Rolling shutters utilize curved slat profiles that interlock to provide security and privacy. Roll forming is an ideal process to manufacture custom shutter slats from coiled steel. This guide covers slat roll former configurations, workings, customization, suppliers, and more.
Overview of rolling shutter slats roll forming machine
- Roll form metal coils into various shutter slat profiles
- Efficient continuous production with high speeds
- Automated cutoff and punching integrated
- Short lead times and lower costs
- Widely used by rolling shutter manufacturers
- Simple operation and quick changeovers between slat sizes
Roll formed shutter slats offer flexibility, speed and precision forming.
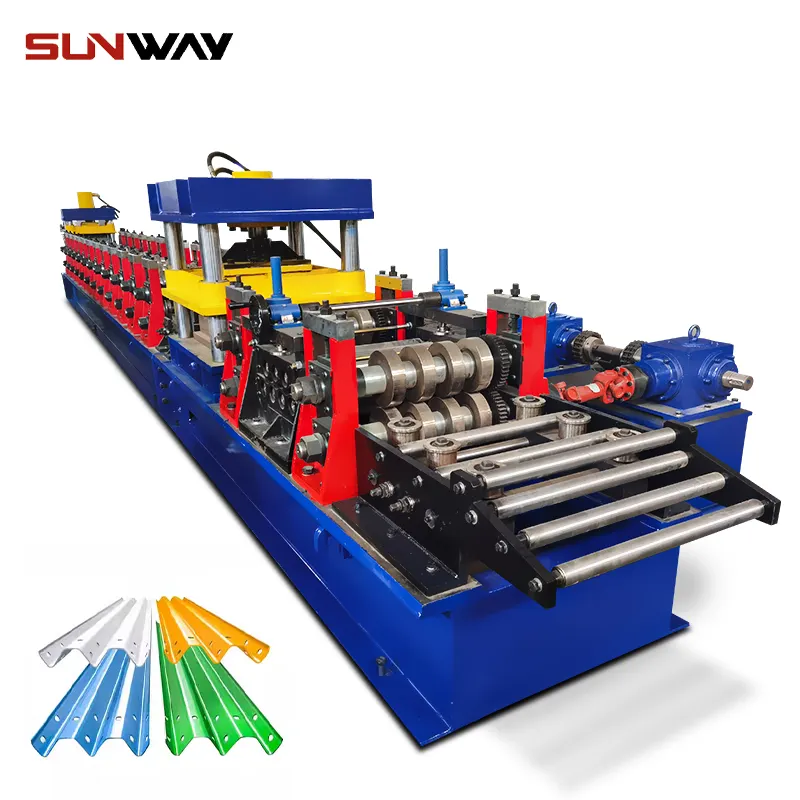
Types of rolling shutter slats roll forming machine
Major types of shutter slat roll formers include:
- Standard roll formers – Basic models with manual adjustment
- Servo motor roll formers – More advanced with precision control
- All-electric roll formers – Eliminate hydraulics for quieter, cleaner operation
- CNC roll formers – Fully automated for optimum efficiency
Higher volumes favor CNC and servo motor controlled roll formers.
Slat Roll Forming Process Overview
The rolling shutter slat roll forming process:
- Coil Loading – Steel or aluminum coil loaded onto decoiler
- Feeding – Coil fed into roll former infeed
- Punching – Any slots or holes punched early in process
- Forming – Slat formed gradually as it passes through roll stations
- Cutoff – Formed slat cut from coil at specified length
- Output – Extract finished shutter slats
The process allows high speed, automated production.
Roll Former Components
Key components of a shutter slat roll forming machine include:
- Decoiler – Unwinds the raw material coil stock
- Feeder – Feeds metal sheet into first roll station
- Punch – Punches holes or slots in slat profile
- Forming stations – Incrementally bend sheet into slat shape
- Shear/Cutoff die – Cuts finished slat profiles from coil
- Conveyor – Transports cut slats to collection
- Controls – PLC automates production and provides diagnostics
Design and Customization
- Roll stations and punches designed for exact slat configurations
- Number of stations determines profile complexity
- Quick change tooling allows fast profile changeovers
- Adjustable for different slat widths and radii
- Optional cambering for curved shutter profiles
- Integration of powder coating possible
Proper design matches required slat dimensions and interlocks.
Key Suppliers and Costs
Manufacturer | Description | Price Range |
---|---|---|
SL Metalform | Complete range of slat roll formers | $10,000 – $60,000 |
AP&T | High end all-electric CNC roll forming lines | $30,000 – $150,000 |
ETG | Affordable standard and servo powered models | $5,000 – $35,000 |
Formtek | Heavy duty lines with tight tolerances | $15,000 – $100,000 |
Venus | Budget manual and automatic roll formers | $3,000 – $15,000 |
Pricing varies based on speed, automation and accuracy needs.
Installation and Operation
- Install securely on level, rigid concrete per supplier instructions
- Inspect machine thoroughly before initial operation
- Gradually increase speeds during initial trial runs
- Apply proper tension to coils before loading
- Ensure safe operation and follow safety procedures
- Perform routine maintenance for maximum longevity
Proper operation and care helps maximize productivity.
Maintenance Recommendations
- Lubricate bearings, chains, gears and motors
- Check roll alignment and adjust/shim as needed
- Inspect drive belts and chains. Replace when worn.
- Verify cutting blade condition and sharpen regularly
- Confirm electrical, hydraulic and pneumatic connections are tight
- Check PLC system for any faults
- Clean machine to avoid dust/dirt buildup
Preventative maintenance reduces unplanned downtime.
How to Select a Roll Former Supplier
Key factors in choosing a shutter slat roll forming machine supplier:
- Experience with rolling shutter and door systems
- Capability to produce needed slat configurations
- Offer appropriate levels of automation
- Availability of quick change tooling for flexibility
- Ability to modify designs as required
- Reasonable delivery times on equipment
- Responsive pre-sales engineering and service
- Operator training and documentation provided
- Positive reputation based on client reviews
- Local representatives and parts availability
Thoroughly vet potential suppliers on these criteria before purchasing.
Pros and Cons of rolling shutter slats roll forming machine
Advantages | Disadvantages |
---|---|
High production speeds | Significant initial investment |
Consistent, accurate bends | Fixed tooling provides less flexibility |
Lower cost than other processes at volume | More maintenance than simpler methods |
Automated production flow | Roll changes take time |
Minimal secondary processing | Floor space requirements |
Scales efficiently with demand | Limited to thinner metal gauges |
Roll forming excels for medium to high volume slat production.
Comparison to Other Manufacturing Methods
Process | Pros | Cons |
---|---|---|
Extrusion | Fastest process, excellent consistency | Fixed dies, high initial cost |
Press brake forming | Very flexible, easy changeovers | Slower, inconsistent bends, labor |
রোল গঠন | Efficient for medium-high volumes, fast | Somewhat fixed tooling, cost |
3D bending | Programming flexibility, precision | Slowest process, equipment cost |
Each process has optimal applications depending on volumes, lead times, and costs.
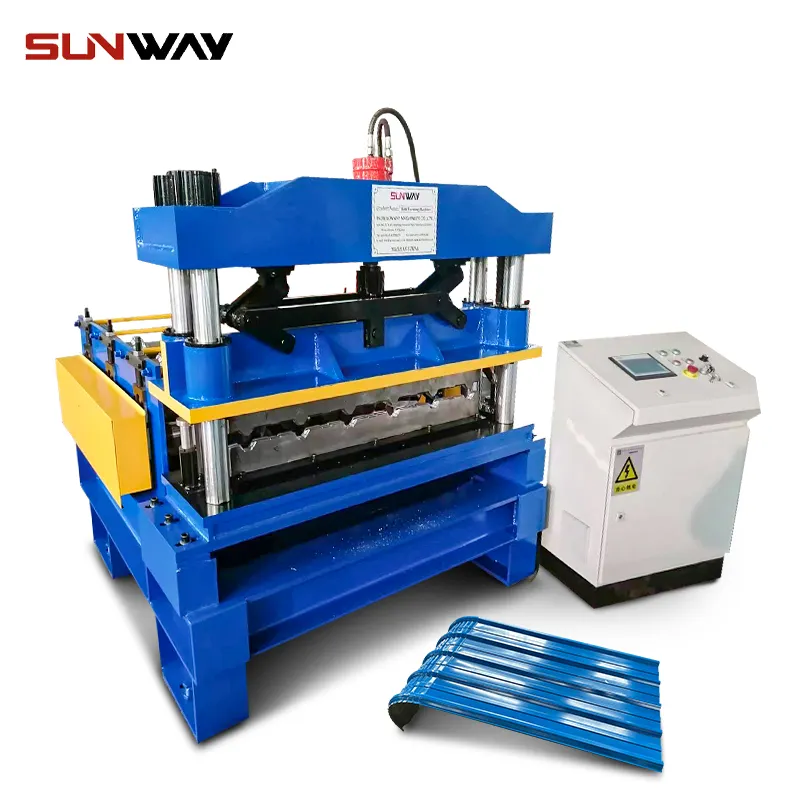
FAQ
What gauge metals can be roll formed into shutter slats?
Typical gauges range from 0.5 mm to 1.2 mm for steel and 0.8 mm to 2 mm for aluminum. Maximum capacities depend on equipment size.
What tolerances are held on roll formed slats?
Standard roll forming accuracy is +/- 0.5 mm. With CNC controlled electric servo roll formers, tolerances of +/- 0.25 mm are achievable.
How long does it take to do a roll change to a new slat profile?
Manual machines require 1-2 hours for a roll changeover. With advanced quick change systems, under 15 minutes is achievable.
Can PVC coating be added as a secondary process?
Yes, PVC coating can be optionally integrated by adding an unwind stand, pre-treatment, and extrusion crosshead for coating after roll forming.
Are powders or liquids required for roll forming?
No. Roll forming bends dry coil stock fed directly into the process. No liquids or lubricants are needed.
উপসংহার
Roll forming provides an efficient, high speed production method for rolling shutter slat manufacturers to meet demand. Integrating punching and cutting into the automated process minimizes secondary steps. With quick change tooling and precision electric or CNC roll formers, different interlocking profiles can be quickly produced on the same line. While needing moderate initial capital expenditure, over time roll forming results in lower overall costs and lead times compared to alternate methods. When properly leveraged, it can give manufacturers a competitive advantage in quality and price for rolling shutter components.