Overview of Roll Forming Machine Design
La design of a roll forming machine plays a crucial role in ensuring precision, efficiency, and durability in metal forming processes. Whether for roofing sheets, solar mounting brackets, or automotive components, a well-designed roll forming machine can deliver high-speed, high-accuracy production with minimal material waste.
Key Elements of Roll Forming Machine Design
✅ Roll Tooling & Roller Stations – Determines profile accuracy and material flow.
✅ Frame & Structural Components – Ensures stability and vibration control.
✅ Drive System & Motor Power – Affects speed, torque, and energy efficiency.
✅ Cutting & Punching Mechanism – Provides precise shaping and hole placement.
✅ Control System & Automation – Enhances efficiency through PLC, CNC, and IoT integration.
In this guide, we’ll explore:
✅ Fundamentals of roll forming machine design
✅ Detailed breakdown of key components
✅ Best materials for roll forming machine construction
✅ How to optimize roll forming machine efficiency
✅ Latest innovations in roll forming design for 2025
Let’s dive in!
Fundamentals of Roll Forming Machine Design
UN machine de formage de rouleaux consists of multiple roller stations that gradually shape a metal sheet into a desired profile. The design must account for:
✅ Propriétés des matériaux – Different metals require different roller designs.
✅ Complexité du profil – Simple vs. intricate shapes determine roller station count.
✅ Vitesse de production – High-speed machines need reinforced structural designs.
✅ Cutting & punching needs – Some profiles require pre-cutting, post-cutting, or inline punching.
Basic Structure of a Roll Forming Machine
Composant | Fonction |
---|---|
Dérouleur | Feeds the raw metal coil into the machine |
Guiding & Leveling System | Aligns the metal sheet for accurate forming |
Stations de rouleaux | Gradually shapes the metal through multiple passes |
Drive System (Motor & Chain Drive) | Provides power to rotate rollers |
Cutting & Punching Unit | Cuts the profile to the required length |
Control System (PLC, CNC, IoT) | Automates and monitors the roll forming process |
Exit & Stacker System | Collects finished products for packaging |
Conseil de pro : A well-designed roll forming machine reduces material waste by up to 30% while increasing vitesse de production par 40%.
Key Design Components of a Roll Forming Machine
The efficiency of a roll forming machine heavily depends on the design of its key components.
1. Roll Tooling & Roller Stations
- Matériau : High-strength tool steel or carbide-coated rollers.
- Design Consideration: The roller pass schedule should ensure gradual forming to prevent stress fractures.
- Optimization: CNC-machined rollers improve accuracy and longevity.
2. Drive System & Motor Power
- Types : Chain drive, gearbox-driven, or servo motor systems.
- Power Requirement: Higher power needed for thicker materials or high-speed production.
- L'innovation : Moteurs asservis enhance precision and energy efficiency.
3. Cutting & Punching Mechanism
- Types : Hydraulic cutting, flying shear, or rotary die cutting.
- Design Consideration: Post-cut systems work best for continuous high-speed production.
- Optimization: Servo-driven punching units ensure accurate hole placements.
4. Frame & Structural Components
- Matériau : Heavy-duty steel frame to reduce vibration and increase machine lifespan.
- Design Factor: Reinforced structures ensure stability at high speeds.
Did you know? A well-designed roll forming machine can last 15-25 ans with proper maintenance!
Best Materials for Roll Forming Machine Construction
The choice of matériaux impacts the durability, precision, and efficiency of a roll forming machine.
Comparison of Materials Used in Roll Forming Machine Design
Composant | Best Material | Reason |
---|---|---|
Rouleaux | High-strength tool steel (D2, SKD11) | Wear-resistant, long-lasting |
Cadre de la machine | Heavy-duty structural steel | Reduces vibration, ensures stability |
Cutting Blades | High-carbon steel or tungsten carbide | Maintains sharpness, reduces replacement costs |
Système d'entraînement | Hardened alloy gears | Withstands high torque and stress |
Sensors & Electronics | Industrial-grade PLC components | Ensures reliability in harsh environments |
Conseil de pro : Carbide-coated rollers last 3x longer than standard steel rollers!
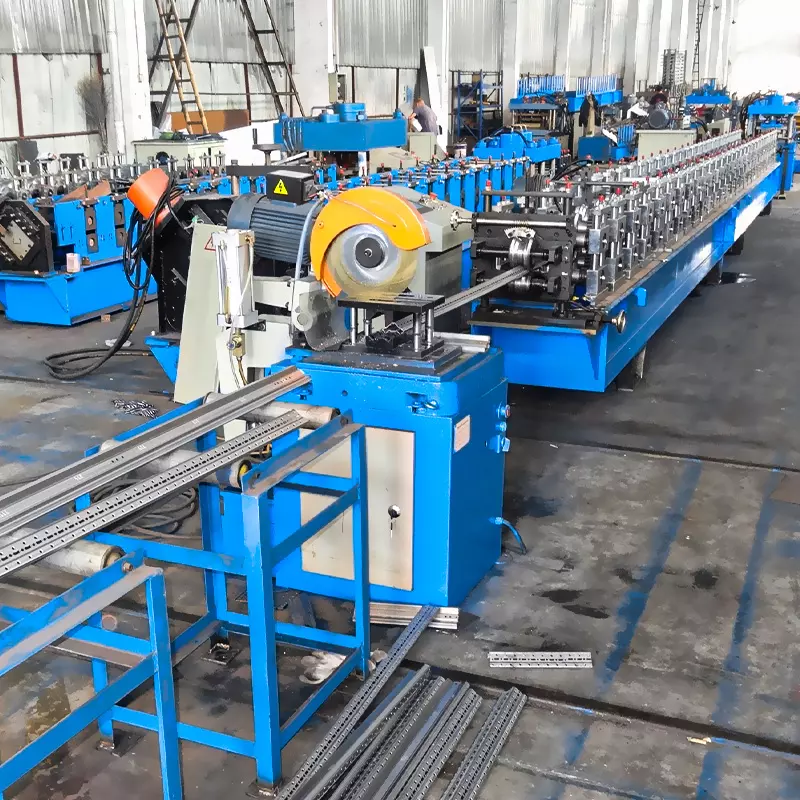
How to Optimize Roll Forming Machine Efficiency
Optimizing roll forming machine design can increase productivity, reduce waste, and enhance precision.
Best Practices for Maximum Efficiency
Optimization Method | Avantages |
---|---|
Use CNC-machined rollers | Veille high accuracy and minimal material stress |
Implement servo-driven motors | Réduit energy consumption et improves speed control |
Upgrade to IoT-enabled monitoring | Allows real-time diagnostics and remote troubleshooting |
Use reinforced machine frames | Réduit vibration and increases stability |
Employ AI-based defect detection | Minimise waste and improves quality control |
Upgrading to an IoT-enabled roll forming machine reduces maintenance costs by 25%!
Latest Innovations in Roll Forming Machine Design for 2025
As manufacturing evolves, roll forming machine design is incorporating cutting-edge technology to improve performance.
1. AI-Powered Roll Forming Machines
- Smart sensors detect defects in real time, reducing waste.
- AI-based adjustments optimize roller pressure and speed dynamically.
2. Industry 4.0 & IoT Integration
- Machines are now cloud-connected, permettant remote monitoring and predictive maintenance.
- Operators can adjust settings via mobile apps for improved efficiency.
3. Hybrid Servo-Hydraulic Cutting Systems
- Combines precision of servo motors avec power of hydraulique découpage pour flawless edge finishing.
- Réduit wear and tear on cutting components.
Future-proof your production by investing in next-gen roll forming technology!
Common Problems & Solutions in Roll Forming Machine Design
Even with a well-designed roll forming machine, operational challenges can arise due to material inconsistencies, roller misalignment, or mechanical wear. Understanding these issues and implementing preventive solutions can significantly improve production efficiency.
Troubleshooting Guide for Roll Forming Machine Design Issues
Enjeu | Possible Cause | Solution |
---|---|---|
Profile Distortion or Warping | Incorrect roller alignment or uneven pressure | Adjust roller stations and check roller pressure settings |
Excessive Material Waste | Improper cutting mechanism or incorrect feed rate | Optimize cutting precision and calibrate feed settings |
Roller Wear & Tear | Low-quality roller material or lack of lubrication | Utilisation high-strength tool steel and apply proper lubrication |
Inconsistent Hole Punching | Misaligned punching dies or weak hydraulic system | Realign dies and check hydraulic pressure levels |
Machine Overheating | Insufficient cooling system or motor overload | Upgrade cooling system and ensure proper motor sizing |
Conseil de pro : Régulière roller realignment et servo-driven adjustments can improve profile accuracy by 30%.
Future Trends in Roll Forming Machine Design for 2025
Avec Industrie 4.0 et smart manufacturing, roll forming machines are becoming more intelligent, efficient, and adaptive.
Top Innovations in Roll Forming Machine Design
1. Contrôle de qualité piloté par l'IA
- Capteurs alimentés par l'IA detect defects in real-time, reducing material waste.
- Améliore product accuracy and reduces rejection rates.
2. Technologie des jumeaux numériques
- Virtual simulations allow machine testing before production, optimizing efficiency.
- Réduit trial-and-error costs in machine setup.
3. Advanced Servo Motor Integration
- Servo-controlled roller stations provide better speed control et energy savings.
- Veille consistent material feed and precise forming.
4. Smart IoT-Connected Roll Forming Machines
- Active remote diagnostics and predictive maintenance.
- Réduit unexpected downtimes by 40%.
Upgrading to AI-powered roll forming machines can increase production efficiency by up to 50%!
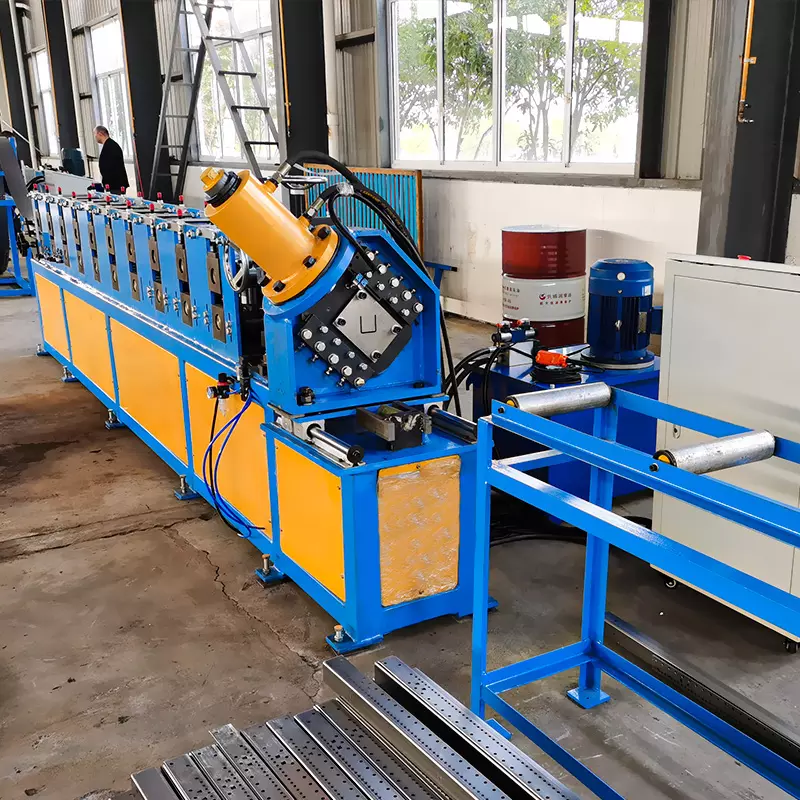
Roll Forming vs. Extrusion: Which is Better?
Both roll forming and extrusion are used for metal profile production, but they serve different applications.
Comparaison entre le laminage et l'extrusion
Fonctionnalité | Forme rouleau | Extrusion |
---|---|---|
Process Type | Continuous cold forming | Heated material pressed through a die |
Compatibilité des matériaux | Acier, aluminium, cuivre | Aluminum, plastic |
Vitesse de production | Higher for long profiles | Slower for custom profiles |
Coûts d'outillage | Higher initial investment, lower long-term cost | Lower upfront cost, but higher per-unit cost |
Meilleur pour | Roofing sheets, solar brackets, automotive parts | Complex aluminum profiles |
Verdict : If you need high-speed production of long metal profiles, roll forming is the best choice.
Automation in Roll Forming Machine Design
Automation is transforming roll forming from a manual process to a high-precision, fully autonomous system.
Key Benefits of Automation in Roll Forming Machines
Fonctionnalité | Bénéfice |
---|---|
AI-Powered Defect Detection | Reduces waste and improves quality control |
PLC & CNC Integration | Ensures precision and reduces manual adjustments |
Automated Profile Adjustments | Minimizes downtime when switching between profiles |
IoT-Enabled Monitoring | Allows real-time diagnostics and performance tracking |
Energy-Efficient Servo Motors | Lowers operational costs and improves sustainability |
Fully automated roll forming machines from Machine Sunway improve production efficiency by up to 40%!
Maintenance Strategies for Roll Forming Machine Longevity
Correct maintenance assure longer machine lifespan and uninterrupted production.
Essential Maintenance Checklist for Roll Forming Machines
Tâche | Fréquence | Objectif |
---|---|---|
Lubricate Rollers & Bearings | Hebdomadaire | Prevents wear and tear |
Check Roller Alignment | Mensuel | Ensures accurate profile production |
Inspect Cutting Mechanism | Trimestrielle | Prevents defective cuts and misalignment |
Clean Machine Components | Quotidiennement | Removes dust and debris that can affect performance |
Update Software & Calibration | Semi-Annually | Keeps automation functions optimized |
Conseil de pro : Scheduled maintenance can extend machine lifespan by 50% et reduce failures by 70%.
FAQ: Roll Forming Machine Design & Best Practices
1. What factors influence roll forming machine design?
Key factors include material type, profile complexity, roller station count, and automation level.
2. Can I customize a roll forming machine for my specific profile?
Oui ! Machine Sunway specializes in conception de machines de profilage sur mesure tailored to unique production needs.
3. What is the best material for roll forming machine rollers?
High-strength tool steel (D2, SKD11) or carbide-coated rollers provide the best durability and precision.
4. How many roller stations does a typical roll forming machine have?
The number varies from 6 to 30+, depending on the profile complexity.
5. What is the lifespan of a well-designed roll forming machine?
With proper maintenance, a high-quality roll forming machine can last 15-25 ans.
6. What industries benefit from roll forming machines?
Industries such as construction, automotive, racking & shelving, HVAC, and renewable energy rely on roll forming machines for precise and efficient steel processing.
7. Where can I get a custom-designed roll forming machine?
Pour high-quality, customizable roll forming machines, visit WUXI SUNWAY MACHINERY CO., LTD.
Réflexions finales
La design of a roll forming machine significantly impacts efficiency, precision, and production costs. Whether you need a standard or custom roll forming solution, investing in advanced design features assure long-term profitability.
WUXI SUNWAY MACHINERY CO., LTD est un fabricant mondial de premier plan of roll forming machines, offering custom-built solutions, expert support, and cutting-edge technology.
Want a custom-designed roll forming machine? Contact us today!