ক corrugated roof panel making machine is an essential equipment for manufacturers of roofing and wall cladding sheets. This guide provides a comprehensive overview of corrugated panel roll forming equipment, including working principles, main components, machine types, production process steps, operational guidance, maintenance procedures, and more. Read on to gain key insights needed to choose, operate and upkeep these sheet metal forming lines efficiently.
How Does a Corrugated Roof Panel Machine Work?
A corrugated panel making machine works by cold rolling and bending sheet metal into wave-like corrugated profiles under pressure using custom roller dies. The raw metal sheet or coil is passed through a series of roller stations to shape it incrementally into finished panels with corrugations as per profile design.
The forming modules apply pressure on the strip to bend and warp it into wavy forms shaped by the roller dies. The sheet metal gets thinner but retains strength due to grain structure changes. Automated feeding, gauging, notching, shearing and stackers allow sequential high-speed production of panels in different sizes as per adjustable parameters.
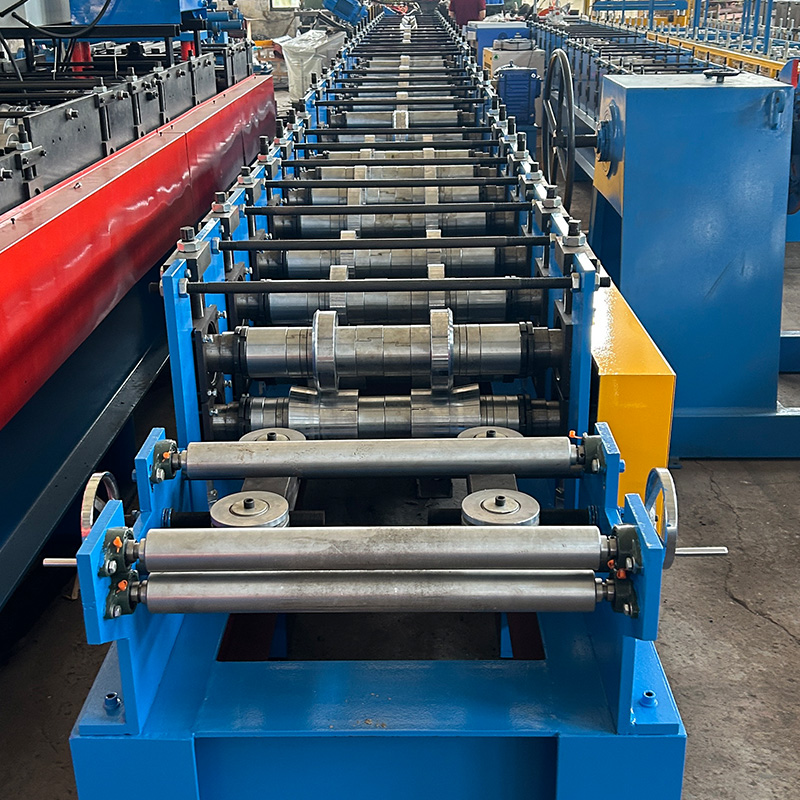
Main Components of a Corrugated Roof Sheet Making Line
A complete corrugated panel production line has several modular components for the shaping, sizing and handling functions. Here are the key forming machine parts:
Table 1. Major Components of a Corrugated Panel Roll Former
S. No | Component | Purpose |
---|---|---|
1. | Coil feeder | Feeds metal coil strip into line |
2. | Feeder rollers | Pulls metal sheet into machine |
3. | Forming stations | Roller dies to bend metal into waves |
4. | Sizing units | Calibrate sheet thickness and width |
5. | Notcher/shearer | Cut notches or trim sheet |
6. | Cutoff knife | Cuts sheets to length |
7. | Stacker | Collects finished sheets |
8. | Control panel | HMI and PLC automation |
Types of Corrugated Roof Panel Making Machines
There are some key ways to categorize the variants of corrugated panel production lines:
Table 2. Types of Corrugated Roof Sheet Making Equipment
Basis | Types | বিস্তারিত |
---|---|---|
Profile design | Sinusoidal wave Trapezoidal Tile shaped Custom profiles | Different wave sizes and shapes |
Production scale | Light duty Medium duty Heavy duty | Varying speeds, widths and thicknesses |
Automation level | Manual Semi-automatic Fully automatic | Operator needed or not |
Roofing type | Asbestos sheets Metal sheets Fiber cement sheets Plastic corrugated sheets | Suitable for specific materials |
So a roof panel line can be obtained for small, medium or large scale needs, with automated or manual configurations, and designed for the material and profile requirements.
Step-by-Step Corrugated Roof Panel Production Working Process
The typical working process on a corrugated sheet making machine involves several steps from raw material inputs to finished outputs:
Figure 1. Corrugated Roof Panel Manufacturing Process Flowchart
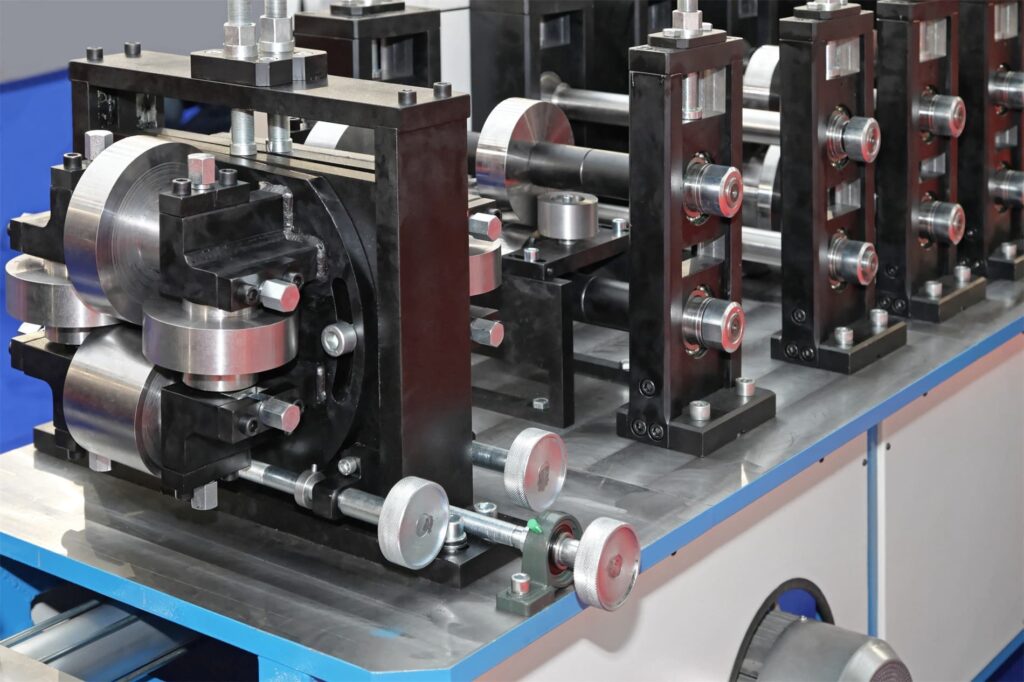
Coil Feed – The metal coil is loaded onto a de-coiler and fed into the sheet line.
Sheet Feeding – Feeder rollers grip the strip and pull it through the equipment at an adjustable speed.
Pre-forming – The sheet gets preliminary bending for distortion removal via pre-forming stands.
Forming – Multiple roller dies bend the sheet in incremental steps into wave-like corrugations conforming to the die profiles.
Calibration – Sizing units calibrate thickness and width to tolerance levels for profile uniformity.
Notching/Cutting – Notching units cut out slots for joining sheets while cutoff shears cut each sheet to length.
Stacking – Formed panels get stacked automatically or manually via stackers.
Bundling – Stacked sheets are bundled for storage and transport.
Quality Check – Formed sheets undergo quality checks before packaging.
Main Assemblies of a Corrugated Roof Sheet Machine
We take a closer look at the key assemblies that input materials, form the waves and handle the finished sheets:
Raw Material Feed Assembly
- Coil holding mandrel
- Powered de-coiler
- Sheet guiding rollers
- Feeder rollers
- Strip joiner welder
Corrugation Forming Assembly
- Pre-forming stands
- Forming stations with roller dies
- Profile monitoring gauges
- Sheet thickness & width calibrating units
Finishing Assembly
- Notching and slotting stations
- Flying cutoff shear/slitter
- Finished sheet conveying belts
- Manual/automatic bundling stacks
- Punching/embossing stations (optional)
The flexibility to add or remove modules and customize for exact production needs is a key benefit.
Key Machine Functions: Material Feed, Forming, Sizing, Cutting, Bundling
We take a closer look at the vital corrugated sheet making processes – raw material inputs, wave profile forming steps, sizing, cutting and bundling of finished panels:
Table 3. Main Functions of a Corrugated Roof Panel Production Line
Function | Working Principle | Components Used |
---|---|---|
Material Feeding | Pulls metal sheet at adjustable feed rate | De-coiler, sheet guides, feed rollers |
Pre-forming | Applies preliminary bending | Pre-forming stands |
Profile Forming | Bends sheet incrementally into corrugations | Forming stations, roller dies |
Sizing | Calibrates thickness and width | Sizing units with rollers |
Notching/Cutting | Cuts notches for joining or slices to length | Notcher & cutoff shear |
Bundling | Stacks sheets automatically or manually | Conveyors, bundling arm stacker |
Fine-tuned automation and sequential functioning of the above processes enables efficient high-speed corrugated sheet production on these machines.
Key Machine Design Aspects
Some notable corrugated panel making machine design aspects from a technical perspective include:
- Roller dies – Made of alloy steel for strength and hardness to shape sheets. Die geometry defines profile.
- Roll forming method – Used for its advantages like high speeds and process control.
- Horizontal layout – For smaller footprint and sequential arrangement of stations.
- Modular assemblies – Enables customization of processes as required.
- Thickness gauges – Laser sensor feedback loops ensure thickness uniformity.
- PLC automation – Touchscreen HMI and software for production monitoring.
Customization Flexibility of Corrugated Roof Sheet Machines
A key strength of corrugated sheet making equipment is flexibility for customization as per user needs:
Table 4. Customization Capabilities of Corrugated Panel Production Lines
Machine Part | Customization Parameters |
---|---|
Roller dies | Wave profile shape and size |
Forming stations | Number of passes for gradua forming |
Sizing stands | Final sheet width and thickness |
Notching units | Notch shape, size and pitch |
Shearing station | Cutoff sheet length |
ডিকয়লার | Compatibility for input coil width |
Stacker/bundler | Batch size for stacking before bundling |
The modular configurations allow adaptations to produce corrugated roofing sheets from 0.4mm to 2mm thickness, maximum 2250mm width, with various profile designs and production volumes.
Choosing Reputable Corrugated Roof Panel Making Machine Manufacturers
With so many suppliers in the market, identifying reputable manufacturers is key for getting high quality equipment. Here is a checklist of factors to consider:
Table 5. How to Select Reliable Corrugated Sheet Making Machine Brands
Parameter | What to Look For |
---|---|
Quality | Use fine materials, advanced construction |
Reliability | Evidence of durable trouble-free operation |
Productivity | Higher production volumesindicate robust design |
Cost | Reasonable pricing levels as per specifications |
কাস্টমাইজেশন | Flexibility for user-specific configurations |
Service | Responsiveness for technical support issues |
Proven Track Record | Case studies, client testimonials on consistent performance |
Production Testing | Ensure machine testing before shipment |
Checking technical parameters is vital but evidence of field performance, service record and client reviews helps validate quality.
Installation & Commissioning
Proper installation and commissioning processes are vital for smooth functioning of a corrugated sheet making line. Here are key guidelines:
Table 6. Corrugated Panel Machine Installation Best Practices
Activity | Methodology |
---|---|
Site Preparation | Ensure appropriate foundation, space, wiring, power rating |
Unloading & Placement | Use suitable lifting gears, align perfectly |
Assembly | Assemble parts sequentially referring manuals |
Wiring | Connect cables securely following circuit diagram |
Earthing | Do earth wiring properly to prevent shocks |
Trial Runs | Set parameters and test sequentially first with dummy sheets |
Taking care to firmly anchor the equipment, connect interlocks, ensure smooth material flow through line, calibrate sensors etc. is needed before operation.
Operation & Control Procedure
We look at the step-by-step functioning sequence and control methodology:
Working Steps
- Set parameters on HMI like sheet dimensions, speed, batch size etc.
- Feed coil strip into decoiler and thread through stations
- Initiate cycle through panel or automated start
- Monitor thickness, width sensors for uniformity
- Collect formed sheets and bundle manually or automatically
- Repeat cycle continuously for production needs
Control Method
- Centralized touchscreen HMI
- Intelligent parametric PLC logic
- Servo motors for operational control
- Laser sensor feedback for precision
- Warning indicators for abnormalities
- Emergency stop for safety
The automated programming synchronizes the speed, functioning and actuation of different components for smooth efficient working.
Regular Inspection & Maintenance
To sustain high uptime and maximum performance, scheduled inspection and maintenance aspects have to be followed:
Table 7. Standard Maintenance Schedule for a Corrugated Roof Panel Machine
Frequency | Activity | Method |
---|---|---|
Daily | Check oil levels Test cycle | Replenish if needed Initiate trial run |
Weekly | Inspect stations Sensor cleaning | Ensure smooth operation Blow compressed air |
Monthly | Bolt tightening Lubrication | Tighten loosened bolts Apply grease |
Quarterly | Replace worn parts | Check rollers, belts, nuts etc. |
Activity logging, wear gauge checks, keeping spares handy and annual servicing contracts are other best practices.
Advantages of Corrugated Sheet Making Machines
Some major advantages of corrugated panel production lines include:
- High production volumes with speeds around 30-40 meters/minute
- Low operational costs due to process efficiency
- Good quality sheets with thickness and profile consistency
- Lower manpower needs owing to automation
- High uptime and low maintenance requirements
- Customization flexibility for user requirements
- Higher yields and reduced wastage
These benefits make them a profitable equipment choice for manufacturers.
Limitations of Corrugated Roof Panel Equipment
However, corrugated sheet making lines do have some limitations buyers should be aware of:
- Large space needed for equipment installation
- High initial capital investment required
- Qualified staff needed for operation and maintenance
- Limited thickness and width capacity per machine
- Restricted to using coil feeds as raw input
- Profiles restricted to available roller die sets
Cost Analysis of Corrugated Sheet Production Lines
A key aspect potential corrugated panel making machine buyers consider is return on investment. Here is an overview of cost economics:
Table 8. Typical Cost Breakdown of Corrugated Roof Sheet Plants
Expense Item | Indicative Cost |
---|---|
Corrugated sheet making machine | USD 100,000 to 500,000 |
Additional tooling and handling equipment | USD 20,000 to 50,000 |
Factory infrastructure and utilities | USD 150,000 to 300,000 |
Total Investment | USD 300,000 to 850,000 |
Typical production costs for finished corrugated sheets from these plants can range between USD 2.50 to 5 per square meter depending on raw material, labor, utility rates etc.
With rising infrastructure activity and plastic replacement trends, demand is increasing, enabling good capacity utilization and ROI.
Corrugated Metal Roofing Sheets – Applications and Use
Corrugated roofing sheets made on these machines find use in industrial, commercial and residential applications.
- Warehouses
- Production facilities
- Agricultural buildings
- Shopping centers
- Apartments
- Tiny homes
- Temporary structures
- Renovation projects
Lightweight affordability along with practical benefits like easy installation, durability, weather-resistance, eco-friendly nature drive widespread usage.
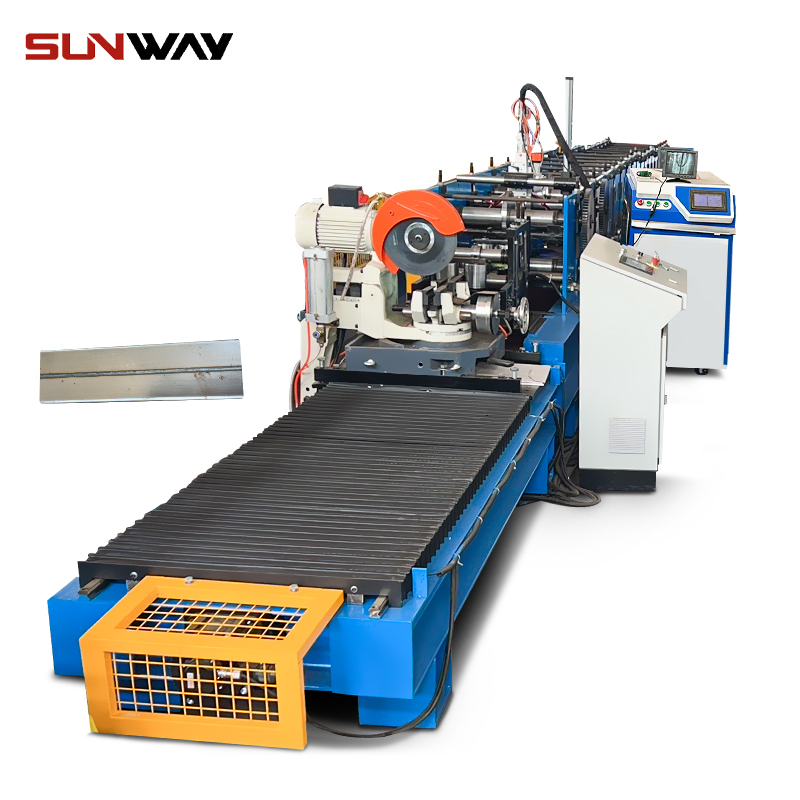
FAQs
Q: What materials can be formed into corrugated sheets?
A: Common materials used are steel, aluminum, zinc but also fiber cement boards, bitumen sheets, recycled plastics etc.
Q: What coil thicknesses can a standard machine handle?
A: Machines can typically process metal coils from 0.3mm to 3mm thickness. Upper limit goes up to 6mm with heavy duty equipment.
Q: Can I get custom profile waves or special coatings?
A: Yes, custom roller dies help obtain different profile shapes. Special coatings or paints can also be integrated using additional finishing stations.
Q: How to reduce noise levels on these machines?
A: Methods like sound enclosures, vibration dampeners, isolation pads help attenuate operating noise. Preventive maintenance also minimizes sound.
Q: What factors affect total line cost?
A: Key determinants are production speed/volumes, sheet width/thickness, automation level, accessory tools, customization needs etc.
Q: How much area is needed to install a corrugated sheet making plant?
A: Around 800 to 2500 square feet area is ideal for a corrugated sheet production line and auxiliary systems installation.
Q: Can used/refurbished corrugated panel making equipment be a good option?
A: Yes, cost benefits can be availed but ensure replacement of all wear items, warranty provisions etc. Verify machine condition thoroughly before purchase.
উপসংহার
We have covered a comprehensive guide ranging from corrugated sheet machine working principles, primary components, functions wise processes, operational guidance, maintenance norms, price economics through to applications of the boards produced on these lines.
The evolution of versatile easy-to-use corrugated panel production plants with automated features has made setting up profitable roofing sheet manufacturing businesses much more viable for small and medium enterprises. Careful selection of equipment capabilities in line with production targets, quality norms and upgradeability for future needs is key for long term success.
With the construction industry projected to continue growing at over 5% annually over the next few years, the demand outlook for pre-engineered metal corrugated roofing and wall panels is promising. This creates a good investment environment for manufacturing businesses looking to enter this market.