Pu sandwich panel roll forming machines are equipment used to produce polyurethane (PU) sandwich panels in a continuous process. This comprehensive guide covers everything related to pu sandwich panel roll forming from working principles, types, parts, parameters, to operation, maintenance, and more.
Overview
PU sandwich panel refers to a composite panel structure made of a PU foam core sandwiched between and bonded to two metal facer sheets, typically steel or aluminum. The metal sheets provide strength and rigidity, while the PU foam core gives thermal insulation.
Pu sandwich panels are used extensively in industrial and cold storage buildings, warehouses, factories, commercial complexes etc. They offer superior insulation compared to other building materials along with structural strength. Their growing popularity is driving demand for efficient pu sandwich panel production lines.
Roll forming allows high speed, continuous production of sandwich panels in varying dimensions customized as per application requirements. Automated pu sandwich panel roll forming machines offer advantages like high output, consistency, and flexibility compared to manual production.
This guide provides a deep dive into all key aspects of pu sandwich panel roll forming machine technology.
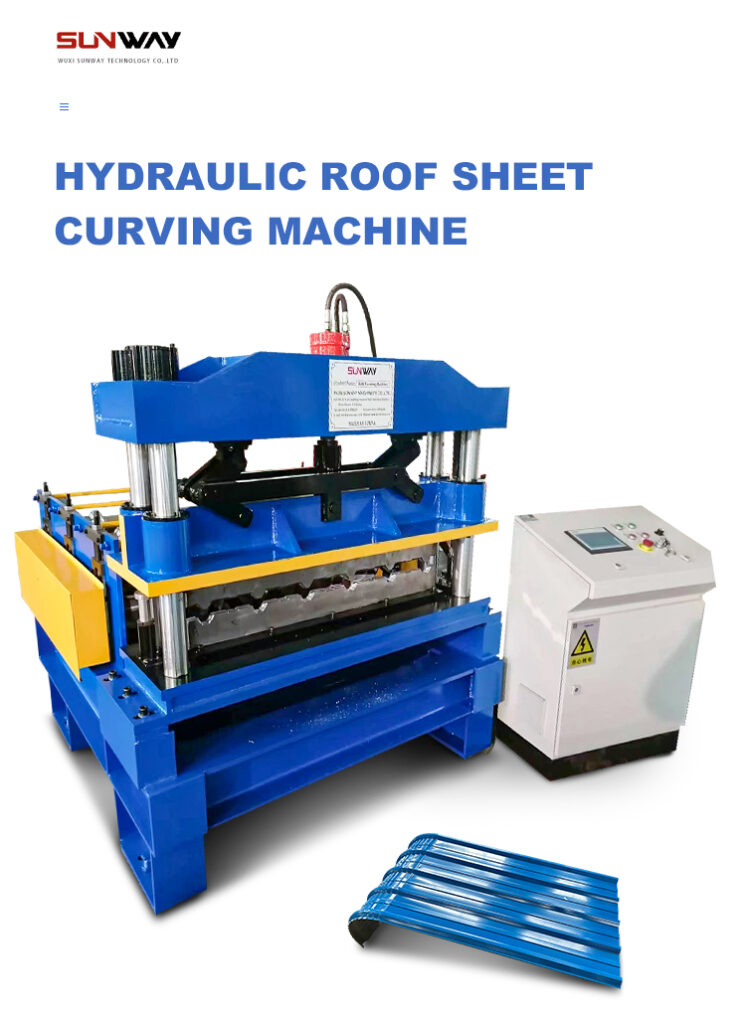
Pu Sandwich Panel Roll Forming Machine Types
Pu sandwich panel production lines are available in different configurations designed to handle widths from 1000mm to 1500mm and more. Main types of pu sandwich panel roll forming machines include:
Machine Type | Description |
PU Sandwich Panel Roll Forming Line | Complete automated line for forming and filling PU foam in metal sheets |
PU Sandwich Panel Roll Former | Only the roll forming section for bending sheets |
Double Layer Roll Forming Machine | Forms the two facer sheets separately |
PU Sandwich Panel Laminating Machine | Bonds facer sheets post production |
The machine type impacts production process, output rate, customization flexibility, cost and other factors. PU sandwich panel roll forming lines allow end-to-end automated production in one line.
Working Principle
The working principle of pu sandwich panel roll forming machine involves:
- Uncoiling & Feeding: Two strip metals (steel/aluminum coils) are loaded and passed through a de-coiler to uncoil and feed into the line.
- रोल बनाना: The sheets go through a series of rolling stands arranged in tandem. Guided by rollers and gears, the sheets are pressed and bent progressively into designed profiles.
- PU Foam Injection: Liquid PU chemicals are mixed, reacted and foamed to the desired density before continuously injecting between the formed profile sheets.
- Cooling & Curing: The injected PU foam expands and cures into solid form as it moves down the line, bonded to the inner sheets.
- Cutting: After cooling, the formed sandwich panel is cut to length by an automatic cutting machine.
- Product Output: Continuous pu sandwich panels of fixed lengths exit the line automatically for collection.
Inline processes like punching, embossing, spraying, inkjet printing can be integrated as per application needs. The pu sandwich panel machine working process enables high speed, uniform production without need for molds. Automated lines ensure stability, precision and consistency difficult in manual operations.
Main Parts of Machine
Key parts in pu sandwich panel roll forming machine:
Part | Function |
De-coiler and Sheet Guiding Mechanism | Smooth uncoiling and straight feeding of metal coil sheets into the production line preventing skewing |
Roll Forming Stands | Rolling metal sheets progressively through series of stands into designed section profiles |
PU Foam Machine | Blending, foaming and injecting PU chemicals to fill space between formed sheets |
Curing Oven | Heating for foam expansion and curing bonded with facer sheets |
Cutting Machine | Trimming formed sandwich panels at fixed lengths |
Supporting Rollers | Guides movement of sheets during production without damage |
नियंत्रण प्रणाली | Automates production parameters, detects issues, ensures smooth running |
Technical Specifications
Pu sandwich panel roll forming machine specifications vary across models and customization requirements. Below table summarizes typical specification ranges:
Parameter | Range |
Production Speed | 20-40m/min |
प्रभावी चौड़ाई | 1000-1500mm or more |
मोटाई | 50-300mm |
Length | Customized as needed |
Temperature | Up to 230oC in oven |
Voltages | 230V/380V/415V as standard |
शक्ति | 15-100kw depending on model |
Working Process Details
Roll formed pu sandwich panel production involves sequential working processes:
1. Material Feeding
- Facer sheet coils of thickness 0.3-1.0mm fed into de-coiler
- De-coiler ensures controlled uncoiling without sudden jerks
- Sheet guiding mechanism straightens any warp or skew
- Friction grip drive rollers engage and feed sheet through production line
- Optional accumulating conveyor inserted for process flexibility
2. Sheet Forming
- Sheet enters forming section with initial sheet guiding stands
- Progresses through series of rolling stands (10-16 typically)
- Each rolling stand bends sheet incrementally by few degrees
- Final stand gives complete designed profile shape – trapezoidal, corrugated etc.
- Eccentric shafts allow variation in profiling
- Top and bottom sheets formed similarly before merging
3. PU Foam Filling
- Liquid PU raw materials (polyol/isocyanate) stored in tanks
- Precise high pressure pumps control flow rates
- Chemicals mixed in impingement chamber before reaction
- Reacted chemicals fed to foaming chamber
- Foaming agent creates bubbles for required density
- Foamed PU chemicals injected between formed sheets
- Automated process ensures correct density and uniform filling
4. Curing and Cooling
- Sandwich panel with injected foam enters temperature controlled oven
- Heating causes foam expansion filling gap between sheets
- As panel moves down cooling section, foam cures bonding with sheets
- Controlled cooling cycle ensures proper curing without blisters
- Optimized oven length reduces process time
- Chilled water circulation used for fast cooling
5. Cutting and Output
- Cured pu sandwich panel profiles cut by automated cutting machine
- Length cutting tolerance within +/- 1mm
- Continuous panels of fixed length exit system
- Output sandwich panels stacked manually or using handling equipment
- Inline process stations like punching, spraying possible
6. Control System
- Centralized control system monitors and coordinates entire line
- Touch screen allows input of production parameters
- Temperature, speed, pressure, level sensors connected
- Monitoring for faults, bottlenecks, safety issues
- Optimized programming maximizes yield and system reliability
Customization Flexibility
Pu sandwich panel roll forming allows significant customization as per user needs:
Element | Customization Capability |
Dimensions | – Width from 1000mm to 1500mm or more – Thickness up to 300mm – Length as needed |
Surface Profile | – Various profiles like trapezoidal, corrugated etc. – Changeable rollers for new profiles – Embossed surfaces possible |
Facer Sheets | – Steel, aluminum, galvanized steel – Thickness 0.3-1.0mm or more – Coatings, pre-painted sheets |
Foam Density | – Density from 30-100 kg/m3 – Higher density = better insulation |
Accessories Integration | – Embossing rollers – Punching equipment – Shearing, drilling, notching – Decoilers, recoilers – Conveyors, panel handling system |
Automation Level | – Manual to fully automated options – Dependent on budgets, skill levels |
Choosing Pu Sandwich Panel Roll Forming Machine Suppliers
With so many pu sandwich panel roll forming machine manufacturers to choose from in China and internationally, proper supplier selection is critical for getting good quality equipment. Below are key criteria for shortlisting suppliers:
Parameter | Checks |
Machine Specifications | – Technical capacity – speed, width, thickness etc – Production output meets current and future demand – Check technical datasheet |
Build Quality | – Robust fabrication of parts – Precision engineered – Finishing and coatings prevent rusting |
Customization Offered | – Flexibility for sheet types, foam density, accessories etc – Integration capability with other equipment – Additions, modifications possible in future |
Control Systems | – Level of automation and ease of operation – Monitoring and safety features – Diagnostics capability |
Additional Services | – Technical advice during purchase – Shipping/transport coordination – Installation/commissioning support – Operator training services – Maintenance contracts |
Cost | – Equipment cost fitting budgets – Total cost of ownership favorable – Cost advantage versus competitors |
Company Credentials | – Experience and installations record – Client reviews and ratings – Local after-sales network – Financial stability |
Approximate Price Range:
- Basic PU sandwich panel roll forming machine: $18,000 – $38,000
- Higher capacity PU sandwich panel production line with accessories: $65,000 – $120,000
Pricing varies based on specifications, production output targets, width of panels produced, level of automation, accessories integrated etc. Larger capacity fully automated lines are higher priced while lower budget options with manual features are also available.
Installation & Commissioning
Proper installation and testing of the pu sandwich panel roll forming machine is key before full scale production. Below are key guidelines:
- Civil structure construction as needed – rails, trenches, floor flatness
- Unloading machine from truck using forklifts/cranes safely
- Assembling various sections according to drawing if required
- Levelling stands, securing to ground as per manual
- Electrical connections to control panel & drives per voltage specs
- Pneumatic/hydraulic systems connections if present
- Trial run checking for any loose parts, odd sounds
- Inch by inch jogging initially, then slow and high speed test runs
- Monitoring current consumption during startup
- Checking emergency stops, safety mechanisms activation
- Integrating other upstream/downstream equipment
- Testing against sample production orders and inspection
- Fine tuning until optimal performance achieved
- Operator training during installation & commissioning
- Initial supervised production before handover
Operation & Working
Pu sandwich panel roll forming machines can be operated in manual mode for low volume requirements. Automated lines offer minimal user intervention for high quantity production.
Typical operating steps:
- Turn on main power to control panel
- Set production speed, oven temperature through HMI
- Feed coil sheets into de-coiler
- Jog buttons to inch sheets into forming section
- Select recipe on interface for desired panel specifications
- Start button to activate production
- Monitor line operation, inspect product quality
- Stop equipment for coil changeovers
- Schedule breaks as needed
- Record production data
- Clean equipment at end of shift
Do’s and Don’ts:
Do’s | Don’ts |
– Follow manufacturer instructions | – Exceed machine capacity |
– Use certified accessories only | – Modify safety mechanisms |
– Maintain cleanliness | – Ignore warning signs |
– Employ skilled workforce | – Compromise on maintenance |
Maintenance & Precautions
Scheduled maintenance activities ensure longevity and performance of pu sandwich panel roll forming machines:
Daily:
- Inspect panels visually
- Check drive shafts, gears
- Monitor wear on guides
- Ensure lubrication
- Verify fluid levels
- Clean debris accumulation
Monthly:
- Thorough cleaning
- Bolting checks
- Electrical terminations
- Calibrate sensors
- Roller surface inspection
- Test emergency stops
Quarterly:
- Inspect chain/gearbox
- Hydraulic unit checks
- Descaling
- PU cleaning if needed
- Review safety mechanisms
- Fine tune control parameters
Yearly maintenance Contracts from OEM supplier proves beneficial for servicing support.
Safety Precautions
- Earthing connections must be proper
- Ensure interlocks & barriers in place
- Never operate with panels removed
- No loose clothing/jewelry permitted
- Strictly implement lockout procedures
Proper operating & maintenance procedures coupled with safety ensures smooth functioning and increased working life of roll forming machines.
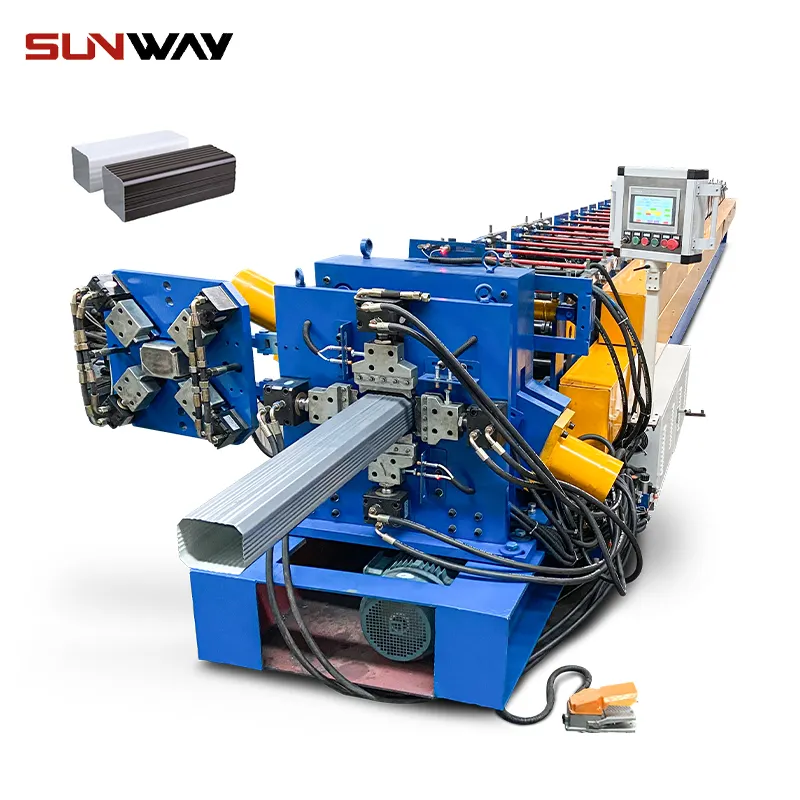
Pros and Cons Analysis
Advantages of PU Sandwich Panel Roll Forming Machine:
- High and consistent production speed
- Low labor cost due to automation
- Excellent accuracy and product uniformity
- Different surface profiles can be formed
- Adjustable for different sheet thickness and coil widths
- Low maintenance compared to hydraulic presses
- No molds required unlike box panel production
- Surface scratch-resistance from roll forming process
- Energy efficient forming process
- High and consistent production speed and volumes
- Flexibility to change parameters through software
Limitations of PU Sandwich Panel Roll Forming Machine:
- Initial equipment investment is moderately high
- Requires some degree of technical skill for operation
- Roller profile changes needed for making design changes
- Limited material thickness that can be formed (up to 1.2mm sheets)
- Shorter product lengths (Generally <25m possible)
- Settings readjustment required for each coil material changeover
- Secondary cutting and finishing needed for final products