Standing seam roll forming machines are specialized lines designed to continuously form interlocking standing seam metal roof panels from coils of sheet metal.
Key features of standing seam roll formers:
- Produce popular architectural metal roofing
- Gradually cold-form panels through progressive dies
- Form seams allowing expansion/contraction
- Avoid roof penetrations with concealed clips
- Ideal for prefinished metal roofing coils
- Faster production versus portable roll formers
- Used for commercial, industrial, residential roofs
Standing seam roll forming delivers efficient in-line forming for seamless, watertight metal roofing.
Types of standing seam roll forming machine
Machine Type | Description |
---|---|
Horizontal | Strip feeds horizontally through forming heads |
Vertical | Strip feeds vertically for compact layout |
Single Wall | Forms simple single wall panels |
Double Wall | Adds inner wall reinforcement |
Mechanical | Cam-operated seam forming |
হাইড্রোলিক | Hydraulic cylinders for seaming |
Horizontal machines provide straight-through forming for long panels. Vertical machines save floorspace. Single or double wall configurations are possible. Mechanical or hydraulic seaming available.
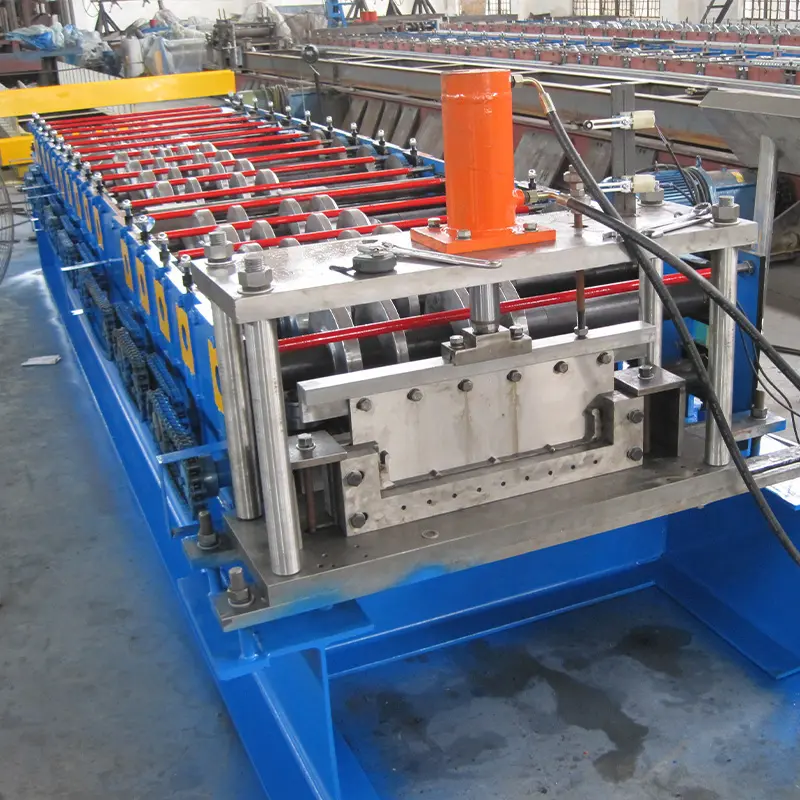
Key Components of Standing Seam Roll Lines
Component | Function |
---|---|
ডিকয়লার | Feeds metal coil into the line |
Leveler | Flattens strip for consistent forming |
Tooling Stations | Gradually form panel profiles |
Seaming | Final stage folds and crimps seams |
Shear/Punch | Cut to length; punch clip holes |
Stacker | Stacks finished panels for easy unloading |
Robust decoiler, precision leveling, engineered tooling, specialized seaming, and stacker optimize standing seam panel production.
Typical Applications of standing seam roll forming machine
Sector | Common Uses |
---|---|
Commercial | Distribution centers, offices, retail buildings |
Institutional | Schools, hospitals, churches, government |
Industrial | Warehouses, manufacturing plants |
Agricultural | Barns, equipment sheds, storage buildings |
Residential | Custom homes, apartments |
Any metal roofing application where an attractive, watertight standing seam roof is desired. Popular in many sectors.
Design Standards for Standing Seam Roll Lines
Component | Standards |
---|---|
ফ্রেম | Heavy welded steel with stress relief |
Tooling | Hardened rolls precision-ground to profile |
Seaming | Hardened crimping dies and guides |
Drives | Helical gearboxes or servo motors |
Controls | PLC control with touchscreen HMI |
Safety | Full guarding, e-stops, access interlocks |
Codes | AISI, ASTM, ASME, IBC, OSHA standards |
Rigorous design criteria ensure consistent forming quality, production uptime, safe operation, and finished roof performance over decades.
Specifications of Standing Seam Roll Formers
Parameter | Typical Values |
---|---|
Line Speed | 10 – 40 feet/min |
Sheet Width | 24 – 48 inches |
Material Gauge | 24 – 22 gauge |
Seam Height | 1 – 3 inches |
Length Tolerance | ± 1/8 inch |
Length Capability | 8 – 40+ feet |
Machine Weight | 6,000 – 12,000 lbs |
Speeds, widths, and lengths vary by machine size and model. Heavier gauges are possible with special tooling.
Pricing for Standing Seam Roof Panel Roll Lines
Manufacturer | Price Range |
---|---|
Metform | $120,000 – $250,000 |
Samco | $140,000 – $280,000 |
Mesco | $100,000 – $220,000 |
China suppliers | $80,000 – $180,000 |
Costs range from $80,000 to $280,000 depending on features. Installation and shipping add 10-20%.
Installation and Setup of Standing Seam Machines
Task | Description |
---|---|
Offloading | Use proper lifting methods and gear |
Positioning | Layout per floor plan drawings |
Anchoring | Bolt machine to foundation at all points |
Leveling | Adjust machine for precise level |
Assembly | Install decoiler, leveler, stacker, conveyors |
Connection | Wire main power and control cables |
Initialization | Power up; test and adjust components |
Trial Run | Run slowly checking all functions |
Proper installation, alignment, and testing prevents issues and ensures high production quality.
Operation and Maintenance of Standing Seam Lines
Activity | Frequency |
---|---|
Safety Checks | Per shift |
Parameter Adjustment | As needed |
Tool Lubrication | Daily |
Hydraulic Service | Quarterly |
Roll Changing | As needed |
Bearing Lubrication | Monthly |
Gearbox Oil | Per manual |
Machine Calibration | Annual |
Daily safety procedures must be followed. Careful operation optimized with regular maintenance sustains performance.
Selecting a Standing Seam Roll Former Manufacturer
Considerations | Guidance |
---|---|
Expertise | Significant experience with standing seam lines |
কাস্টমাইজেশন | Ability to customize machine for needs |
সমর্থন | Installation help, training, service availability |
Reliability | Proven longevity and minimal downtime |
Reputation | Trusted brand known for quality equipment |
Value | Reasonable price for the capabilities provided |
Seeking manufacturers with specialized expertise in standing seam roll forming technology is advised.
Benefits of Standing Seam Roll Forming
- High quality, uniform standing seam panels
- Faster production versus portable roll formers
- Formed on-site from metal coil
- Concealed fasteners avoid roof penetrations
- Allows expansion/contraction of long panels
- Architectural, upscale metal roofing appearance
- Durable and completely watertight
- Resists corrosion, rust, elements
- Recyclable and environmentally friendly
- Lower installation labor versus shingles
Standing seam roll forming offers huge benefits for metal roofing quality, speed, performance and aesthetics.
Limitations of Standing Seam Roll Technology
- Higher cost than typical portable roll former
- Large equipment requiring indoor space
- Qualified operators needed to run
- Significant power requirements
- Rolls and tooling specific to each roof profile
- Specialized troubleshooting and maintenance
- Not as portable as mobile roll formers
- Initial learning curve for operation
- Scrap generation during set up
- Lift required for coil loading
Limitations primarily relate to higher capital cost and specialized operation and maintenance.
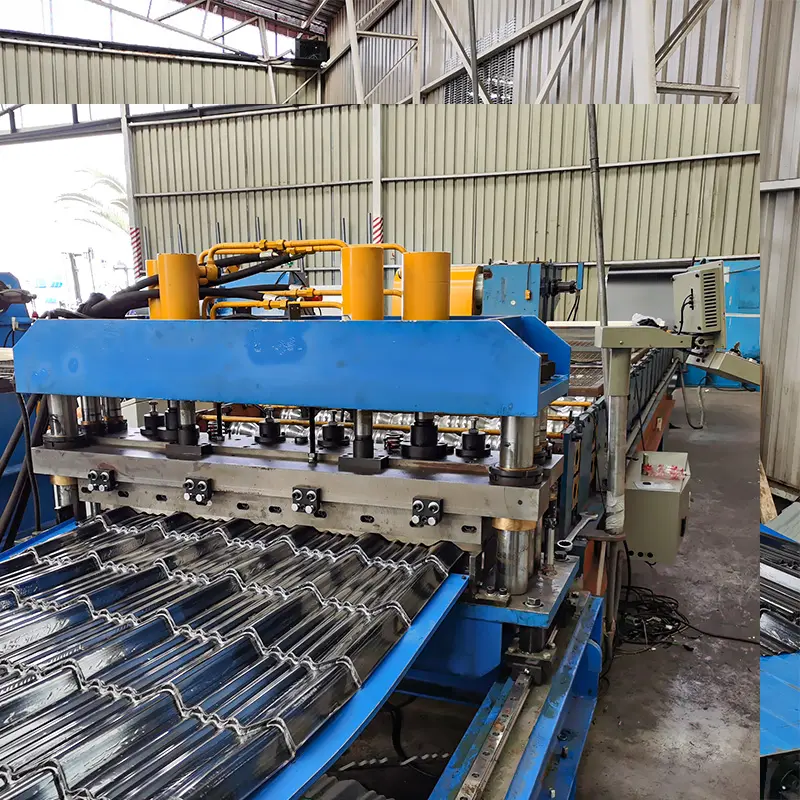
Cost Comparison: Roll Formed vs Portable Standing Seam
Method | Cost | Benefits | Drawbacks |
---|---|---|---|
Roll Formed | $100k – $300k | High volume, speed, consistency | High initial cost, maintenance |
Portable | $25k – $60k | Low cost, transportable | Slower production, variability |
Roll forming offers superior productivity and quality but requires higher upfront investment. Portable machines are slower yet more affordable and movable.
Troubleshooting Common Standing Seam Roll Former Issues
Issue | Solution |
---|---|
Inconsistent seams | Adjust/replace worn crimping dies |
Strip marking | Increase roll hardness; adjust guides |
Sheet jamming | Check leveler gap; smooth tooling profiles |
Hydraulic leaks | Replace seals, hoses, cylinders |
Excess vibration | Inspect/tighten mountings; check alignment |
Electrical faults | Check/replace wires, drives, connections |
Keeping crimping dies in top shape along with prompt repairs prevents unplanned downtime. Proper feed and tooling maintenance also critical.
FAQ
Q: What sheet metal gauge capacities are typical?
A: Most machines accommodate 24 to 22 gauge material. Heavier gauges possible with special tooling.
Q: What seam heights can be formed?
A: Common heights range from 1 to 3 inches. Custom profiles are possible.
Q: How long does it take to changeover to a new roof profile?
A: With quick change dies and tooling, changeover takes 1-2 hours.
Q: What factors affect cycle time and production rate?
A: Sheet gauge, machine power, part complexity, and length all impact production speed.
Q: What are the power requirements for standing seam lines?
A: Power ranges from 30 kW on smaller units to over 100 kW on high capacity lines.
Q: What thickness roof panels can standing seam machines produce?
A: 24, 22, and some 20 gauge steel coils can be formed up to 48 inches wide.
Q: What safety features are incorporated?
A: Full guarding, e-stops, interlocks, and control reliability per prevailing standards.
Q: What is the expected lifetime of a standing seam roll former?
A: Approximately 15-20 years of productive life is typical with proper maintenance.