Purlin roll forming process is a critical step in the construction industry that involves the shaping of metal sheets into purlins. These structural components are essential for supporting the roof and wall systems of buildings. However, this process is not always straightforward, and various problems may arise, affecting the quality of the final product. In this article, we will explore some of the common problems that occur during purlin roll forming process and provide solutions to overcome them. Whether you’re a contractor, engineer, or manufacturer, this post will provide valuable insights to help you achieve optimal results and avoid costly mistakes.
Common problems in purlin roll forming process
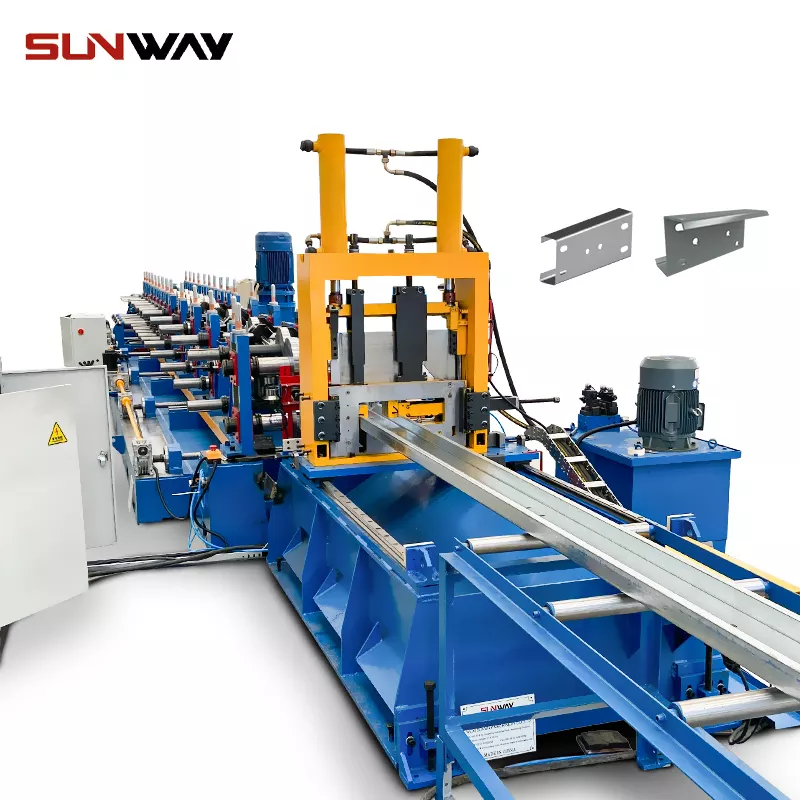
Uneven shape of purlin:
One of the common problems in purlin roll forming process is the uneven shape of the purlin, which can result from several factors. One possible reason for this issue is the incorrect setting of the rollers or misalignment, leading to uneven pressure distribution during the forming process. To avoid this problem, it’s essential to ensure that the rollers are correctly aligned, and the pressure distribution is even. Regular maintenance of the rollers and machine can also help to prevent this issue.
Coil set or cross break:
Coil set or cross break is another problem that can occur during purlin roll forming process. This issue happens when the metal sheet exhibits a permanent curvature that remains after the forming process. Coil set or cross break can negatively affect the quality of the purlin and lead to production delays. To avoid this problem, it’s important to use high-quality metal sheets with minimal internal stress. The use of leveling equipment before feeding the sheet into the roll forming machine can also help to prevent coil set or cross break.
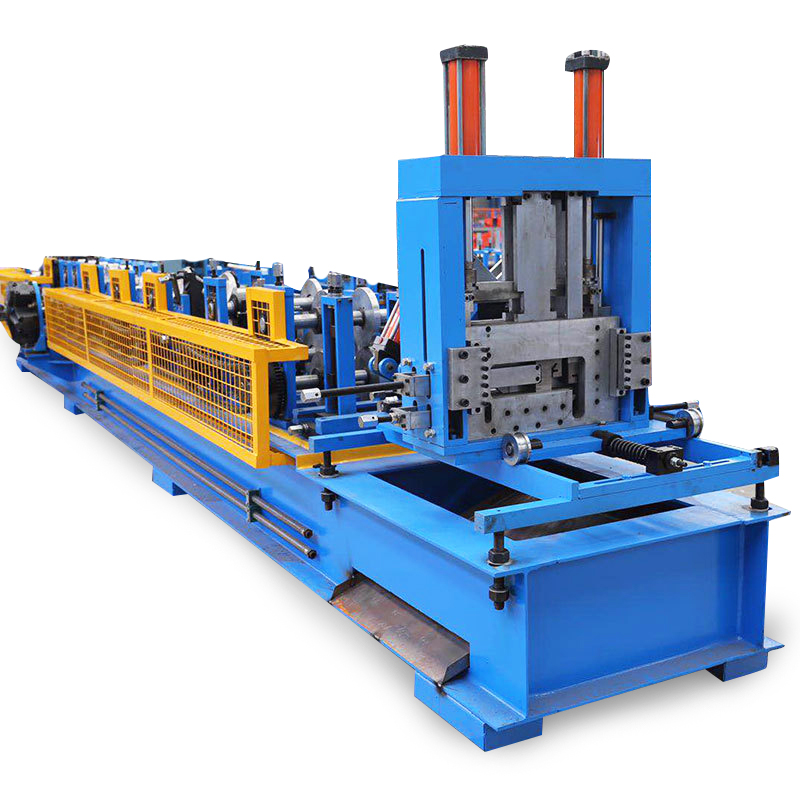
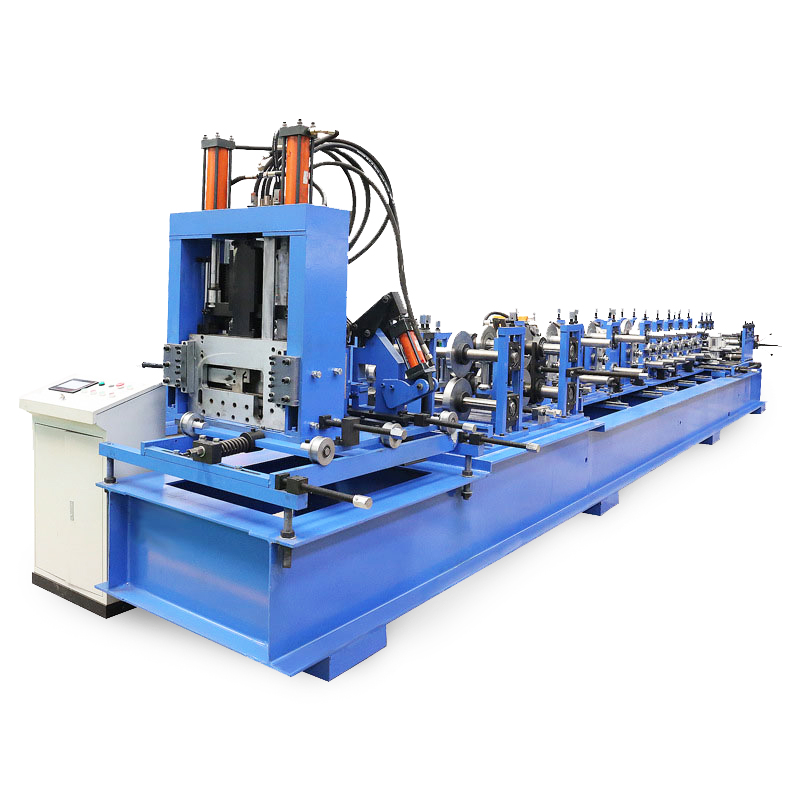
Edge wave:
Edge wave is a problem that occurs when the edges of the metal sheet exhibit a wavy shape, resulting from uneven stress distribution during the forming process. This issue can affect the final product’s quality and lead to rejections and waste. To prevent edge wave, it’s crucial to ensure that the rollers are correctly aligned and set to apply uniform pressure on the metal sheet. Using high-quality raw materials with minimal internal stress can also help to avoid this problem.
Buckling:
Buckling is a common problem that occurs when the purlin’s length exceeds its width, leading to a bending effect. This issue can result from incorrect roll forming machine settings or insufficient material strength. To avoid buckling, it’s crucial to ensure that the roll forming machine is set correctly, and the raw materials used have sufficient strength to withstand the forming process.
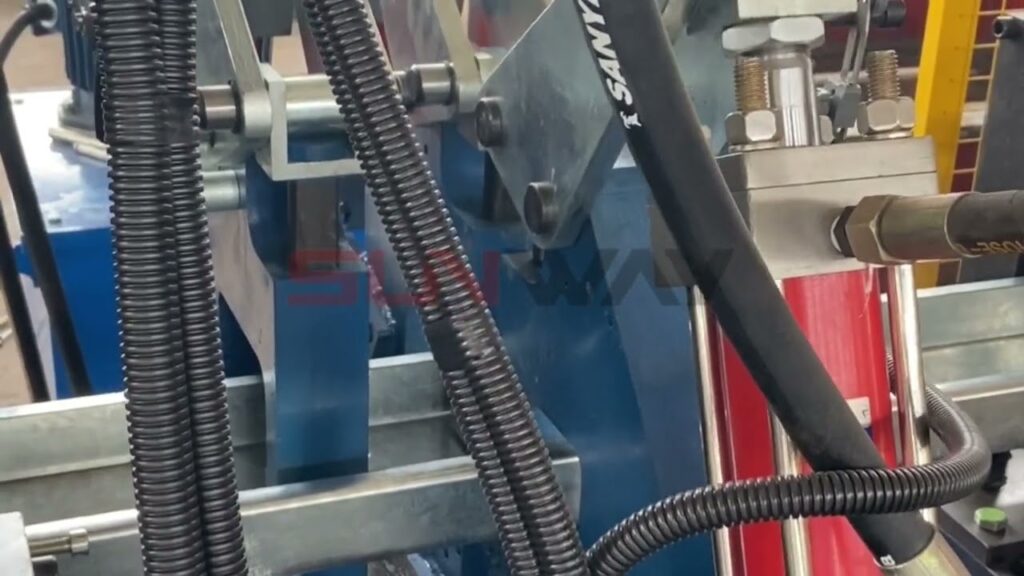
Spring back:
Spring back is a problem that occurs when the metal sheet returns to its original shape after the forming process, leading to the purlin’s inaccurate dimensions. This issue can result from several factors, such as the incorrect setting of the rollers, material type, and thickness. To address spring back, it’s important to adjust the rollers’ settings to apply the correct pressure and ensure that the metal sheet’s thickness and type are appropriate for the forming process.
Other problems:
Other common problems that may arise during purlin roll forming process include material cracking, weld defects, and dimensional variations. To solve these issues, it’s crucial to use high-quality raw materials, regularly maintain the roll forming machine, and ensure proper operator training and handling of the machine.
Solutions to the problems in purlin roll forming process
Adjusting the roll forming machine:
To solve the problems that may occur during purlin roll forming process, it’s important to adjust the roll forming machine settings correctly. For example, to address the problem of uneven shape of purlin, one should check the rollers’ alignment, adjust the roller pressure, and ensure that the roller spacing is uniform. To prevent buckling, adjust the roller settings to apply the correct amount of pressure, and ensure that the material’s thickness is appropriate for the forming process.
Using quality materials:
The quality of raw materials used for purlin roll forming process significantly impacts the final product’s quality. Therefore, it’s essential to use high-quality materials with minimal internal stress, which can prevent problems like coil set or cross break, edge wave, and material cracking. It’s crucial to purchase materials from reputable suppliers who follow strict quality control procedures to ensure that the materials meet the required standards.
Proper maintenance of the machine:
Proper maintenance of the roll forming machine is crucial to ensure its proper functioning and prevent problems that may occur during the purlin roll forming process. Regular maintenance should include cleaning the machine, inspecting the rollers, lubricating the moving parts, and checking for any wear and tear. Any damaged or worn parts should be replaced immediately to prevent further damage to the machine and the final product. Proper operator training and handling of the machine are also critical to prevent accidents and damage to the machine.
In conclusion, addressing the problems that may arise during purlin roll forming process requires a combination of adjusting the roll forming machine, using quality materials, and proper maintenance of the machine. By following these solutions, manufacturers, contractors, and engineers can produce high-quality purlins that meet the required standards and ensure the structural integrity and durability of buildings.
The purlin roll forming process is a critical step in the construction industry that involves shaping metal sheets into purlins. However, various problems may arise during the process, affecting the final product’s quality. To overcome these issues, it’s essential to adjust the roll forming machine settings correctly, use high-quality materials, and properly maintain the machine. By following these solutions, manufacturers, contractors, and engineers can produce high-quality purlins that meet the required standards and ensure the structural integrity and durability of buildings.
As a final tip, it’s important to ensure that the roll forming machine is operated by trained and skilled personnel who can identify and address any issues that may arise during the process. Regular inspection and maintenance of the machine can also help prevent problems and prolong the machine’s lifespan. Using high-quality materials and strictly adhering to quality control procedures can also help prevent issues like coil set or cross break, edge wave, material cracking, and buckling. By following these tips, anyone involved in purlin roll forming process can ensure the production of high-quality purlins that meet the required standards and contribute to the construction of safe and durable buildings.