls
- Packaging assistance available
Table 4: Arch panel profile variations offered by roll former manufacturers
Close customer collaboration during design finalization ensures manufacturability.
-
विद्युत कैबिनेट फ्रेम रोल बनाने की मशीन
-
दीन रेल रोल बनाने की मशीन
-
केबल सीढ़ी रोल बनाने की मशीन
-
पीवी माउंटिंग ब्रैकेट सी शेप प्रोफाइल रोल बनाने की मशीन
-
केबल ट्रे रोल बनाने की मशीन
-
पीवी माउंटिंग ब्रैकेट रोल बनाने की मशीन (एचएटी / ओमेगा प्रोफाइल)
-
पीवी माउंटिंग ब्रैकेट जेड शेप प्रोफाइल रोल बनाने की मशीन
-
सौर बढ़ते अकड़ चैनल रोल बनाने की मशीन
-
स्ट्रट चैनल रोल बनाने की मशीन
Suppliers and Pricing
Manufacturer | Location | Indicative Pricing |
---|---|---|
ASI Solutions | United States | $250,000 – $750,000 |
Formtek | Canada | $200,000 – $600,000 |
Margaret | Taiwan | $150,000 – $500,000 |
BUSSpadora | इटली | €200,000 – €800,000 |
Table 5: Sample of major arch building panel roll former manufacturers and cost range indicators
Total cost varies based on production line speed, level of automation and extent of customization impacting tooling/fabrication expenses.
Installation and Operation
Implementing arch panel roll forming lines requires planning:
- Space – Overall footprint area allowing safe access
- Floor – Reinforced flat concrete able to handle loads
- Power – Voltage, phase to support decoiler/hydraulics
- Layout – Continuous material flow preventing backtracking
- Controls – Touchscreen HMI for monitoring operation
- Safety – Guarding, e-stops, locks per regulations
- Training – Thorough on-site operator guidance
Coordinate provisions in advance for rapid commissioning. Validate all safeguards before operation.
Maintenance Guidelines
Reliable functioning requires consistent maintenance:
- Schedule – Follow prescribed maintenance intervals
- Lubrication – Bearings, slides, conveyors, and decoiler
- Hydraulics – Pressures, cylinders, valves operation
- Filters – Replace oils, elements as needed
- Wiring – Check terminals, junctions for security
- Alignments – Confirm coil feeds, guides, and decoiler function
- Safety – Inspect e-stops, guarding, locks functionality
Execute prescribed preventative maintenance procedures before minor issues become major. Always lockout power before interventions.
Choosing an Arch Panel Roll Former Manufacturer
Consider key selection criteria:
- Experience – Years manufacturing roll form equipment
- Construction – Unitized frames prevent sheet meandering
- Precision – Component machining and finish for consistency
- Safety – UL/CE certification for frameworks and electricals
- Support – Installation help, operator training, manuals
- Customization – Openness to unique aesthetic options
- Cost – Secondary to production volume guarantees
Solicit multiple bids while interviewing client references. Compare proposals beyond just acquisition pricing – seek guaranteed throughput volumes from reputable manufacturers.
Pros and Cons
Advantages | Disadvantages |
---|---|
High linear feet productivity up to 30m per minute | Fixed tooling suits repeat panel profiles without changes |
Quick roll changeouts enable different geometries | Specifying customs adds lead time |
Servo precision feed improves consistency | Specialized technicians needed for complex maintenance/repair |
Compact compared to tandem press lines | Initial investment higher than intermediate sheet stamping approaches |
Table 6: Tradeoffs when implementing arch panel roll forming equipment
Maximizing continuity merits equipment cost when surpassing over 5 million linear feet for major construction projects.
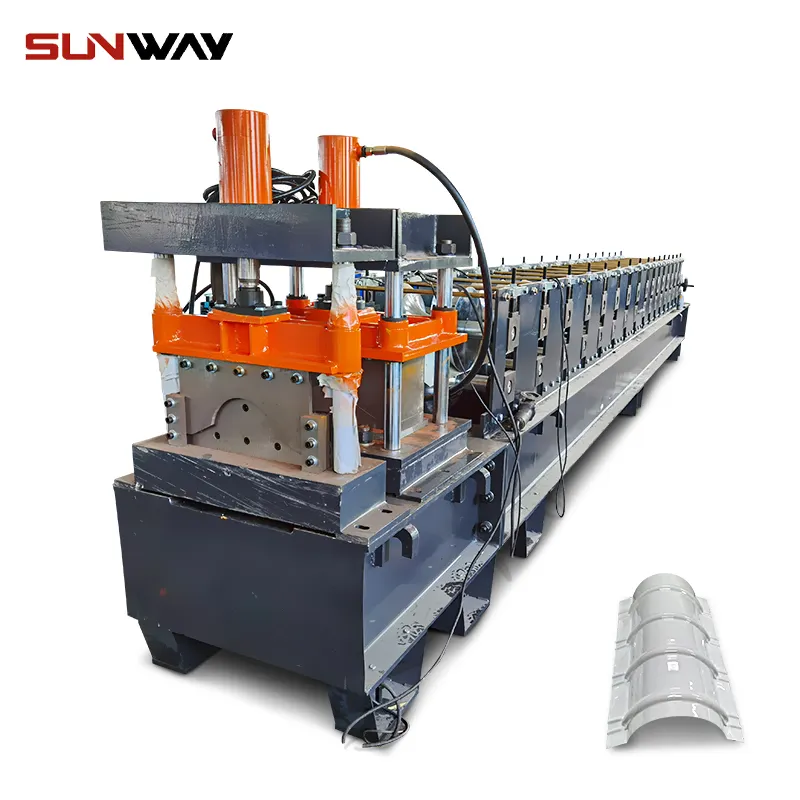
FAQs
Q: What level of quality is required for substrate coils to avoid surface issues after painting?
A: Architectural standard practice requires minimum hot rolled steel coil properties of G90 galvanization combined with machine leveling achieving 1/4 I-unit maximizing flatness without ripple. Aluminum requires 5005-H14 temper for optimal roll forming strength/surface finish balance.
Q: What are common clear coat options for pre-paint exterior architectural metal panels?
A: High durability exterior acrylic urethanes or PVDF coatings apply color primer beneath matte clear topcoats blocking UV degradation for 30-year finishes exceeding AAMA 2604. Avoid silicone-modified polyesters. Roll coating facilitates optimal grain orientation.
Q: Can a single machine make different ribbed wall panel profiles by changing roller dies?
A: Within maximum frame width limits, flexible roll formers reuse common infeed tables while changing only ribbed profiling heads to cost-effectively adapt for new architectural aesthetics differentiated by embossed patterns. Section transitions take approximately 4 hours offline.
Q: What safety standards should North American manufacturers meet for CE-level compliance?
A: Seeking ISO 13849-1 certification for safety-related control systems combined with area guarding rated for at least IP54 ingress protection ensures appropriate risk reduction recognized by international standards. Third party validations add credibility verifying rigorous critical examination.
Q: How does European and North American equipment for architectural sheet metal forming differ?
A: Premier continental suppliers implement advanced servo feed controls with tighter pitches between progressive heads enabling quicker changeovers plus PLC interfaces rivaling top American lines, however at 15-30% discounted acquisition costs. Labor savings from faster product transitions offset initial outlay over 1-2 years.