Perfiladoras de tejados metálicos son equipos utilizados para convertir chapas metálicas planas en paneles personalizados para tejados y paredes. Estos equipos tienen una gran demanda debido al aumento de la actividad constructora y los proyectos de infraestructuras. Hablamos del funcionamiento, los tipos, las consideraciones de coste y los proveedores de estas máquinas.
Equipo de perfilado de tejados metálicos
Una perfiladora de tejados metálicos toma una bobina de chapa metálica plana y la procesa a través de una serie de rodillos para darle forma en varios perfiles largos de panel. Los perfiles de panel que se producen habitualmente son ondulados, acanalados, planos, de junta alzada, de fijación oculta y de otras formas personalizadas.
Los principales componentes de una máquina perfiladora de chapas metálicas para tejados son:
- Desenrollador para sujetar la bobina de chapa
- Sección de alimentación con rodillos de arrastre para alimentar la hoja
- Estaciones de conformado con matrices de rodillos para dar forma a la chapa
- Cizalla volante/cizalla giratoria para cortar paneles a medida
- Apilador para recoger los paneles cortados
Otros accesorios opcionales son la unidad de gofrado, la unidad de entallado y la unidad de perforación, según las necesidades de la aplicación.
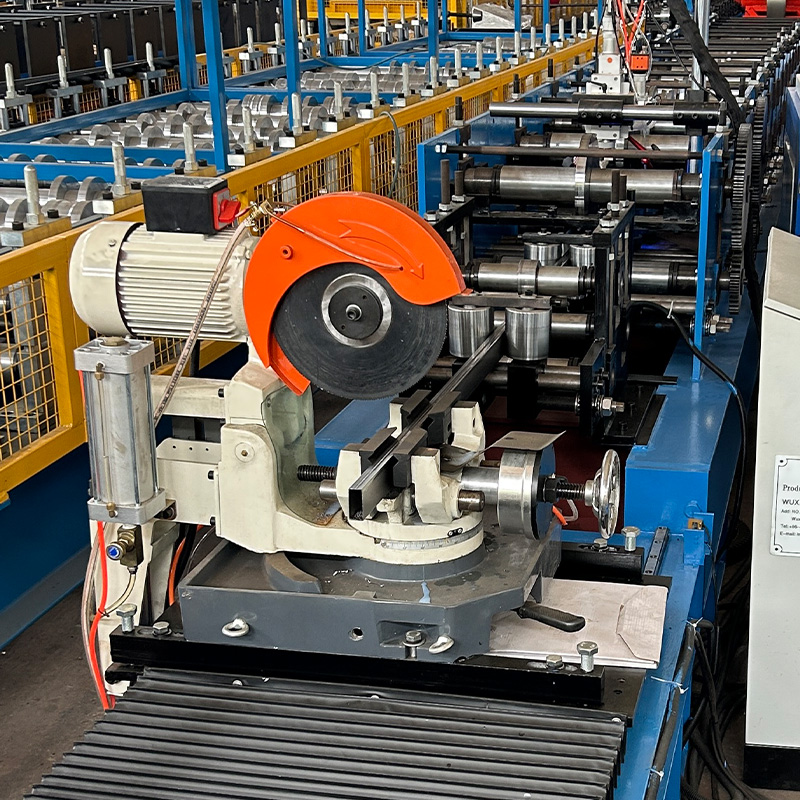
Tipos de Perfiladoras de tejados metálicos
Tipo | Descripción |
---|---|
Por Capacidad | Carga ligera, media y pesada en función del grosor de la chapa manipulada |
Por operación | Manual, semiautomática, totalmente automática con servomotores y control por PLC |
Por tipo de conformado | Perfilado en frío a temperatura ambiente |
Por estructura | Unidades combinadas todo en uno, Máquinas modulares de componentes separados |
Por uso final | Tejados, Paneles murales, Persianas enrollables, Barreras viales, Perfiles de drenaje |
Proceso de Trabajo de una Máquina Perfiladora de Láminas para Techo
El proceso de trabajo consiste en desenrollar una chapa fina y hacerla pasar por una serie de soportes que contienen matrices de rodillos. A medida que la chapa pasa por cada soporte, adopta la forma definida por el perfil de los rodillos. Por último, la larga chapa perfilada se corta en longitudes mediante la cizalla y se recoge en el apilador de salida.
En el caso de perfiles complejos, se utilizan más soportes de conformado para conseguir gradualmente la forma deseada. También pueden incorporarse operaciones en línea como perforación de agujeros, entallado o estampado.
Alimentación de material, formación, diseño en la formación de rollos de paneles de techo
Selección de materiales de chapa metálica
Las chapas más comunes son las de acero galvanizado, acero galvalume, acero prepintado, chapas de aluminio y chapas de acero inoxidable, en función de la resistencia a la corrosión, la solidez y el coste de la aplicación.
Gama de espesores: De 0,15 mm a 1,2 mm Anchura: 600mm a 1250mm
El revestimiento de la superficie del material, la anchura, el grosor y las propiedades mecánicas deben especificarse al realizar el pedido del equipo de perfilado de láminas de tejado.
Opciones de forma del perfil
Es posible fabricar más de 100 perfiles estándar y personalizados para tapajuntas de tejados y paredes. Algunos de los más comunes que se fabrican son:
- Costilla trapezoidal / Chapas onduladas
- Chapas nervadas en caja
- Chapas de costura
- Hojas de sartén anchas
- Fichas Deeplink
- Láminas fijas ocultas
- Paneles compuestos
- Paneles clip-lock
Se pueden desarrollar perfiles personalizados a partir de planos arquitectónicos.
Diseño y plegado de utillaje para rodillos
El perfil se diseña y las pasadas de plegado se calculan con programas como MetalForm y SigmaNest. El patrón de flor delinea los pasos progresivos de plegado.
Los rodillos están mecanizados mediante CNC a partir de acero D2 y tratados térmicamente a 45-50 HRC para la dureza de conformado de chapa.
-
Máquina formadora de rollos de listones de persianas enrollables
-
Máquina perfiladora de postes de viñedos
-
Máquina formadora de rollos Sigma Purlin de tamaño automático cambiable
-
Máquina formadora de rollos de marco de gabinete eléctrico
-
Máquina formadora de rollos de riel DIN
-
Máquina formadora de rollos de escalera de cable
-
Máquina formadora de rollos de perfil en forma de C con soporte de montaje fotovoltaico
-
Máquina perfiladora de bandeja portacables
-
Laminación en frío del canal de la correa de la CZ que forma el perfil de acero galvanizado auto completo de la máquina
Rebanado y personalización en chapas perfiladas
- Cizalla para moscas - La cizalla tipo guilotina con cuchillas superior e inferior se utiliza para el escuadrado instantáneo de los paneles. No raya ni deforma los paneles.
- Cizalla giratoria / Cizalla circular - Se utiliza cuando se requieren bordes curvos o cortes de muesca en los paneles.
- Unidades de perforación - Para hacer agujeros para pernos en la chapa para su fijación.
- Rodillos de gofrado - Para protuberancias/geometría decorativa.
- Unidad de entalladura - Para conectar tapajuntas entre paneles.
- Control de corte longitudinal: corte longitudinal según los requisitos del pedido, desde 0,5 m hasta 12 m.
- Apilador - Recoge secuencialmente los paneles cortados.
Principales fabricantes de perfiladoras y gama de costes
Marca | Ubicación | Precios |
---|---|---|
Zhongli Máquina Perfiladora | China | $5000-$15000 |
Máquina Perfiladora BOTOU Xianfa | China | $6000-$18000 |
Jouanel Industrie | Francia | $8000-$25000 |
Maquinaria Rollwell de Shanghai | China | $4000-$28000 |
Grupo Bradbury | REINO UNIDO | $12000-$50000 |
Formtek | EE.UU. | $15000-$78000 |
Techadoras Dynamik | Sudáfrica | $5000-$21000 |
Wolffkran | India | $4000-$15000 |
Howick Ltd. | Nueva Zelanda | $13000-$71000 |
Tecnologías Framecad | Nueva Zelanda | $14800-$128000 |
Maquinaria de perfilado CO-Z | Taiwán | $8800-$38000 |
Máquinas herramienta SIPPI | India | $3500-$12000 |
Las máquinas básicas ligeras para chapas finas cuestan entre $4000 y $15.000. Las máquinas rápidas totalmente automáticas para trabajos pesados con una producción superior a 100 metros/minuto cuestan más de $40.000.
Los fabricantes europeos y estadounidenses suelen tener precios más altos, pero mejor calidad y durabilidad de hasta 20 años.
Instalación y puesta en marcha
- La perfiladora requiere una sombra cubierta y una plataforma plana para su colocación. Necesita conexión eléctrica trifásica.
- Una vez atornillada y rejuntada en el suelo, la bobina de chapa del desenrollador se carga y se enhebra a través de las guías de entrada.
- La máquina se pone en marcha a velocidad lenta, los preajustes se ajustan para centrar la alineación de la hoja. La velocidad se aumenta gradualmente hasta alcanzar la velocidad de producción mientras se comprueban los problemas de vibración y ruido.
- La unión múltiple de bobinas está configurada para el empalme automático cuando terminan las bobinas. Pase algunos paneles de prueba por todo el proceso, desde la alimentación hasta el apilado. Compruebe si hay arañazos o deformaciones en los paneles.
- Ajuste con precisión todos los preajustes relacionados con el ángulo de avance, la profundidad de corte y las variaciones de la longitud de corte.
- La máquina ya está lista para iniciar la producción tras una puesta en marcha satisfactoria.
Funcionamiento
- El operario de la máquina alimenta la bobina de chapa en el desenrollador y enhebra la chapa a través de las guías de entrada ajustando el ángulo de alimentación.
- El perfil de longitud y forma se selecciona en la pantalla PLCD eligiendo las recetas guardadas.
- Los botones Jog permiten el movimiento en pulgadas para los ajustes. El modo automático inicia la producción según los parámetros de velocidad y longitud establecidos.
- Los paneles cortados caen sobre el transportador de salida y el apilador, y pueden recogerse en un carro. Los contadores controlan la producción.
- Es necesario engrasar periódicamente los ejes móviles. Las guías de los rodillos y las cuchillas de la cizalla deben inspeccionarse y sustituirse cuando estén desgastadas. El cuadro eléctrico, los motores y los cables deben comprobarse para ver si se calientan o si hay contactos sueltos.
Consejos de mantenimiento
- Limpie con frecuencia del suelo las astillas de chapa y los trozos de chatarra
- Asegúrese de que la máquina está correctamente conectada a tierra y señalizada.
- Compruebe periódicamente el apriete de los tornillos de los soportes
- Inspeccionar los rodamientos y los niveles de aceite de la caja de cambios
- Controlar la carga eléctrica durante el funcionamiento
- Aplicar revestimiento antioxidante en piezas de máquinas sin pintar
- Comprobar fugas de aceite del sistema hidráulico, obstrucción del filtro, funcionamiento de la bomba
Un mantenimiento adecuado mejora la vida útil, el rendimiento y la seguridad.
Criterios de selección al comprar equipos de perfilado
Parámetros a comparar:
- Capacidad de manipulación de espesores de chapa
- Gamas de conformado de perfiles: altura, anchura
- Velocidad de producción - metros/minuto
- Capacidad de corte en longitud - mínima y máxima
- Tipo de accesorios de punzonado y entallado
- Material de construcción de los rodillos y de la máquina en general
- Dimensiones de la línea general
- Precio, condiciones de pago, periodo de garantía
- Respuesta del servicio posventa
Obtenga información de varios proveedores antes de decidirse. Compruebe los vídeos de demostración y los testimonios de los clientes. Decide en función de la reputación y la relación entre prestaciones y presupuesto.
Ventajas e inconvenientes del proceso de perfilado de chapa metálica
Ventajas y beneficios
- Altas velocidades de producción de hasta 120 metros/minuto para proyectos más rápidos
- La calidad constante de los paneles producidos reduce las mermas en la obra
- Los perfiles personalizados según el diseño elegido aportan flexibilidad arquitectónica
- Los paneles ligeros de gran luz reducen la carga muerta del edificio
- Menor mantenimiento que los métodos tradicionales de revestimiento de tejados y paredes
- Un mejor drenaje del agua y paneles estancos mejoran la vida útil de la estructura
- Garantía líder del sector de 20 años para el recubrimiento de chapa de los proveedores
- Los paneles ignífugos como las chapas metálicas son incombustibles y no necesitan ningún tratamiento adicional
- El revestimiento al final de la vida útil restaura las chapas y evita los costes de demolición y reconstrucción.
- Las chapas metálicas reciclables 100% ayudan a conseguir la certificación de edificio ecológico
Limitaciones y desventajas
- Elevada inversión de capital inicial que requiere una evaluación del impacto a escala empresarial
- Superficie de la chapa propensa a la oxidación que requiere retoques regulares de pintura tras la instalación
- La dilatación/contracción de chapas largas debido a la temperatura requiere la instalación de juntas de dilatación.
- Los instaladores noveles deben recibir formación para evitar uniones incorrectas o fugas en las paredes.
- Las zonas remotas carecen de acceso de servicio para mantener o reparar las líneas de encofrado en rollo
- Las plataformas existentes pueden requerir evaluación y reelaboración para soportar cargas de equipos pesados.
- El diseño de perfiles a medida y el utillaje para rodillos tienen plazos de entrega largos, de 6 a 8 semanas.
Si se planifican adecuadamente las limitaciones mencionadas, se pueden obtener resultados operativos fiables de estas versátiles máquinas de perfilado.
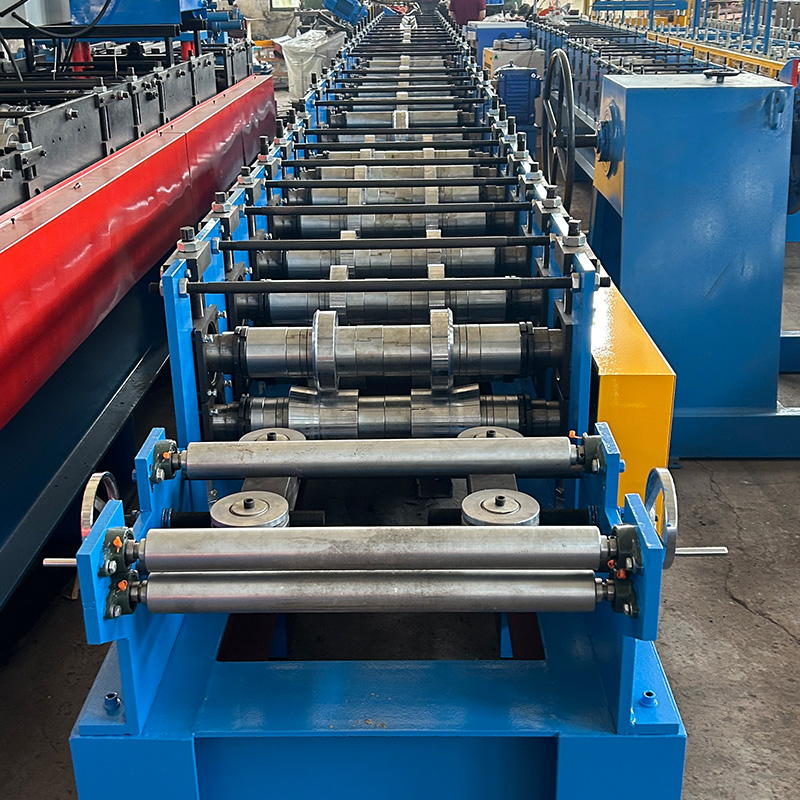
Preguntas frecuentes
P: ¿Qué grosor de chapas se puede formar?
R: La gama de espesores es de 0,15 mm a 1,2 mm para acero/aluminio. Posibilidad de hasta 2 mm de acero inoxidable/titanio.
P: ¿Qué sistema de transmisión se utiliza en estas máquinas?
R: Los modelos básicos utilizan manivelas manuales. Los modelos industriales avanzados utilizan servomotores y accionamientos con control PLC para la velocidad, el posicionamiento y la automatización.
P: ¿Necesita algún tipo de cimentación o base?
R: Se necesita una superficie plana y dura, como una losa de hormigón armado. Los pernos inyectados la fijan firmemente para evitar vibraciones a altas velocidades.
P: ¿Cómo se calcula la potencia necesaria?
R: Depende del grosor de la chapa, del número de rodillos y de los accesorios añadidos, como punzones o muescas. Normalmente, de 11 kW a 30 kW para máquinas de capacidad variable.
P: ¿Se pueden utilizar bobinas de distintos anchos?
R: Sí. Pero habría que cambiar todos los rodillos formadores y el desenrollador para adaptarlos a la anchura de la bobina. Es un trabajo laborioso que requiere experiencia.
P: ¿Qué precisión y acabado superficial se consigue?
R: Los rodillos mecanizados CNC de alta gama proporcionan una precisión de panel de hasta +/- 1,0 mm y un acabado superficial brillante.
P: ¿Qué normas deben cumplir estas máquinas?
R: La certificación de calidad ISO 9001 y el cumplimiento de la marca CE demuestran el rigor en el diseño, el proceso de fabricación y las pruebas de validación.