As global rail networks expand and modernize, the demand for efficient, durable, and lightweight train carriage frames has skyrocketed. At the heart of this transformation is the Train Carriage Frame Roll Forming Machine, an advanced industrial tool designed to produce high-precision profiles and components that form the backbone of train carriages.
In this comprehensive guide, we’ll explore the Train Carriage Frame Roll Forming Machine, its applications in the rail industry, the latest technological advancements, pricing insights, and why Wuxi Sunway Machinery is the leading manufacturer of these machines. Whether you’re a rail manufacturer, an infrastructure planner, or an industry enthusiast, this article offers an in-depth look into how roll-forming machines are revolutionizing train production.
What is a Train Carriage Frame Roll Forming Machine?
ক Train Carriage Frame Roll Forming Machine is a specialized piece of equipment used to manufacture structural components and profiles for train carriages. These components, which include sidewalls, floor panels, roof supports, and reinforcing beams, must meet stringent safety, durability, and weight requirements to ensure the safety and efficiency of modern rail systems.
The roll-forming process involves passing metal sheets or coils through a series of rollers that gradually shape the material into the desired profile. This method ensures high precision and consistency, making it ideal for producing the complex and lightweight components required for train carriages.
Whether for high-speed rail, metro systems, or freight trains, Train Carriage Frame Roll Forming Machines are indispensable tools for producing frames that can withstand the stresses of rail transport while maximizing passenger comfort and operational efficiency.
Applications of Train Carriage Frame Roll Forming Machines
Train carriage frames are critical to the structural integrity and performance of rail vehicles. Let’s explore the key applications of roll-formed components in train manufacturing:
1. Sidewall Frames
- Use Case: Roll-formed profiles are used to create the structural framework for train carriage sidewalls.
- Why It Matters: High-precision frames ensure consistent dimensions, reducing assembly time and improving aerodynamics.
2. Roof Supports
- Use Case: Roof supports provide structural integrity to the carriage’s ceiling and protect against external forces.
- Why It Matters: Lightweight yet durable supports enhance passenger safety and optimize fuel efficiency.
3. Floor Panels
- Use Case: Roll-formed panels form the foundation of train carriage floors, supporting passenger and cargo loads.
- Why It Matters: High-strength floor panels ensure stability and durability under heavy loads.
4. Door Frames
- Use Case: Door frames made from roll-formed profiles provide a precise fit and seamless integration with modern train designs.
- Why It Matters: Ensures smooth operation of automated doors, enhancing passenger convenience.
5. Window Frames
- Use Case: Precision-engineered roll-formed profiles are used to create the frames for train windows.
- Why It Matters: Guarantees a perfect seal, reducing air leakage and improving energy efficiency.
6. Reinforcement Beams
- Use Case: Beams provide additional strength to the carriage structure, especially for high-speed and heavy-duty trains.
- Why It Matters: Ensures the frame can withstand dynamic loads and vibrations during operation.
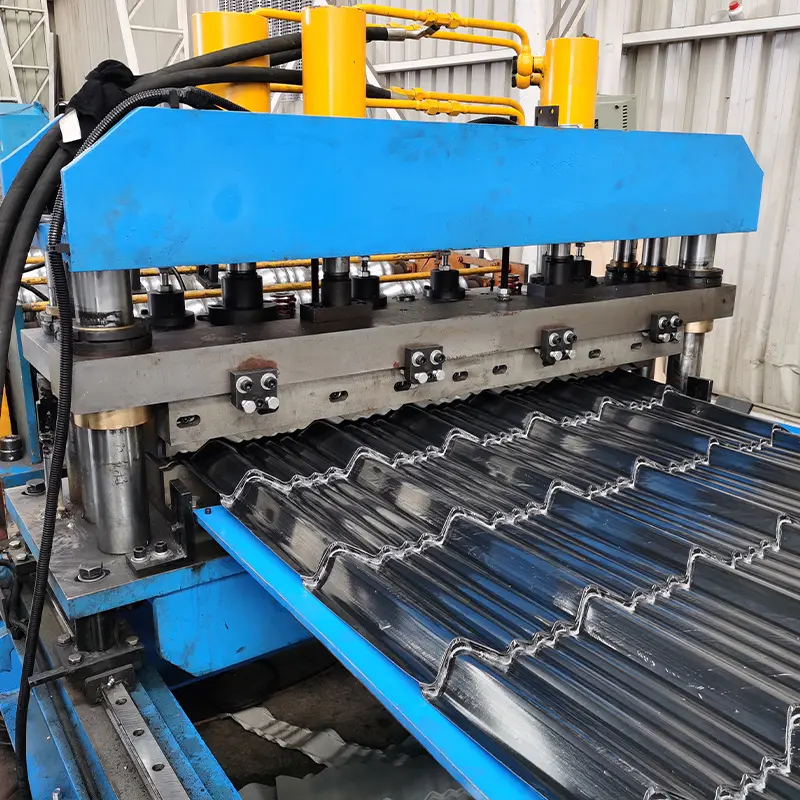
Key Features of Wuxi Sunway Train Carriage Frame Roll Forming Machines
When it comes to producing high-quality train carriage frames, Wuxi Sunway Machinery provides state-of-the-art roll-forming machines designed to meet the unique requirements of the rail industry. Here’s what sets their machines apart:
1. High-Precision Forming
- What It Does: Produces profiles with tight tolerances and smooth finishes.
- Why It’s Important: Ensures components fit perfectly, reducing assembly time and improving overall structural integrity.
2. Material Versatility
- Supported Materials:
- Aluminum alloys
- Stainless steel
- High-strength steel
- Galvanized steel
- Why It’s Crucial: Allows manufacturers to produce lightweight yet durable components, optimizing the performance of modern trains.
3. Multi-Profile Capabilities
- What It Offers: Capable of producing a variety of profiles, including U-channels, Z-sections, and custom designs.
- Why It’s Revolutionary: Supports diverse applications, from passenger cars to freight wagons.
4. Advanced Cutting and Punching Systems
- Features: Servo-driven cutting and punching systems ensure precision in creating holes, slots, and edges.
- Why It Matters: Reduces the need for secondary operations, saving time and resources.
5. High-Speed Production
- Performance: Capable of producing up to 20 meters of profiles per minute, depending on the design complexity.
- Why It Matters: Meets the high-volume demands of rail manufacturers.
6. Modular and Compact Design
- What It Does: Offers a space-saving design that integrates seamlessly into existing production lines.
- Why It Matters: Optimizes factory floor space and allows for easy upgrades.
7. PLC-Controlled Automation
- Features:
- Fully programmable logic controllers (PLC) with an intuitive touchscreen interface.
- Stores multiple design parameters for quick setup.
- Real-time monitoring and error detection.
- Why It’s Revolutionary: Simplifies operation and ensures consistent quality across production runs.
8. Eco-Friendly Design
- What It Offers: Energy-efficient motors and waste-reducing technologies.
- Why It Matters: Supports sustainable manufacturing practices.
Production Workflow of a Train Carriage Frame Roll Forming Machine
The production process for train carriage frames is streamlined for efficiency and precision. Below is an overview of the workflow:
1. Decoiling
- Metal coils are loaded onto the decoiler, which feeds the material into the machine.
2. Leveling
- A leveling system ensures the material is flat and free from warping before entering the roll-forming section.
3. Roll Forming
- The material passes through a series of rollers that gradually shape it into the desired profile.
4. Punching and Cutting
- Integrated punching units create precise holes and slots, while cutting systems trim the profiles to the specified lengths.
5. Surface Treatment
- Some machines include options for surface treatments like anodizing or anti-corrosion coatings.
6. Stacking
- Finished components are automatically stacked for easy packaging and transportation.
Pricing of Train Carriage Frame Roll Forming Machines
The cost of a Train Carriage Frame Roll Forming Machine depends on its features, production capacity, and customization level. Below is a general pricing guide for 2025:
Machine Type | Capabilities | Price Range (USD) |
---|---|---|
Standard Machines | Basic train frame production | $180,000–$250,000 |
High-Precision Machines | Advanced tolerances and surface finishes | $250,000–$400,000 |
Fully Customizable Machines | Multi-profile and material capability | $400,000–$600,000 |
For tailored pricing and financing options, contact Wuxi Sunway Machinery.
Advantages of Using Train Carriage Frame Roll Forming Machines
Investing in a Train Carriage Frame Roll Forming Machine offers numerous benefits for rail manufacturers:
1. Enhanced Efficiency
- High-speed production reduces lead times and increases output.
2. Precision and Consistency
- Ensures uniform quality across all components, minimizing assembly issues.
3. Material Compatibility
- Supports a wide range of high-strength and lightweight materials.
4. Cost Savings
- Reduces material waste and labor costs, improving overall profitability.
5. Scalability
- High production capacity allows manufacturers to meet growing demands for rail infrastructure projects.
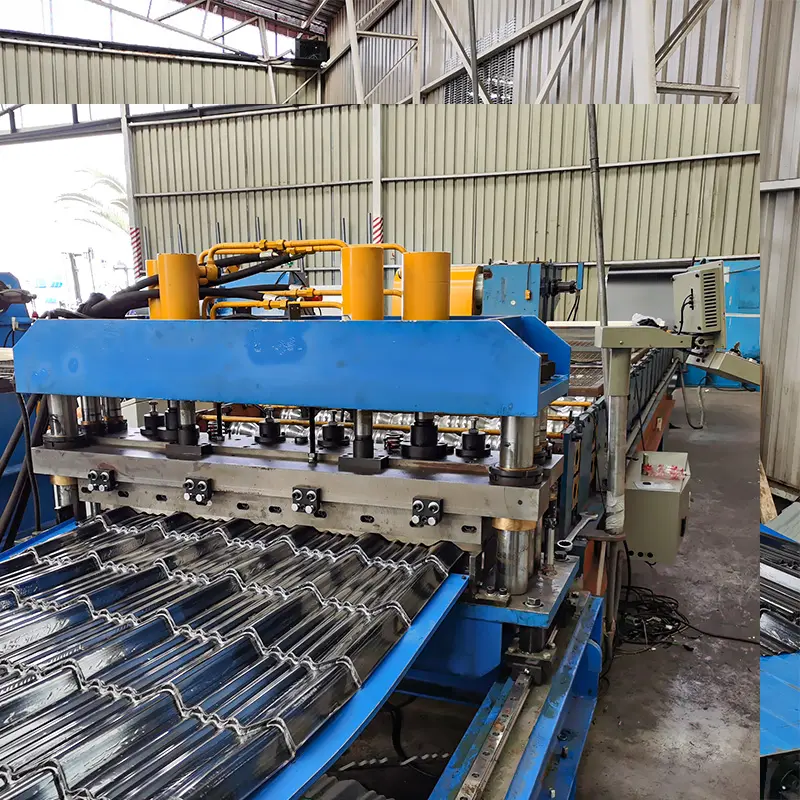
FAQs About Train Carriage Frame Roll Forming Machines
Question | Answer |
---|---|
What is the production speed? | Machines can produce up to 20 meters of profiles per minute, depending on the design. |
Can the machine handle aluminum profiles? | Yes, it is specifically designed for lightweight materials like aluminum. |
What is the maximum material thickness? | The machine can process materials up to 4.0mm thick, depending on the profile design. |
Does Sunway provide installation support? | Absolutely! Sunway offers on-site installation and commissioning services. |
What is the machine’s lifespan? | With proper maintenance, the machine can last 10–15 years or more. |
Is operator training included? | Yes, comprehensive training is provided with every machine purchase. |
Global Trends Driving the Adoption of Train Carriage Frame Roll Forming Machines
The rail industry is undergoing a seismic shift, fueled by the need for sustainable transportation, rapid urbanization, and technological innovation. These trends are driving the demand for Train Carriage Frame Roll Forming Machines in 2025:
1. Expansion of High-Speed Rail Networks
- The Numbers: Global investments in high-speed rail are projected to surpass $300 billion by 2030, with new projects in Asia, Europe, and North America.
- Impact on Manufacturing: High-speed trains require lightweight, aerodynamic, and structurally sound carriage frames.
- Why It Matters: Roll-forming machines enable manufacturers to produce precise, consistent, and high-strength profiles that meet these requirements.
2. Shift Toward Lightweight Materials
- The Context: Lightweight materials like aluminum and high-strength steel are becoming standard in rail manufacturing to improve energy efficiency and reduce carbon emissions.
- Impact on Roll Forming: Machines capable of handling these materials are essential for producing components that optimize train performance.
- Why It’s Exciting: Reduced weight translates to better fuel efficiency, faster speeds, and lower operational costs.
3. Urbanization and Metro System Expansion
- The Trend: The global metro systems market is growing as cities invest in public transportation to reduce traffic congestion and pollution.
- Impact on Component Production: Metro carriages require precise, durable, and modular frames to accommodate high passenger volumes.
- Why It Matters: Roll-forming technology ensures the production of scalable and high-quality components for metro systems.
4. Sustainability Goals and Green Rail Projects
- What’s Happening: Rail manufacturers are adopting eco-friendly production methods and materials to align with global sustainability goals.
- Impact on Roll Forming Machines: Machines with energy-efficient motors, optimized material usage, and recyclable outputs are becoming industry standards.
- Why It’s Important: Green manufacturing practices aren’t optional—they’re a competitive advantage in today’s environmentally-conscious market.
5. Demand for Customization
- The Push: Customers increasingly demand customized train designs to meet specific operational and aesthetic requirements.
- Impact on Roll Forming: Machines must offer multi-profile capabilities and quick changeovers to accommodate custom designs.
- Why It’s Exciting: Customization allows manufacturers to cater to niche markets without sacrificing efficiency.
Technological Advancements in Train Carriage Frame Roll Forming Machines
The evolution of Train Carriage Frame Roll Forming Machines is driven by technological innovations that enhance productivity, precision, and sustainability. Let’s explore the cutting-edge advancements shaping their future:
1. Digital Twin and Simulation Technology
- What It Does: A digital twin creates a virtual replica of the machine, allowing manufacturers to simulate production processes and test new designs.
- Benefits:
- Speeds up prototyping by eliminating trial-and-error processes.
- Identifies potential bottlenecks before production begins.
- Reduces time-to-market for new train models.
2. IoT-Enabled Smart Machines
- How It Works: IoT (Internet of Things) sensors collect real-time data on machine performance, material usage, and output quality.
- Advantages:
- Enables remote monitoring and diagnostics.
- Provides actionable insights to optimize production.
- Reduces downtime through predictive maintenance.
3. Servo-Driven Precision
- The Technology: High-speed servo motors control the roll-forming process with exceptional accuracy.
- Why It’s Important:
- Ensures consistent dimensions and smooth edges.
- Reduces material waste, improving cost efficiency.
- Enhances the structural quality of train carriage frames.
4. Multi-Material Processing
- What It Offers: Machines can seamlessly switch between different materials, such as aluminum, stainless steel, and composites, without compromising precision.
- Why It’s Revolutionary: Expands the range of products manufacturers can offer, making these machines versatile for various train types.
5. AI-Driven Quality Control
- What It Does: Artificial intelligence monitors the production process, identifying defects in real-time and ensuring consistent quality.
- Benefits:
- Reduces waste by catching errors early.
- Ensures that every component meets stringent rail industry standards.
- Improves overall production efficiency.
6. High-Speed Production with Modular Design
- Performance: Modern machines can achieve production speeds of up to 20 meters per minute, with modular designs allowing for future upgrades.
- Why It Matters: Meets the high-volume demands of rail manufacturers while providing scalability.
Environmental Benefits of Train Carriage Frame Roll Forming Machines
Sustainability is no longer a buzzword—it’s a necessity. Here’s how Train Carriage Frame Roll Forming Machines contribute to greener rail manufacturing:
1. Reduced Material Waste
- How It Works: The roll-forming process optimizes material usage, minimizing scrap and waste.
- Impact: Lowers production costs while conserving precious resources.
2. Energy Efficiency
- The Innovation: Machines are equipped with energy-efficient motors and systems that consume less electricity.
- Why It Matters: Supports manufacturers in reducing their carbon footprint and aligning with global sustainability goals.
3. Recyclable Components
- The Advantage: Profiles made from aluminum and steel are fully recyclable, contributing to a circular economy.
- Why It’s Important: Encourages sustainable practices across the rail industry.
4. Localized Production
- What It Does: Enables manufacturers to produce components locally, reducing the environmental impact of transportation.
- Outcome: Supports regional economies while enhancing sustainability.
Comparison: Train Carriage Frame Roll Forming Machines vs. Traditional Methods
Let’s compare Train Carriage Frame Roll Forming Machines with traditional manufacturing methods like manual welding or stamping:
Feature | রোল ফর্মিং মেশিন | Traditional Methods |
---|---|---|
Precision | High; ensures consistent dimensions | Moderate; prone to human error |
Production Speed | High; up to 20 meters per minute | Slow; labor-intensive processes |
Automation | Fully automated with IoT and AI integration | Mostly manual or semi-automated |
Material Waste | Minimal; optimized processes reduce scrap | Higher; less efficient material usage |
কাস্টমাইজেশন | Easily customizable for various profiles | Limited flexibility; requires separate tooling |
Cost Efficiency | Higher initial cost, lower operational costs | Lower initial cost, higher long-term costs |
Scalability | Ideal for mass production | Limited scalability for high-volume demand |
Additional FAQs About Train Carriage Frame Roll Forming Machines
Question | Answer |
---|---|
What is the maximum material thickness? | The machine can process materials up to 4.5mm thick, depending on the design. |
Can the machine handle composite materials? | Yes, modern machines can process advanced composites alongside metals. |
What is the typical lead time for delivery? | Delivery takes 3–6 months, depending on customization requirements. |
Does Sunway provide operator training? | Yes, comprehensive training is included with every machine purchase. |
Is remote monitoring available? | Absolutely, IoT-enabled machines allow for remote diagnostics and performance tracking. |
What industries benefit from this machine? | Besides rail, industries like aerospace, automotive, and construction can also utilize these machines. |
Why Choose Wuxi Sunway Machinery for Train Carriage Frame Roll Forming Machines?
Here’s why Wuxi Sunway Machinery is the trusted partner for rail manufacturers worldwide:
- Proven Expertise: Decades of experience in designing and delivering innovative roll-forming solutions.
- Global Reach: Trusted by rail manufacturers across Asia, Europe, the Americas, and beyond.
- Customization Excellence: Machines tailored to meet specific rail production needs and design standards.
- Sustainability Commitment: Eco-friendly designs that minimize waste and reduce energy consumption.
- Innovation Leadership: Cutting-edge features like AI-driven quality control, IoT integration, and servo-driven systems.
- Comprehensive Support: From installation to troubleshooting, Sunway ensures smooth operations and customer satisfaction.
Conclusion: Redefining Rail Manufacturing with Roll Forming Technology
দ্য Train Carriage Frame Roll Forming Machine is a cornerstone of modern rail manufacturing, enabling the production of lightweight, durable, and high-quality components that meet the demands of today’s rail systems. Whether for high-speed rail, metro systems, or freight trains, these machines deliver the precision, speed, and reliability required to excel in a competitive industry.
Ready to transform your production line? Contact Wuxi Sunway Machinery today to explore their advanced roll-forming solutions. Together, let’s shape the future of rail transportation—one frame at a time!